Let's provide some background to provide a bit of credibility to this story, as they have a long and successful history developing noteworthy audio products. Soundmatters was founded in 1998 as an audio research and development company with projects for Logitech, Viewsonic, Roku, IGT, and Jawbone as well as for the many brands that Eastech (a large Asian OEM/ODM) supplied.
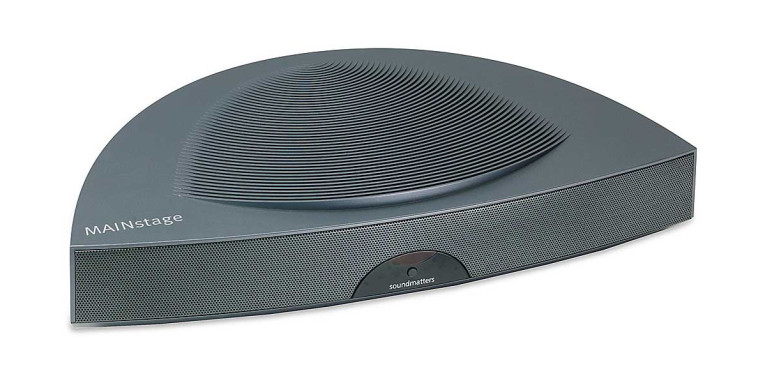
In 2003, soundmatters introduced its first product for itself, the MAINstage 1-Box Surround System. This powered speaker converted any TV, computer, or other audio source into a mini home theater and was the prelude to the one-box soundbar surround solution. Powered stereo/virtual surround; easy hookup; just 2.5" tall; analog and digital inputs. Opening up a new category entirely, soundmatters lacked the mindshare to make it stick. Not surprisingly, consumer electronics giants including Samsung, Vizio, Harman, and company, quickly got into the game and ate soundmatters' lunch. Nevertheless, soundmatters evolved the concept and are still very much alive and kicking today, now based in Taiwan.
In 2018, startup Level 10, engineered by soundmatters was created to launch the UPstage360 speaker on Kickstarter, which was one of the most-funded speaker projects on the platform. UPstage360's aim was to reinvent traditional speaker soundstage to a 360-degree sweet zone. After a year of further development, Level 10 has new tricks with its UPstage180 concept and it is combining music and soft lighting with a streamlined design for wall mounting or to just sit on a flat surface with even beamwidth 180 coverage.
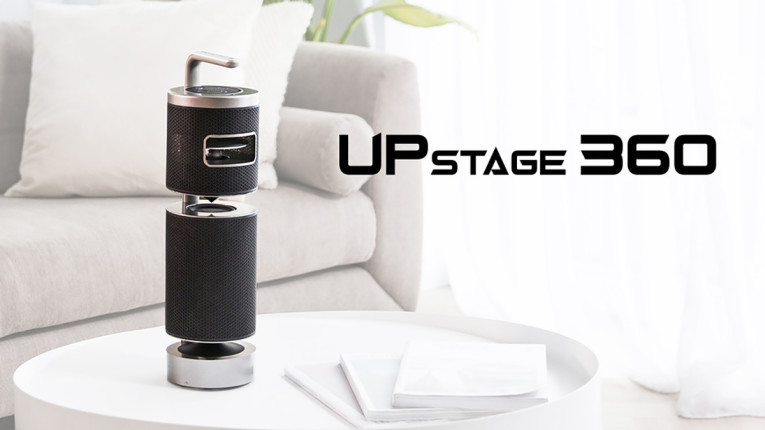
Let's Roll Back
With the UPstage introduced, let's roll back and introduce the illustrious founder of soundmatters, Dr. Godehard Guenther, NASA scientist and audio legend. Born in Germany, Dr. Guenther earned his PhD in astrophysics at the University of Heidelberg. Recruited by Dr. Wernher von Braun, Dr. Guenther immigrated to the United States where he worked with a group of scientists at NASA on the development of America's first space station.
In 1972, he left NASA to pursue his passion for audio, initially importing Braun loudspeakers to the US, then founding Analog + Digital Systems (a/d/s/), which later acquired Braun Audio. There he led the development of such innovations as the use of rare earth metals, including samarium cobalt and neodymium in loudspeakers, the first fully digital surround sound system, the first in-wall loudspeaker, and a pet project of a fully automated tweeter production machine. In 1998, Dr. Guenther went on to establish soundmatters.
