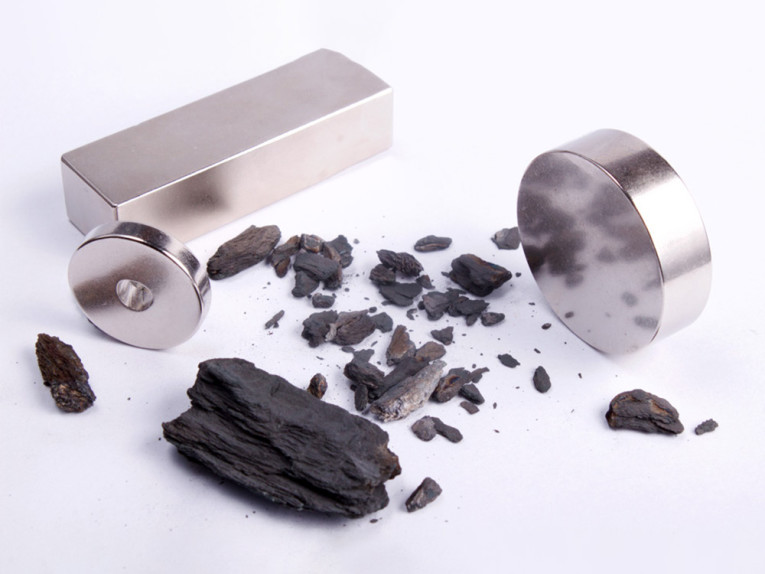
Geographically, for the US, the only significant alternative source of neodymium would seem to be the ore deposits, the mine, and the state-of-the-art refining complex at Mountain Pass, CA, as detailed in the first part of this article. Yet there is another almost unlimited source of neodymium - "mined" from recycling electric motors (the Prius first entered the market 20 years ago!), wind turbines, alternators, hard drives, cellphones... and loudspeakers.
Urban Mining Company
Five years ago, a couple of entrepreneurs and a Slovenian magnetics scientist banded together under the company name of Urban Mining Co. (UMC) and (briefly) attended the ALMA International Symposium & Expo 2018, which is the Association of Loudspeaker Manufacturing and Acoustics (ALMA) International annual event (now called ALTI). The plan was to recycle neodymium for speaker magnets. At the time, this venture was premature as there were many challenges, but this tenacious team eventually was granted patents. In 2016, they raised $25 million to put together a neodymium magnet recycling facility near Austin, TX. As you read this, there is already a pilot operation in place and a purpose-built “refinery” on schedule for completion. Initially capable of producing 250 tons of recycled magnets annually, a future expansion is planned within two years to recycle 1,000 tons per year.
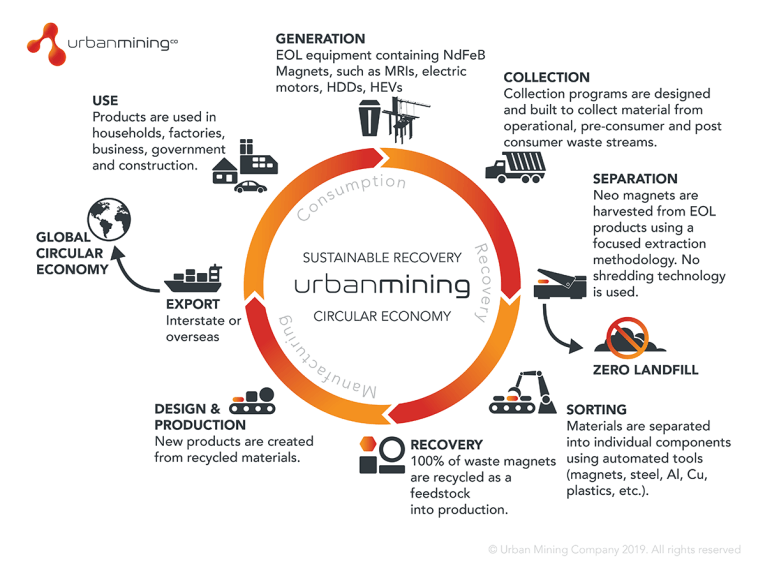
Future Recycling Processes
Urban Mining is not alone. Many private, government, and academic research facilities have invested significant effort in developing somewhat different recycling processes. The operational and financial feasibility of optimizing any bench-top scale extraction process to large manufacturing scale has yet to be proven. Currently, no neodymium magnet suppliers have the ability to economically collect used magnets and re-process them. For post-consumer magnets harvested from equipment at the end of their life cycle, the material composition is unknown and may be different from unit to unit, which creates significant problems in achieving good quality from the recycled product.
I can envision a business model for specific products (e.g., car alternators and EV permanent magnet motors) with the “duds” sent back for recycling and the reprocessed magnets used for the identical application as they began. This might also make sense for the almost identical smartphone loudspeakers from the 1.6 billion smartphones produced each year.
I read through a few studies and the recovering procedure starts with collecting neodymium magnets from used electronics or equipment, demagnetize them, and render the raw material. Obstacles to the process are many. The early neodymium recycling resulted in a product that could not be re-magnetized! While this has been long resolved — due to its iron content, exposed neodymium magnets can be easily degraded, oxidized, and corroded, especially the stuff that was produced a while back, which is exactly what is likely to be recycled. Purification or refining needs to be put in place to remove the excess oxides and recreating or refurbishing the material back to its original magnetic properties can be difficult.
