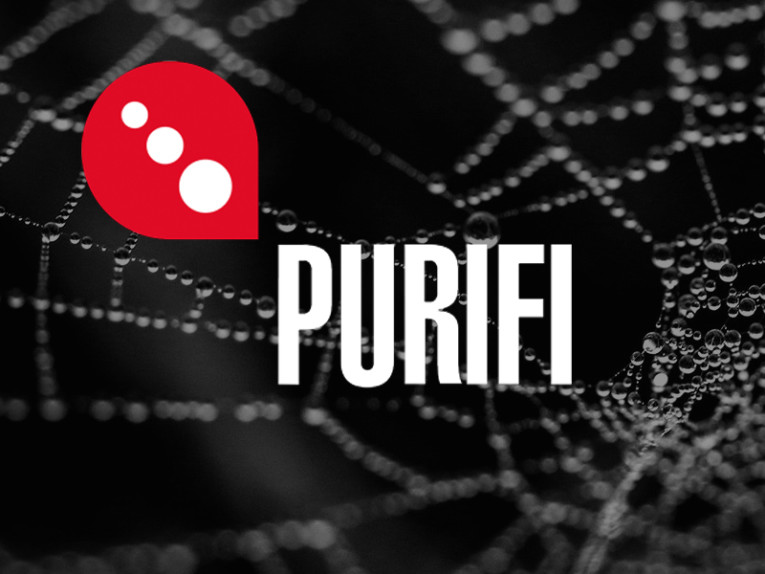
Purifi Audio was born out of the research work of Class-D pioneers Bruno Putzeys (of Philips, Hypex NCore and Kii Audio fame) and Lars Risbo, who pioneered direct switching PCM-PWM audio amplifiers as founder of Toccata Technology, later acquired by Texas Instruments (TI). With these two founders, we also find the names of Claus Neesgaard, Søren Poulsen, and Kim Madsen, also coming from Texas Instruments and holding multiple audio patents in the domain.
On the loudspeaker side of the research we also find as co-owner the name of Carsten Tinggaard, the founder of PointSource Acoustics (2009), the most reputed Danish loudspeaker lab and prototype facilities, and a leading research company in motor design simulation and loudspeaker measurements. Carsten Tinggaard was previously the product manager for Danish Sound Technology (2003) and CTO of Tymphany Denmark (2005) and he is responsible for R&D for Peerless, Vifa and Scan-Speak brands.
Also now at Purifi is Morten Halvorsen, a Senior Acoustic Engineer at PointSource Acoustics. He co-developed both the loudspeakers and sound unit of the Montana by PointSource products and specialized in electromagnetic simulations, measurements, and procedure optimization. Halvorsen researched force factor modulation, and was responsible for much of the measurement equipment and simulation models developed at PointSource, which Purifi Audio is now expanding.
audioXpress had the privilege to meet the Purifi Audio just before the opening of another edition of the High End show in Munich, Germany, where the team was making its first public presentation to the industry. During the meeting, we had the chance to learn a little more about Purifi's first product, the 1ET400A, a Class-D single-channel, analog-input, amplifier module - based on the company's new "Eigentakt" self-clocking amplifier technology. We also discussed the PTT19-W02-03 ultra-low distortion 6.5" long-stroke woofer (Xmax ±14.7 mm), which we had the chance to hear.
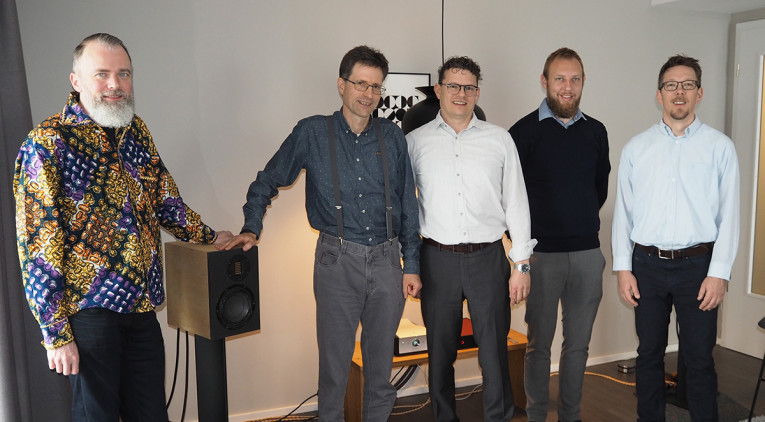
The following are some of the topics regarding the team's projects on loudspeaker drivers and audio power amplifiers. We started by discussing the amplifier platform and its self-oscillating technology but we quickly understood that Purifi's research is deeply related with trying to solve the whole audio-chain equation and that their loudspeaker research was always coming up... because, as Lars Risbo explained, they continued to see " a mountain of problems, of speaker problems..."
