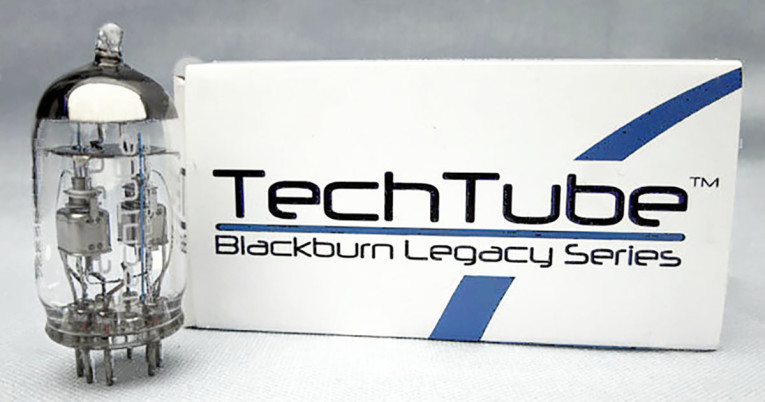
One of the reasons, I believe, that tubes sound so good is that, simply put, the electrons have plenty of space to move around—i.e., a low current density. On the other hand, solid-state devices squeeze all those electrons across tiny p-n junctions and the like. It’s a bit like egg production where transistors are the battery hens, while tubes are definitely free-range!However, before all you semiconductor aficionados start reaching for pen and paper, I must stress that solid-state devices do have an equally important place in hi-fi — an all-tube no-transistor DAC could certainly generate a lot of heat!
A Bit of History
The story begins in 1919 with the collapse of the Z Electric Lamp Company of Southfields run by Captain Stanley R. Mullard! The following year, Captain Mullard set up the Mullard Radio Valve Company Limited.
In 1924, still wanting to expand as the demand for tubes continued to grow, Captain Mullard sold half his shares in the Mullard Radio Valve Company to NV Philips Gloeilampenfabrikken of Eindhoven, Netherlands. This injection of capital allowed for the construction in Blackburn of what was to become the largest tube assembly works in the world. When the doors opened in 1938, the new Mullard Radio Valve Company Limited employed 28 staff. This grew to about 3,000 people by 1945, and by 1954 the site was capable of manufacturing 500,000 tubes per day.
At its peak in 1961, the Mullard site generated its own gas and electricity, making it fully independent of the local 3town supplies. Over 6,200 people were employed both in Blackburn and the various feeder factories supplying raw materials and sub-components to the tube works. Sadly, due to the demise of the tube in favor of the transistor, by 1984 all these factories had closed or moved to other activities. The Mullard organization changed its name to Philips Electronics Components (the main shareholder) and continued to make and develop cathodes for use in cathode ray tube (CRT) applications.
Alas, even the good old CRT is now history for domestic televisions since solid-state LCD and plasma displays have taken over in recent years as display devices. This might have marked the end of an era, had it not been for those astute people at Blackburn who realized that there is now a growing demand for tubes to be used with high-end audio equipment. The company’s name was changed once again, this time to Blackburn MicroTech Solutions. With all the local expertise (indeed some of the engineers served apprenticeships in the original workshops!) and background knowledge of tube manufacturing and cathode development, the Blackburn factory turned its attention to audio tubes with the ambition of once again being at the leading edge of tube development.
