I have co-authored previous articles on Magnetic Materials for the Loudspeaker Industry with Salvador Magdaleno (Salvador Consultant), a noted magnetic and electromagnetic consultant, who was instrumental in sharing his work on introducing Niron to our readers, for his magnetic simulations in numerous articles, along with his contribution to the design of most of the magnetizers currently in US speaker factories.
Most of us assume that neodymium ore must only come from China and that is how they have achieved a monopoly on neodymium (neo) magnets. And it is true that China is the dominant supplier of neo magnetics, globally controlling 87% of the global permanent magnet market, and thanks to its control of most of the world's rare-earth production, it is also the low-cost producer.
Pricing on neodymium seems to be determined by China. Yet, about 20% of the ore sourced by China comes from California (from the Mountain Pass deposit near the border with Nevada off Hwy 15), and another 20% from Australia.

Neodymium magnets were developed and commercially produced around the same time in the early 1980s by GM's Magnequench and Sumitomo. So why aren’t there more neo-magnet factories outside of China? The answer is that when any competition in forming neo-magnets shows up outside of China, then pricing from China would drop – and stay low until the new magnet vendors are starved out of business!
With high magnet costs imposed by China, not to mention the vulnerability of not having access, or just not having the pricing under our control, the United States is being forced to start its production of rare-earth magnets. There is a half dozen neo-magnet factories outside of China, from Malaysia and Vietnam, and a couple coming online in the US.
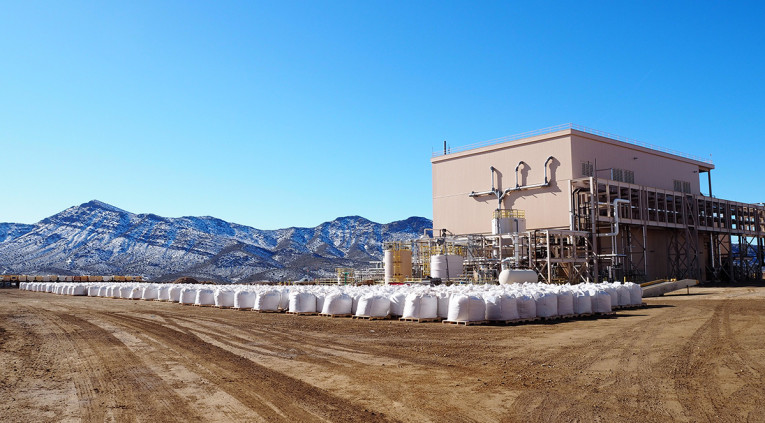
What Is the Process of Making Magnet Powder?
There are several steps in neo-magnet processing, starting with getting the ore out of the ground, then first stage separation, and cleaning. There are also several processes for making magnets, but the most common method is powder metallurgy. In this process, a recipe is pulverized into a fine powder, compacted, and heated to cause densification via "liquid phase sintering." Therefore, these magnets are most often called sintered magnets. There is also a bonded process for lower performance neo magnets ("refrigerator magnets").
The powder is pressed together to form a solid that has a preferred magnetization orientation (die-upsetting), where the powder is pressed with a die at elevated temperatures of about 725°C. This process requires powerful magnet powder presses and enables magnet production of specific shapes and sizes. Making the powder into magnets involves compressing the fine particles together, typically using a hydraulic press. The pressed magnets can then be further processed in a second die, where it is compressed to a wider shape that's about half its original height. This aligns the preferred direction of magnetization parallel to the pressing direction and includes an electromagnet that generates a magnetic field during pressing to align the particles. Additives are added at this stage to achieve desired magnetic characteristics, such as increased coercivity or high-temperature stability.
The latest development in reshoring neo-magnet production is Gasbarre Products, with a new range of magnet powder compaction equipment for the processing and production of rare-earth magnets. A project that I learned about because of the technical support provided by Salvador Magdaleno.
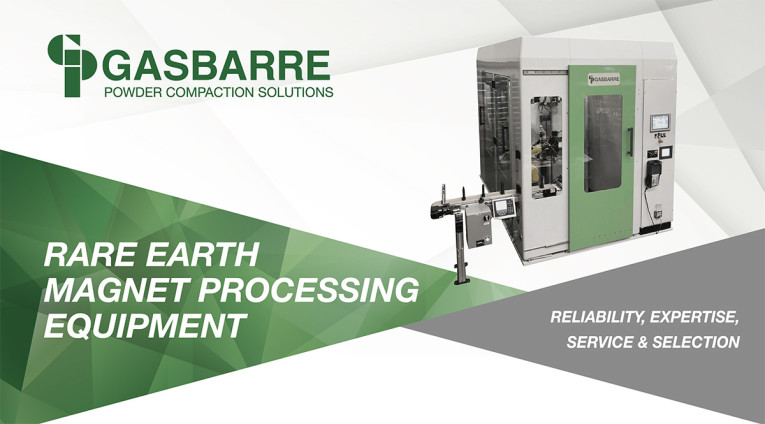
Gasbarre, headquartered in DuBois, PA, was founded in 1973 to design, manufacture, and service a complete line of powder compaction and sizing presses for the powder metallurgy industry. Since that time, Gasbarre evolved to a full-service supplier to the powder metallurgy, particulate materials, and thermal processing industries, with more than 200 employees in seven locations. Today, Gasbarre offers mechanical, electric, hydraulic, and isostatic presses for the compaction of powders.