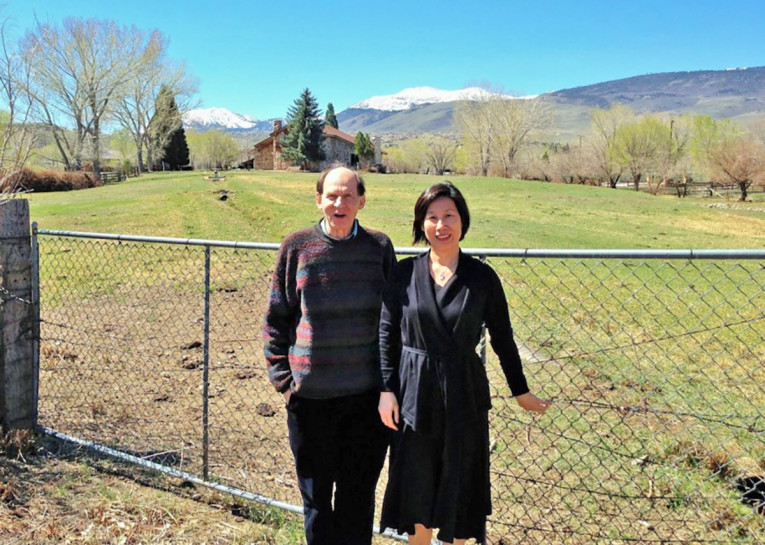
At this stage, let me introduce Beijing Design and Creation Electronics Company (BDNC), founded 2007 as the R&D arm of a Taiwan semiconductor company and later spun off in 2016. One of its more recent developments is a unique damped glass diaphragm shallow speaker. And the UPstage180 speaker is the launch customer for BDNC's high-power, flat glass woofer with a 0.2 mm glass diaphragm and the highest excursion-to-thickness Index without the interference of rocking modes common in other transducers.
UPstage180 is compact, about one-quarter the size of the classic bookshelf speaker, and yet delivers solid bass that can reach down to 60 Hz. soundmatters' Linear Magnetic Drive Twoofer is both a tweeter and a woofer - it is the first single device produced by carbon fiber injection technology with sound-enhancing capabilities on both ends of the audio spectrum.
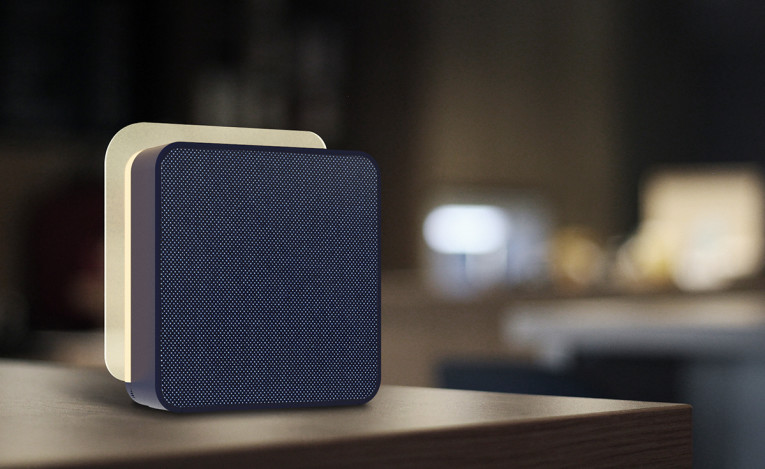
I talked with Emma Yu, soundmatters' CEO for the global operations, about her selection of the drivers for the Upstage 180; "I chose our Twoofer carbon fiber diaphragm and glass speaker, which both have very high Young's modulus in similar speed to transfer soundwave. Quick response. The quality is very even with both Carbon Fiber and Glass. Take a listen to 'The Sheffield Track & Drum Record' and enjoy very impressive sound quality."
For Bluetooth, the UPstage180 design uses Microchip's BM83 module with Bluetooth 5.0, to support also Sony's LDAC 24-bit/96 kHz Hi-Res audio and maintain a reliable connection. This Bluetooth module also features an innovative application of True Wireless Stereo (TWS) and Bluetooth Wireless Concert Technology (WCT) so that users can connect multiple UPstage180 speakers. Just like your TWS earphones, using two UPstage180 speakers with its proprietary app will automatically assign left and right channels to the two units. Finally, the design is powered with Infineon MERUS Class-D amplifiers, known for compact, cool stable operation and good sound.
