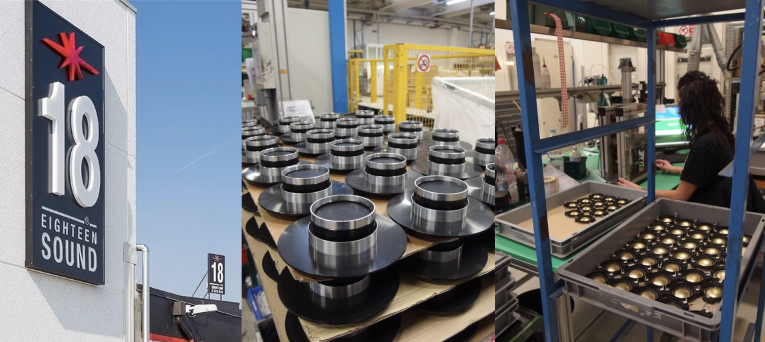
Eighteen Sound is a manufacturer of professional loudspeakers, with manufacturing facilities and offices located in Reggio Emilia, Italy, a region with strong industrial traditions. It is also the headquarters for the Landi Renzo Group, to which Eighteen Sound belongs. The company manufactures a full range of high-quality low-frequency transducers and high-frequency drivers in neodymium and ferrite versions, as well as coaxial drivers, line array waveguides, horns and crossovers. As with most OEM speaker manufacturers focused on professional audio and very demanding applications, Eighteen Sound is not a large volume operation in comparison to other companies in the segment, including other rival Italian transducer companies — and neighboring RCF — also based in Reggio Emilia.
The company’s production capability reaches 260,000 units per year and 92% of its products are for export. Around 50 people work at Eighteen Sound’s headquarters and, as we could see for ourselves, its workforce is young and extremely dedicated. With the appointment of Pierpaolo Marziali as the new CEO in October 2014, Eighteen Sound started to pursue expansion opportunities and growth strategies, following a five-year business plan established by the Landi Renzo Group board.
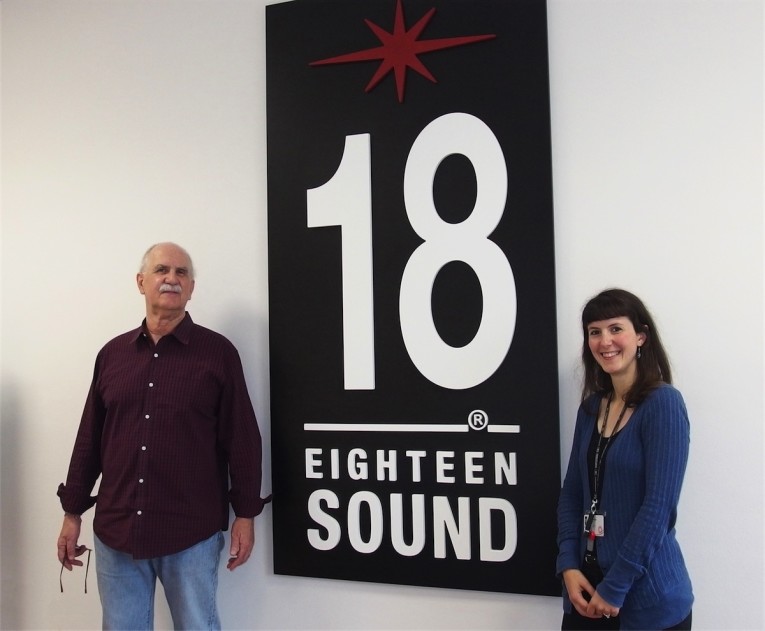
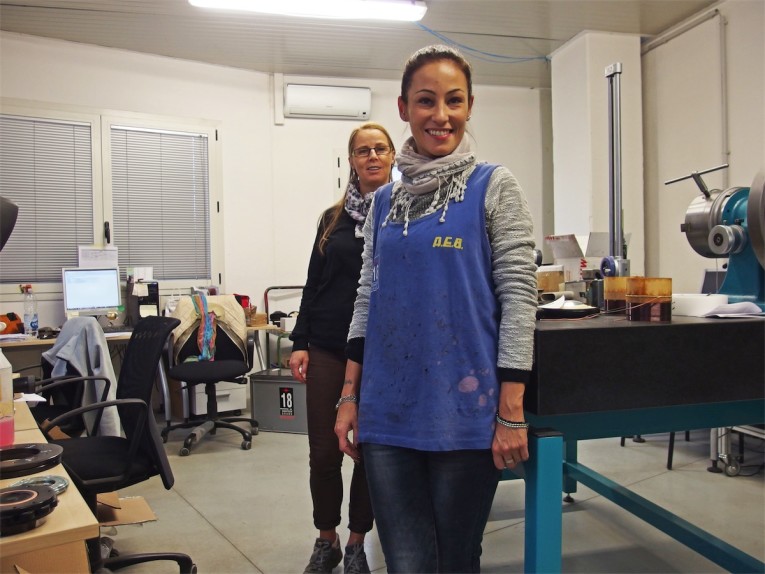
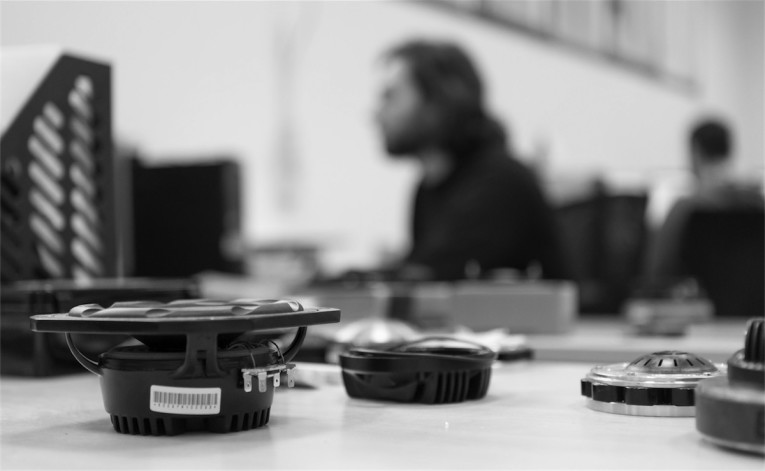
18 Years of Eighteen Sound
Eighteen Sound was founded in 1997 and its first product was an 18” woofer, which inspired the name. The original Eighteen Sound R&D and engineering team, led by Andrea Manzini, came from RCF prior to RCF’s acquisition by Mackie. They received the support of Vincenzo Baroni and Ivan Paterlini, the owners and founders of AEB Technologies, an alternative fuel company also from the region of Reggio Emilia, Italy.