Bruno Putzeys (BP) : We decided to split the amplifier and the speaker problems, because initially we were sort of trying to build a "clever amplifier" that also fixes the driver problems - and we know a lot about how to do that. I think the knowledge base that we have is probably the most mature when it comes to putting something like that together. But we decided - as a startup company - that we wouldn't be breaking the bank trying to design an IC for that, and we decided it was a better move to actually improve the driver just fundamentally as a mechanical item.
Lars Risbo (LR): And do a super amplifier. We will be able to scale a lot more power on this development platform easily over the next year.
Claus Neesgaard (CN): We put the amplifier to very vigorous testing and applied all the learning from doing IC-level design and taking that to market in automotive and consumer. So, it's pushed into extreme corners of operation - robustness matters as much as performance - and I don't think you see that widely in the industry, with people caring for all these levels.
BP: When I met these guys, I thought that they were completely crazy. The sort of testing that they subjected the amplifier to was unheard of. And with all respect to my previous employer... this was so way above anything that I've seen!
They would try to run the amplifier in its current limits continuously for half an hour or so, and they walked off and have a cup of coffee. When they came back - if it was still working - they would start applying shorts while it was cooking. They had this short box, with faster and long shorts timed differently...
LR: That's a lesson we learned at TI, when we were selling products in the millions... When we have a large customer and they have a problem, they would call the CEO, and that's not fun...
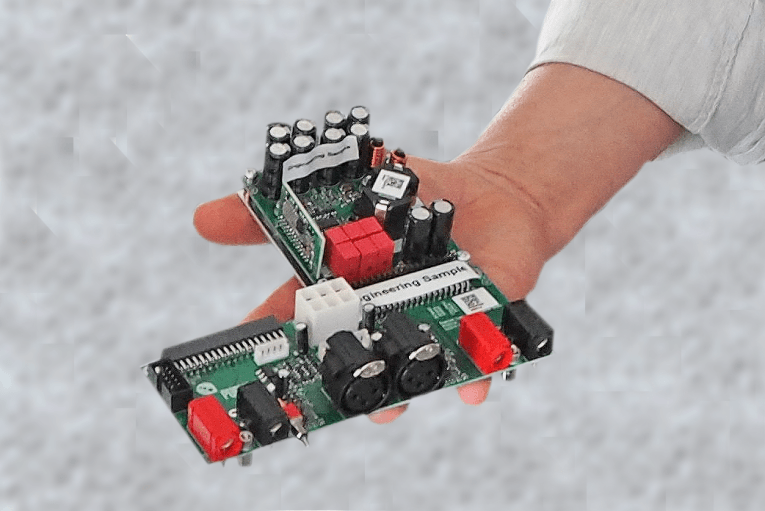
CN: If the performance is good, you can win a few customers and they can live with it. But we don't want to be just the highest performance high-end, addressing a few people's wishes and concerns, we want to really take this out and have everyone benefiting from it.
BP: It's the same as in live sound. If something is practical and portable, and if it's reliable, etc., only then will they choose the one that sounds best. But only after you've got all the other boxes ticked.
LR: We don't see ourselves as a high-end company in that sense. What we want is to do better sound that reaches out to all music lovers. We are not trying to do something that only works sometimes, or something that's based on these very special materials. We are trying to apply clever design, clever geometry, with industry standard materials and see how far we can get with that.
BP: Actually, we can get further without applying "magical materials" to an industry standard design, which is what everyone else does.
CN: Our drivers are a very good example of that.
For a moment, we stopped the conversation to look at the driver's measurements... some of which are available online on Purifi's website.
BP: When you look at other driver manufacturers' datasheets, you will not see these graphs. When we ask why don't they put distortion measurements in the datasheets, they say that is something that people measure for themselves. A) That's probably not true. B) If I want to buy a driver, I want all the data that allows me to actually select the one that I want without having to buy samples. There needs to be data that you can actually extrapolate. It's not just about data that shows "look what this baby can do!" It's about data that tells me what I can do with that baby!
CN: We also wanted to introduce a new level of measurements. We would like to tell everybody how we measure and why we measure, the detail of analyzing both harmonic differential tones and multitudes, complex signals, and find where it hurts... But for that, we also needed a new analyzer...
LR: When we started looking at motors we found a major distortion source that was flying under the radar. And it's not captured by the conventional graphs. We can have all these symmetrical plots and as part of that you can have loads of signal distortion. So there was obviously something that's not covered.
