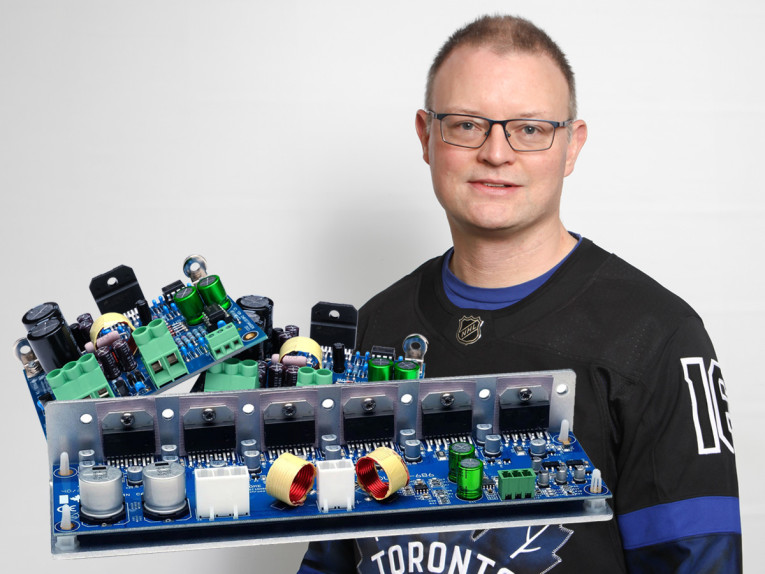
One hundred and thirteen dollars! That was my weekly food budget in 2010 when Neurochrome started to take form. At the time I was working on a power amplifier based on the 300B vacuum tube and needed a regulated high-voltage power supply. The only snag was that my chosen low-volume circuit board manufacturer wanted a minimum order of $113, which would result in about 30 regulator boards. I only needed two. But professionally manufactured circuit boards are much nicer to work with than DIY boards, and given the high voltages involved I decided to have the circuit boards manufactured and see if I could sell the excess. I set up a simple website and announced the boards on a forum for fellow do-it-yourself audio enthusiasts, diyAudio. All the boards were sold before they even arrived from the manufacturer! This was the genesis of Neurochrome as an audio company.
My interest in electronics started around age five. Most of my early work involved the exploration of the power dissipation limits of resistors (i.e., letting out the magic smoke by hooking resistors up to batteries). This spurred my interest in test equipment and laboratory power supplies, as the latter allowed me to burn up resistors without having to buy batteries. It was through the design of these power supplies that I learned about the power dissipation limits of power transistors, heatsink sizing, chassis design, and manufacturing—all before reaching my teenage years.
Electrical engineering felt like a natural career choice to me, and I earned my bachelor’s degree in electrical engineering from the Engineering College of Copenhagen in 1999 and my master’s in 2002 from the University of Washington in Seattle, WA. I drifted into the Ph.D. program and after a few years I was horribly burnt out and not getting anywhere with the degree. When offered a summer internship in the Precision Amplifiers Group at National Semiconductor’s design center, south of Seattle, I jumped at the opportunity.
The National Semiconductor Years
Precision circuit design was the perfect fit for me. It required me to use both my understanding of electronic circuits and my knowledge of semiconductor physics and materials. It also greatly expanded my understanding of circuit simulation. When a company like National Semiconductor spends $1 million on an IC mask set, they will want some reasonable assurance that the IC will meet the specs that the marketing folks promised the customers. So, the performance of the circuit is simulated across variations in power supply voltage, die temperature, and the semiconductor process for the operating conditions in the datasheet before it is even committed to layout. All to ensure that the manufactured product will perform according to specifications and have an acceptable yield when produced by the millions. I carry the same design philosophy forward in my current work.
My work in the Precision Amplifiers Group also instilled in me the importance of good circuit layout in high-performance circuits — even at audio frequencies. Audio is basically DC that wiggles a little bit, so how could PCB layouts, never mind the much smaller IC scale layouts, impact the performance of an audio circuit? My manager kept saying, “the layout is the circuit,” but it appeared to be a lesson I had to learn on my own. The eye-opening moment came during the design of a cross-point switch in a precision operational amplifier (op-amp). It is a simple circuit that allows the polarity of the input signal to be reversed. The circuit consists of four analog transmission gates, each containing two MOSFETs (Figure 1).
