TPCDs have since seen successful use by loudspeaker manufacturers, such as SB Acoustics (Photo 1), SEAS, Scan-Speak, and Eminence, and finished product designs from Ex Machina Soundworks, (its reference studio monitors are shown in Photo 2), and Perlisten THX home theater loudspeakers (Photo 3).
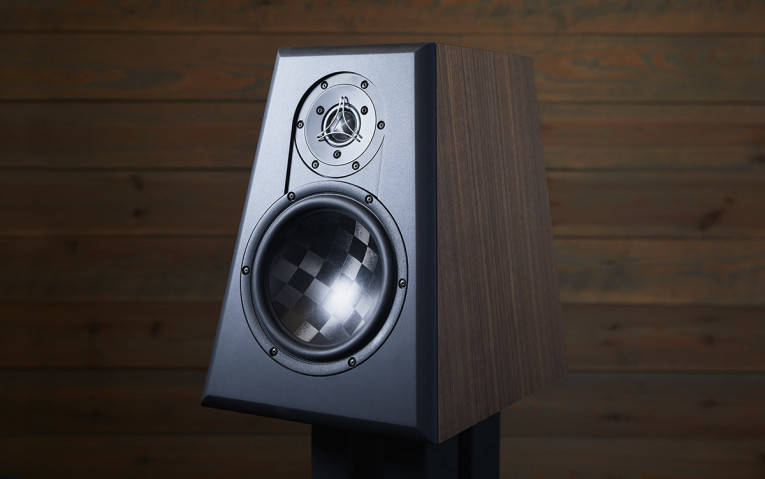
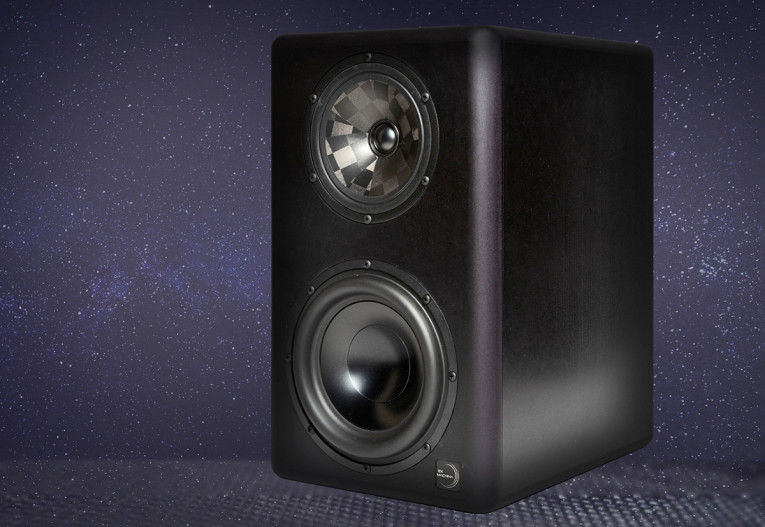
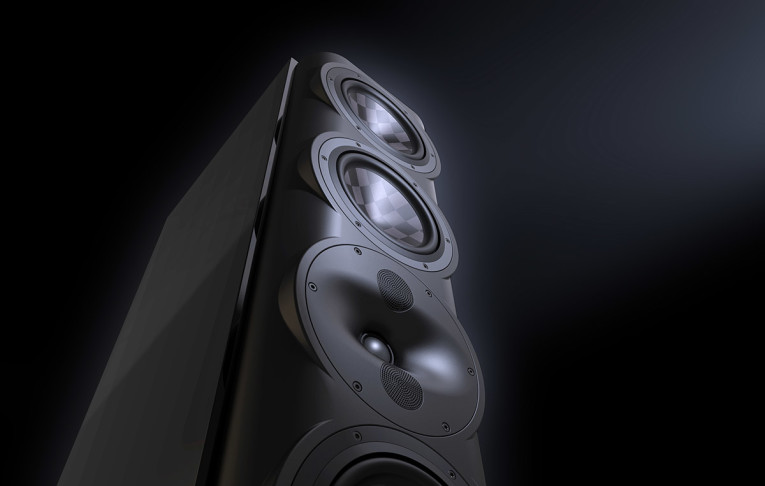
Based on the technical and commercial success of the original TPCD speaker diaphragms, in 2021 Oxeon spun off its audio-related business into Composite Sound. The purpose of the spin-off is to expedite the development of TPCD technology and accelerate growth through a company fully dedicated to the development and production of speaker diaphragms. Delivering on that strategy, Composite Sound introduced its second-generation TPCDs, which is called Composite Sound Metamodal.