The enclosure is light yet very rigid due to the injected-molded thermoplastic with a very high carbon fiber loading. I would mention that soundmatters is working with my firm and other partners evaluating various injection molding resins for acoustic properties and related mechanical attributes.
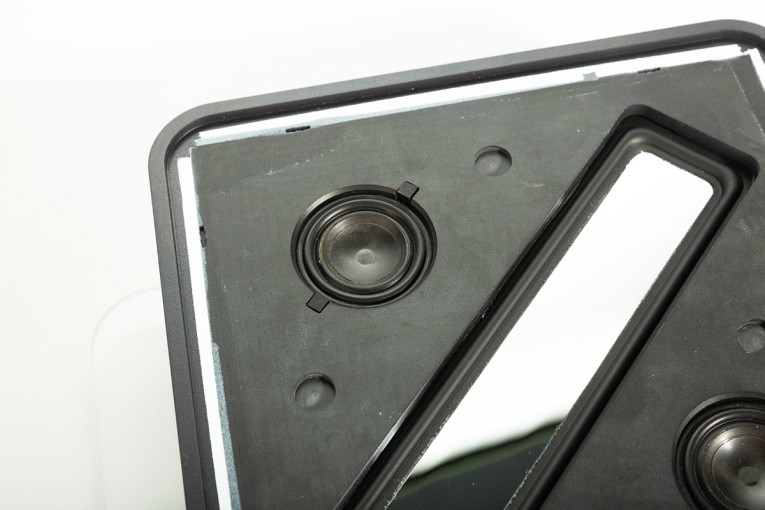
Both the UPstage360 and 180 projects involved the use of great electroacoustic measurement technology. The UPstage180 was tested at Warkwyn, Klippel's US training, calibration, and distribution partner. The test was done with the latest Klippel R, which is part of an interesting story in of itself. Back in the 1990s, I worked with Bell Labs on its SYSid acoustic analyzer and the agency for Taiwan and China was run by Emma Yu. But Bell Labs was lost when AT&T was disassembled. Yu also founded SOMA, which today is the agency in Taiwan for both Klippel and Loudsoft.
The BDNC Glass Speaker and Other Developments
As discussed, the already available UPstage180 speaker was the launch platform for BDNC's high-power, flat glass woofer that uses a 0.2 mm glass diaphragm. We briefly touched on the application of the BDNC glass diaphragm, as the high-excursion yet ultra-low profile woofer in the UpStage, so this time we will drill deeper.
From the transducer side, there are three noteworthy pillars. Starting with the ultra-thin tempered glass diaphragm, complemented with the anti-rocking thin yet high-excursion suspension, and coupled with low-end operation extended well below in-box resonance (small box eq'ed for extended bass). In this article, we will expand on those pillars.
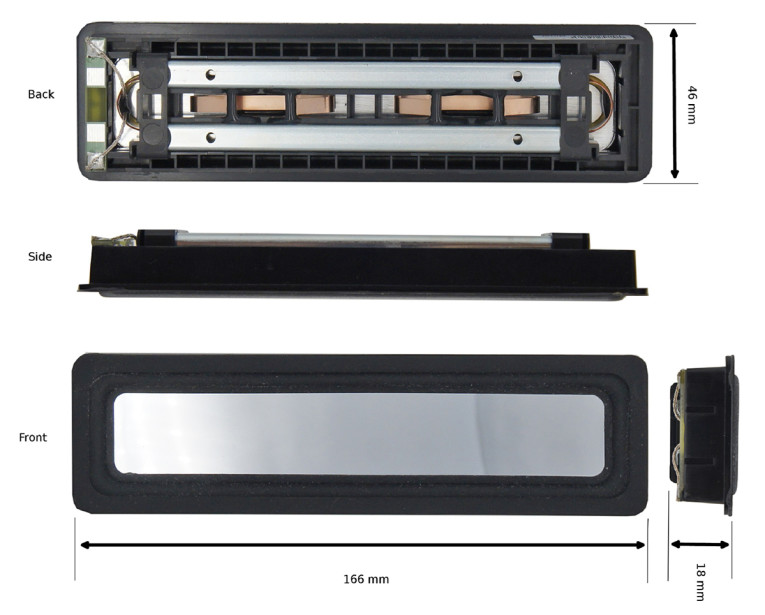
But let's step back and start at the beginning. BDNC, Ltd. began in 1995 as an R&D think tank by a Taiwan semiconductor company. The founder bought out the technology and assets in 2007, and then in 2016 raised funding from Taiwan. The core business was consulting in signal processing, mixed-signal, and electroacoustics.