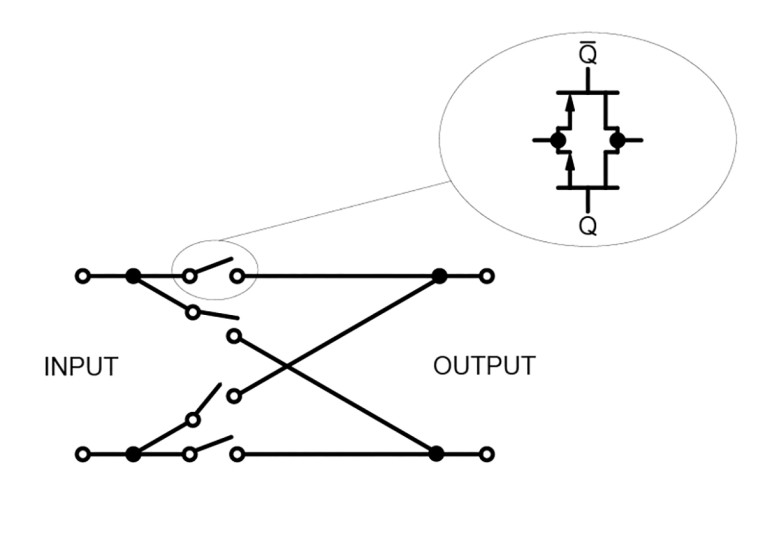
I learned about charge injection in MOS devices in a semiconductor devices class during my master’s degree work, so I made sure to account for this effect. The circuit worked beautifully in simulation, and I proceeded with the IC layout of the switch. With the knowledge I have today I would describe the layout as a pretty good connect-the-dots layout with the MOS devices laid out to ensure good matching. The switch was to operate at frequencies slightly above the audio band, so I had full confidence that it would work well. Imagine my surprise when I ran the simulation with the IC layout parasitics included and found the performance of the circuit had degraded by a factor of 100! It then dawned on me that compensating for charge injection required matching of both the MOSFETs and the layout parasitics.
Following two weeks of detail-oriented IC layout I finally had the production layout, which performed only marginally worse than the schematic simulation. This was one of many aspects of this project that really tickled the detail-oriented side of me and further stimulated my passion for precision analog circuits and audio amplifiers.
National Semiconductor closed my local chapter of the Precision Amplifiers Group in the Summer of 2008. We were absorbed into the Precision Timing Group in the same office. The following seven years of my career were essentially a deep dive into the internals of clock jitter cleaners, frequency dividers, and RF IC design. I have several designs with industry-leading performance that are part of National Semiconductor’s clock jitter cleaner and clock generation products. I found it a bit ironic that I went from designing precision op-amps that were designed to never oscillate to designing crystal oscillators where reliable oscillation is key.
I wasn’t super passionate about crystal oscillators, but the Precision Timing Group turned out to be a good place to hunker down during the economic recession and layoffs that followed. And I managed to survive the acquisition of National Semiconductor by Texas Instruments (TI) in 2011. My survival, both in general and with the company, hinged on the fact that the Precision Timing Group had strong business cases and large key customers to pay the bills. Also, our group manager moved up the corporate ladder, which gave us greater exposure within the company for a bit of additional protection from layoffs. Sometimes you get lucky…
Culture Changes
In the Spring of 2009, National Semiconductor laid off 26% of its workforce. The layoffs were not isolated to National Semiconductor or the tech sector, so I felt rather vulnerable at that time. Soon thereafter I had a health scare that further compounded my feelings of vulnerability. I realized how quickly my life could have been turned upside down if I had been laid off and lost my healthcare coverage. The combination of these events and my sense of US society changing in a direction I found increasingly incongruent with my values made me consider moving elsewhere, and in 2015, I immigrated to Calgary, Canada, as a permanent resident.
I was extremely burnt out in my last years at TI and thought the solution was a career change. Psychology has always been a strong interest of mine, and my plan was to pursue a master’s degree in psychology so I could start my own practice. The first step was to complete a bachelor’s degree in psychology.
In 2017, I was about halfway through my psychology studies and Neurochrome had really started to congeal as a reliable source of income. Neurochrome covered my expenses and, even though it didn’t leave a lot in the way of savings, it was clear that the company and I had potential. When the time came to select optional courses for my degree, I chose courses that applied both to my degree and to my business. I studied consumer psychology, human memory, human sensing and perception, human factors engineering, and entrepreneurship to name a few. I use the learnings from these courses in my product designs and interactions with customers daily. I graduated from the University of Calgary with a Bachelor of Arts degree in Psychology in 2019 and have focused on Neurochrome full time since then.