Mechanical powder compaction presses are commonly used for powdered metal and technical ceramics production but are well-suited for other industrial applications. The Gasbarre magnet presses can be automated to be integrated into the production line along with a range of industrial heat-treating equipment for the development, processing, and production of rare-earth magnets. The company offers industrial furnaces for permanent magnet development and production, with batch and continuous vacuum furnaces that are also designed for rare-earth magnet production.
Gasbarre electric presses offer precise powder compaction for numerous geometries. These machines comprise various parts designed for maximum accuracy and repeatability, with features such as high-efficiency drives and freely programmable axes for complete compaction cycle control, including die filling, die motion, upper punch motion, and ejection cycle. For more information about Gasbarre magnet production equipment please contact Gasbarre here.
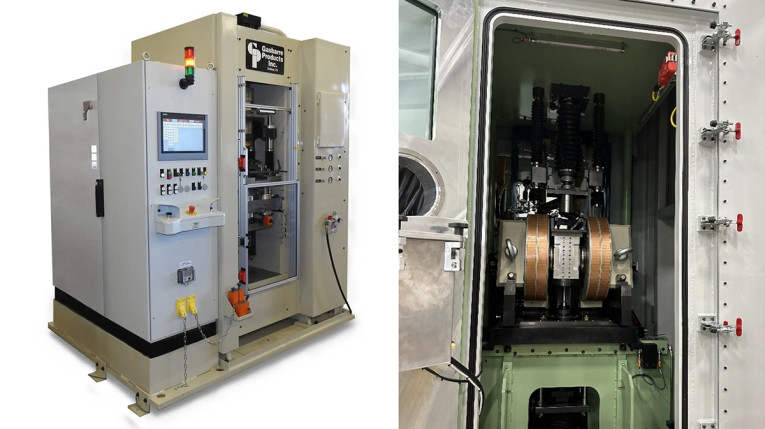
Winds of Change
From a 30,000 feet view, 2023 will be remembered as an inflection point in magnetics development and reshoring. MP Materials (the Mountain Pass mine company is building a new permanent magnet factory in Fort Worth, TX, in a joint venture with GM. This is part of a $700 million investment in building a fully domestic US supply chain, primarily for EV's Made-in-USA.
Last June, neo recycling leader Noveon Magnetics cut the ribbon on their state-of-the-art manufacturing facility in San Marcos, TX. The only fully active producer of sintered NdFeB magnets in North America.
In Europe, Stena Recycling in Norway has participated in REE4EU, a European Union-funded project that has tested several new recycling methods from neodymium recovered from wind turbines. This has been made possible (on a pilot scale) by several process steps, which begins with the dissolution of the magnets in acid and ends with electrolysis at high temperatures resulting in a metal alloy that is suitable for producing new neodymium magnets.
The results from Stena Recycling show that recycled neodymium is of the same high quality as that made from virgin materials. It can also be produced with 35% less energy consumption compared to the production of brand-new neodymium in China.
Finally, what is old is new again – Proterial, Ltd. (Hitachi Metals) has disclosed its NMF 15 high-performance ferrite magnet technology as an alternative to neo for electric motors and Salvador is already looking to explore this for loudspeaker applications – stay tuned!
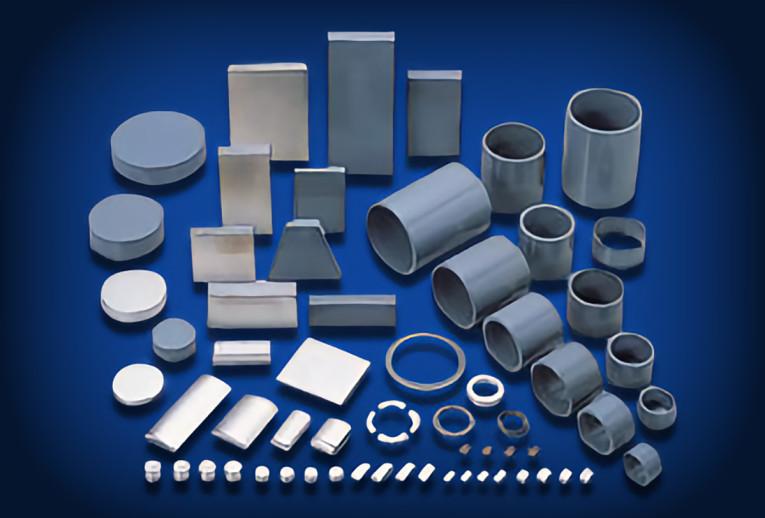
For more on neodymium and magnet applications for the audio industry, contact Mike Klasco at Menlo Scientific.
This article was originally published in The Audio Voice newsletter, (#447), November 30, 2023.