With expanded resources for product development, the BDNC team was able to pursue their dream, which they call the miniMAX concept. This design philosophy is a ground-up approach for audio system development, where all the speaker design aspects are optimized using signal processing when effective. As BDNC explains, miniMAX is "a system-level technology" and an integrated approach from product design to manufacturing, applying DSP where it makes economic sense. Focusing on drawbacks that can be effectively "corrected" by signal processing while the remaining transducer parameters are concentrated on where the processing cannot mitigate performance.
BDNC considers frequency response - and with more effort, harmonic distortion - to be "DSP-friendly" while "non-DSP friendly" factors are maximum excursion ("Xmax"), specific force factor (BL/√Re), sensitivity, and power handling. If we can disregard the frequency response in the design stage, the speaker topology can be dramatically changed, allowing for thinner, more compact, high aspect-ratio rectangular or even tube-shaped products.

The smartphone and more specifically LCDs have inspired high-performance glass development. BDNC realized this new generation of high strength, ultra-thin glass from Schott, Corning, and others also has applications for speaker diaphragms. Let's take a look at some of these engineering glass formulas.
Schott AS 87 eco is an aluminosilicate glass suited for chemical strengthening (via an ion exchange treatment) that offers a high level of mechanical impact resistance and bending strength in a thickness range of 0.1 mm to 0.4 mm. Corning's Willow (available from 0.8 mm down to 0.03 mm), is roughly the thickness of a sheet of paper. Fabricated from Corning's amorphous Si O2 fusion process, molten glass is homogenized and conditioned before it is released into a collection trough with a V-shaped bottom (isopipe). Flowing evenly over the top edges, forming two sheet-like streams along the outer surfaces, the sheets meet and fuse into a single sheet which feeds into drawing equipment as it lengthens and cools in midair, as thin as 100 microns.
This process adds to the toughness of Willow (and also Gorilla) Glass and is not prone to breaks and cracks. Post processing for glass speaker diaphragm applications can include attributes such as a constrained layer damping of other materials (e.g., 3M's Viscoelastic Damping Polymer 112 acrylic polymer).
Another sophisticated element is the anti-rocking thin high-excursion suspension. The rocking problem is a known issue in high aspect ratio speakers, as there are billions of these smartphone microspeakers with the omniscient 10 mm x 15 mm x 3 mm format. While these microspeakers utilize a one-point suspension, BDNC realized that a high linearity spider was also needed, but would have to fit into a shallow form factor. The epiphany solution was actually derived from a pre-World War II field coil speaker. Specifically, a phenolic spider in a Jensen field coil speaker found in the designer's personal collection.
A solid spring spider has better linearity performance than a cloth spider in small signals. Over the years, there have been other attempts with varying results, including Sony's low distortion old-style spider and Doug Button's EVX 1800 high output 18" pro-sound woofer, which featured a glass epoxy spider.
Achieving high excursion in shallow high-aspect-ratio transducers means fighting rocking modes (undesired rotational vibration patterns). In a number of Audio Engineering Society (AES) papers the Klippel team has explored the various rocking mechanisms and the resultant voice coil scrapes with the observation that the suspension is the main cause and cure.
