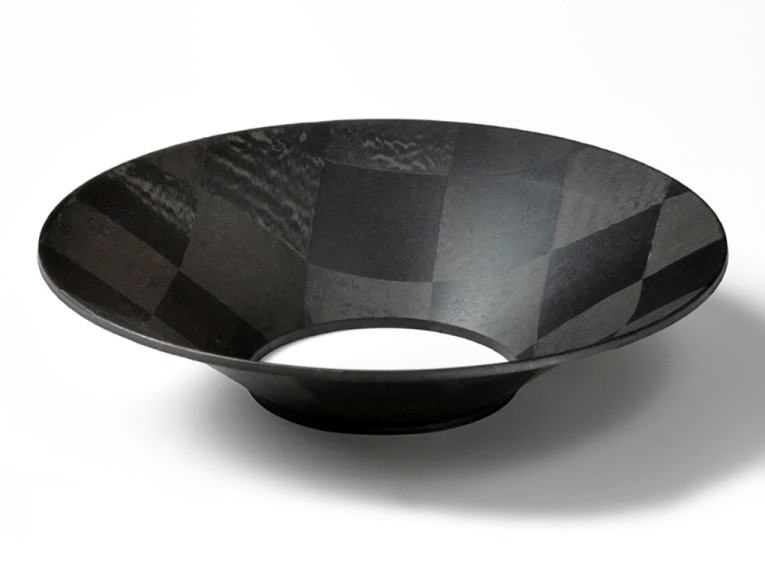
The issue is that the typical carbon fiber yarn used for woven cones is too thick and to fix the shape and seal the cone too much epoxy binder is needed. The resulting existing construction is a superior cone, but it is limited to woofers and midranges. While there has always been the promise of carbon fiber compression drivers, super tweeters, and headphone diaphragms, the carbon fiber would have to be finer than linen.
Oxeon’s Thin Ply Carbon Diaphragms
Welcome to 2019. Oxeon of Sweden has introduced thin ply carbon diaphragms — a new category of speaker diaphragms based on its TeXtreme thin ply carbon reinforcements (see Photo 1). Founded 15 years ago, Oxeon is an advanced composites fabrication specialist and holds patents both for its technologies and unique materials. A thin ply carbon material is created by arranging layers of carbon fiber in an optimized manner.
Materials can be anisotropic with the same properties in all directions (e.g., molded paper cones), while commonly extruded materials, such as thermoformed poly (PP) cones, and film diaphragms (e.g., those for tweeters, headphones, and microspeakers) can have a machine direction (MD) or even be biaxially oriented such as those in some polymer films used in tweeters and headphones. The properties of thin ply carbon materials can be application-specific and tailored in different directions from cross-ply 0/90, but also tri-axial offset plies and more. By optimizing the way the layers are organized, mechanical performance can be maximized, weight minimized, and the part can be engineered to behave in certain desired ways in different areas and different directions.
The speaker cone breakup modes can be reduced by breaking the symmetry in the diaphragm, as Bowers & Wilkins pioneered with its well-known yellow aramid (Kevlar) cones or as Scan-Speak does with its elliptic voice coils. With thin ply carbon diaphragm technology, this can be taken several steps further and applied to high-frequency diaphragms. Not only is the symmetry broken, but the fiber architecture can be engineered to optimize and control the breakup behavior. For example, if stiffness in one direction is preferred, then more fibers in that direction are used — and might be beneficial in an oval headphone driver or “race-track” smartphone speaker diaphragm, providing controlled and precisely defined characteristics. Defining the characteristics throughout the membrane to suppress modal buckling will enable the design engineer to avoid the usual notches in response of shallow diaphragm transducers.
Application Specifics
Thin ply carbon diaphragms are application-specific anisotropic and, therefore, have varying stiffness over the diaphragm area and in different directions. By optimizing the fiber architecture, the symmetric breakup modes are replaced with more but smaller and local breakup modes. This creates a distributed breakup with smaller peaks in the frequency response and ultimately smoother and more natural sound without harshness.
Oxeon engineers advanced composite constructions to fully exploit the potential not only being as light and stiff as possible, but also to behave in certain ways when subjected to a load, excitation, temperature or other variables. Initial applications required the absolute highest performance in combination with ultralight weight from cryogenic tanks for space applications, the next generation of commercial airplanes and Formula One cars, and ballistics. Consider the form of seats for commercial airplanes—while having the ultimate goal of being as light as possible, they must behave in certain ways when subjected to extreme forces. Or consider a golf driver head that should maximize the speed of the ball in a controlled manner while producing the right sound when impacted.
Speaker Diaphragm Tests
Next, the Oxeon team wanted to explore whether these same attributes could be used in speaker diaphragms to help improve the sound quality by enabling a combination of high breakup frequency with controlled breakup behavior for low distortion and freedom from ringing and self-noise.
