A lightweight military aviation-grade nanocomposite from Alpine Advanced Materials, HX5 may be an alternative to beryllium and high-performance aluminum alloys used in woofer, midrange, and full-range cones. Compared to aluminum, cones can be made at half the weight with comparable strength. And the material is an obvious candidate for enclosures and cabinets in outdoor applications or portable active-lifestyle designs.
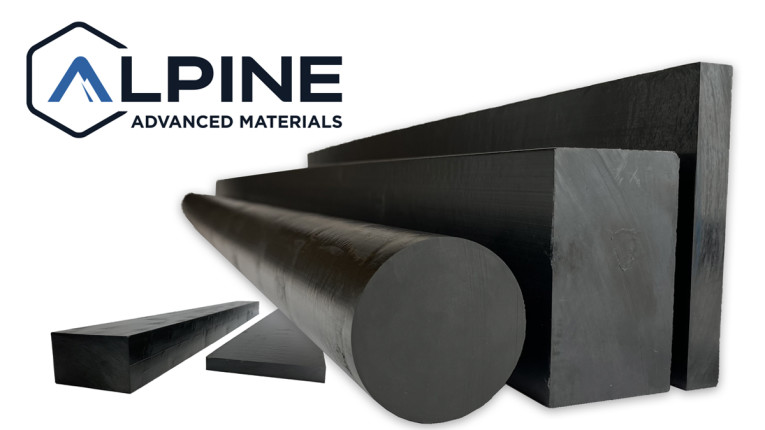
There have been quite a few high tech materials that have trickled down from aerospace and military applications, but here is one exciting material that literally has been in the stealth (fighter plane) mode but is now about to step into the spotlight.
Thermoplastics and composites have great potential, and most of these have been in the form of sheets for compression molding using a positive and negative die. The challenge for speaker enclosures has been getting a deep enough draw for forming shaped parts, and the even greater challenge is the audio industry is very much invested in injection molding, not compression molding. On the other hand, composite speaker cones are most commonly compression molded as tooling is less expensive than injection molded parts which is a consideration as there are so many variants in cone profiles.
The latest entry in this arena is HX5, a lightweight military aviation-grade nanocomposite produced by Alpine Advanced Materials (Dallas, TX), a subsidiary of Catalyze Dallas Holdings. HX5’s creator, Lockheed Martin SkunkWorks (Palmdale, CA) is known for creating the legendary SR-71 spy planes, the Lockheed-Martin F-35 stealth fighter and other awesome stuff. Alpine designs and manufactures purpose-built parts using advanced materials, focused on replacing metal with composites.

HX5 is an engineered nanocomposite material developed and tested by Lockheed Martin SkunkWorks to replace aerospace grade aluminum alloys. Used in Commercial Aerospace, Defense, Space and other applications, presents an alternative to beryllium, high-performance aluminum alloys, and conventional carbon fiber composites. With more than a decade of testing and validation with an R&D investment in excess of $50 million, HX5 has application to lightweight super-strong speaker enclosures from mobile DJ speakers, touring sound arrays, outdoor speaker enclosures to very high-performance injection molded or extruded compression molded speaker cones.
While we do not get to take a deep look “under the hood”, I can say that HX5 is a proprietary nanocomposite of an engineered resin system with reinforcing carbon fibers and “other” secret sauce nano-ingredients. Compared to aluminum, parts can be made at half the weight with comparable strength to today’s most advanced aerospace aluminum alloys.
While Alpine’s HX5 does require changing the manufacturing process, it enables designers to convert from metal to a material that allows gains in production and improve the quality of finished products. This combination allows manufacturers to achieve superior prototypes, even when injection molding is involved. While cost-effective for production, injection molds aren’t normally efficient for prototyping and are only viable after a design is finalized. 3D printed parts for prototypes typically have poor acoustical properties. With HX5, the injection-molded prototypes can be affordably extruded or machined, and tested to anticipate the performance of the finished product.
