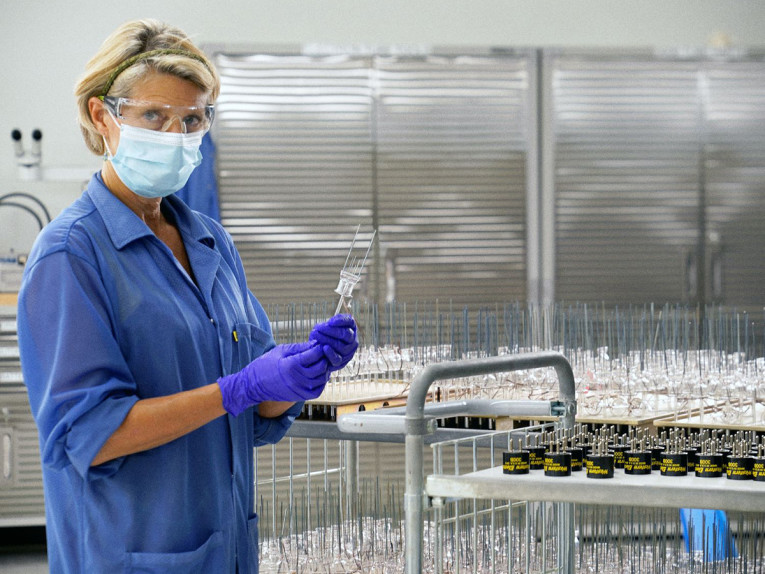
“We’re honored to continue serving music listeners and amplifier designers who’ve trusted the quality of our electron tubes for years,” says CEO Charles Whitener. First introduced by Western Electric in 1938, the 300B is now praised among audiophiles for its ultra-long life and sonic purity. “Making sure our customers get the ‘real thing’ is a great challenge. We rely on decades of experience and a strict adherence to quality standards set in stone long before our time,” Whitener adds.
With the return of the famous triode comes the re-establishment of Western Electric manufacturing — now at the company’s new facility located in Rossville, GA. Officially established in 2018, the Rossville Works facility contains an entire wing dedicated to continuous 300B production. On the production floor, state-ofthe-art, modern machinery harmonizes with original machinery — some first commissioned in the 1940s. Easily the most advanced tube operation in company history, the Rossville Works represents a commitment to the future of the vacuum tube industry and high fidelity audio.
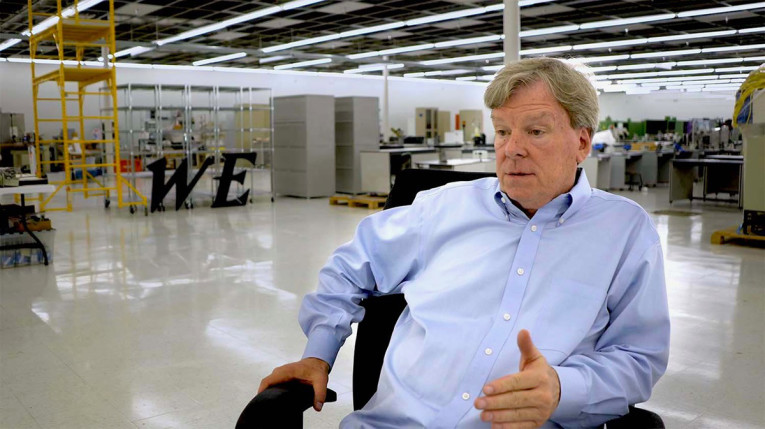
Anticipating the official announcement of the return of the 300B and Western Electric’s commitment to quality manufacturing, audioXpress had long planned a visit to the new facility, which unfortunately was not yet possible in time for this edition. However, Whitener was kind enough to grant a brief interview and he supplied some exclusive photography, which we used to put together this article.
The Interview
Richard Honeycutt: Can you give us a summary of the history of Western Electric’s vacuum tube manufacturing from the New York, Hawthorne, Allentown, and Kansas City Works to the present?
Charles Whitener: Western Electric is an American manufacturer, founded in 1869, with an enduring relationship with quality. Today, we make stunning listening experiences through innovative audio equipment and legacy hi-fi like the 300B vacuum tube. The history of our company has strong ties to the history of the vacuum tube itself. In 1912, Western Electric engineers witnessed a demonstration of Lee de Forest’s “Audion,” a primitive yet ingenius device that showed them—and subsequently the world — the amplifying power of the high vacuum tube. AT&T purchased de Forest’s patent and Western Electric’s Engineering Department went to work, setting up a small tube shop on Hudson Street in New York.
The operation was small, but grew to employ more than 1000 people by 1929. As demand exploded, tube manufacturing was expanded to the Hawthorne Works and later the Allentown Works. Western Electric supplied millions of tubes of various types to fuel the electronics industry in the US, and as Westrex internationally.
As the era of the vacuum tube faded, all remaining operations were moved to the Kansas City Works. This move was completed in 1970. Eighteen years later, Western Electric employees manufactured what they thought would be their last 300Bs. I approached AT&T in 1992, finally re-establishing manufacturing at the same Kansas City location in 1996. The Western Electric name, all of the tube specs, tooling, and machinery — not to mention decades of employee know-how — was going to disappear. In a way, we rescued it all from being put on a shelf forever.
We’ve been manufacturing legacy products like the 300B and new high-fidelity ever since then. Our latest manufacturing facility, the Rossville Works is our fines yet. Our staff operates state-of-the-art machinery alongside much of the old machinery to produce the same incredible product people have known for years.
