Since 1990, US Enclosure Company has developed a series of purpose-engineered composite wall materials specifically for loudspeaker cabinets that meet or beat the acoustic qualities of MDF, plywood, plastics, or metals at the same wall thickness. An added benefit is OEM loudspeaker companies can visually stand out from their competition with custom-shaped complex curved cabinets with Class-A finishes in the same cost bracket as a basic wooden box cabinet.
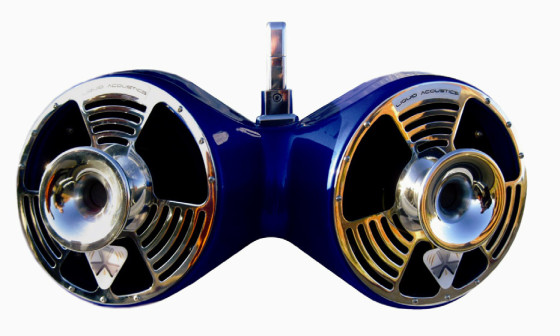
This technology can provide an important opportunity for improved market share, margins, or profits to OEM loudspeaker manufacturers. The technology is also useful wherever higher sound clarity (extreme cabinet damping) is required, from home loudspeaker systems to recording studio and mastering monitors to headphones to concert reinforcement, from auto to distributed sound to turntable bases.
Company Background and Achievements
Since 1990, US Enclosure has amassed an impressive list of commercial firsts: composite cabinet wall material designed to perform better than wood; 36” diameter carbon-fiber braced spherical loudspeaker enclosures (possibly the largest ever produced); and the largest egg-shaped loudspeaker enclosures ever sold. Other examples of unique cabinet shapes include curved wing-shaped cabinets housing two-way ported loudspeakers (see Photo 1), multidriver parabolic eggshaped enclosures, and the first spherical enclosures with egg-shaped interiors both ported and sealed.
From 1996 to 2002, the company developed a full line of THX compliant home-theater curved loudspeaker enclosures including: mains, center-channel, ceiling or wall mounted di-pole rear channel, and subwoofers. Thiele-Small (T-S) parameters won’t get a blank stare from this cabinet manufacturer.
Company policy does not allow us to disclose OEM loudspeaker client names. However, the following non loudspeaker companies have utilized US Enclosure: Boeing, Circus Circus Casino, Columbia and Princeton universities, Cirque du Soleil, Ericsson (of Sweden), and Dolby Labs both for loudspeaker enclosures for anechoic sound chamber calibration.
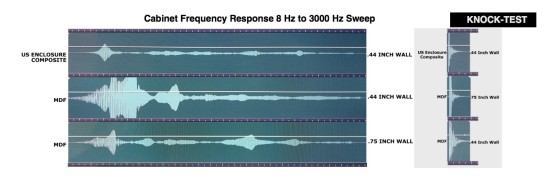
US Enclosure’s Design division can use client-provided drawings, contractor provided cabinet design drawings, or speaker stand design and fabrication for virtually any style cabinet. Custom-shaped cabinets can resemble a vase, a sculpture, a building, or a headphone. Sizes for elliptical shapes up to 4,190 ft3 and cubical up to 8,000 ft3 (20’ × 20’ × 20’). Spherical-, egg-, wing-, and parabolic-shaped cabinets can be constructed up to 240” long.
The company’s “Loudspeaker Cabinet Design Studio” page on US Enclosure’s website features more than 140 rough but thought-provoking cabinet shapes, which can be manufactured using the company’s process. The goal is to encourage creative thinking for various loudspeaker cabinet shapes, both curved and box-shaped, which would be difficult to achieve using wood or other materials. Posted as a starting point, the company expects clients to modify the shapes to their needs.
There are several key employees at US Enclosure. Among them is Kris Metaverso. He is responsible for engineering/manufacturing material developments. His 20 years of experience and two engineering degrees are buffered into understanding loudspeaker enclosures. His previous background includes engineering and materials development at United Technologies.
D.S. Ragsdale has 15 years’ experience as Vice President, Operations, and Quality Control for the company’s subcontractor. Ragsdale has comprehensive composite manufacturing and estimating experience and an engineering degree. He also provides a fundamental knowledge of the requirements needed to take a potential job from concept or engineering drawing to completion. Previously, Ragsdale was an engineer at Western Digital (Hard Drives).
He also has been involved with Engineering Contract-Project Management for companies such as Disneyland, BD Medical Disposal, Burger King, Rainbird, and an electrical utility company named Western Montana. His father, Michael Ragsdale, advises the company and is an inventor/consultant with more than 40 years of experience installing, designing, and manufacturing home and professional audio products. Michael Ragsdale has designed products for several companies including Associated Sound Systems, Altec Lansing, AT&T, Audio Logic, British Sound Reproduction (BSR), JBL, PicturTel, Uni-Sync Professional Audio Products (Trouper Series), United Recording Electronics Industries (UREI), and Vidicom.