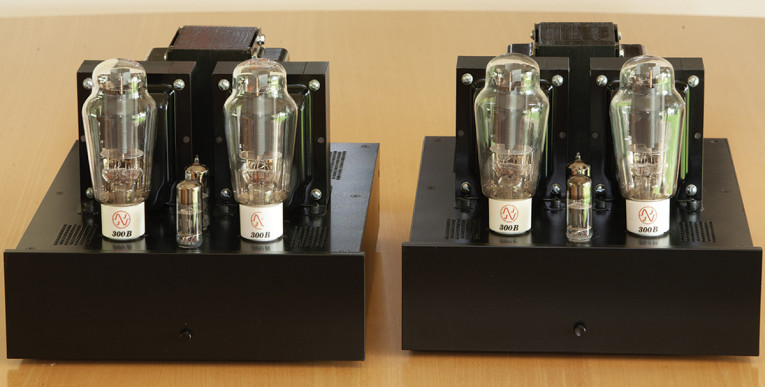
Neurochrome
It’s fair to say that Neurochrome was born from equal parts of boredom and nostalgia. I was at work running phase noise simulations on crystal oscillators for the umpteenth time, and the simulations ran just long enough that I got bored waiting for them to finish. I started reading the Tubes forum on diyAudio during this idle time and was reminded of when I first learned about vacuum tubes. This spurred a couple of designs, including the Darn Good 300B (Photo 1), the Universal Filament Regulator, and the 21st Century Maida Regulator. The Maida Regulator is still part of my product portfolio, and the Universal Filament Regulator is making a comeback after a significant redesign (Photo 2).
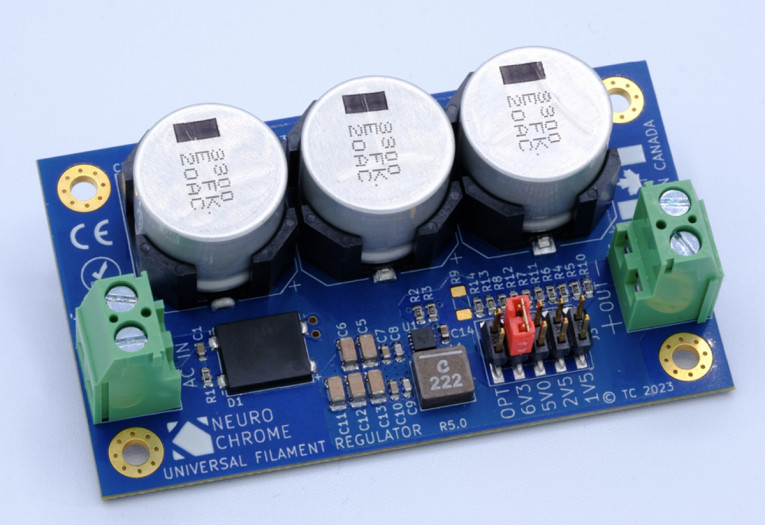
Composite amplifiers use multiple cascaded amplifiers to obtain a level of performance that exceeds the performance of the individual amplifiers. As such, the Modulus-86 uses a precision op-amp to perform error correction on a less precise power amp IC. This results in a power amplifier that has all the power of the power amp IC and the ultra-low distortion of the precision op-amp. But composite amplifiers tend to have marginal stability across the wide range of load impedances presented by speakers and are, therefore, not widely used. Getting the Modulus-86 to remain stable across a diverse set of speaker loads was indeed a major design challenge.
The Modulus-86 launched in July of 2014 and the current version, Rev. 3.0 from 2021, features a total harmonic distortion better than -130dBc at the full rated output power with an 8Ω load. It remains stable even with 2.2µF in parallel with the 8Ω load. The launch of the Modulus-86 helped put Neurochrome on the map as a precision audio amplifier company. The Modulus-86 and the DG300B provided me with enough income that I could contemplate leaving my day job at Texas Instruments.
I left TI in July of 2015. At the time I figured that Neurochrome could pay the bills in most months. Since then, Neurochrome has paid the bills in all months except for one. That said, I did take an 80% pay cut when I left TI and I have yet to make as much as I did in my last year there. But, I’m having 10 times the fun. I enjoy charting my own course and enjoy being able to play hockey in the middle of the afternoon when I want. And, most importantly, the state of my mental health is much, much better.
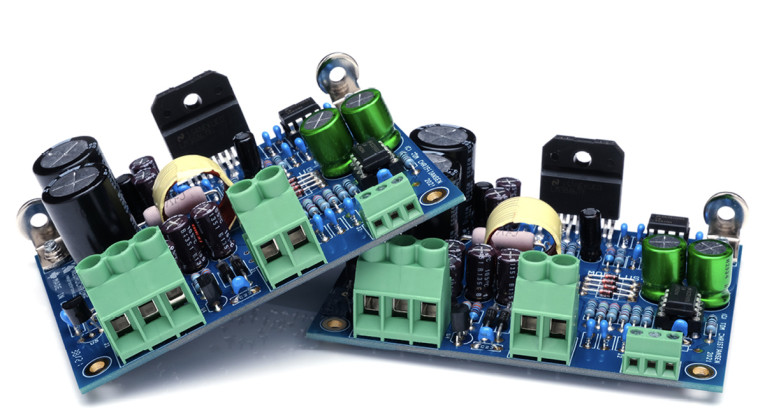
Lessons Learned
Today, Neurochrome offers a full lineup of power amplifiers, power supplies, speaker protection circuits, and power control circuits along with a high-end chassis. I also have a headphone dummy load available as a retail product. In addition, I am commissioned for bespoke amplifier builds and perform analog electronics engineering consulting for businesses and DIYers. I did not take the most linear path in life, but I have very few regrets. I do have some advice and lessons learned for those who wish to follow in my footsteps, though.