AEB wanted to diversify its activities and saw the opportunity to support this group of talented loudspeaker engineers, clearly focused on high-end professional audio applications and already with promising projects in hand.
During his time at RCF, Manzini worked with George Krampera, a true industry legend and a pioneer in active sound reinforcement. Born in Czech Republic, Krampera was responsible for several incredibly successful products and developments at RCF. He left to work in transducer development at B&C Speakers, which is also in Italy. In the 1990s, he relocated to the Czech Republic to create a new company in partnership with Marcelo Vercelli, also from RCF. Their new company was called Fussion, which was eventually bought by Mackie, which subsequently also bought RCF. When Krampera and Vercelli left Mackie to create KV2 Audio, they trusted Manzini and Eighteen Sound to build the speakers they co-designed and to be their preferred OEM driver partner.
It is important to note that, apart from the mentioned facts, there is no relation between AEB Technologies and Arturo Vicari’s RCF Group, which also owns another company called AEB Industriale s.r.l. (dBTechnologies). Because of the name “AEB” (which is common in Italy) and the circumstances surrounding both companies’ history, many people assume Eighteen Sound was owned by RCF, which was never the case. AEB was looking to create a new company very different from RCF. Eighteen Sound designed different products, and the clear focus on pro audio transducers clearly worked.
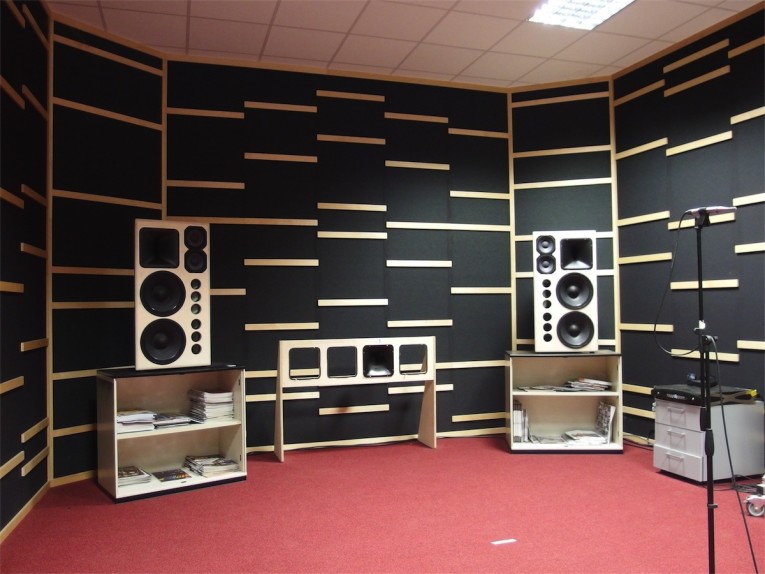
In 2010, the two original founders — Vincenzo Baroni and Ivan Paterlini — sold AEB Technologies to the Landi Renzo group, a powerful industrial conglomerate of companies with activities spanning from energy to automotive and robotics. In 2013, Eighteen Sound moved to its new Reggio Emilia world-class setting and production facilities, and announced its organizational independence from the corporate structure of AEB Technologies.
In the process, they hired industry veteran Jeffrey Cox, former vice-president of pro audio for Loud Technologies (EAW, Mackie, and Martin Audio) to help with worldwide marketing and business development, with particular emphasis on North America. As Cox says, “These beautiful Italian transducers are the key to some of the most unique and satisfying professional systems in the world. Eighteen Sound resides in many of the loudspeaker systems known as ‘flagship’ in our industry. The technologies, friendships, and reputation for excellence that are essential in a strong, ongoing manufacturer-to-manufacturer bond are here in Eighteen Sound.”