BP: In this specific case, the important information that you need to extract from the motor measurements is the inductance at all frequencies and all positions. And then suddenly you can discover a lot. That's something that we never see being done. Eventually we will see some sort of inductance at a certain position at an unknown frequency, and that doesn't actually tells us what the speaker will do when it sees a signal with one or two frequencies or whatever. So we've built our own analyzer for that and what we care is of course about the data that we needed to understand the problem. Many people will be gutted to ear that we are not going to sell the analyzer... Essentially, you mount the driver in a fixture like you would do with a Klippel analyzer and then you measure for two seconds and out pops all the data that a Klippel analyzer produces, plus the bit of data that we want.
CN: I guess it was the realization that in order to have that level of understanding and dig into the deepest corners, we needed to build our own machine...
BP: It was actually once that worked, once that level of detailed knowledge was in a mathematical model, we knew where to start looking to fix the problem.
LR: And once you understand the problem, the solution almost presents itself... We are driven from an understanding in closing the loop between our model and measurements.
CN: It's very far from the traditional trial and error. A lot of people talk about simulation, but simulation is also trial and error. This is way more about understanding the problems before you even try to do anything about it.
BP: And the understanding comes from the mathematical model. Not from the simulation. Usually, the simulation is actually more about catching writing errors in the mathematical derivation. Because once that's done on the simulation it just ends up exactly what the model already told me.
CN: We go so far as to prove that the model was actually working, then we build the machine that actually could take the voice coil and move it against the magnet system, get all the data out, as a function of the position, frequency, and then we compare with our analyzer. That has been a constant. So when we have a question, we build, we measure, we compare, to see if there's something that is not matching, and the question will be there until we have solved it and the simulation is verified. So it is a kind of an adaptive signal processing where we are constantly in a loop, between simulation modeling, building, measuring, and listening, back and forth.
LR: The more you can condense a mathematical formulation, the more you can computerize the model. Because the mathematical model is so fast to evaluate, you can actually have a computerized optimization that takes a little more time than taking a cup of coffee.
BP: Exactly! It's exactly the same thing we did with the amplifier. We actually solved one of those things that was completely flying under the radar, but the bit that I am most proud of is that I finally figured it out how to make a sample data model of a PWM, away from 50%. That's the sort of thing I'm happy about. That in the end, the amplifier performed fantastically well. That I now have the whole thing... a unified model.
CN: Another strong thing that we have is that we can now take out all the different distortion components, because that's what we focused on. Getting the distortion down. Removing all the distortion components. In the driver - where you have the complexity of the electromagnetic, mechanical movements, acoustic radiation, and again not knowing what comes from where - by putting it into a very sophisticated, not only static, but dynamic model, in just two-seconds of measurements, we can decompose all the distortion components and we can begin to see which one of those is.
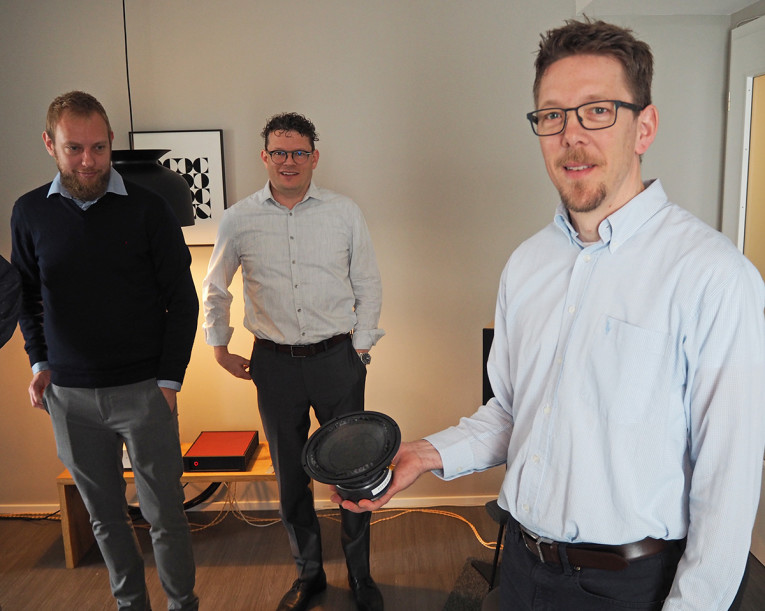
AX: So, you have been working on the amplifier and on the driver. How do you connect both?
BP: It's quite simple. We have a technology company with two specific areas. One is doing the amplifier and the other doing drivers. Of course, it is the same team so we do the marketing together, but basically people can buy the driver or they can buy the amplifier, or if they want we can combine both. As soon as we decided not to mix the two problems in just one product, at that point we just said, OK let's market and sell them separately so that the people who just want to buy drivers from us can do that.
CN: Yes, they don't depend upon each other in any way. You get the full benefit of the amplifier as a standalone and you get the full benefit of the driver as a standalone, of course you can combine it and get something that's even better, because you are improving two layers or two parts of the signal chain. But there's no requirement in doing so.
