Injection-molded thin-wall lightweight plastics give designers more flexibility to achieve aesthetic and efficient assembly goals but at the expense of sonic integrity. We are faced with cheap plastic soundbars made of flimsy thin-wall plastic construction and table radio sound. Perhaps large-screen TVs provide enough distraction from the lack of sound quality, but Bluetooth speakers, in-wall and ceiling speakers, headphones and earphones, and smart-speakers are typically injection-molded plastic. ABS, HIPS, PC, Poly, and other plain materials dominate today’s speaker enclosure products.
Yet, the sound reproduction and perceived quality is a direct function of the enclosure materials and construction. In the first part of the article series, we discussed that aside from the acoustic aesthetics, enclosure resonances degrade acoustic performance acoustic feedback where the enclosure contributes to the speaker system’s peaky response and those peaks trigger acoustic feedback in sound systems with an open mic. Higher tan delta, which is the internal energy absorption within the material itself, keeps the Q of the resonances tamed. Drop the Q of the loudspeaker’s peaks through more heroic ribbing in the right spots and/or more highly damped materials and this enables more gain before feedback.
Enclosures should suppress vibrations that ripple through them and provide higher sound transmission loss (a measure of how good a barrier the enclosure is to prevent sound from passing through it). Higher stiffness is needed to drive resonances into higher frequencies where they are more easily controlled.
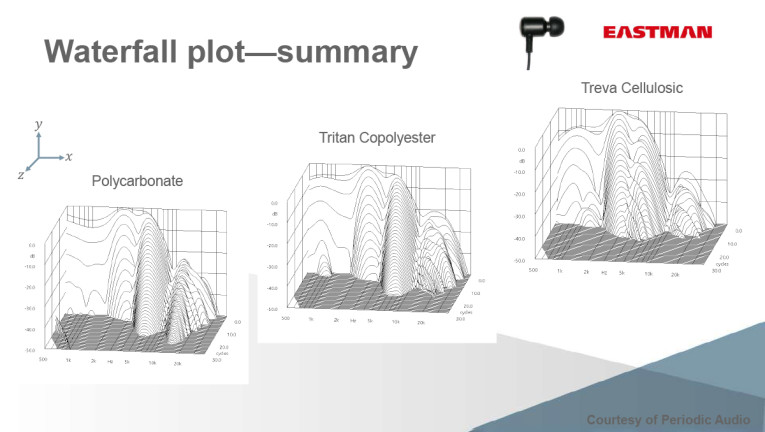
For improving the acoustics of injection-molded products that are already tooled, the obvious solution is the selection of a more damped plastic. Yet not so fast. In the real world switching out plastic resins can get complicated as the net part shape may change even from the same tooling due to shrinkage after molding. Other characteristics aside from damping also count—don’t forget impact strength, flow in the tool, moisture sensitivity (some plastics require storage with humidity control, and more dry time in the hopper, and so forth.
While working on a project for a two-way direct woofer, compression driver/horn portable speaker, the system’s response showed a peak and high distortion around 1 kHz. But this spurious stuff was coming from the horn, which was cut 18 dB octave below 1,200 Hz! When the compression driver was disconnected, the distortion from the horn remained! The woofer was causing the horn bell to resonate. None of this is news to speaker designers, but I think many people would be surprised at how much quality is lost to the spurious contributions due to ABS and other commodity plastic components.
Material Testing
Eastman Chemical has two thermoplastics with higher damping than polycarbonates and ABS. Its Tritan copolyester has good appearance, clarity, toughness, hydrolytic stability, and heat and chemical resistance. Free from BPAs (plasticizers), so contact with skin, earphones, or food is not an issue and even the molded release is derived from vegetable-based sources.