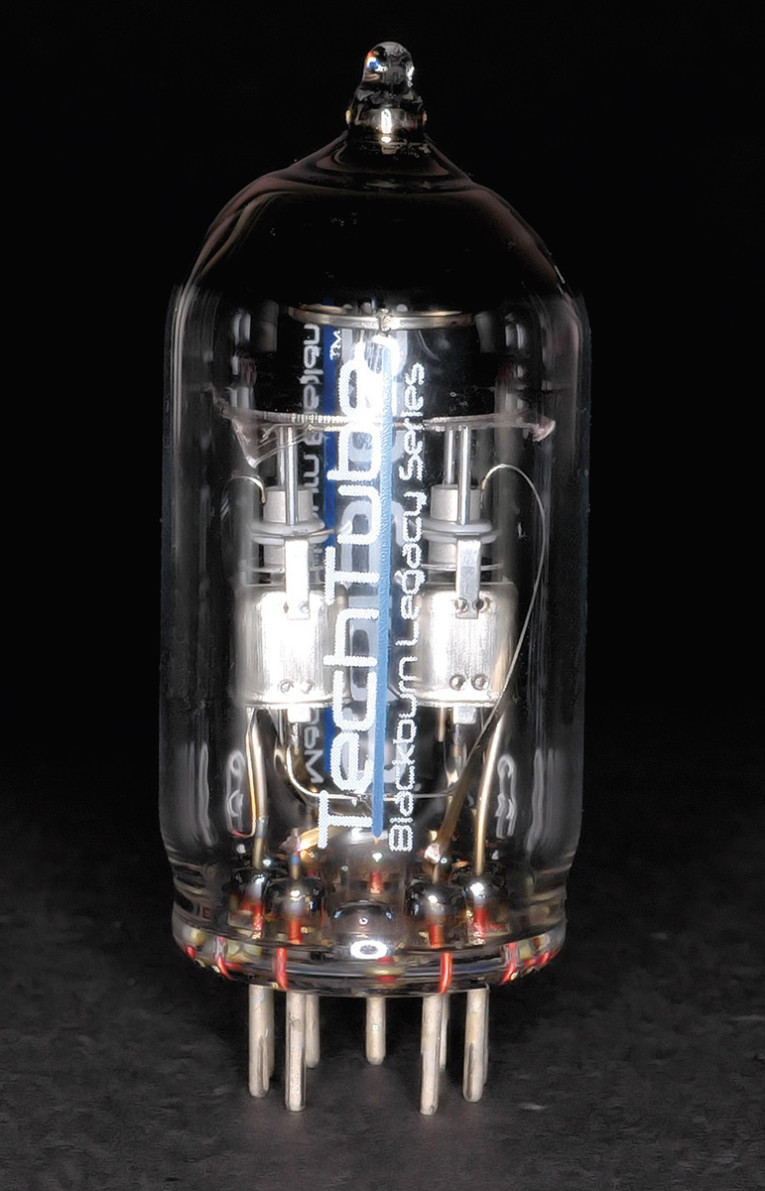
The Dawn of a New Era
The company is, of course, no longer able to use the “Mullard” name because this brand is still owned by Philips Electronics in the Netherlands. However, with the launch of the TechTube brand, Blackburn MicroTech Solutions hopes that the heritage and tradition associated with the Blackburn factory will be revived. In fact, 2008 saw the launch of the first real tube development since its initial launch back in the 1920s, with the production of the E813CC double triode.
The TechTube E813CC is functionally identical to the ECC83, but the new designation gives a clue that this is not simply a “me too” copy of an old favorite. What those clever chaps at Blackburn MicroTech Solutions have done is to channel all their expertise into electron gun technology, resulting in a radical re-think of the design of a triode tube.
Blackburn MicroTech Solutions has put a copy of an original Mullard history film on their website showing how their tubes were made. By examining frame captures from the film, you can see that a standard indirectly heated triode audio tube is constructed as a set of concentric cylinders. In the center, there is a filament that is inserted into a thin metal tube to form the cathode, which is electrically insulated from the filament and has a special coating to facilitate the release of electrons when heated by the filament.
