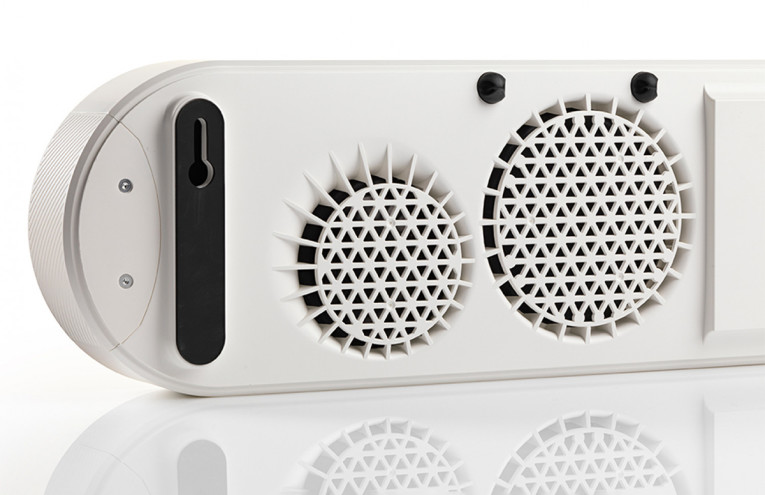
Wood and wood particle board cabinets were traditionally used for speaker enclosures, but that is mostly in the rearview mirror. Back in the 1970s, plastics were relegated to table radios, “transistor” radios, “shoe box” cassette recorders, and other inexpensive electronics. That has changed in a big way for various reasons, one being that back then plastic tooling costs for upscale audio products could not be amortized by the product sales numbers. Now, consumer audio electronics are mainstream and global, and the quantities are huge.
The days of the US union machine shops and hand tooling on lathes are history. Today, tooling for injection molds for plastic parts are done on computer numerical control (CNC) machines directly from 3D CADs in China from very efficient specialists, and the costs are reasonable.
Over the years, there has been great interest in finding alternatives to wood enclosures. The ideal material to replace wood construction should be as strong, light, and thin as plywood and for these reasons injection-molded plastics dominate audio these days. Simplified construction is another consideration as moldable material eliminate most joint assembly and enable rounded edges and shaped front baffles minimizing edge diffraction, time alignment, waveguides, as well as esthetic flexibility.
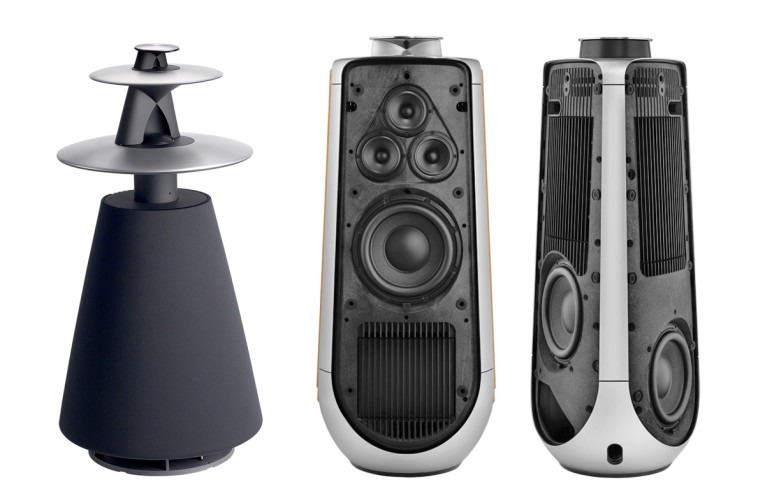
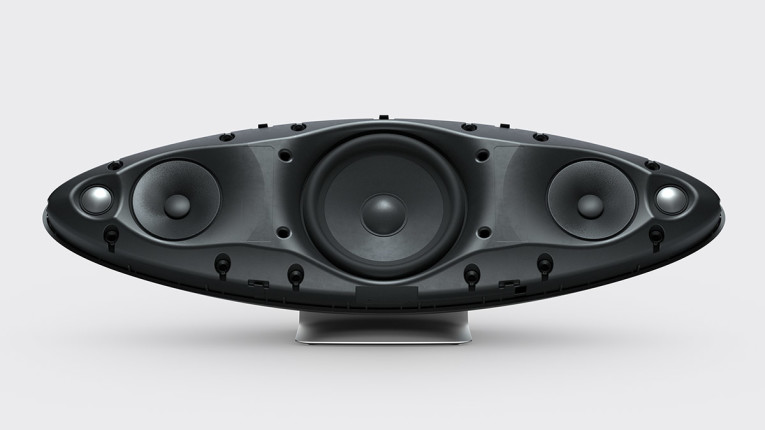
Injection-Molded Plastics
Due to their stylish shapes and consistency along with an established supply chain and well-known design rules, injection-molded plastics are hard to beat. Moldable materials give speaker designers more flexibility to achieve aesthetic and technical goals. To achieve an optimum engineered design for a more precise or “focused” soundstage, the drivers’ acoustic centers should be acoustically aligned, which is especially beneficial in the vicinity of the crossover frequency. The molding of a tweeter horn/waveguide is a useful tool to control directivity, increase sensitivity, and provide for the time alignment of the acoustic centers of the woofer and tweeter in the crossover band. Elegant contouring can avoid the sharp edges that cause diffraction for smoother response. None of this is easy nor cheap with wood construction.
Dramatic enclosure styling that combines unique materials and forms takes engineering and marketing courage, but the rewards can be great. Consider Bowers & Wilkins (B&W) distinctive Nautilus 800 series, a breakthrough in style and performance in the late 1990s. When introduced, the Bang & Olufsen Beolab 5 (Photo 1) and the B&W Zeppelin’s iconic looks (Photo 2) enhanced each company’s Brand recognition. Yet injected-molded products of plastic are still perceived as “cheap” and most have tolerable but mediocre acoustic characteristics.
