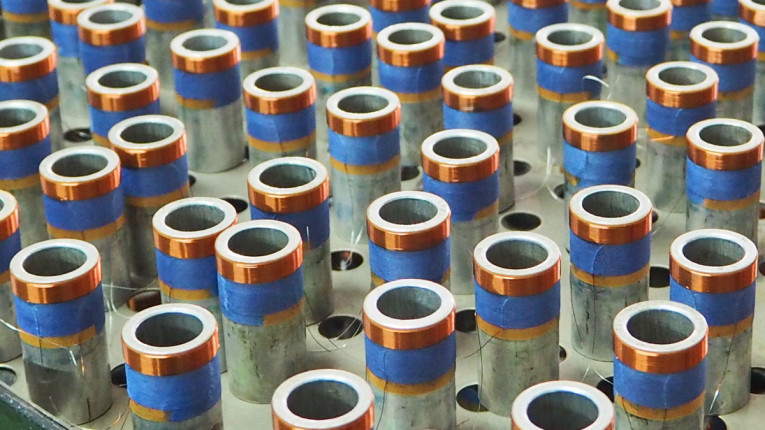
Wire Cross-Sections
Flat wire that is wound on edge has been with us for more than 75 years, starting with the Western Electric and Jim Lansing compression drivers and woofers for the early movie theater “talkies” that used this technique. Why flat wire? To eke out a bit more sound from the few Watts the first tube amps had in them to fill the theater with sound.
However, round cross-section wire has about 20% less packing density than flat wire. Round wire’s thermal transfer and mechanical integrity is not ideal as the contact area between layers is marginal. Yet, fabrication of ribbon wire voice coils is not easy. Flat wire with high aspect ratios requires the enamel insulation coating applied after flattening, and it requires winding at slow speeds with special wire guides and sophisticated tensioning devices. To add insult to injury, flat wire coils are single layer, so the wire must find its way to the speaker terminals back through the voice coil gap. This return home through the gap means a wider gap, or groove, not to mention solder splices from the bottom of the coil to the return wire, a hot spot on the coil from the return wire, as well as warranty returns due to the failure modes of all these problematic aspects.
Perhaps the best of all worlds is square wire (Photo 1). Square wire has performance and cost advantages over ribbon wire. Specifically, the increase in the conductor’s volumetric occupancy ratio (packing density), the advantage of skin effect, greater heat dissipation/heat transfer throughout the coil layers, and a decrease in coil size while increasing current carrying power. These features enable a tighter gap with higher BL — from both the tighter gap (B) and increased wire length (L) for the same winding height. With 20% more cross-sectional mils from square wire vs. round wire, a heavier gauge wire can be used to replace the round wire coil and still drop into the same gap. Figure 1 shows the round wire vs. the square wire.
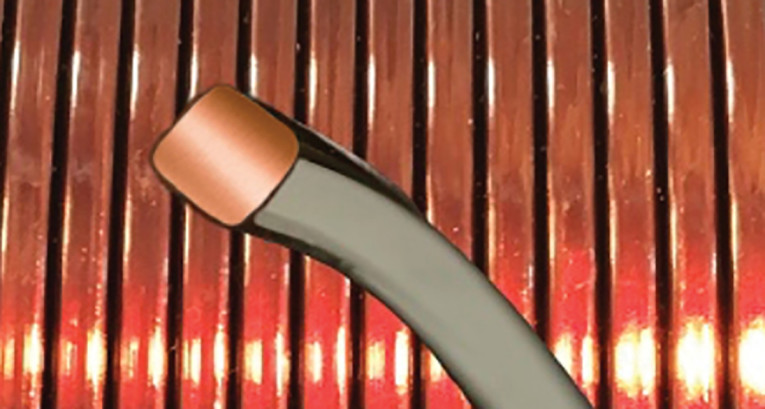
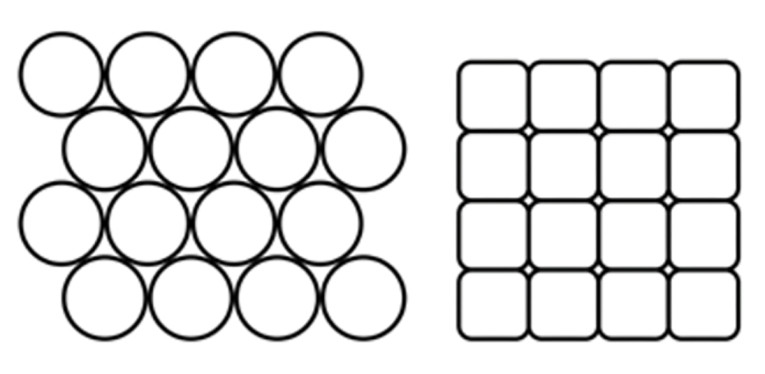
All this is applicable regardless of the conductor material such as copper, aluminum (and anodized aluminum), and copper-clad aluminum. Goto and others offer speaker voice coils with square wire.