Growth Strategy
Ciare is a well-known speaker manufacturer based in Senigallia, Italy. While Eighteen Sound is a relatively young company compared to other established Italian audio brands, Ciare was founded in 1947. The company manufactures almost all driver parts, including paper pulp cones and silk and titanium domes internally and is respected in the market for its research and development efforts and expanded product line serving both professional and consumer requirements. On December 10, 2015, Eighteen Sound confirmed the acquisition of the Ciare brand.
Apart from extending the product portfolio considerably with new home-audio and car-audio market segments as well as an extended range of pro-audio drivers, including midwoofers and high-frequency drivers, Ciare could also considerably extend Eighteen Sound’s manufacturing capabilities in components and materials where traditionally the Reggio Emilia company relies on external suppliers.
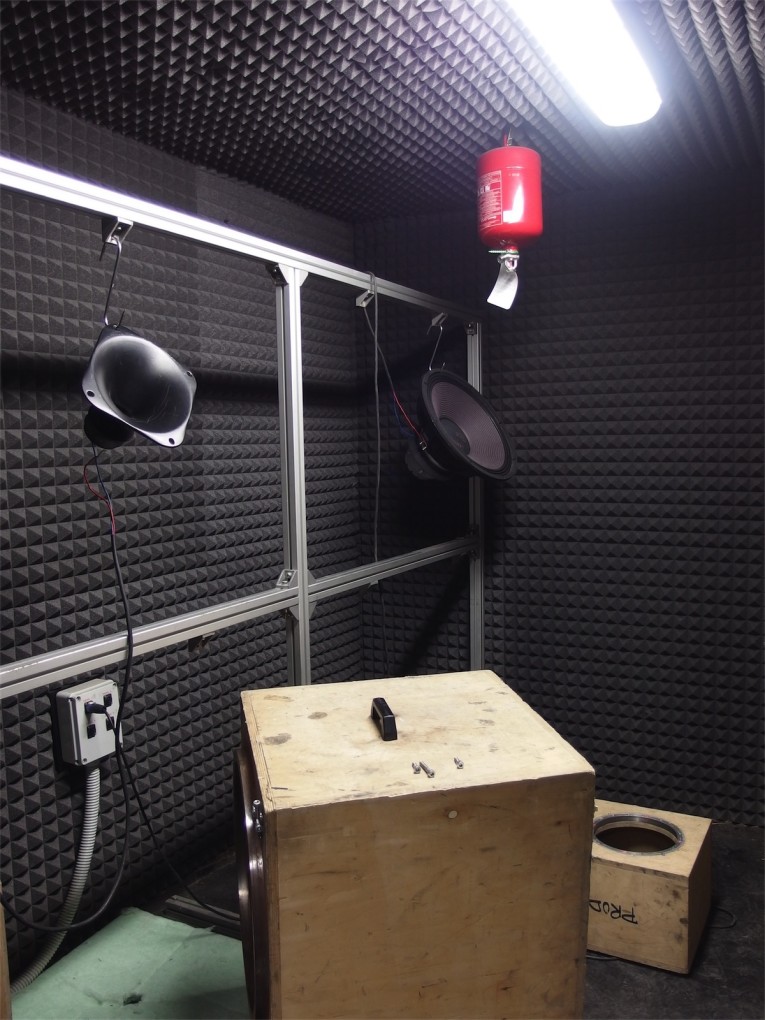
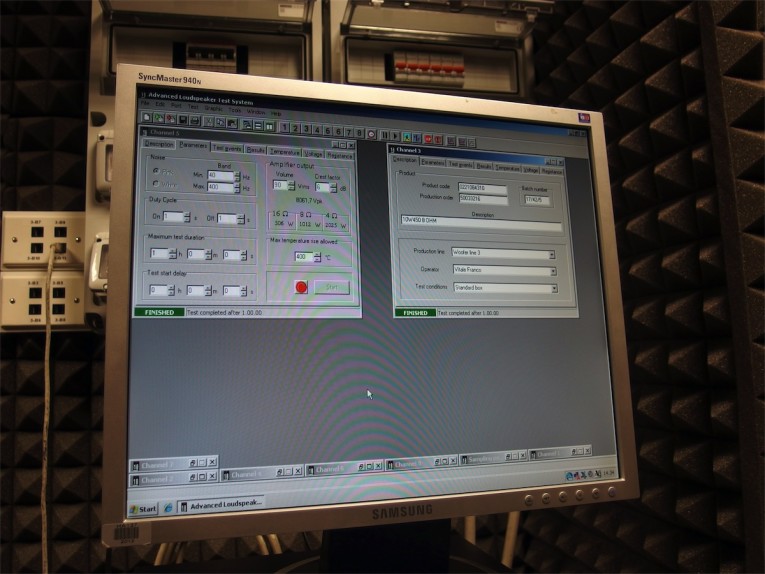
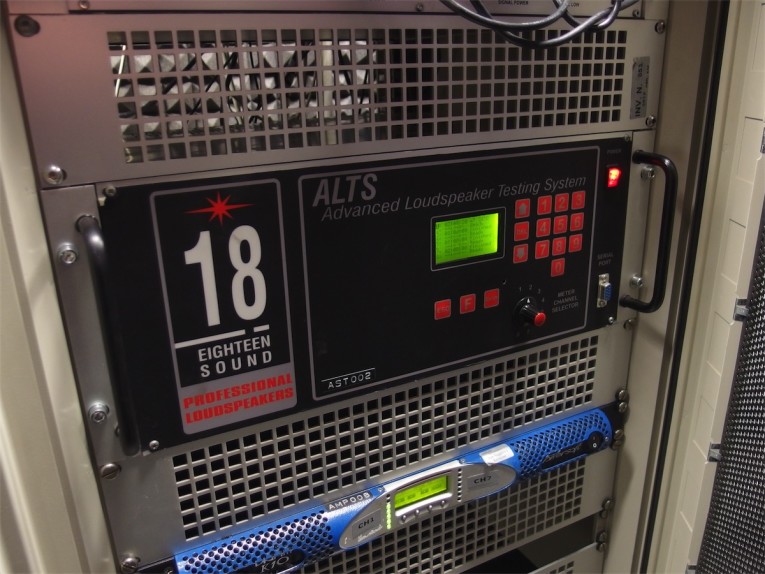
Our host during the visit to the recently expanded factory in Reggio Emilia, allowed us to discuss details about Ciare with Jeffrey Cox who confirmed how deeply impressed he was with Ciare’s factory and operations. “They have very good products with a different focus than Eighteen Sound and its market is something that we don’t speak to. The thing that fascinated me from the very beginning is that Ciare is a two-hour drive from Eighteen Sound and their capabilities and people are really good. And there is a very good product blending with both catalogs.”