Oxeon talked to the audio industry to understand the conditions and challenges faced when developing loudspeakers. “The more people we spoke to the more we felt they were looking for the things we are specialized in — ultralight weight and high mechanical, tailored performance,” says Martin Turesson, Head of Thin Ply Carbon Diaphragms at Oxeon. “Initial basic simulations of thin ply carbon diaphragms showed that the breakup frequency could be pushed up considerably, but we didn’t know how they would behave when finally breaking up, even less how they would sound.” There were concerns that, given that they were stiffer and with a considerably lower density than aluminum, that they would breakup badly and sound harsh.
Oxeon decided to manufacture thin ply carbon diaphragms, have them built into drivers, measure and listen to them. Oxeon teamed up with a major audio company and made ten 80 mm midrange cones to compare with their premium aramid (Kevlar) midrange cones. Measurements showed a considerably pushed up breakup frequency and a smooth frequency response curve. Turesson said, “Then we knew the thin ply carbon cones measured well, but how would they sound?” In listening tests, the acoustic team of one of the audio companies in the trials concluded that the sound quality was considerably improved compared to their premium aramid cones. In the words of the acoustic engineers: The sound was cleaner, more detailed and had a better room representation. Details in the music that were not audible in the aramid cones (e.g., the light tap on the cymbal, were now clearly heard using the thin ply carbon cones. The placement of the musicians was much clearer with no “holes” in the stereo imaging.
“This is when we knew we had something,” Turesson said. Most surprising was the sound, despite being clear and detailed, was not at all harsh but smooth and natural. How come they could sound so smooth despite the high stiffness and low weight?
Controlling Breakup
Speaker diaphragms should be light and stiff to allow for pistonic movement. For a number of variables, such as diaphragm geometry and topology (size and shape), the speed of sound of the material itself and the size of the diaphragm vs. the wavelength dimensions, the diaphragm will breakup at some transition frequency. The higher the Young’s modulus (speed of sound through the material) the higher the frequency point where the response gets jagged and we have seen this transition point in the response curve in all the speakers with which we work. If the diaphragm material is well damped the response anomalies will not be severe but in a poorly damped material (e.g., titanium), the breakup will result in trashy self-noise (stress noise) rattling/ringing and the corresponding irregular response.
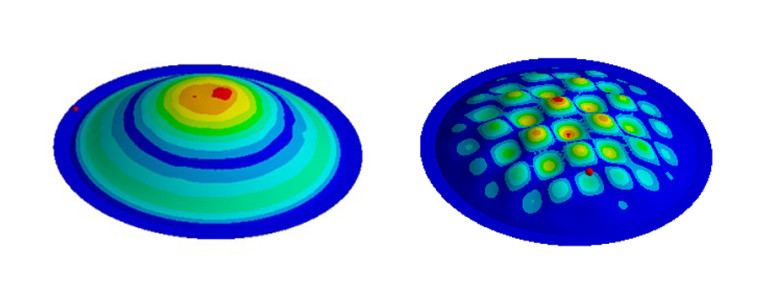
Traditionally, the effects of the breakup can be reduced by increasing mass (damping) but the stiffness is reduced by loading on constrained layers, damping goop, etc. Consider the analogy of a silk scarf compared to aluminum foil — and in the case of speaker diaphragms, the noisy rattling generated by the aluminum foil (titanium would be worse) would be an “after taste” imposed on the audio, masking the more subtle elements of the signal.
Compression drivers are another significant application where thin ply carbon diaphragms could provide real benefits. Consider that titanium’s poor internal damping haunts design engineers, but we have been stuck with this for its toughness and extended (but nasty) response characteristics. A light and tough but not trashy sounding material would be wonderful and being able to put a bit more meat strategically at the right sectors of the diaphragm is a huge advantage.
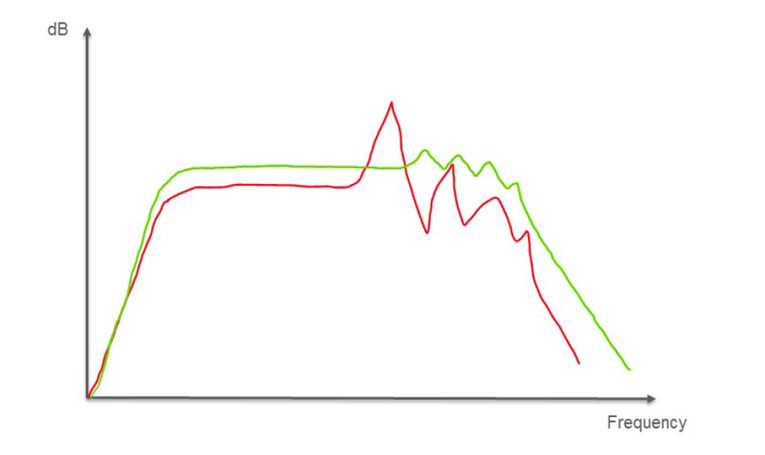
Figure 1 depicts the effect of the controlled breakup as exemplified in a compression driver diaphragm. The first breakup mode of a 3" titanium compression driver diaphragm can be seen to the left and a thin ply carbon diaphragm on the right. The few big, symmetric breakup modes of the titanium diaphragm are replaced by many small and local breakup modes in the thin ply carbon diaphragm. Lower amplitude and higher frequency breakup tend to have a faster settling time. The same effect applies for thin ply carbon cones and tweeter domes.