Inspired by Composite Sound’s mission to enable you to make it sound like you want it to sound, “Metamodal” refers to the ultimate goal of designing a loudspeaker or transducer tailored for an intended purpose. Composite Sound understands how that process has always been largely about making compromises. And many of those compromises come from limitations in the speaker diaphragm — the cone or diaphragm is not able to transform the electromagnetic signal into sound without distorting or coloring it. Much of that in turn is related to an inability to control resonances in the diaphragms.
Very often, the measures intended to reduce the negative effects of diaphragm resonances, just adds or removes information from the original sound signal. Composite Sound engineers diaphragms that address that problem at the source. The key to doing so is to engineer the modal behavior of the diaphragms to control resonances by simulating their exact properties and behavior. The resulting Composite Sound Metamodal TPCDs are a physical representation of the simulated model that is only achievable through its unique proprietary production process.
In this context, the term diaphragm will be used to describe what can be a cone, dome, or membrane, targeting any frequency ranges from very low to very high frequency.
Avoiding Hard (Soft) Choices
It is said that the ideal speaker diaphragm should be stiff, of low density (and low mass), and well damped. Although true in theory, an ideal combination of stiffness, mass, and damping capacity is difficult to achieve in reality. The reason is that these properties are highly incompatible — materials that are stiff are usually poorly damped and vice versa. This forces the loudspeaker designer to compromise and make sacrifices. This typically involves the choice between two extremes: Either go for a hard diaphragm with high stiffness but poor damping; or the opposite, choose a soft diaphragm with good damping properties but low stiffness. The idea in the former case is to move the resonances (break-up) higher up in frequency — out of the intended frequency range — or accept resonances in the used frequency range but reduce their amplitude in the latter.
The attempt to reduce the negative effects of the resonances without removing the causes comes at a cost. As an example, maximizing stiffness to move resonances higher up in frequency tends to make the resonances’ amplitude larger when they finally occur. Adding damping tends to remove parts of the sound spectrum, add weight, and reduce the ability of the diaphragm to precisely follow the movements of the voice coil.
And relying exclusively on material properties can only take you so far because increasing the value of one characteristic (e.g., stiffness), typically reduces the value of another (e.g., loss factor). This leads to compromises and sacrifices.
What if there was a way to maximize stiffness but not compromising on damping or sensitivity? Composite Sound’s approach is not to reduce the effects of undesired resonances, but to go directly to the root cause (don’t prescribe pain killers to reduce the symptoms, cure what is causing the pain). Composite Sound engineers the modal behavior of the diaphragms to control the resonances from the start. Composite Sound TPCDs can be made with a tailored stiffness, meaning they can also be made soft, if that is desired, allowing an exact modal behavior across a given surface and shape. That enables diaphragms that are stiff, well controlled/damped, and of low mass — all at the same time.
To explain how this is done, we need to start with the material technology used in Composite Sound’s TPCDs.
The Enabler—TeXtreme Thin-Ply Carbon
TeXtreme is an advanced carbon fiber material used in the most demanding applications when it comes to ultra-light weight, mechanical performance, and durability. Examples of TeXtreme use are found within Formula One and space exploration — NASA’s drone flying on Mars is largely made of TeXtreme thin-ply carbon (Photo 4).