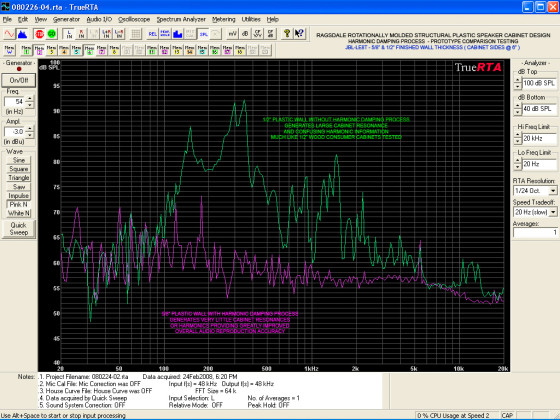
Why composites? Composite fabrication has an illustrious role in human civilization, and has many applications where sound, vibration, and strength are key issues. US Enclosure has developed the best loudspeaker enclosure materials available and the material formulations are adjustable so cabinets can be mass-manufactured to its customer’s exact requirements.
US Enclosure’s cabinet wall composites are specifically engineered for improved loudspeaker cabinet performance. These composites are based on several material dampening concepts as well as (among other factors), density, Youngs Modulus/Modulus of Elasticity, various tensile strength ratings, and Poisson’s ratio. The original material, developed by Metaverso in 1992, is named MultiModulus. Ragsdale then developed the Harmonic Dampening Material. Both materials use elastomers and up to six additional components to create encapsulated constrained boundary layers inside each component constrained boundary layer.
Enclosure wall densities can vary from 20 to more than 150lb/ft3 as determined by the application. The highest available density is well over twice the density of an MDF or Baltic birch materials. The walls are waterproof and comprised of up to 50% recycled materials, and can additionally be dyed during manufacture or painted afterwards with Class-A automotive finish levels. The walls can also be textured during manufacture to resemble wood, leather, or nearly any other material.
MDF and plywood are moderately good cabinet materials as both are constructed with glue and have a somewhat different overall modulus than the primary wood component. Nonetheless, neither material was engineered specifically for loudspeaker cabinets. Furthermore, they are expensive when producing complex curves. They can also exhibit a series of strong resonances without substantial bracing. US Enclosure’s cabinets are mold produced and strive for no more than two piece cabinets—standard box cabinets have a minimum of six pieces. Fewer vibrating panels have obvious benefits for sound quality. Curved enclosures have the added benefit of a stronger wall than the same material used in a flat-shaped wall.
These composites have been developed over the last 25 years to be effective and are fully tested to surpass accelerometer knock-tests and sound and vibration absorption tests compared to aluminum, other metals, all woods, concrete, and all plastics at the same wall thickness. Yet, the overall manufacturing cost is about the same as standard wooden cabinets. These accelerometer-based tests used similar sized actual cabinets without drivers, electronics, or stuffing.
The Knock-Test utilized a weighted ball dropped at an equal distance to measure the vibration in joules as a function of time (see Figure 1). The Frequency Response Test was created with an 8-to-3,000-Hz sweep with the driver sealed on the main driver with the cutout face inward (see Figure 2). In both cases, the accelerometer was on the back wall of the cabinet.
Unlike other quality cabinet wall material, US Enclosure’s wall materials can be easily and cost-effectively mass manufactured into any complex curved shape. This enables a loudspeaker manufacturer to avoid acoustically damaging transitions (e.g., edges and slots) in the loudspeaker cabinet as the transitions behave as acoustical sources following the primary wave in time and often reversed in polarity. With careful design of a cabinet’s internal shape, the enclosures can reduce reflective bleed-through from the interior of the loudspeaker enclosure through the loudspeaker cones.
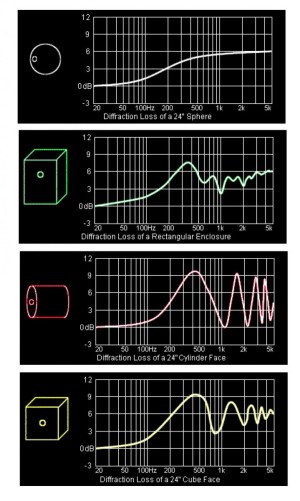
from different enclosure shapes,
as shown in Harry Olsen’s article
“Direct Radiator Loudspeaker Enclosures,”
Journal of the Audio Engineering Society
(JAES), 1951.
Curves and Other Shapes
The optional opportunity for enclosures to have complex curves allows for unique-looking or décor-friendly cabinets, which differentiate the products from the competition and provide a true corporate identity at a cost similar to wood cabinets. An additional opportunity of lowering diffraction can improve products sales, while maintaining all the positives associated with competitive enclosure materials.
