
U-Turn Audio realized that making its new tonearm from magnesium offered improved mechanical and physical properties over conventional materials. The challenge, however, was finding an organization with proven experience in "thixomolding," a unique process used in magnesium injection-molding.
To execute on its innovative tonearm concept, U-Turn Audio tapped the unique expertise of Phillips-Medisize, the largest magnesium injection molder in North America. At its Wisconsin-based facility, Phillips-Medisize applies more than a half-century of expertise to provide end-to-end manufacturing services, spanning front-end design, development and manufacturing services for highly regulated industries including medical devices made from magnesium.
As an audio innovator, U-Turn Audio wanted to consolidate multiple components into a solid, one-piece tonearm made from magnesium to reduce resonance and produce better sound. Phillips-Medisize delivered a special process used in magnesium injection molding, allowing the company to consolidate three-part assembly into a single, unified part, reducing tooling costs, supply chain requirements and assembly time.
The September 2022 launch of U-Turn’s Orbit Theory turntables featured the new magnesium tonearm that offers improved mechanical and physical properties over conventional materials. The widely acclaimed turntable has been so well received that U-Turn plans to ship the new tonearm on additional models going forward.
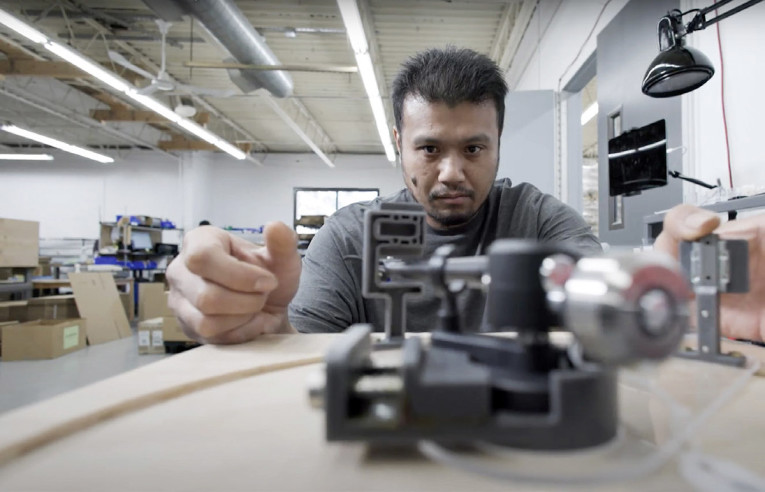
"The tonearm is basically the heart of the turntable," says Bob Hertig, president and CEO, U-Turn Audio. "It’s responsible for so much of the actual audio production. We wanted to simplify what we had by taking multiple components and forming them into one solid piece to reduce resonance and create a more rigid and better performing tonearm."
U-Turn and Phillips-Medisize worked together to unify various tonearm parts into a single, continuous piece, dubbed the OA3 Pro. Designed for U-Turn Audio’s high-end Orbit Theory turntable, the tonearm design was incredibly complex, requiring very thin wall thickness as well as a long, slender core for the tonearm’s stem. Extremely high heat and pressure involved in the thixomolding process added another level of difficulty, which was eased by Phillips-Medisize’s decades of experience in mold-design and flow analysis.
"The work with U-Turn Audio was a great collaboration as they involved us early in the design phase," says Eric Semingson, advanced development manager for Phillips-Medisize. "They were open and accepting of the design assistance we offered. The value of designing a part that is a single-piece component versus a three-piece assembly is that you reduce tooling costs, supply chain requirements and assembly time. Ultimately, the total cost of the product is reduced."
From concept to completion, the entire planning and development process for the new tonearm took more than a year. U-Turn Audio also took the opportunity to refresh other turntable features for launch of the Orbit Theory turntable.
www.phillipsmedisize.com | www.molex.com
www.uturnaudio.com
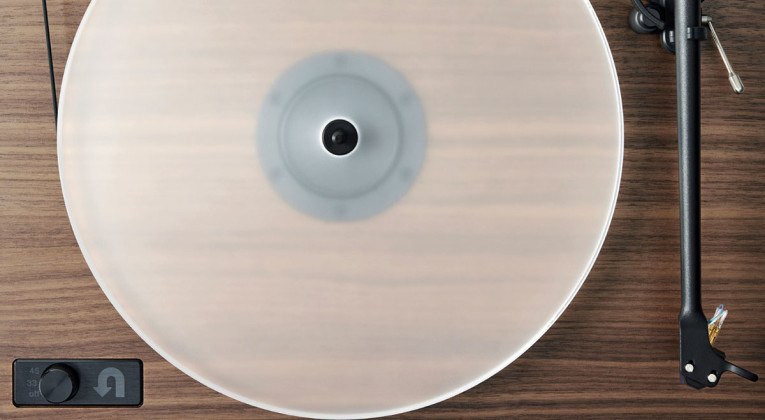