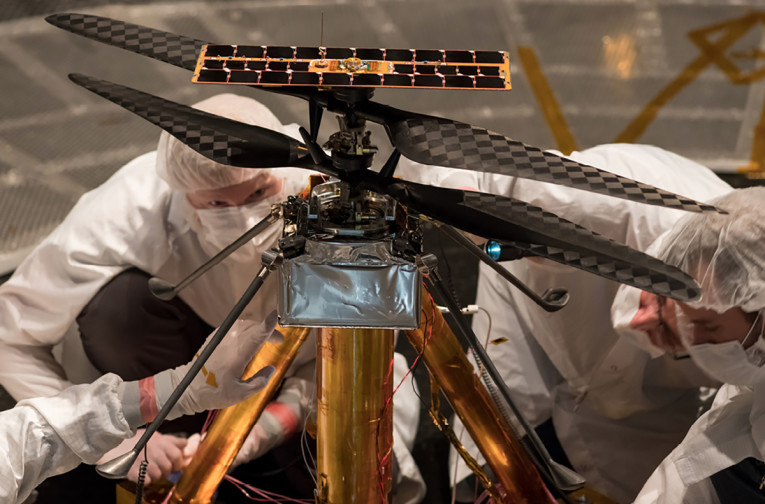
The materials used to engineer Composite Sound TPCDs are TeXtreme Thin-Ply Carbon. TeXtreme is not one material, but rather a technology enabling the design of a near infinite number of materials for which different properties can be tailored. Some specific features of TeXtreme making it a great speaker diaphragm material include:
Stiffness: TeXtreme has a straight and more optimum fiber structure than conventional carbon fabrics. The fiber structure also enables stiffer fibers to be used. This results in a stiffness far greater than conventional carbon fabrics and a stiffness-to-density ratio far exceeding readily available metals.
Ultra-light weight: TeXtreme is produced by spreading carbon fiber yarns into ultrathin tapes. Even when stacking multiple layers, the total thickness and weight is lower than conventional carbon fabrics.
Constrained layer damping: A Composite Sound TPCD made of TeXtreme consists of multiple layers of extremely stiff thin-ply carbon, separated by thin layers of a lower stiffness special resin. This creates constrained layer damping in which the resin layers stretches and compresses turning vibration energy into heat.
Distributed Modes
Besides constrained layer damping, there is another built-in damping mechanism in a Composite Sound TPCD — Distributed Modes. In a conventional diaphragm made from isotropic materials (isotropic means a material having the same properties in all directions), such as metal, paper, or plastic, both the driver and diaphragm are axi-symmetric, which will result in symmetric concentric break-up modes (Photo 5).
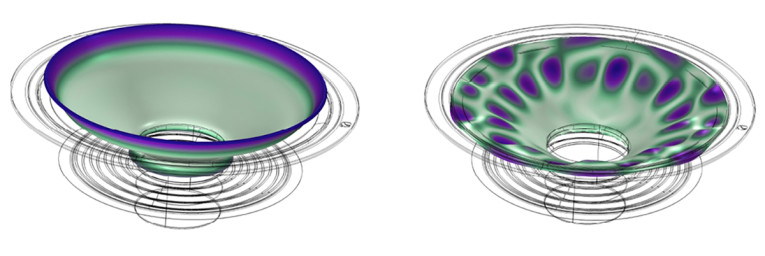
Due to symmetry, resonances will cause large areas of the diaphragm to move in and out of sync at certain frequencies, resulting in big and sharp variations in sound pressure level. Diaphragm break-up occurs. This can be seen as sharp peaks and dips in the frequency response.
A Composite Sound TPCD is by its nature orthotropic, meaning the properties including stiffness, loss factor, and Poisson’s ratio are different in multiple planes and directions, and these properties can be further engineered. The symmetric break-up modes will therefore be eliminated and replaced with smaller, local, distributed modes, each having a smaller effect on the sound radiation. This enables a combination of improved pistonic motion, ultra-light weight and controlled behavior.
A number of driver and loudspeaker companies have successfully used Composite Sound’s TPCD technology to design drivers and loudspeakers setting a new standard with award-winning products. SB Acoustic’s Satori TeXtreme speaker line has been integrated in numerous high-end designs and has received high praise, while new brands such as Ex Machina, with its Quasar and Pulsar studio monitor lines, and Perlisten with its THX Dominus certified tower, bookshelf, and custom install speakers are racking up awards among 2021’s best. Many more drivers and finished products are in the pipeline and will be launched during 2022 and 2023.