“Basically they have a steel in, product out, facility. There’s not much that enters that building that’s not basically metal or raw materials. Everything is built inside, from steel to paper. I’ve been to Asia and visited many manufacturers and Ciare had equipment in their factory that I had never seen in my life. It’s very impressive” says Cox. Following the acquisition announcement, Eighteen Sound also confirmed that new products would leverage the synergy between the two R&D departments.
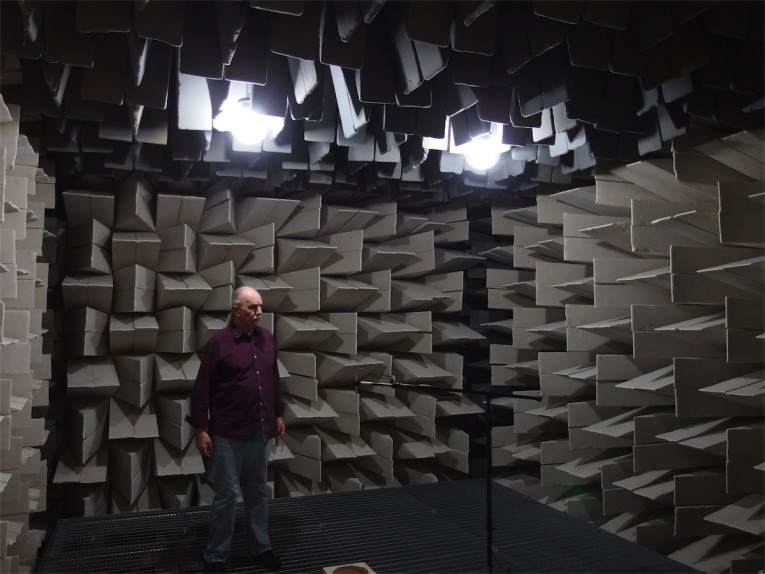
When Eighteen Sound moved to its new location in June of 2013, the company suffered a major setback. In July of that same year, a large-scale fire destroyed key areas in the newly acquired production and office facility. The fire caused serious damage and displaced key testing, quality control, and warehousing activities, but the effort to redesign and rebuild was immediate. An “even better” space within the new building was created and equipped with new state-of-the-art equipment, as well as a newly designed anechoic testing chamber. Simultaneously, an additional 1,000 m2 for logistics and warehousing was added allowing for an optimized production flow. All the new facilities were operational in 2015.
When we visited the facility, we could appreciate how Eighteen Sound was able to streamline the flow process throughout the buildings. The new factory includes semi-automated assembly lines, and operations target repeatability of design in every production unit, using proprietary equipment that precisely performs tasks such as applying adhesives in exacting amounts, while skilled assembly technicians handle the essential human interface segments.
Quality control is instituted at every stage of the manufacturing process, whether by automation and software, or close visual and tactile review. In the first stage of manufacturing, all sourced raw materials are individually tested for consistency. Throughout the production process, each stage is equipped with automation and QC workstations. Each product is tested and documented in the company’s database, before proceeding to packaging.
Guided in a full-access visit by Cox, we could see how versatile the whole production area can be, with modular production islands allowing simultaneous items, from large sized woofers to compression drivers.
