Supply chain issues are a familiar problem for product-oriented and manufacturing businesses and the last two years have shown how extensive the consequences of any disruptions can be. For most consumers, the semiconductor shortage was the most visible sign of the market interdependency problems, where natural disasters in one country can cause ripple effects all over the world. The effects of the global pandemic have thrown a powerful combination of multiple, consecutive disruptions that are causing long-lasting shortages in the most unsuspected places.
Over the last two years, the audio industry has felt the direct effects of those disruptions in the supply chain across all its market and product segments. While "chip shortages" have been extensively debated in mainstream media, a much less visible shortage of apparently non-critical electronic components is actually causing wider-reaching problems for all manufacturers who have been unable to meet demands, some even forced to stop production completely while implementing product redesigns to offset those challenges. And after two years, audio manufacturers - as in many other industries - have transitioned from just-in-time and build-to-order strategies, to design for availability.
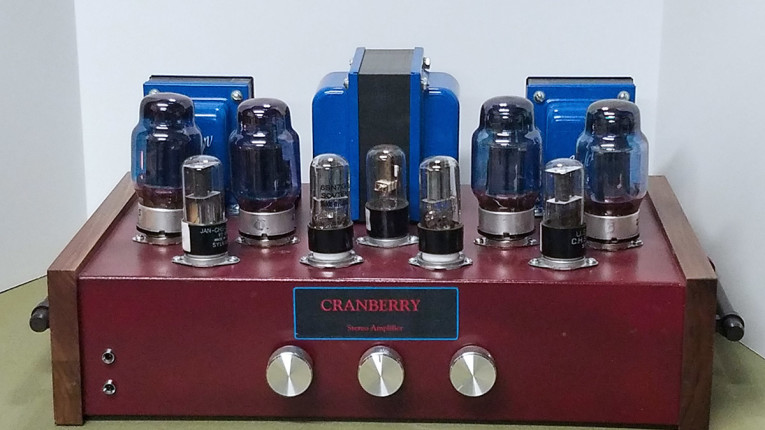
More recently, the cumulative effects of lockdowns and geopolitical tensions have caused even more strain over the supply of raw materials, directly reflected in escalating costs for aluminum, neodymium, and even more common materials such as steel and nickel. Adding the escalating transportation costs and shipping delays generates a perfect storm that is causing a complete rethink of non-essential product production. And I would like to highlight how manufacturing and logistical challenges are causing despair among many startups and entrepreneurs dreaming about new product categories and brand strategies - including the thousands of innovative crowdfunding campaigns in the electronics space that have suddenly become not viable and impossible to execute.
The global supply chain was already feeling all the severe effects of two years of pandemic, when the invasion of Ukraine and the resulting sanctions imposed on Russia further impacted the supply of raw materials, and many important parts and components. It's a known fact that both Ukraine and Russia are important suppliers of raw materials, particularly steel and aluminum, but also many critical parts and components for the electronic industry. But the scale of the impact on vacuum tube production seems to be much larger than we could imagine.
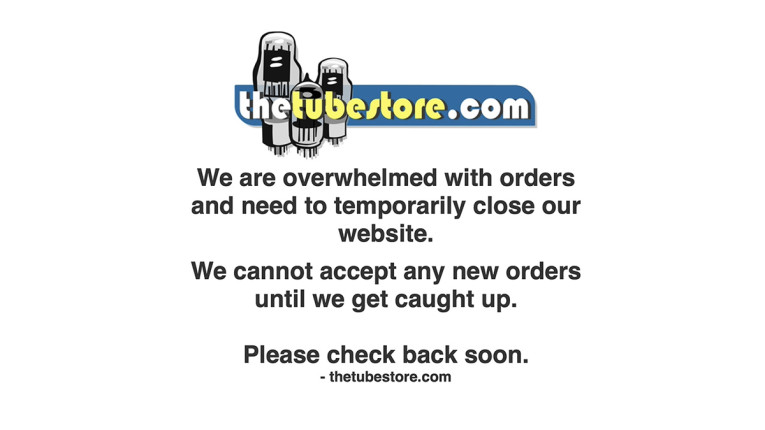
As audioXpress is getting ready to send its traditional Glass Audio May 2022 "tube issue" to the printer, most of the traditional amplifier tube suppliers have gone silent. The current situation is obviously having a significant impact on the global supply of tubes - of all the product categories that are so dear to the audio industry.