Second Generation TPCD - Composite Sound Metamodal
The term “Meta” (as a prefix for beyond/transcending) describes something that goes beyond the naturally occurring. A “metamaterial” is designed, or artificially structured, to have properties or determined behaviors that are not occurring in its natural state.
Composite Sound Metamodal diaphragms are engineered for a performance level and specific behavior that is beyond the material properties that bounds the performance of traditional speaker diaphragms. In the same way that metamaterials can be artificially structured to control light, and metasurfaces to manipulate soundwaves, Composite Sound Metamodal technology controls and manipulates resonances (Photo 6 and Photo 7).
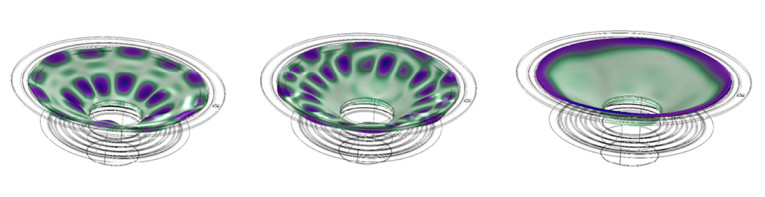
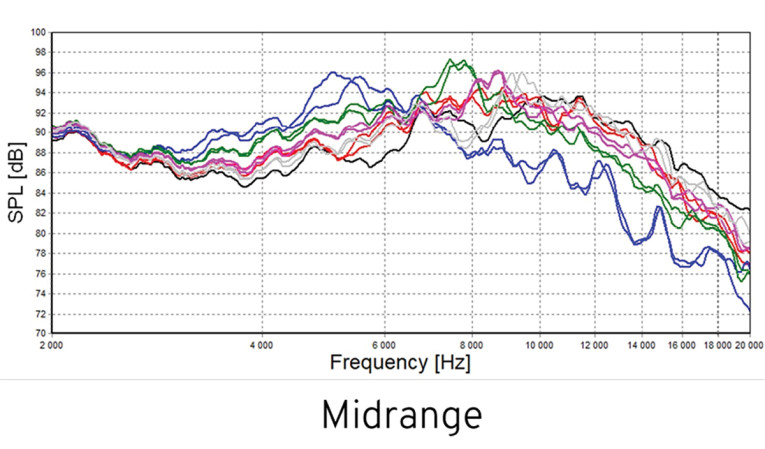
Any physical part has a certain modal behavior and depending on how it interacts with its boundaries, it will resonate in certain ways when excited. The same happens with a speaker diaphragm. By changing the properties in any location (thickness, stiffness, or density), the modal behavior and the way it resonates will change. In an isotropic diaphragm (metal, paper, or plastic), the modal behavior for a given geometry and boundary conditions is set and can’t be changed in the diaphragm itself. In a Composite Sound Metamodal diaphragm, the thickness, stiffness, and loss factor (the latter two in different directions) can be optimized at any given point. This enables the modal behavior to be tailored so that the diaphragm resonates in a desired way.
For a specific geometry, an infinite amount of different Composite Sound Metamodal diaphragms can be engineered, in which each diaphragm construction will have its unique modal/resonance behavior, frequency response, radiation pattern, and so forth. The first-generation TPCD showed that it was possible to combine high stiffness, low weight, and controlled behavior. The second generation — Composite Sound Metamodal — takes the concept further by enabling the resonances to be engineered to match the requirements a designer has for a specific diaphragm/driver/loudspeaker. As a bonus, when optimizing thickness and stiffness where it is needed, Composite Sound Metamodal enables improved pistonic motion and lower mass compared to the first-generation diaphragms.