AX: Bruno, but with KII Audio you were involved in a project where you designed an active system that involved precisely tuning all the aspects of the chain, including using DSP to help solving many of the problems you identified. There are currently manufacturers working on developing new drivers that are actually tied up to a dedicated amplifier and a sensor that helps counter nonlinearities...
BP: We have been looking at the sensor thing but actually it's more expensive and less effective than actually fixing the driver. Because for instance, motional feedback - there are no practical ways that you can make the loop band of a motional feedback system much better than a couple hundred hertz. Which means that if you have intermodulation distortion, that is not being corrected by the motional feedback system. So, if you want to fix that as well, actively, you can, but it means that at that point your DSP will have to contain that particular model, so that it can actually predict what that motor will do. Motional feedback with a simple sensor is kind of a dead-end. The sensor is useful in the case of where we have a model and there is a positional parameter in there and then it's a good idea to know the position within a half a millimeter or so... and to get rid of drift. But at that point that sensor is no longer really in the loop. It's only applied to that function of the model.
I see the point of selling a driver with an amplifier, because that's how we started this project. It's just that it turned out that it was cheaper to build a driver that didn't have all those distortions. I don't think that's necessarily the case that companies will be co-selling drivers and amplifiers. Of course, it just happens that we would be terrifically pleased to do exactly that. But at the moment...
LR: We don't rule out that at some moment we will have something with a sensor. But as long as the problem is actually cheaper to solve...
BP: Exactly. The combination of a sensor and the model, not for real motional feedback but simply using the sensor to inform the model roughly where the cone is - it doesn't even have to be accurate.
CN: At the end of the day, it is about solving problems where it makes sense. There were some obvious problems that it really made sense to solve in the driver, and at no extra cost. Not by using fancy materials, but something that we can apply to the entire market eventually.
We also have the experience of some things we have done in the past, where the more it becomes a "solution sell," where you have to change multiple things at a time, the longer the timeline you need to live with. Where is, if you can swap out individual things it is much faster and you get some feedback on the way and it's easier to shape.
LR: We were able to improve our understanding of the project... One thing that's bad is when you are trying to do a control of a system you don't understand.
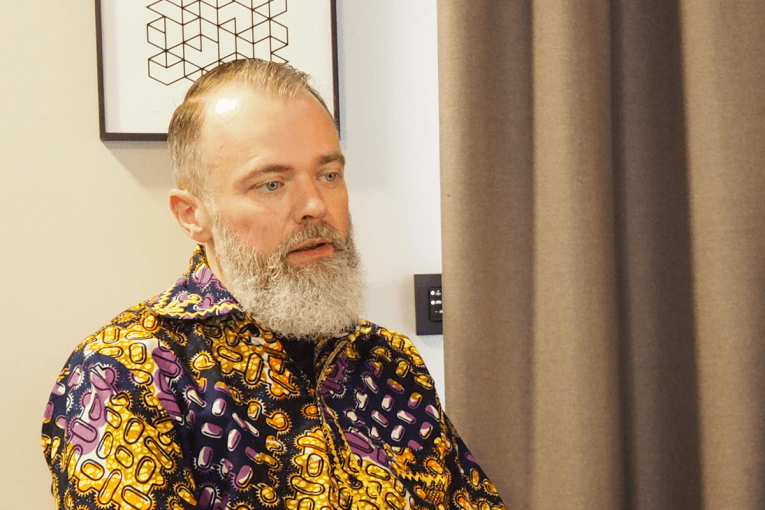
AX: But one thing that we see often in combination is the Class-D amplifier and the power supply. What is your opinion about that?
BP: Oh. It's just a matter of time until we do that as well. We designed the Class-D amplifier first and the power supply comes next. As a research company, we needed to get our fundamental IP in order because we started thinking about a product line-up. But I think quite clearly that amplifiers with a matching power supply bolted-on is a product proposition that's here to stay.
CN: You will see that coming from us, in parallel with seeing the expanding product portfolio of modules, to get broader coverage. Higher power, higher current, higher voltage.
BP: It's simply a matter of practical experience. I was also there when Hypex started and if at that point we would have tried to do integrated modules, straight off the bat, then probably we would have gone bust before we could solve anything. You have to start selling what you have to the people who most want it. Clearly, our first module offering is something that we are mostly pitching at high-end audio companies, because that's a good way to start. But it's not our intention to restrict ourselves to that space. We definitely want to end up doing fully integrated power solutions.
AX: On the driver design. Can you expand the fundamental principles with different materials?
CN: Yes, different sizes and different materials and we can accommodate different requirements. We are very well positioned to scale from where we are today.
Purifi Audio is now continuously updating its website, where we can find a lot of measurements that are not very common to find in product datasheets - as discussed - and there are also some relevant technical briefings, like a PDF named "Distortion, The Sound That Dare Not Speak Its Name." aX