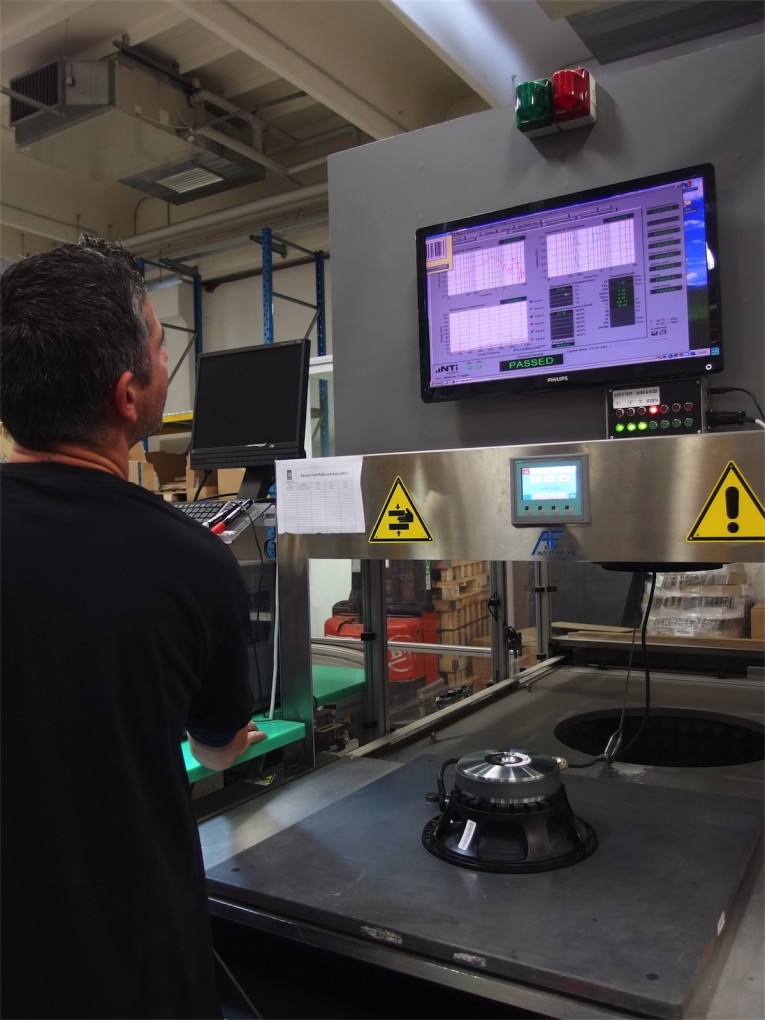
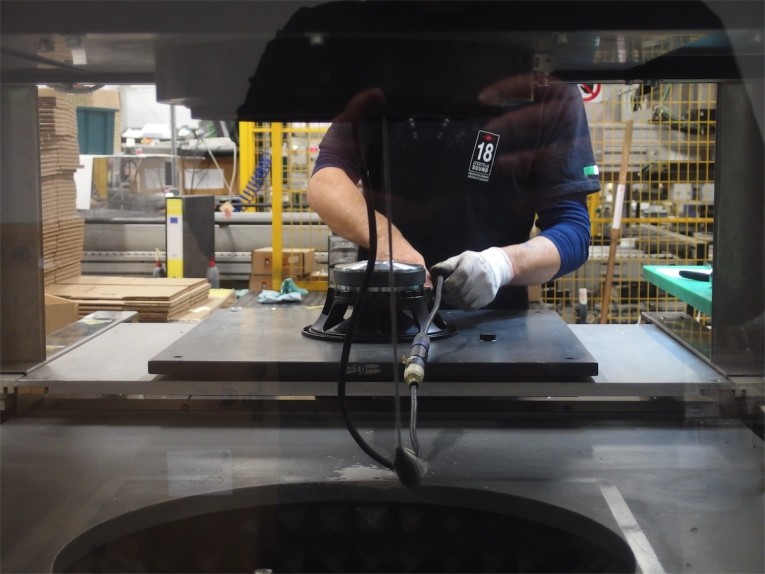
Given his previous experience with Eighteen Sound’s products while working with EAW, we asked Cox about his impressions of the company since he joined in 2013. “Kenton (EAW co-founder Kenton Forsythe) was a huge advocate of Eighteen Sound. That led me to go and listen and pay more attention to what was coming out of this company. It was clear that the performance was incredible. For me it was the accuracy of performance, the capabilities of the device itself, and the stability of the product. When I heard an enclosure that was being developed by the company, using different speakers and doing measurements, it was remarkable the capability with Eighteen Sound. Those are the kinds of decisions that designers and engineers like Kenton Forsythe, Jeff Rocha, and Nathan Butler are making. Those are the people that are key to our focus and our growth intention where we want to go. Continue to mark by what the most responsible, the most dynamic, the most adventurous are doing. What do they need? What are they looking for? What is that we have the capability for and maybe they don’t even know it...?”
Cox’s experience in the North American market also confirmed high acceptance for Eighteen Sound as a brand. “There’s a very high perception of the company as a manufacturer. The products are very competitive, incredibly competitive. I’ve been able to spend some time with designers in companies and I always see the expression in their faces when I talk about pricing and capability. The door of acceptance is there and is just a question of going through the process of evaluation and testing and acceptance, like we would expect of any professional manufacturer.”