This week, while we were already in contact with some of those suppliers trying to assess the scale of the problems, companies started to make their positions more clear. Many of the European and US-based suppliers and distributors of tubes have stopped taking further orders, and some websites were temporarily suspended. audioXpress received an update from Tube Amp Doctor Musikhandels GmbH, an established supplier of amplifier tubes, which has been around since 1993, always with products designed in Germany but outsourcing its manufacturing from China.
"Without a doubt, the current situation on the tube market can be classified as dramatic,” they state. As Tube Amp Doctor explains, for years, manufacturing for the most common tube types, such as 12AX7, ECC83, EL84, EL34, and 6L6GC has been dependent on only three manufacturers. Following the closing of the Shuguang Electron Tube Factory operation in August 2019, the largest manufacturer of tubes in China, which has not reopened during (and probably because of) the pandemic, Tube Amp Doctor says that it is now working with a small manufacturer in China since 2020, but that facility is only producing the larger volumes types, while gradually introducing the production of further models.
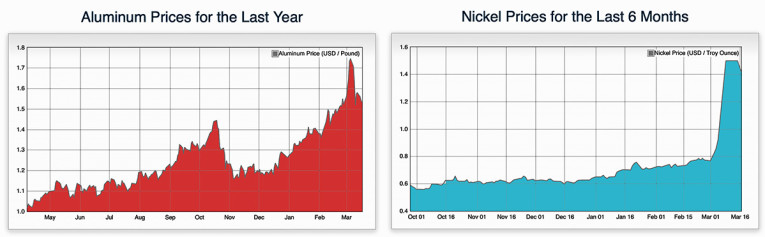
A few contacts that audioXpress established looking for clarification of those interdependencies, and to understand which manufacturing operations remained in operation, led us to realize the level of uncertainty. No one knows for certain how many tube manufacturing operations remain viable in Russia, being certain that the sanctions not only make exporting tubes almost impossible, but that the sanctions are likely to cause further strain over operations and the supply of source materials that those manufacturers in Russia need. And from China, there are significant disruptions caused by the consecutive pandemic lockdowns, transportation challenges, and cost increases.
One of the companies sourcing all its production from Russia is Electro-Harmonix (EHX). The company, founded by Mike Matthews in 1968, has been continuously expanding its business serving the music and audio industry - from its beginnings in guitar effects pedals, to being the highest volume supplier of vacuum tubes for amplifiers and professional audio equipment. Starting from New Sensor Corp., in NY, EHX today owns its own vacuum tube factory in Saratov, Russia, where it produces tubes under the Sovtek, Tung-Sol, Mullard, and Genalex/Gold-Lion brands.
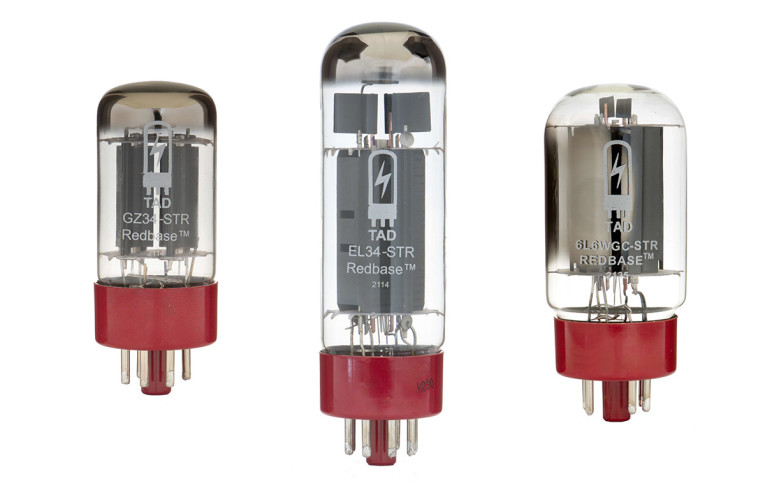
Contradicting that announcement, websites such as the popular valvetubeguitaramps.com say that, "nothing is being shipped out of Russia" and that supplies are already running very low, while some popular items that can be sourced from JJ Electronic are not expected to be replaced "until 2023." Another popular website, Thetubestore.com simply announced that it is temporarily closed and not accepting any new orders after being "overwhelmed with orders."