Voice Coil Wing Tensioners
In visiting voice coil winding factories over the years, I am amazed at how rudimentary some of the winding tensioning devices are in otherwise sophisticated production lines. There are quite a few special applications where servo-controlled tensioners would be “magical.” If you spec voice coils but don’t wind them, then I should explain that typically voice coils are wound from a large spool. In the case of flat or square wire, shaping processes (milling, extrusion, etc.) start with a large spool of round wire run through the shaping process and then wound onto the shaped cross-section wire spool.
For more than a couple of speaker applications, there are special requirements that high-performance tensioning may both speed up and provide higher precision in the coil fabrication.
Back a couple of years ago, I came across BTSR Technology, a specialized manufacturer of sophisticated tensioners, and similar to Textreme/Composite Sound, their technology and experience comes from the weaving industry. As with clothing and other fabric goods, winding voice coils also requires both speed and precision. Yank a spool of yarn or magnet wire from the feed spool and the yarn breaks (or the wire stretches a bit with a shift in the coil’s wound when the feed spool is full vs. the coil’s direct current resistance (DCR) toward the end. Their servo double closed loop is impressive and is operated by means of multiple motor controls (Photo 2).
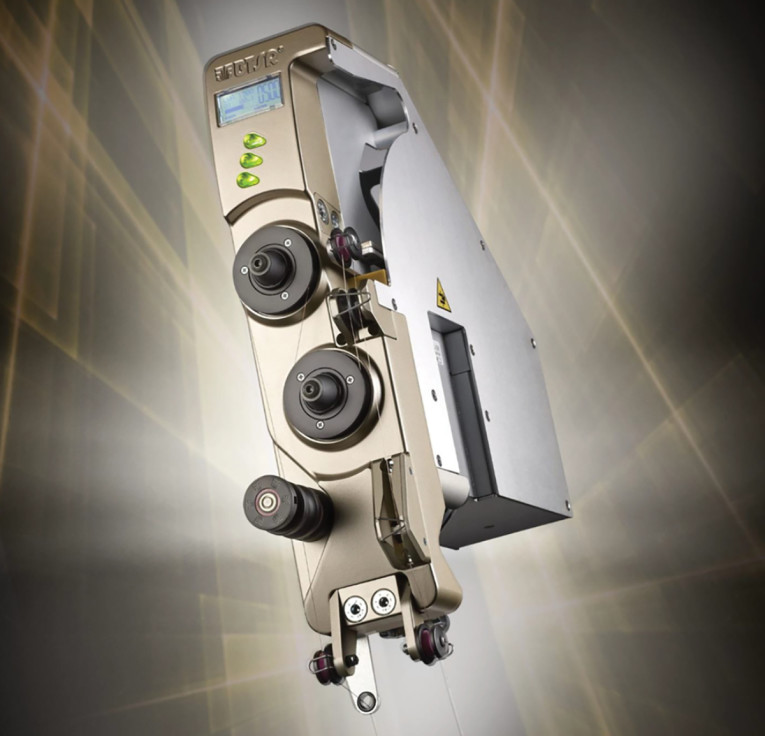
I was never involved in dress making, but for production of air coils (hard drives and solenoids), flat strip bobbin coil speakers (e.g., Resonado), square coils as in some microspeakers, wireless charger coils, conventional speaker voice coils, antennas, and RFID/NFC coils, this tensioner enables faster and more precise coils. Beyond a more constant coil, this enables a bit tighter gap, and most important, the coil winding does not jam, break, or stretch the wire, which results in a fast return of investment due to an accurate monitoring and precise wire tension control as well as lower blood pressure in the production team.