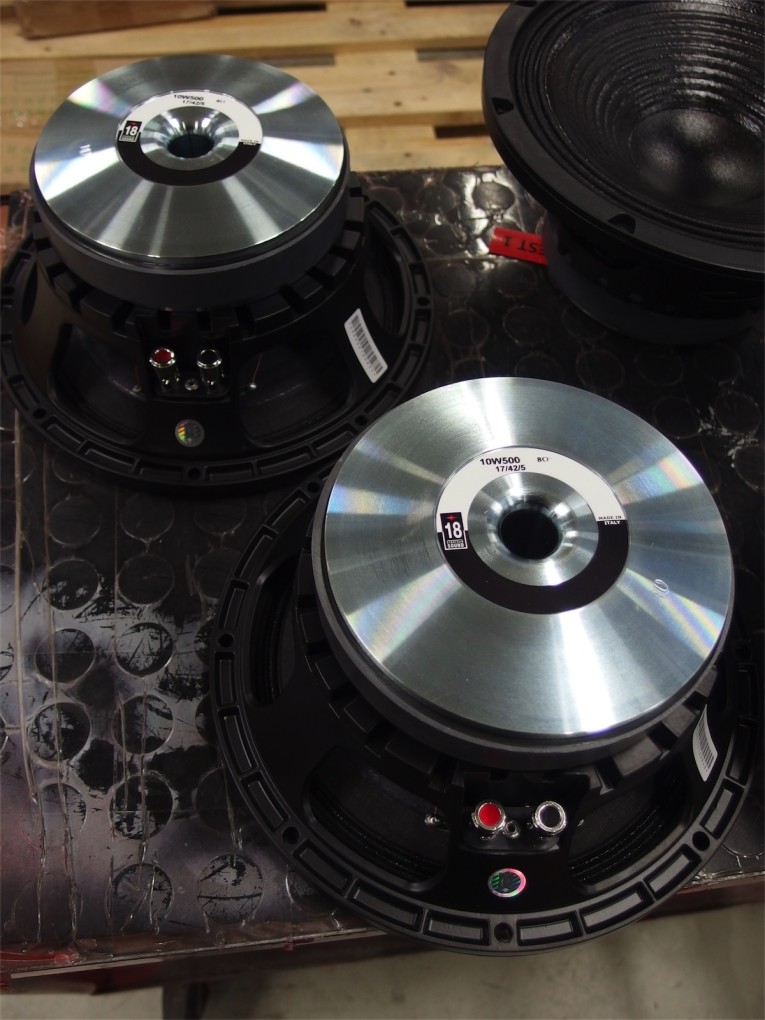
R&D and Engineering
Another crucial transition in Eighteen Sound’s evolution occurred following Manzini’s departure in November 2012. In the interim, the company hired industry-consultant Steve Hutt to reinforce the R&D department and implement new procedures and test protocols as well ensure the development of new high performance transducers, which included new beryllium products.
During our visit to Eighteen Sound, we found a solid team of transducer engineers and a restructured R&D operation, fully in control of the company’s projects. All design, evaluation, measurements, and beta versions are handled internally. The company eventually cooperates with other companies for prototyping when they have special needs, but essentially the overall design and prototyping is all done in-house.
Eighteen Sound uses a combination of Klippel tools and Audiomatica’s Clio for small signal measurements and they use Audio Precision and other audio measurement tools (sound-card-based) for displacement and acceleration data. During our visit we found the entire team busy handling multiple projects in the recently built anechoic chamber or in the listening room. Close to the power/thermal test rooms, we also found a rack with a dedicated solution labeled ALTS (Advanced Loudspeaker Testing System). This is a system developed by Eighteen Sound for measuring, among other parameters, the temperature of the voice coil during tests. The ALTS is a standalone system and only needs an amplifier. It only uses a computer to provide the user interface, which also stores a database with all the data for all the units. Otherwise, Eighteen Sound relies on NTi Audio solutions for quality control stages and the production line.

Technologies and the Future
Fabio Blasizzo, a transducer engineer in charge of Quality Assurance, helped us to categorize Eighteen Sound’s catalog. According to him, Eighteen Sound’s hallmark is a combination of technology innovations and the high quality of the final product. Many of the innovations listed in the brand’s catalog are not necessarily proprietary to Eighteen Sound but the result of many specific projects and key developments, which the company tries to make available to all manufacturers.
Among those key developments, Blasizzo highlights the Tetracoil Double Voice Coil (TTC) technology as something that is proprietary to Eighteen Sound and evolved there. TTC technology is based on an innovative magnetic structure where two different inside-outside voice coils are wound on the same former and suspended evenly in the two magnetic gaps. Key advantages include ideal motor symmetry over large displacement and excellent thermal dissipation and reduction of thermal distortion. The Double and Triple Silicon Spider technologies were also developed by Eighteen Sound.
Other key design features of Eighteen Sound’s products include different ways of extracting heat from the transducer motor to minimize power compression and increase power handling, as well as the exclusive titanium nitride coating process and the use of pure beryllium membranes that dramatically improve stiffness with great benefits in transient and intermodulation distortion response.
According to Blasizzo, Eighteen Sound was able to achieve excellent results with beryllium for demanding applications. “We have a very good beryllium dome (ND4015BE), which is something only a few companies in the world have. The sound of that product is very good.” He also highlights the company’s neodymium driver with nitrogen-coated diaphragm (NS4015N) and treated titanium drivers as fine examples of their development efforts. “Our customers truly appreciate the nitrogen treatment, for very demanding applications, since the results are similar to beryllium with much lower costs. Maybe other companies have something similar but it’s not the same treatment. For instance, B&W in their systems uses diamond treatment on the surface and the quality of the sound is very similar, but we have a different physical and chemical treatment,” he notes.