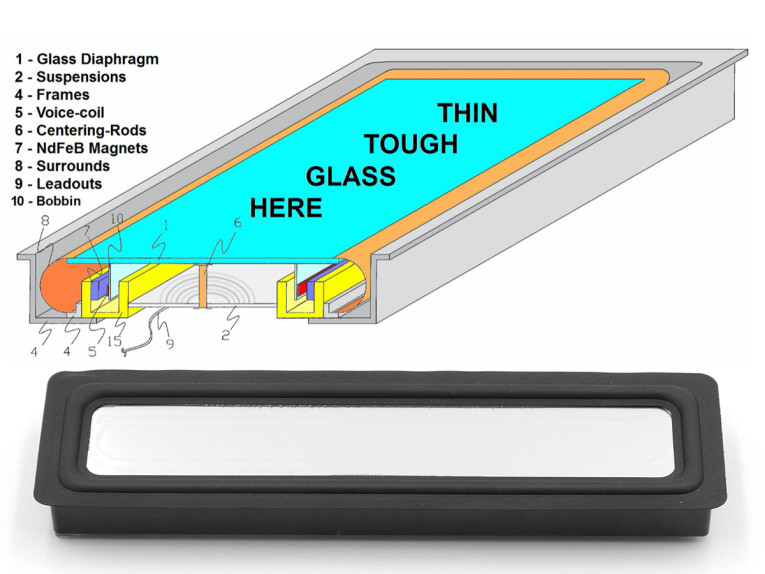
Rocking modes are caused by the inhomogeneous distribution of mass, stiffness, and force factor shifting the center of gravity, and electro-dynamical excitation away from the pivot point, which is the cross point of the nodal lines of the two rocking modes. Due to the high Q of the rocking resonators, only a very small asymmetrical force is required (which is usually a few percent of the transversal force) to generate a critical rocking behavior having more energy than the desired piston mode. Assessing the relative rocking level (RRL) and identifying the imbalances is a convenient way to keep voice coil rubbing under control and to avoid impulsive distortion from impairing the quality of the reproduced sound.
Woofer diaphragms vibrate through the compliances suspending the diaphragm. Compliance is the inverse of stiffness (stiffness = Young's modulus). Aside from many other considerations, the Young's modulus of the diaphragm should be as high as possible while the surround stiffness should be as low as possible.
A more compliant suspension enables the enclosure to be a smaller volume but also offers a more consistent bass response in mass production - as low-end response is dependent on the consistent back volume air compliance (air suspension) rather than variations in the surround compliance. To restate this, the resonant frequency is dominated by the effect of the back volume. This is defined as acoustic suspension (air suspension or sealed box). The compliance of the membrane must be far higher than the compliance of the back volume.
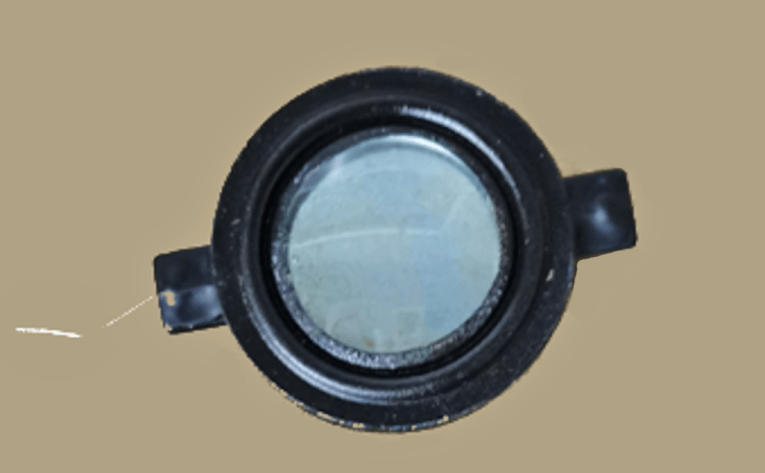
Invented in 1954 by Edgar Villchur of AR speaker fame, acoustic suspension systems reduce distortion in the bottom end of the speaker's response that can be caused by stiffer nonlinear suspensions. While Acoustic Research, Inc. and Bose are odd bedfellows in the same sentence, the Bose 901 of the late 1960s used an array of 4" full range cones speakers in the tight volume enclosure and eq'ed the heck out of them below 200 Hz (almost 20 dB at 20 Hz!). So the entire bass range was used below resonance where the frequency (and phase) response was consistent and could be electrically compensated. Same here for the miniMAX approach.
On its product development roadmap, BDNC has three different sizes for its rectangular series of glass woofers. There's the middle size FP-SPK-M (160 mm x 40 mm x 17mm), the large size FP-SPK-L (584 mm x 92 mm x 25mm), and a small size FP-SPK-S (80 mm x 20 mm x 7.2mm). The next steps on the company's speaker road map are glass cone speakers (see image above), audiophile headphone drivers, and another long-term project of very low impedance (VLO) speakers.
www.soundmatters.com
www.newbdnc.com
This article was originally published in The Audio Voice weekly email newsletter (287 and 288).