Because any shape can now be produced, US Enclosure enables loudspeaker companies to have new, fresh looking products in consumer-accepted shapes. Companies can use existing drivers and electronics in curved cabinet shapes, many times without crossover adjustments. In some highly curved shapes, crossover modifications may be required.
Metaverso points out “Dr Harry Olsen in the 1930s did the first measurements, which showed curved loudspeaker cabinets reduce diffraction effects when compared to other shaped cabinets, as seen in Figure 3. Properly implemented, your products nearly disappear from the acoustic soundstage even when the system uses very inexpensive drivers.”
US Enclosure Manufacturing Facility
Located minutes from Ontario International Airport, US Enclosure’s manufacturing facility has the benefits of low-cost production runs and nearly unlimited design possibilities, with highest quality products at the lowest possible cost. And, the company’s equipment is among the largest in US (see Photo 2). US Enclosure’s manufacturing role is engineering support and dedicated production management as well as working with clients to migrate existing products to the superior cabinet materials using existing shapes or help develop and manufacture new complex curved or otherwise unavailable cabinet shapes.
US Enclosure’s CADsupported programs supported range from Audocad and Solidworks to Dassault Systems Catia. IGES files are also supported. Drawings can be adapted for fasteners and connectors as well as for ports. Prototyping via in-house 3-D printing is also available.
Economy-of-scale is achieved at the state-of-the-art facility in Ontario, CA, housing 300,000 ft2 and an additional 100,000-ft2 facility in North Hollywood, as both offer advanced manufacturing and warehouse space with the capability to deliver to virtually any destination in the world via the logistics department. This ensures that products arrive to their destinations safe and on time. Additional company departments include: quality control, assembly, fulfillment, packaging, and warehousing (see Photo 3).
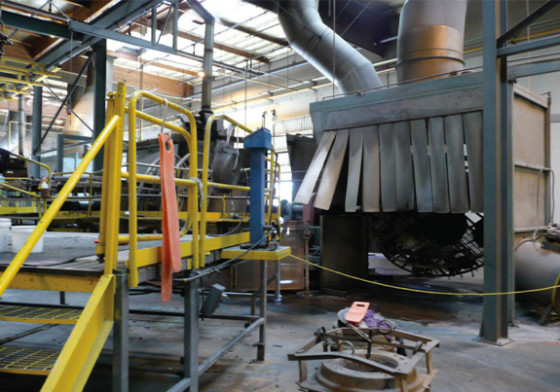
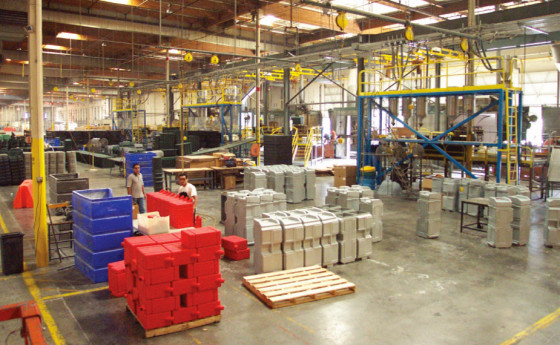
Manufacturing Capabilities
The plant produces relatively inexpensive tools for both small and large parts especially compared to other processes. Various shapes, from simple to complex, can be made at the same time for quick and economical prototypes, short production runs, and for high-volume production. In-house, a tooling department and custom wall formulation department keeps costs low. Image embossing or color graphics can be embedded into the wall material to help defeat product counterfeiting.
As Ragsdale explains, “The process begins when a client either provides a drawing or asks for US Enclosure Design to create a shape based on the client’s desire. For provided drawings, phone discussions immediately occur. Any element in the specification that has an issue is discussed and a workaround created. Also, US Enclosure provides suggestions for cost savings during manufacturing. Once a design is approved by the client, a production mold is produced. No-cost test cabinets are produced and shipped to the client until the cabinet meets the client’s needs and desires. Then manufacturing occurs.
US Enclosure provides storage at no cost up to one year after production and will execute the client-specified product releases to all locations the client desires.” “Tooling can be designed for less than 1,000 units or up to 75,000 units before tool rehabilitation. Post-prototype quantities begin at 50 units and plant capacity is more than 1,000,000 million units per year total,” Ragsdale added.
usenclosure.com
Email Brian O’Neill
2135 North San Antonio Ave., Upland, CA (US) 91784
Phone: 909-851-2273
About the Author: JB O’Neill has 25 years of outside sales experience. After college, he worked for an audio video production company directly associated with MTV Networks. This company concurrently is a full blown recording studio, which recorded live albums for artists such as David Bowie. He also has five years of experience as a radio on-air/producer.
This article was originally published in Voice Coil, July 2015.