Eastman Trēva is a cellulose-based engineering bioplastic that offers both superior damping and reduced environmental impact. Trēva is chemically resistant, dimensionally stable, and has excellent flow, and it is BPA-free. Eastman undertook acoustic testing of molded in-ear monitors using cumulative spectral decay (CSD) 3-D waterfall and total harmonic distortion (THD) along with an expert panel of listeners to evaluate the role of materials on resonance, distortion, and perception sensitivity (see Figure 1).
Damping loss factors were compared for Eastman Tritan copolyester, Eastman Trēva engineering bioplastics, and the incumbent polycarbonate (PC) and ABS resins. A frequency generator created vibration at the center of rectangular test bars. An accelerometer measured the motion of each bar as the input vibration traveled through the part. The damping loss factor (tan delta) was determined from the comparison of vibrational damping capabilities of direct comparisons between the different test materials molded with the same geometry. Tritan and cellulosic (Trēva) demonstrated faster settling times compared with PC and ABS with faster settling time.
Eastman also conducted subjective listener testing to determine whether changing enclosure material provides a discernible benefit for audio engineers, designers, and consumers. For expert listeners, the differences between the in-ear monitors (IEMs) were “subtle but audible and consistent.” Other interesting comments noted differences such as: reduction of sibilance, resonance is toned down, and reduction of “buzzyness.” The majority of improved listener experiences favoring copolyester and cellulosics correlated with faster decay of the waterfall plots and reduced THD. Eastman will be building on this work, beginning with understanding other applications where vibration damping materials could enhance audio performance and provide value to its customers.
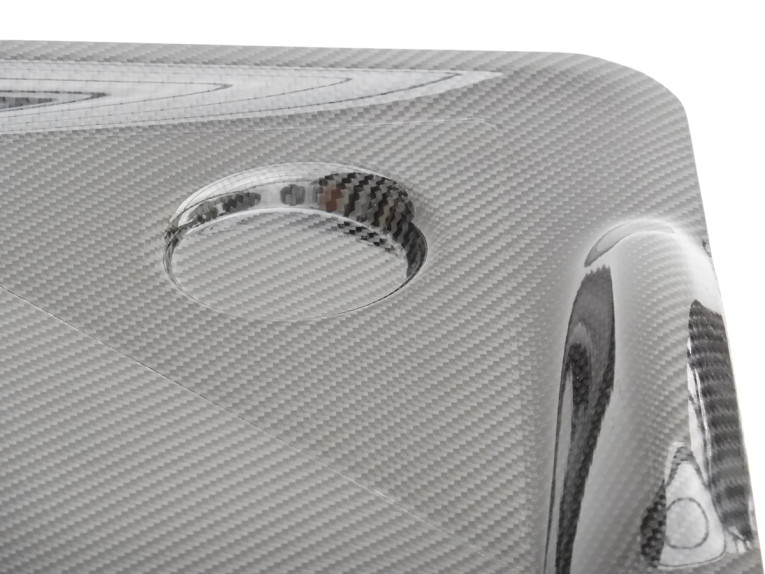
INEOS Styrolution is introducing Stylight aesthetic and structural thermoplastic composites for woofers, mid-range cones, and compact full-range drivers for smart speakers and soundbars (see Photo 1). Stylight is a thermoformable sheet (positive and negative molds). The sheet is comprised of two key components—a fabric (e.g., woven carbon fiber or woven glass) and a resin (e.g., styrenic copolymers) for enclosures and most recently, polypropylene for speaker cones (see Photo 2).
Obviously, the Stylight sheet thickness optimum for enclosures versus speakers will differ with a range of 0.25 mm up to 2 mm. While the fiber fabric plays a key role in the material’s mechanical performances, the polymer matrix has a great influence on the part surface aesthetics. Stylight offers the low “surface waviness,” allowing high-gloss surfaces direct from the molds, but it is also easy to paint or decorate with foils. The translucency of natural StyLight enables backlighted surfaces or a “carbon fiber look.” Stylight is a new combination of aesthetic and structural stiffness, low weight, and cost-efficient production.
