MEMS’ microphone development over the first decade was painful. However, MEMS mics became practical when they could be manufactured with high yields using integrated circuit (IC) fabrication and device packaging processes. Today, MEMS devices include microphones, accelerometers, vibration/shock sensors (e.g., burglar alarms and airbag sensors), gyros and now µSpeakers and earphone transducers. And different types of MEMS microspeakers are now entering production.
It took more than 20 years for the first billion MEMS microphones, and two years for the second billion’s production, compared with monthly production now reaching about 1 billion units. Today, MEMS microphones totally dominate smartphones, tablets, laptops, portable media players, speech recognition systems, personal computers, surveillance cameras, 3D cameras, radars, anti-theft alarms, headphones, smart speakers, music recorders, and various smart home voice command appliances, including air conditioners, refrigerators, and service robots. Compared to microphones, the implementation of Piezo-MEMS in microspeakers is daunting, due to the far higher excursion requirements.
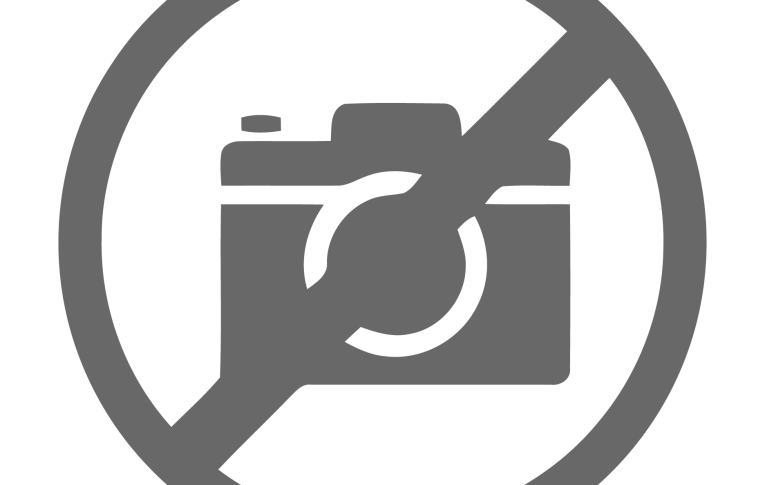
The big news is xMEMS Labs, a company founded in January 2018 and headquartered in Santa Clara, CA (click here for more insights), has announced it is now in mass production of its Montara, a monolithic MEMS “µspeaker” with a slim 1mm profile, already on its way to market. xMEMS now has 36 granted patents and more than 100 patents pending for its technology.
As audioXpress reported recently, xMEMS’ Taiwan fabrication partner, TSMC, is the world's largest semiconductor foundry (and partner for Apple's new SoC and SiP processors, found in AirPods, iPhones, iPads and MacBooks). Montara’s initial 1st tier design win is with Inventec Appliances Corp. (IAC), which selected it for the company’s flagship Chiline TR-X TWS Earbuds, powered by xMEMS Aptos, a Piezo-MEMS audio driver IC.
The µSpeaker and earphone driver market is valued at about $10 billion annually. Just considering the work needed to shift production lines, even automated speaker production line manufacturing, over to semiconductor foundries, the impact could be mind boggling. The titans of µSpeaker manufacturing typically have about 50,000 employees, while MEMS foundries producing similar quantities of devices have staff of less than 500. Yes, the wafers from the foundry will still need to be “packaged” but a few zeros in workforce numbers would be still lobed off. With the rising cost of salaries in China, MEMS microspeakers will have a dramatic impact on staffing along with other far-reaching implications.
But it is not just the fabrication of the transducers, but the promise of automated pick-and-place of Piezo-MEMS µSpeaker for surface-mount technology (SMT) board stuffing - rather than hand soldering of billions of speakers - that is bound to create the most immediate impact.