The Bluetooth speakers that are so popular have enclosure panels that resonate and whatever bass that can be eked out of their small speakers is further reduced through losses by enclosure “barrel” flexing as all the walls balloon together. Put in a hefty amplifier, some needed bass EQ, along with a decent speaker and the plastic enclosure will just rattle louder. Enclosures should suppress the vibrations that ripple through them while provide higher sound transmission loss (a measure of how good a barrier the enclosure is to prevent sound from passing through it).
Most plastic enclosures have high levels of breakthrough. This is from the speaker’s back-wave sound energy passing right through the enclosure shell and is measured as in building construction room to room isolation acoustics as sound transmission loss (STL).
Higher STL is the measure of the barrier the enclosure has to prevent sound from passing through its walls. When driven hard, cheap plastics contribute too much of their own “self-noise” from rattle resonances and creaking (stress) noise, further degrading sound quality, the “acoustic aesthetics.”
One solution is increased stiffness to drive resonances into higher frequencies where they are more easily controlled. A good place to start is a combination of stiffer plastics and designing in ribs at the panel break-up points. None of this is news to experienced speaker designers. There are plastics that we will discuss in this report that are better behaved than the commonly used Acrylonitrilebutadiene-styrene (ABS) or polycarbonate (PC), but first let’s take a brief look at the incumbents...
ABS is the go-to low-cost thermoplastic that offers both acceptable impact and at least moderate chemical resistance. The heat resistance of acrylonitrile-butadiene-styrene is lower than that of polycarbonate. Like polycarbonate, halogen containing additives may be used to increase resistance to burning (flame retardant denoted by “FR”). PC is a rigid thermoplastic that provides visual clarity, toughness, and good heat resistance. By itself, polycarbonate has reasonable resistance to burning, and that resistance increases by adding flame retardants that are typically halogen-containing. Not an issue for a speaker box, but today most devices have a power supply and amplifier, and most pass scrutiny by UL. Even some quality resins, such as styrene (SAN) have flammability issues for use in laptops, smartphones, soundbars, and other integrated electronics.