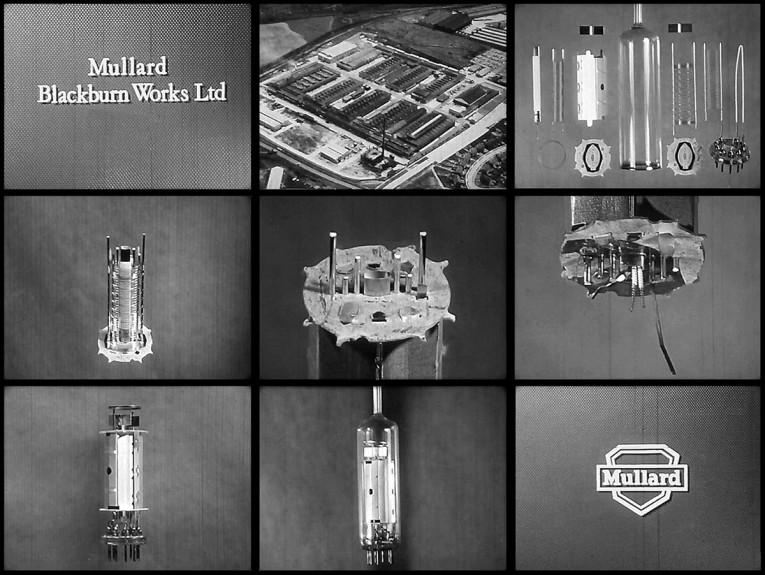
Around the cathode is the grid, which is a larger diameter tube made of fine mesh or a spiral of wire that the electrons pass through to reach the plate. The plate is an outer tube of metal that is the final destination of the thermionic electrons as they pass through the tube elements. This traditional electrode assembly is supported by two insulating mica washers — one at the top and one at the bottom of the cylinder. By making the plate positive with respect to the cathode, the electrons are attracted to it and their flow is controlled by a small potential applied to the grid—simple!
However, Blackburn MicroTech Solutions has gone back to the drawing board and developed their own structure for triode assemblies. It is a completely new way of making triodes based on microassembly techniques previously used in the CRT industry. The result, they claim, is more accuracy and, most important, more consistency.
A New Tube Is Born
The tubes come in a well-designed cardboard box that elegantly does the job of holding the tube securely without going “over the top.” I am very happy that not too much of the cost of the tube is being diverted into fancy packaging. Having said that, the blue and white printing on the tube is very refined, and the use of the Union Jack on the box leaves no doubt as to their origin!
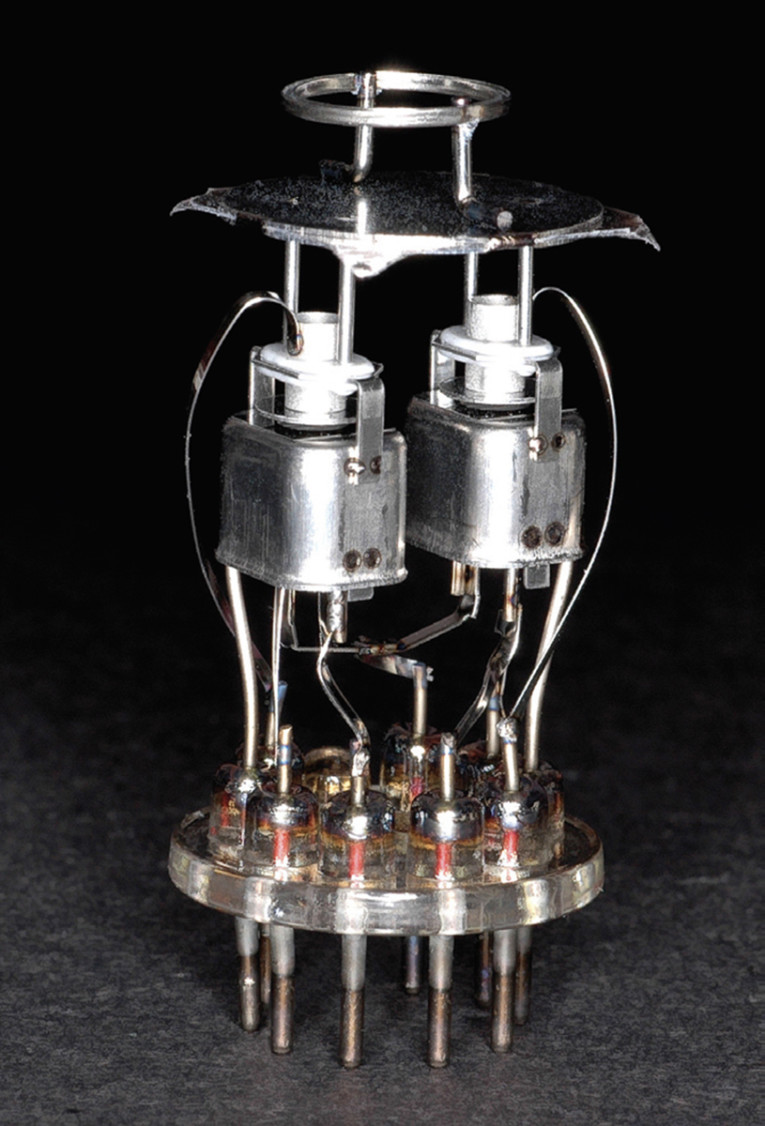
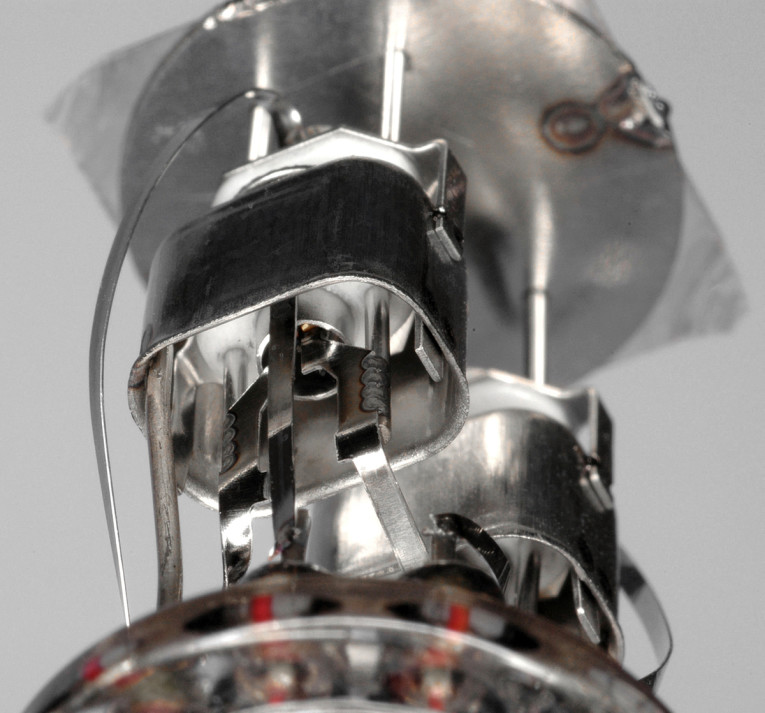
From the close-up photographs of the electrode assembly of the new tube, you can easily see how different it looks from a conventional tube. The filament and cathode assembly, together with the grid, are located inside a metal can. Instead of being emitted radially as in a conventional tube, the electrons are directed through an aperture at the top of the can that has the grid laser-welded to it. The plate that collects the electrons is situated on the other side of the grid just above the can and is in the form of a little metal “top hat.”
So the elements of the tube are of a planar construction, instead of the conventional radial design, which is strikingly similar to the design of electron guns used in CRTs. This is, perhaps, not surprising when you consider that the factory has been specializing in electron gun components for the past 40 years!
This planar tube design results in a tube with very low capacitance and minimal structural restraint. The low capacitance bodes well for a tube with excellent high-frequency characteristics. The fact that there is only one mica support at the top of the tube, instead of the more usual two, should reduce the mechanical coupling of the electrode assembly with the outer glass envelope and, therefore, reduce coloration through acoustic feedback to the tube. However, you must balance this against the risk of microphony caused by a reliance on the internal structures for support of the electrodes.