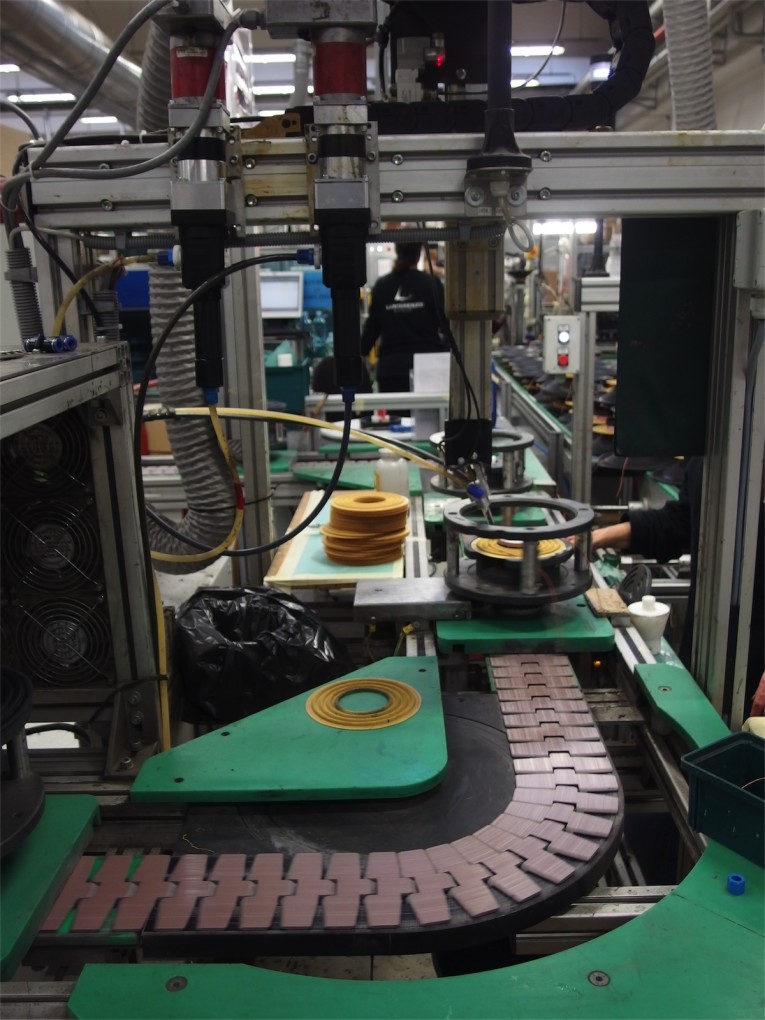
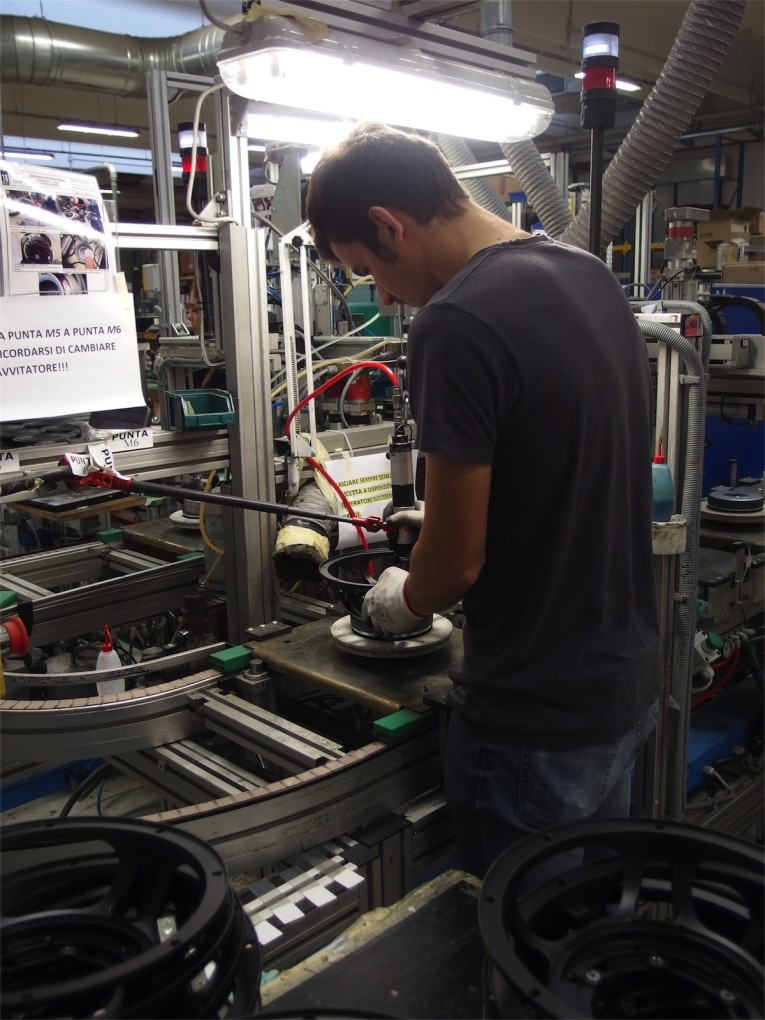
Ten years before, Eighteen Sound started to invest in new product families and recently increased the number of drivers. “In general our products are very robust, the 3” is able to manage much more power, than stated in the catalog,” says Blasizzo. In its catalog, Eighteen Sound also features loudspeakers designed to couple with iPAL Differential Pressure Control technology from Powersoft. The iPAL power amplification module features a zero latency pressure-sensor feedback applying real-time correction that maximizes the control of these specific high efficiency transducers for unparalleled output at low frequencies.