A Composite Sound TPCD is associated with high stiffness and the Composite Sound Metamodal technology enables even higher stiffness. However, the Metamodal technology also enables tailored stiffness for which areas of the diaphragm can be made with a low stiffness and even with a degree of compliance. Making strategic areas of a diaphragm soft can be a very effective way of controlling resonances.
Since resonances can be controlled, while also having a high stiffness, it opens up the possibilities to optimize other areas. As an example, instead of designing a geometry for stiffness, the geometry can be optimized based on acoustic performance, removing limitations, and reducing compromises. That is just in line with the company’s mission, to enable you to make it sound like you want it to sound.
Simulation and Engineering in 3D
As drivers are usually axi-symmetric, most simulations are made as 2D axi-symmetric models. In a Composite Sound TPCD, the properties are optimized in three directions. To engineer the diaphragms, Composite Sound makes 3D simulations. 3D simulations are considerably more complex than axisymmetric simulations since the basic properties—Young’s modulus, Poisson’s ratio, and loss factor — vary and can be optimized in the three directions. Thickness can also be varied over the diaphragm area. Depending on the diaphragm construction, density can be made constant or also vary over the diaphragm area. While the orthotropic optimization makes the simulations more complex, the potential to vary and optimize these properties also provide unique possibilities to optimize performance and behavior and enable solutions not possible with conventional (isotropic) diaphragm solutions.
To fully utilize this, mastering 3D mechanical and acoustical simulations is crucial. Composite Sound is spending considerable resources on building world-leading capabilities in 3D simulations. Translating these complex simulations and calculations into an actual physical diaphragm that delivers the intended results is only possible with TPCDs and Composite Sound Metamodal technology.
Product Range
As detailed, there are some commonalities between the different types of Composite Sound diaphragms: the ability to control resonances, achieve high stiffness, and low mass. All steps of the manufacturing process, including materials, are done in-house, allowing the company to optimize the TeXtreme thin-ply carbon materials for the intended application. That provides a unique flexibility to engineer and tailor Composite Sound diaphragms to be used in all types of diaphragms for which resonance control, high stiffness, and low mass are important. This includes tweeters, midranges, full ranges, woofers, compression drivers, headphone diaphragms, and flat diaphragm speakers, including distributed mode loudspeakers (DMLs) and balanced mode radiators (BMRs), and microspeaker diaphragms (Photo 8 and Photo 9). There might also be other applications out there that would benefit from the possibilities of Composite Sound Metamodal technology that have yet to be discovered.
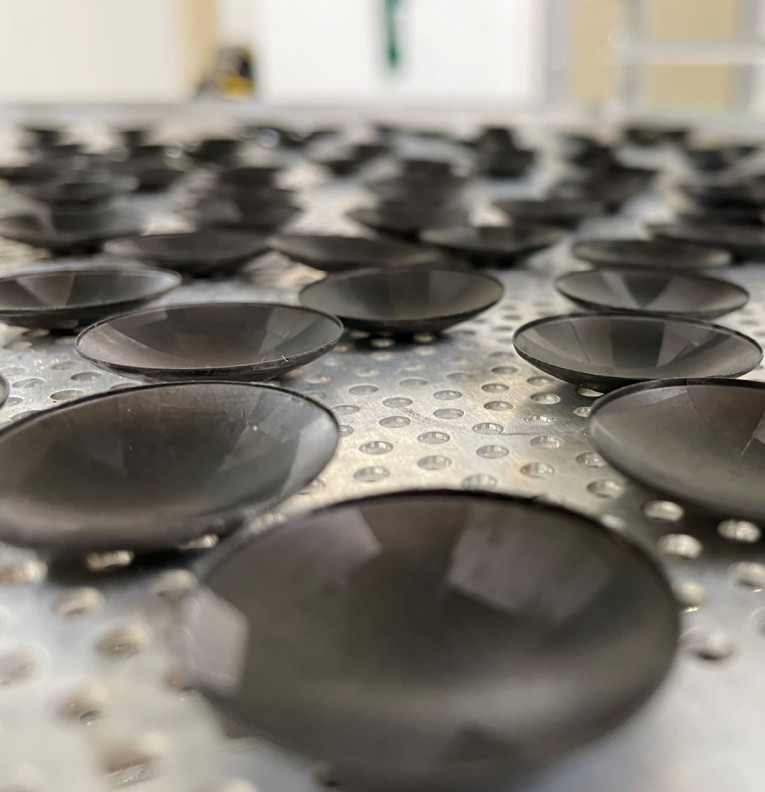
Explore, Evaluate, and Realize
While this might sound complicated — and yes, the technology behind the Composite Sound TPCD is complex — the whole process is handled seamlessly by the dedicated team at Composite Sound. Exploring, evaluating, and realizing the benefits of Composite Sound technology for anyone having an interest can be easy. To make the whole design process easy and transparent, Composite Sound developed a three-step process:
- Pre-study analysis: The company performs simulations on the diaphragm/driver for which you would like to explore the potential of a Composite Sound TPCD. The simulations will show the potential performance of Composite Sound TPCD compared to your reference diaphragm.