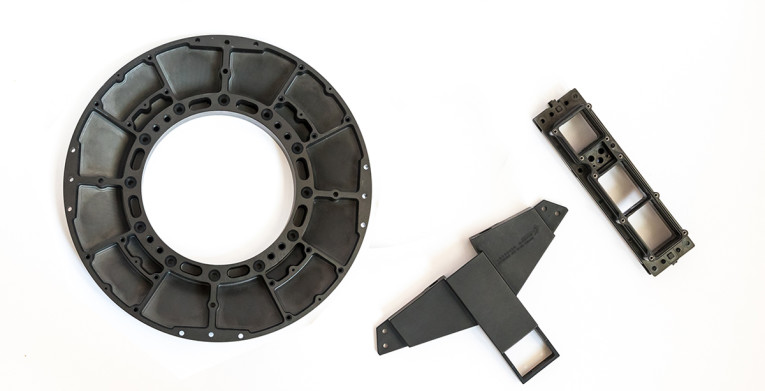
Molding and Secondary Processes
HX5’s low viscosity has the ability to flow in very thin sections and highly complex shapes where other similar materials can’t – facilitating very intricate designs such as speaker diaphragms, thin wall enclosures, and compression driver phase plugs. Low shrinkage rate (.5%) means tighter tolerance parts, and constant cross-section for extruded parts.
The material coats extremely well for both decorative and functional applications due to its high surface energy and the ability to cure at higher temperatures. These include mundane coatings like painting, but also metallic plating for EMI shielding, electrical and thermal conductivity. While not related to the audio market, the aftermarket car market can have radar absorbing car hoods to keep your speeding tickets down. And HX5 is compatible with insert molding/overmolding and with various joining methods from ultrasonic welding to adhesive bonding and mechanical fastening.
Alpine is also available to help on the conversion process, with the advantage that the use of finite element analysis (FEA) and simulation will be more directly reflected in the prototype stage by directly controlling the design topology optimization even at the detail of fiber orientation. Something that is proving increasingly effective in loudspeaker design.

Bring on the Sun, Rain, and Weed Whackers!
Another reason to look very closely at HX5 is to do with outdoor applications, such as for garden speakers. HX5 survives the harshest environments – and if you think of selecting a plastic that is tough to meet the challenges of the UV resistance needed by your garden speakers to survive years of summers and winters, imagine the ballistic requirements for a stealth fighter. Let’s start with HX5’s extreme temperature tolerance of -65° up to 500° Fahrenheit. Also, extreme resistance to solvents, fuels, lubricants, and chemicals as well as non-hygroscopic.
While most of us may have to design for outdoor speakers, there is also HX5’s radiation resistance to UVA, UVB, UVC and Gamma wavelengths. So if your speakers are used out in the sun and you design with a material suitable for a nuclear powered unshielded spy satellite, you can bet your HX5 speaker enclosures and cones won’t degrade.
HX5 meets rigorous guidelines for flame, smoke, and toxicity (FST) and while most of us are not designing speakers for commercial aircraft or spy satellites, ceiling speakers have similar FST issues. Specifically, ceiling speakers in plenum spaces are a critical firewall barrier from smoke spreading throughout a building in a fire. Typically, dropped ceilings facilitate the air return for circulation for heating and air conditioning systems. These pathways for return airflows, usually have greater than atmospheric pressure, and if the ceiling speaker back-can succumbs to burning, then the smoke from the room fire can be a fatal flaw. Drop-ceiling speakers must meet stringent UL requirements for protecting the return air path for HVAC from smoke during a fire.
For headphones, HX5 also looks to offer superior creep and fatigue resistance than Nylon 12, the incumbent solution with exceptional compression and tension performance at a wide range of temperatures as well as keep the tension on your head the same throughout a long flight.
Independently of the application, this is a material that could prove effective to generate completely new levels of product optimizations. aX
For additional information about HX5, please visit:
www.alpineadvancedmaterials.com
Or send an Email
This article was originally published in audioXpress, January 2022. This article is an extract of an extensive Market Update feature on speaker technology.