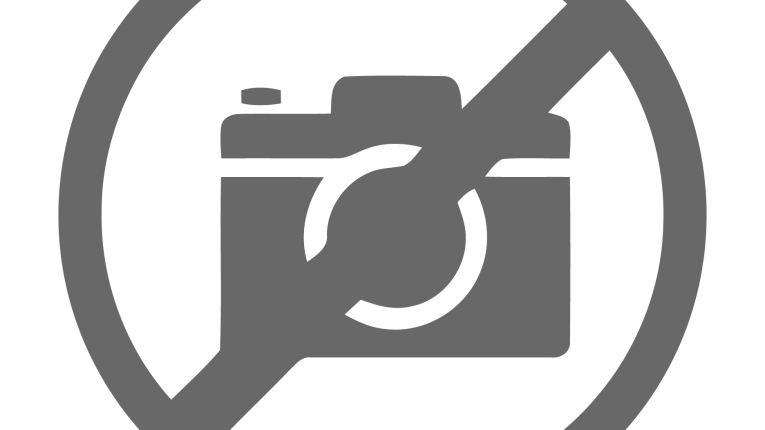
There are quite a few steps in MEMS fabrication and getting high yields at every step always seemed to be another development phase away. Earlier-generation MEMS earphones and speakers were based on a two-step fabrication process where the “motor” was fabricated in a MEMS process, then sent for final assembly of the diaphragm/suspension into the package. The most recent generation of Piezo-MEMS earphone transducers are completely fabricated in the MEMS process resulting in a high yield, very tight uniformity, and the environmental robustness ideal for true wireless stereo (TWS) applications.
In full-range occluded (in-ear) applications, these transducers achieve smoother and more extended full-range response compared to balanced armatures. In two-way or higher designs with a dynamic “woofer” driver higher sensitivity is also achieved. Future smartphones will have ultra-wide band receivers and eventually MEMS for the hands-free speakerphone.
xMEMS’ Montara is the world’s first monolithic Piezo-MEMS µSpeaker. Monolithic, meaning the implementation of both actuation and diaphragm in silicon, resulting in superior part-to-part consistency in frequency response and phase. Montara’s fast mechanical response results in the industry’s lowest group delay and phase shift and can be seen in the smooth ultra-wideband response to beyond 70kHz. For manufacturers, these characteristics reduce calibration and speaker matching. The 1mm profile, SMT-ready package and IP58 rating for dust/water simplify system design, integration, and assembly.
All this makes piezo-MEMS microspeakers ideal receivers for over-the-counter (OTC) in-canal hearing aids and implantable hearing devices (cochlear and auditory brainstem implants). These applications have small “air pumping volume” required for adequate acoustic output due to the enclosed duct and close middle ear proximity.
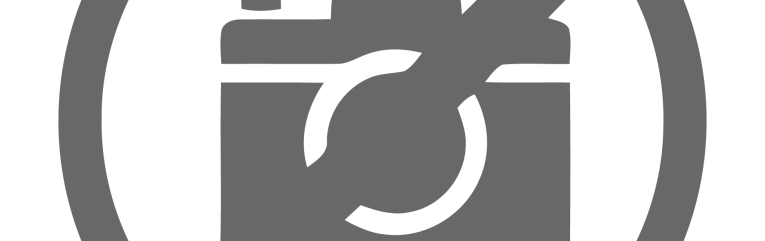
And There Is More...
This week, xMEMS announced Cowell, the world’s smallest monolithic MEMS µSpeaker. At just 1.15mm high and 3.2mm wide, the Cowell side-firing package only weighs 56 milligrams and delivers an impressive 110dB SPL at 1kHz. Cowell provides up to 15dB of gain above 1kHz for improved speech-in-noise performance and greater vocal and instrumental clarity versus electrodynamic and balanced armature µSpeakers. This is also the first Piezo-MEMS to use xMEMS’ second generation M2 speaker cell architecture, offering improved SPL/mm2, enabling increased loudness in smaller form factors. And Cowell engineering samples are available now, with mass production in early Q2 2022.
Cowell’s attributes will enable designers of TWS hearables unique benefits in high-res audio and immersive sound, as well as OTC hearing aids. For TWS applications, Cowell can be implemented as a full-range driver in occluded earbud architectures or as a small, high-performance tweeter paired with an electrodynamic woofer driver in non-occluded or leaky two-way solutions.
For hearing aid applications, Cowell is a full-range driver that is 45% smaller than an equivalent balanced armature receiver, making receiver-in-canal applications possible. The driver's superior high-frequency response, lack of in-band resonance peaks, and 15dB of gain above 1kHz make it ideal for addressing high-frequency hearing loss and improving speech intelligibility in noise. Lastly, Cowell’s speaker diaphragm is vented (front-to-back), enabling the relief of air pressure that may build up over time inside the ear canal, resulting in reduced fatigue with increased long-term wear and listening comfort.
The side-firing package and 1mm-thin profile provides for placement flexibility in the earbud making space for larger batteries and additional sensor components. And the SMT-ready package boasts an IP58 rating for dust/water, simplifying system design, integration, and assembly.
xMEMS has samples and evaluation kits ready for companies working on new designs.
For more information, visit www.xmems.com
This article was originally published in The Audio Voice newsletter (#351), November 2021.