Blending ABS and PC is the first step in upgrading the resin formulation and this approach is common in consumer electronics housings. Unlike PC alone, alloys of PC+ABS result in a better flow through the tool. PC+ABS materials are very tough although not as strong as PC alone and also have higher heat resistance than pure ABS. A “nonhalogen” flame retardant technology is used in some FR PC/ABS blends, which expands the applications.
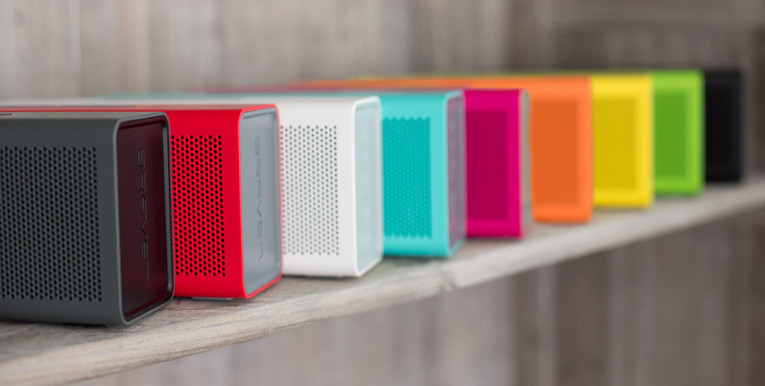
Today, ABS plastic resins dominate commodity consumer electronics, but they have mediocre acoustical characteristics. Filled ABS usually requires painting, and even then, the surface finish can be an issue. Higher-grade resins, such as polyetherimide (PEI, which you may know as Ultem), are costly and the injection-molding temperatures require expensive special high-temperature steel tools.
Aside from the acoustic aesthetics, the resin characteristics impact enclosure resonances and can improve or degrade the full-duplex acoustic echo cancellation (AEC) performance when speakers and mics inhabit the same space. High Q break-up modes in the enclosure are excited by the speaker and the peaks set off panel resonances, which can trigger the AEC running out of margin, both through sound and vibration reaching the mic from the speaker. A comparable issue is acoustic feedback where the enclosure contributes to the speaker system’s peaky response, triggering acoustic feedback. Drop the Q of the peaks through more heroic ribbing in the right spots and/or more highly damped materials and this enables more gain before feedback. For injection-molded products that are already tooled, the obvious solution is a more acoustically damped selection of plastic.
Most speaker engineers feel they are stuck with the hollow, buzzy sound that comes from plastic speaker enclosures and we will discuss the best of plastic resins. Yet, most acoustically interesting materials struggle to gain acceptance in the consumer electronics supply chain.
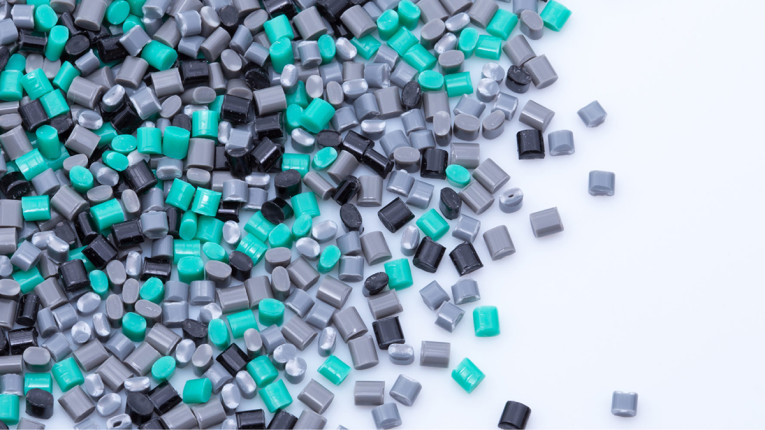
Supply Chain
Having spent more than 35 years crawling through Asia to introduce new materials into the supply chain, it is the factory production managers who are always concerned about changes, and for good reason. Perhaps intuition, or just still open wounds, but there are good technical reasons to be cautious. But how do you judge the potential cost of new materials and processes? The science of this is known as diffusion of innovation theory. The challenge is about effectively developing strategies for the introduction, optimization, and acceptance of new technologies and materials.