Due to its vulnerability to corrosion, plating is applied as a protective layer. The surface finishing comes in various materials, varying from nickel to plastic, and makes the recycling process more complicated. Since there are many choices of grades for various applications, separation methods must be determined and depend on the chemical and process selections and whether the procedure produces any byproduct would be an additional issue.
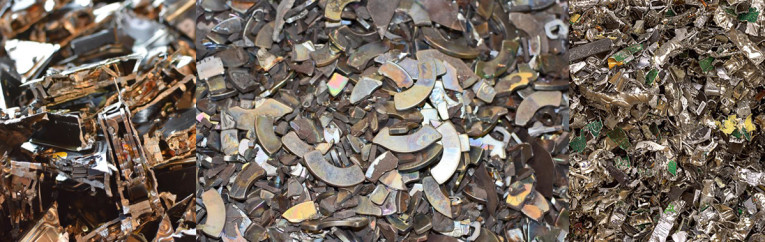
The Pros and Cons
The idea of recycling neodymium is “Politically Correct” along with the strategic implications of having a domestic back-up supply. Yet if not done efficiently, it can be an energy-intensive process that causes more problems than it solves. Conversely, mining rare earths is really nasty, as the mining process may expose workers to radioactive fumes and particulates both in the extraction and the separation of ores. Since recycling only involves re-processing magnets that only contain neo, boron, and iron (NdFeB), the scary stuff was separated out a long ago during the first time around. Compared to the mining process, recycled magnets potentially have less environmental impact, consuming an order of magnitude of energy with fewer pollutants.
Recycling rare earth minerals may have the wind behind its back if neodymium is in the cross-hairs of trade conflicts, along with the success of UMC's Texas operation. UMC will be able to supply to both the sintered and bonded magnet markets in the US by offering two product lines, consisting of sintered and machined NdFeB magnets and feedstock material for bonded magnet production in the US. While there is no sintered magnet manufacturer in the US (although sintered magnets have the best magnetic properties as they are 100% metal), there does exist a bonded magnet industry.
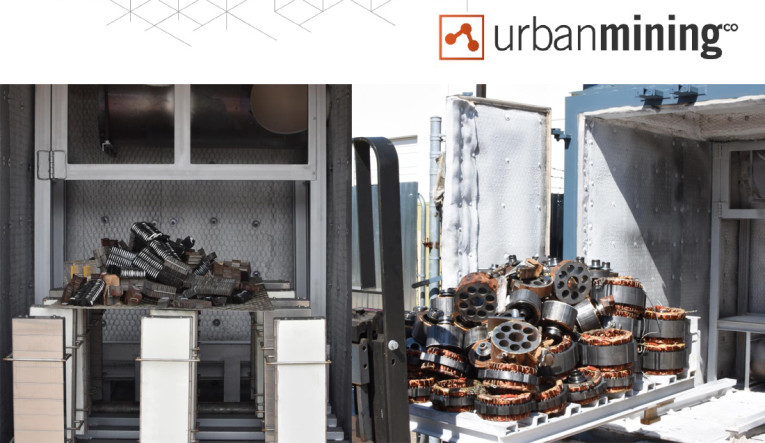
The US Bonded Magnet Industry
The US bonded magnet industry currently procures their feedstock material internationally, typically from Asia and uses the material as a feedstock for injection-molding machines within the US. UMC has invested in equipment and technology to be able to supply bonded magnet feedstock material to US bonded magnet manufacturers. This traditionally has not been a supply option for US bonded magnet manufacturers as the manufacturing process to produce bonded magnet feedstock requires access to rare earth material. However, access to rare earth feedstock material is something that UMC has solved with its sintered magnet production. Therefore, by using end-of-life (EOL) harvested feedstock materials extracted from US goods, UMC can supply magnets to two markets, the high-performance sintered magnets and the existing bonded magnet manufacturers within the US.
Based on UMC’s research, there is an exponential growth in the EOL equipment that contains NdFeB material — enough that through the proper collection channels, we could domestically support NdFeB production. UMC looks very much like a stand-alone solution for the Department of Defense and potentially some commercial industries. VC
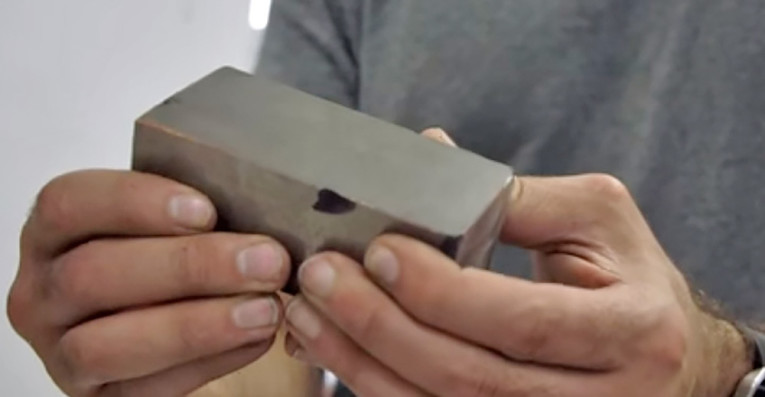
This article was originally published in The Audio Voice newsletter of August 23 and 30, 2018. An extended version, also divided in two parts, was later published in Voice Coil magazine in November and December 2018.
Read Part 1 of the Article Here.