The term “microphony” describes the injection of a metallic ringing into the audio signal and is caused by mechanically induced vibrations being transmitted from outside the tube to the electrode assembly inside.
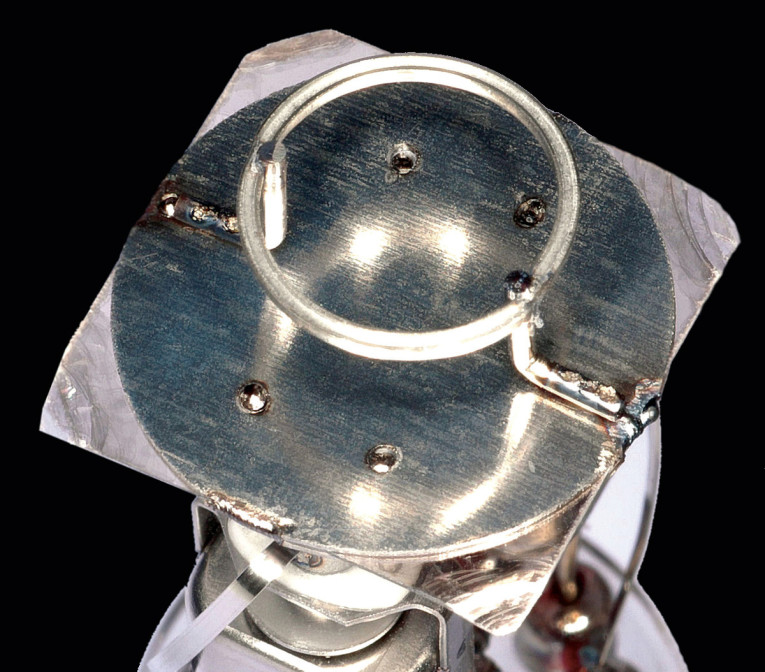
Although the E813CC has the same electrical characteristics as the 12AX7/ECC83 and also the identical B9A pin base and 6.3V heater for each triode, it is constructed to much tighter tolerances. Blackburn MicroTech Solutions claims that the tubes will have extended life. Also, the variability in performance between tubes has been dramatically reduced. Due to the small surface area of the tube and the micron cathode and plate-to-grid distances, the internal capacitance is very low indeed, with a quoted grid-to-cathode capacitance of 0.4pF (25% of that of a traditional tube) and a grid-to-plate value of 0.9pF (50% of that of a standard tube).
Finally, the filament of each triode consumes a mere 112mA. This is about 75% of the heater current of a standard tube, so the tubes should generate a bit less heat, which is a good feature. Of course, “different” doesn’t necessarily mean “better,” so how exactly do the TechTubes stand up against the competition?
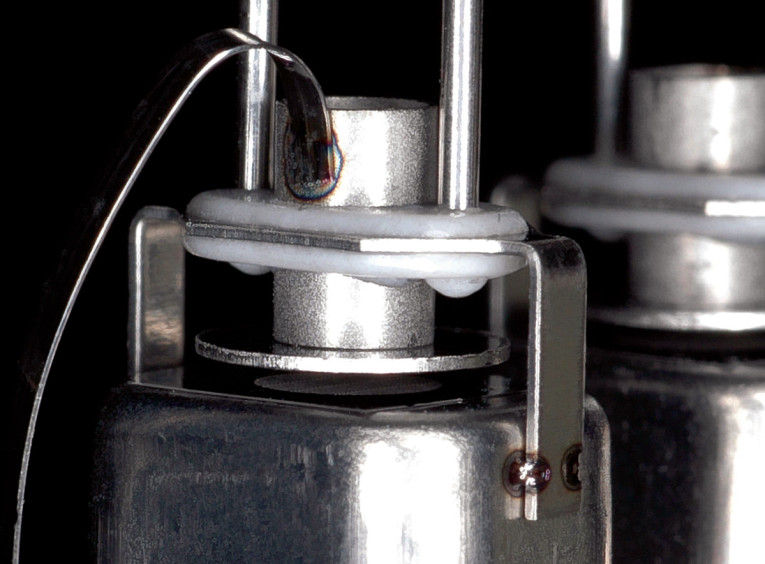
The Techtube on Trial
After some extensive listening with my top-of-the-range conventional audiophile tubes (with a price tag to match!), I decided it was time to swap the three 12AX7s in my phono preamplifier unit with the new E813CC tubes. Straight out of the box, they certainly sounded impressive in the lower registers. The bass performance was crisp, tight, punchy, and well extended. The bass drum in my well-used copy of Stravinsky’s “The Firebird Suite” (The Atlanta Symphony Orchestra—Telarc digital recording DG-10039) was truly breathtaking!