The five main factors that affect the diffusion of innovation include the relative advantage, compatibility with existing processes, complexity, trial ability, and communicability. Each enhancement to the selection and type of material typically has hidden problems when changing materials and processes. As this is an article in itself, it is enough to just mention this here.
By definition, premium ingredients have a price by weight, but there are less apparent cost drivers than dollars per kilogram when selecting resins. For example, lighter and stronger resins such as Covestro Bayblend’s polycarbonate + ABS have high flow and high stiffness enabling thin-wall construction for less material—so if after tooling you find your enclosure walls too thin, then the next step is to consider this option as “the good stuff.”
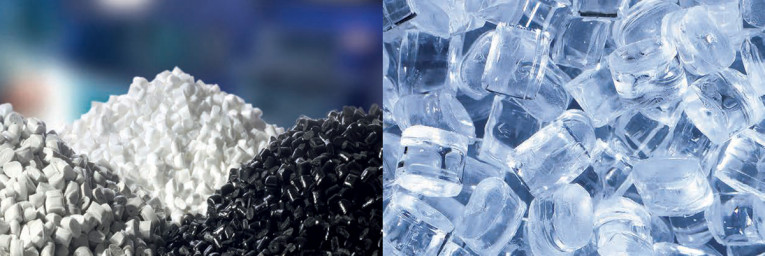
Design to Manufacture (D2M)
Attributes that are important to the factory in considering new materials include injection-molding cycle time, compatibility with existing tooling, flow in the tooling, moisture absorption (drying time in the hopper), and material costs per part. Another issue is painting (polypropylene has good attributes but it is hard paint or metalize). Also, plastics with carbon or other conductive fill block antenna reception.
The shrink rate of resins must be evaluated when considering changing to another resin with existing tooling as differences in shrink during cooling may require the tooling to be touched up. Then there is resin viscosity as thin sections that filled properly with an ABS might not do as well with a lower flow resin.
Glass-filled resins deliver high strength, but tend to have a less than wonderful surface finish and chew up the tool and other components of the injection-molding machines. Another finishing consideration is whether the part out of the tool needs painting? Polypropylene has good acoustics, but is tough to get the paint to stick—requiring a primer treatment and then painting. Yes, there is a reason a lot of glue containers are polypropylene!
With wood-based panels (e.g. particle board) having such good acoustical characteristics, and injection-molded plastic have its advantages, what if you could develop an injection-moldable wood? Actually, for more than 50 years American Wood Flour has supplied milled saw dust “wood flour,” which has been compounded with various plastic resins over the years.
Today, there are both vendors and speaker products that use wood cellulose compounded with plastics (bio-plastics). While the automotive industry uses this stuff for interior parts because it is light, waterproof compared the “real wood,” tends not to squeak or creak when there is vehicle body roll, and has a good sustainability story. Hey, doesn’t that all sound good for a speaker enclosure?

A few early examples include the Genelec Natural Composite Enclosures (NCE). Genelec’s M Series NCE studio monitors, which were made of a fully recyclable injection-moldable wood-based composite material (Photo 3). The wood fibers contained in the material provide high internal losses which contribute to excellent enclosure performance, resulting in studio monitors that were affordable without compromising the sound.
For the product managers, considerations such as surface finish, impact resistance, temperature tolerance, and acoustics must be taken into account. There is also growing demand from brand owners and consumers for electronic products with reduced environmental impact and greater sustainability such as bioplastics.
One vendor of wood-based bioplastics for consumer electronics is Sappi, a global wood pulp supplier. Its Symbio is a natural composite of cellulose fibers (with options of 20% to 60% cellulose) dispersed in a polymer matrix (polypropylene) and delivered as granules for standard processing equipment, such as injection molding and extrusion. Symbio does have outstanding acoustical performance and enables thick wall molding without sink marks so even a subwoofer can now be injection molded.
Other benefits are a more natural look, soft and warm touch, high rigidity and low density, and excellent acoustics. It can be used in a wide range of applications across furniture, consumer electronics, and automotive components. Another cellulose plastic is Eastman’s TREVA (bio-based content of 42%) that also has excellent acoustics (superior damping than polycarbonates and ABS) and reduced environmental impact. TREVA is chemically resistant, dimensionally stable and has excellent flow.