As Cox explains, the 18iD and 21iD woofers were developed in-house. “This is a market that Powersoft was defining and it was something that we felt we could provide with a better motor than was currently available and it was something that we went into on our own. Knowing the IPAL technology, Eighteen Sound developed those two products, both in neodymium.” Trying to work with increased power amplification, increased professional demands, and dealing with power compression and heat dissipation has become very important for the development of products.
As Blasizzo confirms “when we test and make choices for speakers, we consider the maximum peak power, the current that flows in the voice coil and the mechanical stress that we have on the speaker. The RMS power is pretty much the same as it was 10 years ago. It’s the peak power that it’s much more now. We have better soldering points on the terminals and we need bigger lead wire and the wire section is higher and the voice coil has much more mass than in the past.”
“On another perspective we have some speakers that allow managing as much power as we want, which even the most powerful amplifier in the world could take to the maximum level — like the 18TLW3000 woofer and other products that are able to manage very high power,” he adds.
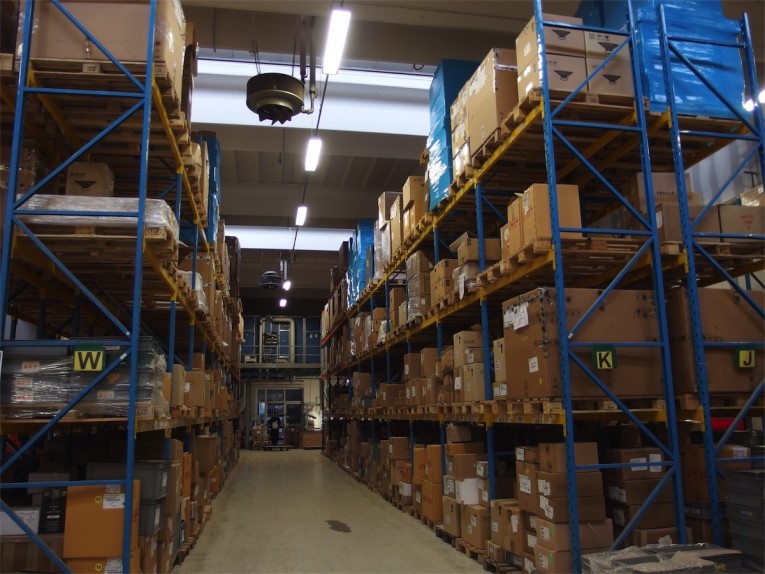
Cox anticipates we should see Eighteen Sound leading the way as a serious player in the professional audio market. “It’s clear that performance balanced by weight is a very important design element. But we also need the capabilities to have additional performance that measures. Development of products is not inexpensive at all. This is a pricey industry to be involved in. The materials to achieve that lightweight product is an expensive endeavor,” Cox explains.
“We are also looking at capability and size performance. Can we get the performance of a 10” out of an 18” size? What can we do with an 11” speaker? I would say that we are looking at those kinds of things. Performance is always key. If we have learned something in this decade, is that the technologies are morphing quickly. So why can’t we think further out of the box?” aX
www.eighteensound.com
This article was originally published in audioXpress, February 2016.
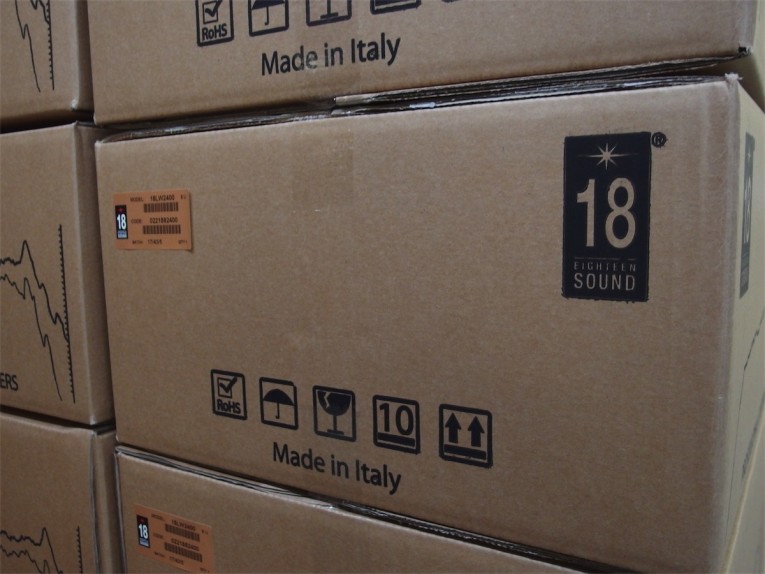