Thermosets and Thermoplastics
Thermoset plastics and thermoplastics have very different properties and in consumer electronics, thermoplastics have the lion’s share of the market. Thermoplastics can be remelted back into a liquid, whereas thermoset plastics are cured into a permanent solid state. Think of thermoplastics (HIPS, ABS, PC, PP, nylon, etc.) as being similar to butter — butter can be melted and cooled multiple times to form various shapes.
Thermoplastics are typically injection-molded into shaped parts although thermoplastics can be the binder for woven glass, Kevlar, carbon fiber and tapes. Once the final state is achieved, any additional heat beyond would lead to charring. Thermoset plastics contain polymers that cross-link together during the curing process to form an irreversible chemical bond. The cross-linking process eliminates the risk of the product remelting or warping when heat is applied.
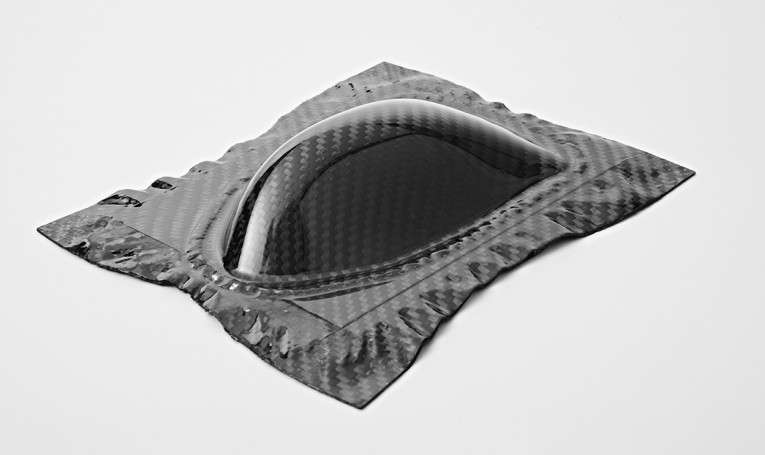
Bulk-Molded and Sheet-Molded Thermosets
Bulk-molded compound (BMC) composite (compressed of glass fiber, talc, mica, etc.) can be molded into enclosures. BMCs were traditionally compression-molded in a positive and negative tool with curing times longer than thermoplastics. BMC offers good acoustic performance, in part because of the high-density material and easily molded ribs, making it practical for radiused edges and baffles.
Long ago, brands such as Polk and NHT, among others successfully used this material. These days, cost-sensitive products (soundbars, smart speakers, and in-walls) cannot defend the higher cost of goods versus inexpensive ABS and other commodity injection-molded, thin-wall plastics. The serious higher grade soundbars with immersive sound would appear to be a good fit for these materials.
Industrial Dielectric (IDI) is a long-established producer of BMC and SMC materials. IDI’s engineers have expanded its line of Structural Thermoset Composites (STC) with the introduction of Fortium, a high-glass-based composite material, and Ultrium, a carbon fiber-based composite material. Fortium and Ultrium STC enables product designers and engineers to bridge the cost and performance gap between lower performing traditional materials (e.g., metal) and higher cost advanced composites. Fortium and Ultrium possess exceptional stiffness and strength and STCs provide greater design flexibility at a lower price than an advanced composite and at a far lower density than metal.
A.Schulman, a long-established supplier of resins to the speaker industry has a comprehensive product line of thermosets, both BMC and SMC. Now A.Schulman has been acquired by LyondellBasell, one of the largest plastics, chemicals, and refining companies. Its Premi-glas vinylester glass fiber composite is intended to compete with magnesium alloys more than injection-molded plastics.
Damping properties of Premi-Glas was tested to have twice the superior damping compared to pure magnesium and two magnesium alloys (AZ91, AM50, Cp-Mg). Globe Plastics is a fabricator of BMC-molded speaker enclosures, horns, and other parts, and its products are well-established in the audio market. The material has extreme temperature tolerance and is weather resistant enough for speakers permanently installed outdoors.