Eastman’s plastics from cellulose are based on more than a century of cellulose photo film development. Eastman undertook acoustic testing of various resins in earphones, which showed significant impact on measured and audible sound quality. I would mention that in an earphone, especially an in-canal type, the plastic housing resin characteristics would likely contribute far more influence on the audibility of the resin characteristics. Pro-sumer speakers (e.g., karaoke, DJ, and PA speakers with a woofer and horn) would also be far more critical applications, compared to a Bluetooth speaker.
Some Testing
Warkwyn (MISCO), the US agency for Klippel and Microflown, working with Tonly, (the manufacturing side of TCL), has spent considerable effort in evaluation of a half-dozen resins used in soundbars. They used the same soundbar tool but run off the soundbar enclosure using the same tooling mold and powered from the same amplifier module. The question to be answered is would various resins used for soundbars (ABS, PC, ABS+PC, and impact strength/flame retardant “FR” variants) have similar influence on sound quality of the finished product? Warkwyn performed laser measurements aimed at a section of the soundbar empirically determined and selected by the enclosure wall’s high flexing displacement (break-up mode point).
The bottom line is that the differences in acoustic performance were slight among all the materials — and the lower price and good flow of ABS explains why the market considers it a value proposition that makes sense. Also, it was shown that PC + ABS blends and pure PC performed better than ABS for speaker enclosures, as the added stiffness of the PC helps a bit. The softer ABS does not seem to contribute to damping, compared to PC-enhanced characteristic contributing stiffness.
What was interesting was that PC and PC+ABS blends with impact resistance additives revealed better control of flex and resonance, and that the impact resistance plastics (which also feature FR) had the best acoustic characteristics. Two “hints” are that impact resistance may be conferred by powdered rubber (EPDM) additives or other performance enhancing polymer additives and this likely provided enhanced acoustic damping.
For professional and audiophile products — with higher acoustic output and strong bass, then PC+ABS with enhanced impact resistance should be considered. Yes, there are plastics that do perform better than the products we have discussed and so we are not quite done with our exploration of injection-molding plastics. Let’s finish with a couple of exciting next-generation injection-molding composites that are becoming available.
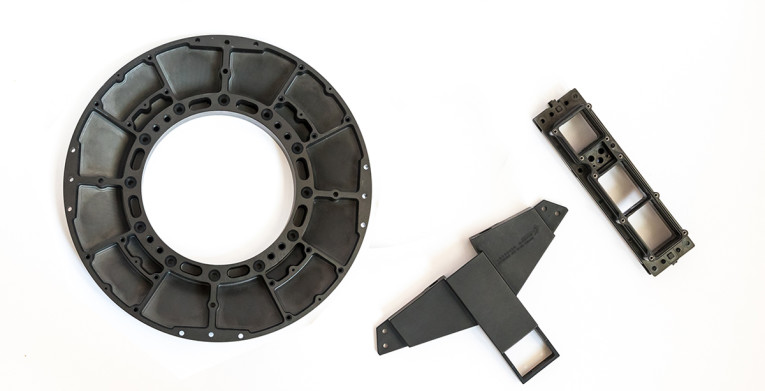
Alpine HX5 — Injection-Molding Nanocomposite
Thermoplastic composites have great potential but most of these have been in the form of sheets for compression molding using a positive and negative die. The challenge has been getting a deep enough draw for forming shaped parts, and the even greater challenge is the audio industry is very much invested in injection molding, not compression molding. HX5 is Alpine Advanced Material’s flagship injection-molding composite material using conventional machinery.
Originally designed for aerospace and defense uses by Lockheed Martin SkunkWorks, this ultra-light and mechanically superior nanocomposite is designed to be the most capable, versatile and best-in-class aerospace-grade option for high-performance applications. The material presents an alternative to high-performance aluminum alloys at half the weight, as well as high resistance to solvents, fuels, lubricants and chemicals, UV and even radiation resistance, giving it the ability to withstand the most demanding applications. Already certified for use in rockets and satellites, mobile DJ speakers and tour sound systems are not likely to be beyond its capabilities. Read more about HX5 here.