Meanwhile, while targeting the higher end of the audio market, Western Electric has resumed manufacturing 300B tubes in its state-of-the-art Rossville Works in Rossville, GA. Looking to better understand the perspectives for tube audio, I reached out to Charles Whitener, the entrepreneur who had the vision to carry on the Western Electric operation, and currently the company's president and CEO. In a brief conversation, we've learned that this situation is not likely to improve significantly, at least over the next two years.
In his ambition to revitalize Western Electric, Charles Whitener is probably one of the very few individuals who has visited all the tube factories that remained in operation over the last three decades. In fact, since 2006, Whitener acquired some of those factories in the US and Europe, or acquired all the machinery that was left, and which is now being used at the Rossville Works to produce 300Bs, but can also be applied to revive production for other models.
But, as Whitener states, no effort in tube manufacturing will be able to change the current situation in a short period. The challenges faced being cumulative in key areas that he acted upon over the last decade. First by acquiring the machinery, production equipment, and processes that are required. Second, training the people to resume production and achieving quality production yields, which is something that cannot happen quickly. In fact, as he confessed, Western Electric had to surpass many additional challenges over the last five years, including finding a supplier for the glass tubes, following the disappearance of the incandescent light bulb, and the closing of the last remaining glass factories, including General Electric, Philips, and Osram. Apparently, the quality of glass required for vacuum tubes is now only available from a single source in Germany, and requires volumes that far surpass years of production for the audio industry. Adding the rising costs of key materials, such as nickel, means that the investment level required for a manufacturing operation of tubes is higher than ever.
If there is a company well prepared to challenge those obstacles and anticipate the timeline, it will be Western Electric. Over the last two decades, Western Electric acquired the know-how and machinery from the Philips Mullard operations, including grid and cathode machines, processes, and all the metal parts from Siemens, Mullard, and Telefunken. And that helps explain why Charles Whitener is optimistic that he will be able to meet future demand, even considering the costs of shipping and rising costs of materials.
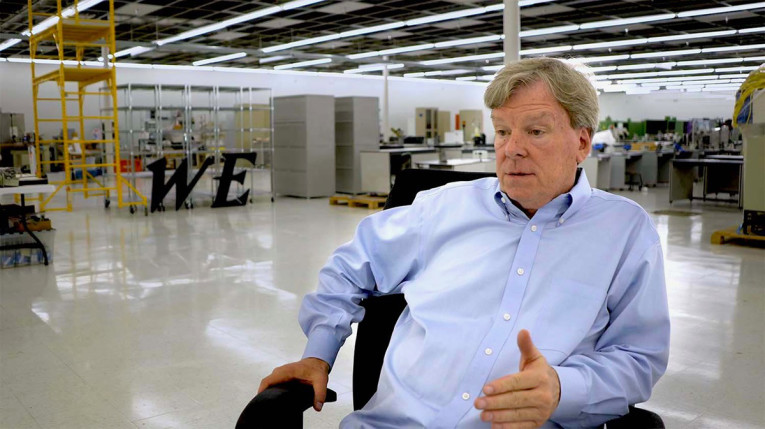
"We are already up to our necks meeting demand for the type 300B vacuum tube. However, our factory was originally designed to sustain production of other tube types," they add. The company created a page for those interested in receiving more information about those plans for potential supplies of 12AX7, 6L6, EL84, 6H30, KT88, and 274B types. On that page Western Electric predicts: "in light of recent worldwide events, we believe our capacity to do so may become vital to the industry."
This article was originally published in The Audio Voice newsletter (#367), March17, 2022.