Racing cars and dream cars from Lamborghini, Ferrari, McLaren, and such have a high carbon fiber content. Over the years, touring sound speaker engineers, crazed with the design requirements for huge line arrays have looked to carbon fiber composites for rigid, lightweight, and well-damped enclosures. This construction was a nightmare for joints and speaker and hardware attachments.
Now we have Maezio, the next generation of continuous fiber-reinforced thermoplastic composite (CFRTP) from Covestro. Made from carbon or glass fibers mixed with polycarbonate (PC), thermoplastic polyurethane (TPU), or other thermoplastic resins, Maezio products are made as unidirectional reinforced tapes and sheets for formed sections that would, for example, result in lightweight, durable, aesthetic headphone headbands. For deeper draw parts such as ear cups, choppedcMaezio can be injection molded (from manufacturing waste from sheets). Covestro, formerly Bayer Material Science, is a world-leading supplier of high-tech polymer materials (see Figure 2). Covestro has addressed the main issues surrounding the production and use of composites—cost-effectiveness, scalable manufacturing of a high-performance, sustainable material.
Maezio works with existing thermoforming tools at high yield rates and low cycle times—a feature that can be vital when manufacturing scales are in the range of millions of parts per year. Other production technologies appropriate for Maezio include hybrid injection molding, automated Uni Directional tape laying, and automated fiber placement. Maezio is offered in a range of finishes from colored and textured, to black and glossy, to matte, and untouched unidirectional fiber. Covestro is providing Maezio materials for application-specific evaluation and confirmation trials.
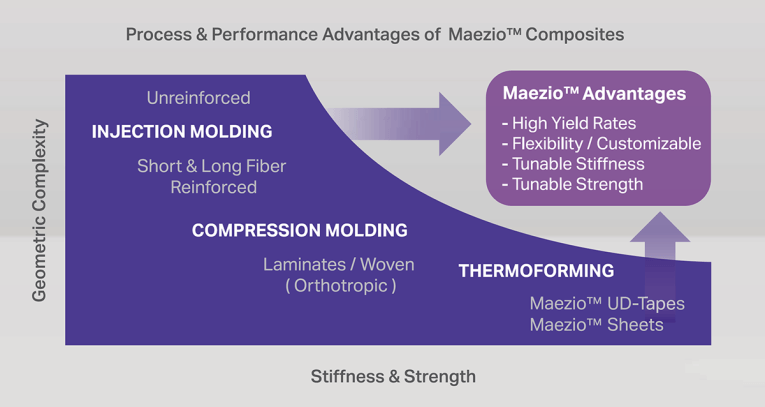
Factory Evaluation of Manufacturability
Attributes that are important to the factory when considering new materials include injection-molding cycle time, compatibility with existing tooling (if the spring-back shrinkage is different than the existing plastic the tooling will need modification), flow in the tooling, moisture absorption (drying time in the hopper), and material cost per part. Other issues range from painting (polypropylene has good attributes but there is a reason that glue bottles are made from poly—it is hard to stick to or metalize). Plastics with carbon or other conductive fill block antenna reception.
For the product managers, considerations such as surface finish, impact resistance, temperature tolerance, and acoustics must be taken into account. Chemical resistance is important if the product will be exposed to sweat—such as in wearables—and even tougher is detergent cleanup. There is also a demand from brand owners and consumers for electronic products with reduced environmental impact and greater sustainability. VC
This article was originally published in Voice Coil, May 2019.
References
Eastman Chemical - www.eastman.com
INEOS Styrolution - www.ineos-styrolution.com
Industrial Dielectric (IDI) - www.idicomposites.com
A.Schulman - www.aschulman.com
LyondellBasell - www.lyondellbasell.com
Globe Plastics - www.globecomposites.com
Covestro - www.covestro.com