The effect on the frequency response curve can be seen in Figure 2. The big peaks of the titanium diaphragm (in red) are replaced with more but smaller peaks in the thin ply carbon diaphragm (green). Furthermore, higher stiffness to density ratio as well as the distributed breakup is shown as the breakup is moved up in frequency. The lower moving mass of the thin ply carbon diaphragm results in higher sensitivity.
Potential of Thin Ply Carbon Diaphragms
Thin ply carbon is not one material with one set of properties, it is a technology that enables the engineering of an infinite number of materials with different properties that can be constructed in diaphragms in yet an infinite number of ways. That enables it to be optimized and used for a large number of speaker diaphragm applications.
The combination of ultralight weight, high stiffness, and controlled breakup behavior could provide immediate benefits for mid- to high-frequency applications (e.g., tweeters, compression drivers, midranges, and full ranges). One customer had an aluminum alloy tweeter and wanted to reach the high-resolution target of a 40 kHz breakup. The aluminum alloy diaphragm could reach just around 25 kHz. Simulations for thin ply carbon diaphragms showed very promising results, indicating a breakup frequency above the 40 kHz target while staying below the original diaphragm’s weight. It was decided that prototypes were to be made, measured, and listened to. After being built into drivers, the thin ply carbon diaphragms did show an increased breakup frequency compared to the original diaphragms but not to the extent the simulations showed.
A deeper analysis showed that it was not the thin ply carbon diaphragms that did breakup; it was the voice coil former. After a new assembly was made using a higher-performance former, the measurements matched the simulations and a breakup frequency meeting the 40 kHz high-resolution target was met.
Another customer had an aluminum full-range cone speaker with a severe breakup well within the audible frequency range. The breakup also resulted in clearly audible distortion at lower frequencies. The customer wanted to know if it was possible to push the breakup outside the audible frequency range (above 20 kHz) as well as make it smoother to reduce harmonic distortion. The thin ply carbon diaphragm were able to achieve pistonic movement above 20 kHz. Thanks to the distributed and smoother breakup, harmonic distortion at lower frequencies were dramatically reduced for a clear and smooth sound.
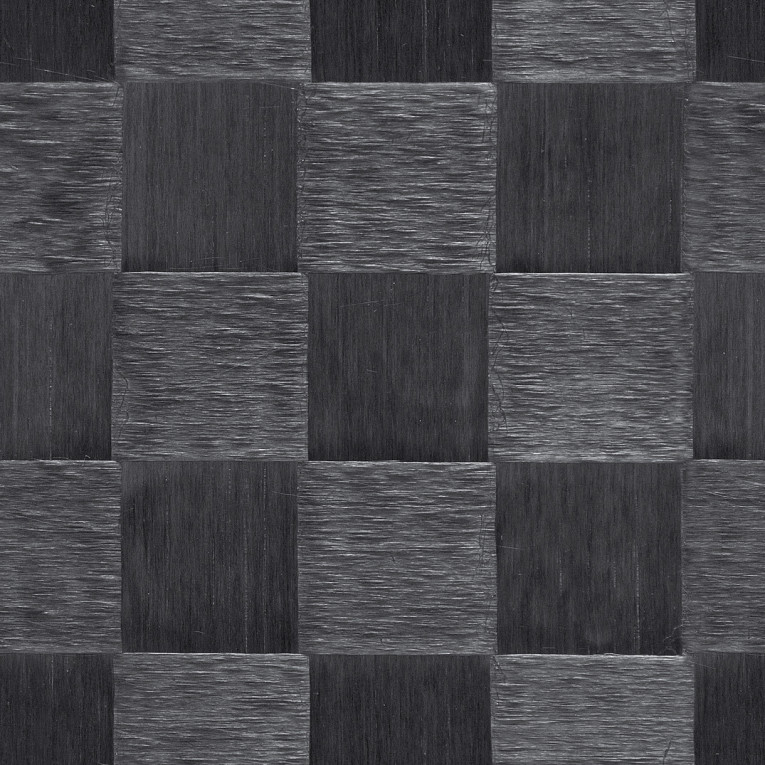
Conclusions
Thin ply carbon diaphragm technology offers great flexibility when it comes to performance and cost, enabling it to bridge the gap between esoteric solutions (e.g., beryllium) and more mainstream types of solutions such as aramid, titanium, and aluminum or the usual paper or polymer diaphragms.
Oxeon is working with the speaker industry to evaluate the potential of the thin ply carbon diaphragms for those interested in the technology. Its approach is transparent and realistic — with the first phase of the evaluation being simulation-based, meaning it is possible to get a good view of the potential performance quickly and efficiently. If the simulation results look interesting, the next step is to sample diaphragms into prototype drivers to properly measure and listen to them.
The flexibility of the technology enables a high degree of optimization to the specific customer’s requirements for truly tailored and customer unique solutions. Voice Coil readers who want to see the potential of this technology in their applications can contact Martin Turesson, Head of Thin Ply Carbon Diaphragms at Oxeon.
www.textreme.com/markets/audio. VC
This article was originally published in Voice Coil, February 2019.