Failing to Plan is Planning to Fail … or so they say: I wish I had started my business with a business plan. It need not be elaborate or written on corporate letterhead. Just do yourself a favor and research your target market a bit. Analyze the competition. What are they doing well? What are they not doing so well? What can you do differently that would make your business stand tall among the competition? Is there an unserved or underserved niche within the market that you can fill? Think about it, write it down, and update it periodically.
One of my challenges with managing a hobby-turned-business is that I started my business without a plan or even a sense of direction. I just did what was fun to me at the time. There is nothing wrong in that, per se, but I wish I had taken the time to look at the DIY audio market more broadly and found my niche within it sooner. It would likely have accelerated my path to success.
Get a Business License. I would have saved about a thousand dollars had I licensed my business a year earlier. Applying for a business license is usually easy and cheap, and doing so allows you to deduct your business expenses from your income which, effectively, gives you a discount on those expenses corresponding to your marginal tax rate. That’s a benefit worth having.
Minimize Overhead Costs. Neurochrome turned a profit in its first year. It was basically beer money but a profit, nonetheless. At the time, I intended for Neurochrome to be a self-sustaining hobby, so I was content. But it illustrated to me how much overhead costs eat into the profit in a low-volume business. Even though Neurochrome has grown by a few orders of magnitude since then, I still aim to minimize the overhead cost (i.e., to reduce the costs that are not directly related to producing the products). As a result, I do not have a warehouse or a brick-and-mortar storefront. Rather, Neurochrome occupies two bedrooms in my house. I also have no employees, though I now contract a friend on occasion to help packing parts kits and to ship orders when I am out of town. By minimizing overhead costs early on I gave myself a fighting chance of survival in a niche market.
Procrastination and Motivation. Self-employment can be a lonely existence and with no boss to check in periodically it can be a challenge to remain motivated and make progress continually. For me, this is further exacerbated by my participation on diyAudio, which is part of my marketing strategy, something I enjoy, and my primary form of procrastination. I have never been able to enforce time limits for enjoyable activities on myself, so instead, I apply goal-setting theory; I have a goal of making one hour’s worth of progress on one key task each day. One hour of work is certainly an attainable goal, which makes it more likely that I will get started and succeed. One hour may not sound like much, but I find that the key to making progress is to get started and it is remarkable how much progress one can make in one hour of focused work. In addition, if scheduled right, that one hour will often stretch into a couple of hours or even a full day of focused work, and suddenly the task is complete. Having that daily sense of accomplishment is a large part of how I remain motivated.
Take Care of Yourself. Take a break every now and then. When highly motivated, I sometimes find it difficult to resist the temptation to work until the point of burnout. To address this, I schedule my exercise and social activities first. Then I schedule my work activities. This ensures that I will get a reasonable amount of exercise and social interaction — both activities linked to good mental health. I also try to spend more time outdoors, especially in the summer when I schedule a mid-week camping trip or two. Camping in the Rocky Mountains is one of my favorite ways to decouple from the stressors of everyday life. I tend to succumb to the temptation to work if I have Internet access, so I really need a few days without Internet to clear my head. I derive a great amount of new energy and new ideas from even a short trip in the mountains. Decoupling does not have to be that involved, though. Even a walk to my neighborhood park often provides enough of a context change that I return with a clearer mind and new ideas. For example, the insight that led me to the Modulus-286 came during a walk to the mailbox at the end of the block.
The Bottom Line
Starting and running your own business is not easy and there is no guarantee of success. In fact, 20% of businesses fail within the first year and the chances of lasting five years in business are scarcely better than 50%. If financial stability and material wealth are important to you, you may not want to quit your day job just yet. If, on the other hand, you are reasonably frugal and comfortable with change, being your own boss may be a good fit for you. I have always been frugal, but it has taken me years to become comfortable with the income volatility that comes with running a small business. I still feel a bit abandoned when I go days without a new order. I guess that’s the price of freedom and independence. To me, that’s a fair price.
Neurochrome serves DIY audio enthusiasts with a complete range of circuit modules and power amplifiers, ranging from 40W to 240W (8Ω), all well-engineered, thoroughly tested, and well-documented.
Resources
diyAudio, www.diyaudio.com
Neurochrome, www.neurochrome.com
This article was originally published in audioXpress, May 2024