Looking at the BTSR servo tensioner, the double closed-loop technology for Motor Torque and exact length wire absorption (LWA) enables management of sudden wire absorption or release during the working process and simultaneously keeps the wire feeding tension at the set value.
Featuring simultaneous dual control on both wire feeding tension and wire running speed for a complete tension feeding control along the whole wire path (from the feed spool to the final coil) enables a wire flattening to direct coil winding, avoiding the round wire spool to flatten to the shaped wire spool followed by the shaped spool to coil winding process. Loudspeaker old timers would appreciate that an early attempt was successfully achieved at Eminence by Bob Gault a half-century ago! Being a tape deck nut, the similarities of the BTSR servo tensioner is also reminiscent to the famous Technics RS-1500 open-reel tape deck’s servo capstan drive mechanical tensioning impedance roller tape handling system (introduced in the late 1970s).
“Inverter” Magnet Wire for High-Power Speakers
Electric vehicle motors are AC while the batteries are DC. An inverter is a device that converts DC to the AC motor. The inverter can change the speed at which the motor rotates by adjusting the frequency of the alternating current. The inverter — also called an AC drive, Variable Speed Drive (VSD), Variable Frequency Drive (VFD), or frequency converter — sits between the electrical supply and the motor. Power from the electrical supply goes into the drive. There is lot going on with smoothing the output of the inverter, but even so, an inverter motor design is brutal on the motor windings. For stable long life without the magnet wire enamel insulation arcing, we now have super tenacious hi-temp enamel magnet wire from many wire vendors. Some of the wire is 10 microlayers (so the same as the single “build” thickness common for speaker voice coil wire). But some of the layers are thermoset and some are thermoplastic for “self-healing” from arcing. The inverter-grade copper and aluminum magnet wire is available in gauges for woofers — even some that are square cross-section wire.
Looking Ahead
Just over the horizon are new conductor alloys for voice coil wire conductors. Until now, there have only been a couple of options—copper, aluminum, and copper-clad aluminum. Because of its superior conductivity, annealed copper is the international standard to which all other electrical conductors are compared. Yet, the copper alloy typically used can be tweaked to lower the temperature coefficient of resistance (TCR). The temperature dependence of electrical resistance and of the Thiele-Small (T-S) parameters must be considered when considering implications for power compression to voice coil outside diameter when the coil is running hot. The temperature dependence of copper and aluminum conductors is significant when used in smartphone microspeakers or ringtones, speakerphone operation, or concert speakers. Pure copper in its International Annealed Copper Standard (IACS) is 100% IACS=58 MS/m at 20°C, decreasing by 0.393%/°C. Aluminum has 61% of the conductivity of copper. An aluminum conductor’s cross-sectional area must be 56% larger than copper for the same current carrying capability. The need to increase the thickness of aluminum wire is a consideration in its use in tight voice coil gaps—especially as it expands more than copper voice coils when hot.
Thirty years ago, noted speaker engineer Doug Button, when working at JBL, applied for a patent (5,664,023 granted in 1997) on what might be an ideal magnet wire alloy. There is still work by various engineers on a wonder wire that is lighter than copper, has a current-carrying capacity several orders of magnitude higher than copper, and behaves more linearly at high power. Count on Voice Coil to be the first place where you will read about these innovative products when they are introduced.
Finally, let me end with these words of wisdom from Jon Van Rhee who had been at Precision Econowind for much of his working life; “It seems silly, but with all the technology in the world, we are still trying to wind wire around a circular former without any hiccups.” VC
Company Resources
BTSR
Via S. Rita, 21057 Olgiate Olona (VA)
P: +39 0331.323202 | info@btsr.com | www.btsr-coil.com
Goto (see the Voice Coil Vendor Directory for other locations)
Goto California, Inc.
6120 Business Center Court, Suite F 200, San Diego, CA 92154
P: 619-691-8722 | www.goto-california.com
This article was originally published in Voice Coil, August 2024