Initially, the top end was slightly muffled and the midrange was not as clear as I had been used to. Vocals were recessed in the sound stage and there was a general feeling of restraint to performances. I was expecting quite the reverse, given the low capacitance construction. However, after a few hours of running in, the situation changed dramatically. The bass performance was unchanged, but the top-end reappeared from nowhere.
Following a full 24 hours of running, the TechTubes had clearly bedded in well. The muffling had gone and the tubes produced a sound of effortless clarity and openness. Vocal soloists took up their rightful place in front of the orchestras again and electric guitars demonstrated fantastic speed and detail in all the harmonics. This is not to say that they are at all harsh.
In fact, Blackburn MicroTech Solutions seems to have achieved the wonderful tube smoothness without sacrificing clarity and detail. On jazz recordings, “hi-hats” sound crisp, fast, and sparkling. The bass notes in rhythm sections are clearly defined and well proportioned with the rest of the music.
A direct-to-disc live recording from the 1970s of “Lincoln Mayorga and Distinguished Colleagues Volume III” (Sheffield Labs LAB-1 SL5/SL6) was scarily realistic and the TechTubes gave one of the finest reproductions of this LP that I have ever heard. Similarly, with the vocals of Thelma Houston’s “I’ve Got the Music in Me” on Sheffield Labs LAB-2 SL7/SL8, the overall balance, presentation, and realism of the sound was superb.
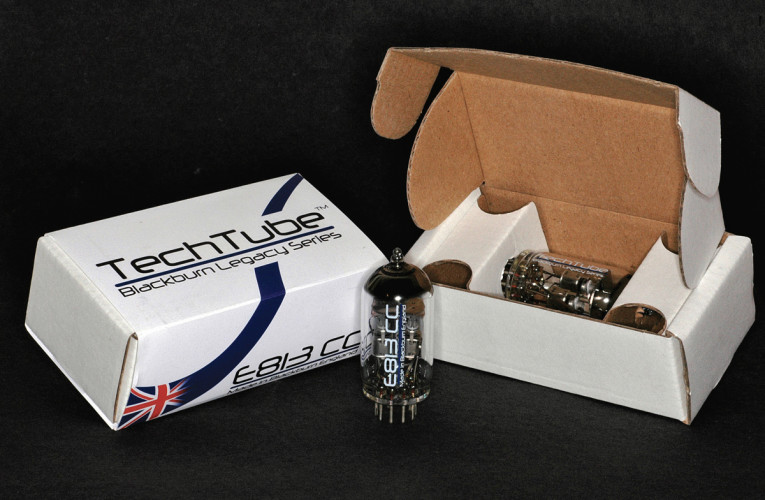
Again, the performances were thoroughly enjoyable, providing a musical and tuneful presentation that is very easy on the ears.
It was also interesting to note that these tubes definitely run cooler than their conventional counterparts. Even after constant running overnight, the case of my phono amplifier was barely warm and you could easily grasp a tube with your fingers to remove it.