- Sampling: Should you wish to test physical samples, the company will provide Composite Sound TPCDs optimized for you. Alternatively, drivers can be made using Composite Sound TPCD for you to test.
- Volume production: When you are ready, Composite Sound will optimize the diaphragms for performance, quality, and volume manufacturing, and start the production of your optimized Composite Sound TPCDs.
Composite Sound - www.composite-sound.com - has only scratched the surface of what is possible with this technology. If you/your company would like to be part of the journey, receive more information, or explore the potential of Composite Sound TPCDs in your audio products, please reach out to Composite Sound directly and send an e-mail to Martin Turesson. VC
This article was originally published in Voice Coil, February 2022.
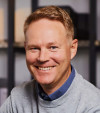
Martin Turesson is currently Head of Thin-Ply Carbon Diaphragms at Composite Sound, which is a spin-off from Oxeon AB, a leading manufacturer of ultra-light carbon composite solutions using spread tow and thin ply technology. Martin started to work at Oxeon as industrial sales manager, in 2009, and became the lead business development manager for thin-ply carbon diaphragms in 2018, promoting Oxeon’s TeXtreme solutions for the audio industry. He concluded a Master in Mechanical Engineering from Chalmers University of Technology, in Gothenburg, Sweden and holds a bachelor degree in Marketing from the University of Gothenburg.
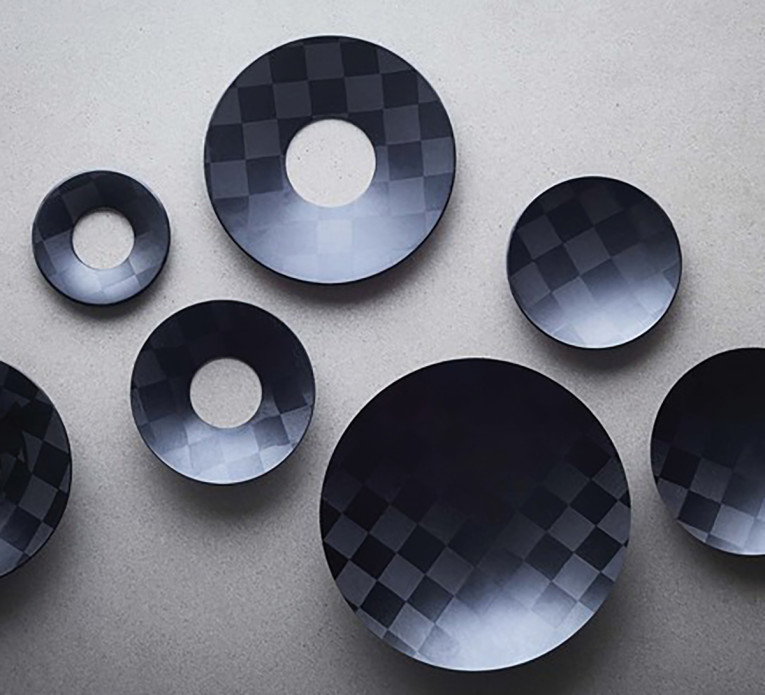