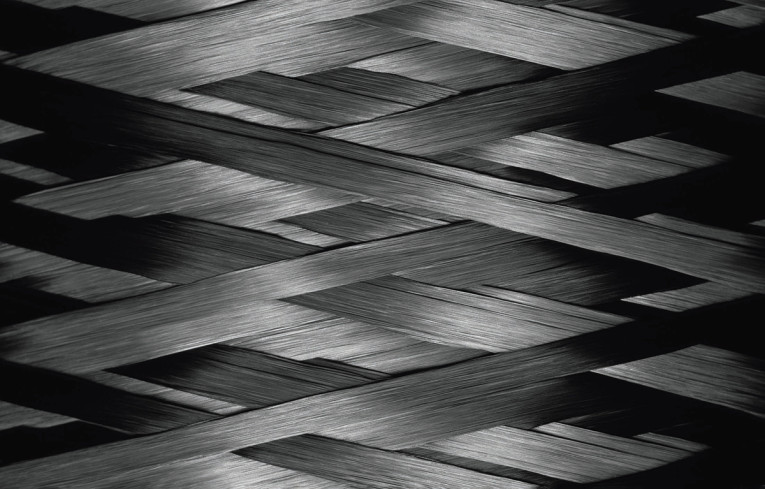
Covestro Maezio
Covestro, one of the leading global resin suppliers introduced Maezio in 2018. Maezio thermoplastic composites combine strong carbon or glass fibers with the power and flexibility of thermoplastics (Photo 5). Thermoplastics like polycarbonate are used as the substrate material, and carbon or glass fibers are used for reinforcement. The results are composite uni-directional tapes that also can then be laminated at different angles to form sheets tuned to a specific mechanical performance objective. These laminates are light, strong, and beautiful and offered in a range of finishes from colored and textured, to black and glossy, to matte, and untouched unidirectional fiber.
Maezio is thermoformed with existing thermoforming tools at high yield rates and low cycle times for millions of parts per year. Other production technologies such as hybrid injection molding (overmolding), automated UD (uni-directional) tape laying and automated fiber placement (AFP) can be integrated. Being thermoplastics, they can be recycled at the end of their life, making them a sustainable material choice. If your in-house personnel or subcontractor has compression-molding capabilities and if Maezio fills your requirements then you might also consider Covestro’s regrind process for using the (expensive) scrap from the Maezio sheet for very high performance injection-molding applications (Photo 6).
TLC Products
Just over the horizon may be something special — PET Graphene injection-molding thermoplastic composites — which promise good strength and acoustics. TLC Products is bringing a new category of plastics to market (Thermoplastiset) combining the re-molding characteristics of thermoplastics with the rigidity of thermosets. This product is still in the later stages of development with sales of pellets for initial evaluation to be followed by sub-licensing the compounding machines to partners.
Plastics are available as thermoplastic (re-melted or re-molded) and thermoset (molded only). An integrated process has been developed to efficiently and inexpensively exfoliate graphite particles in molten polymers, and is being scaled up. The composite is lightweight, high specific modulus and strength, and is promised at low cost. Stay tuned for updates on the innovations in plastic resin composites for audio applications. VC
References
Alpine HX5 — www.alpineadvancedmaterials.com/hx5/
Eastman Treva - www.eastman.com/Brands/Treva/Pages/Overview.aspx
Covestro Bayblend | Maezio - www.covestro.com - www.solutions.covestro.com/en/brands/maezio
Sappi Symbio - www.sappi.com/symbio
TLC Products - www.tlcproductsinc.com
Warkwyn - www.warkwyn.com
Other articles from Mike Klasco on speaker enclosures:
More Developments in Loudspeaker Enclosure Materials
Loudspeaker Enclosure Materials - Part 1
Loudspeaker Enclosure Materials - Part 2
This article was published originally in Voice Coil, March 2022