Now, a word or two about microphony. Blackburn MicroTech Solutions puts a “Don’t flick the tube” warning in their literature! This is all about flicking the tube with the fingers and the ringing that this will inevitably cause. They go on to say that this effect is perfectly normal and is a characteristic of the design.
I was using the tubes in a phono stage to amplify the very tiny signals from a moving coil cartridge, so any microphonic effects would be very apparent. It was noticeable that the tubes, when new, were somewhat microphonic. However, this effect diminished remarkably during the running in period, which was quite surprising. In fact, when fully run in, the tubes exhibited significantly less microphony than my existing audiophile tubes—most impressive!
Retailing for around £30 per tube or £40 for a matched tube (about $48 and $64, respectively), the TechTube E813CC is certainly a winner. In the near future, the company is also planning to introduce the E812CC and E811CC tubes as replacements for the 12AU7/ECC82 and 12AT7/ECC81, respectively. Further downstream, Blackburn MicroTech Solutions intends to produce replacements for the EL34, EL84, KT66, and KT88 power tubes, and investigate other tubes of various types to assess their suitability for the new technology.aX
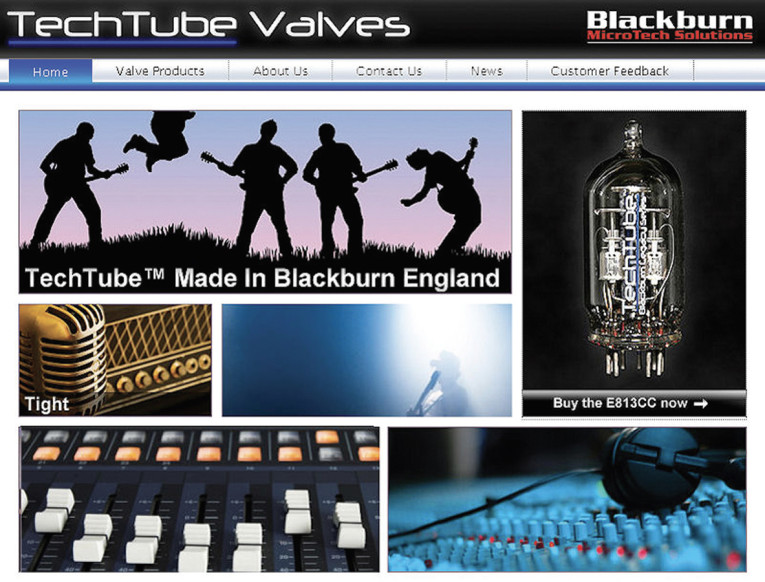
This article was originally published in audioXpress, November 2009
Note from Neville Roberts
Sadly the venture ended quickly – Blackburn Microtech Solutions went into administration in September 2009 and folded in December 2009 – just a few months after they’d started shipping out their first new tubes.
The sad truth is that Blackburn Microtech Solutions had been vulnerable since 2007 when its parent company stopped covering its losses. Its main income was as a specialist supplier of CRTs, and a fatal blow was struck when its only customer, a Chinese firm, refused to negotiate over prices. This left the Blackburn MicroTech Solutions unable to pay suppliers and a month later in December 2009, it went into administration after a hunt for a buyer failed. The report to Companies House showed that the business failed with unsecured debts of £12.4million, of which £9.8m was owed to the parent company, Holland-based LP Displays, which also happened to be in administration.
So, the company actually folded due to the cessation of CRT manufacture, rather than a failure of the audio valve production. Given the continuing increase in demand for high quality audio valves since then, would Blackburn MicroTech Solutions have survived nowadays had it not been carrying debts from its CRT days and reliant on a single customer? My guess is probably yes, given that the valves were really good. So, the demise of the British valve industry was probably down to bad timing – how very sad.
Sources
2009 Blackburn Microtech Solutions Bankruptcy Story
www.lancashiretelegraph.co.uk/news/4793721.blackburn-firm-collapsed-owing-12-4m/
Neville Roberts website
http://rssconsultancy.co.uk