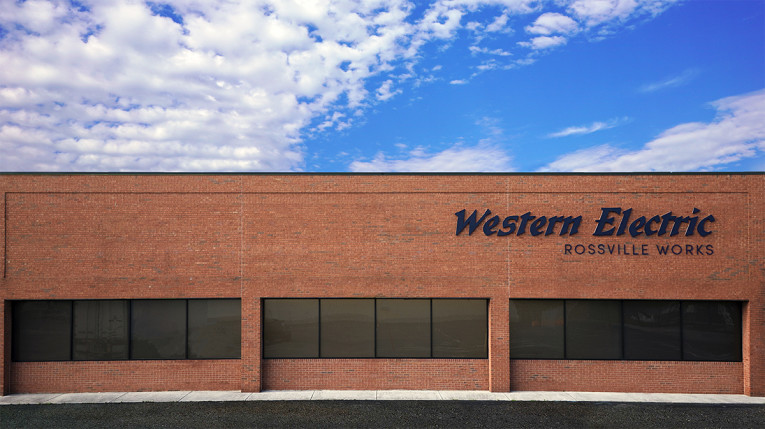
Richard Honeycutt: How is the 300B different from other power triodes, other than its iconic status?
Charles Whitener: The real magic of the 300B is in the filament. An equipotential cathode allows transconductance to be sustained symmetrically across the anode, when excited with direct current. The nickel filament core is from a 1963 melt from the Hawthorne Works. It’s coated with a proprietary, double carbonate mixture, which contributes significantly to the tube’s legendary long life and overall performance. In fact, the tube’s metallurgy is based on designs originally intended for underwater sea cable transmission, where minimal maintenance is obviously essential.
I would also add that because the 300B has a directly heated cathode, as opposed to indirectly heated, it offers superior impulse response. Thermal latency is reduced. So, when we experience the pleasurable sound of a 300B, we’re experiencing the low thermal inertia of a directly heated cathode.
Richard Honeycutt: In general, how do your 300Bs compare with other ones now on the market?
Charles Whitener: Those who love the 300B know there’s nothing like the real thing in terms of performance, longevity, sound, and overall quality. As we’re now set up for continuous 300B manufacturing, we hope people are less and less inclined to resort to replica tubes. Some out there are better than others.
But the 300B is, as the saying goes, often imitated, never duplicated. When you see the name on the base, you know you can trust the quality. We guarantee it with a five-year warranty.
Richard Honeycutt: If a customer buys a pair or quad of your 300Bs, how much advantage will they notice if hand-matching is chosen?
Charles Whitener: All pairs and quad sets that we sell are computer-matched based on a range of performance characteristics. We perform this test as part of our final inspection. Offering tubes that are as close to identical as possible gives the end user confidence. They have put lots of careful thought into getting the best sound possible with every other component in their setup, so we’d hate for our product to throw off the balance! Particularly with push-pull configurations.
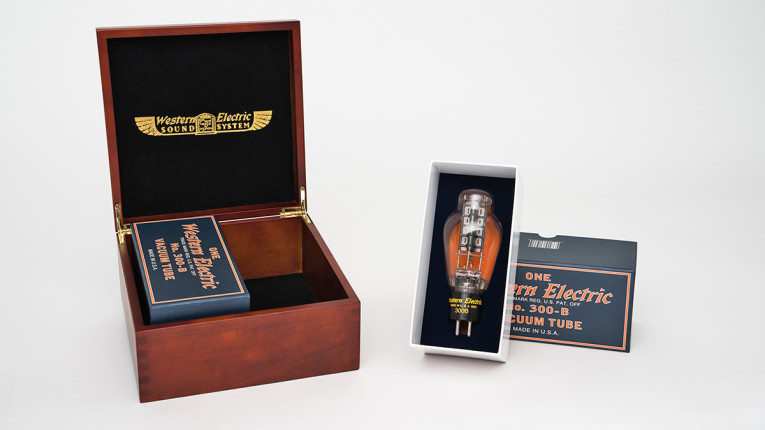
Richard Honeycutt: How big is the market for premium vacuum tubes presently?
Charles Whitener: Since we re-established manufacturing in 1996, the market has remained niche. But we also have reason to believe it’s growing. When we made the official announcement that we were bringing back the 300B in 2017, we did this with the idea to reach new 300B lovers. We then launched an online pre-order campaign and were met with more interested people in one week than we had been in the past 10 years combined. We’re now in regular production and look forward to seeing how far our reach as a manufacturer can go. Niche? Yes. But the demand for good sound will never go away.
Richard Honeycutt: What does your crystal ball show for the future of hollow-state audio equipment?
Charles Whitener: As long as there are new amplifier designs, particularly single-ended, people will need 300Bs. It seems every week we learn about something new and exotic from customers and friends in the industry. As a tube manufacturer, we’re always encouraged by these new designs. It produces steady demand for 300Bs and shows the world that it’s not always about nostalgia and legacy products.
I’d also like to add that these new products, our 91E Integrated Amplifier included, produce an outflow of conversation and memorable listening room moments. This is the world of hi-fi. It’s up to us to influence and educate younger generations about good sound and encourage them to enter the conversation. Anyone who has listened to their favorite music with a good tube amplifier knows it’s an experience worth sharing. aX
Western Electric | www.westernelectric.com
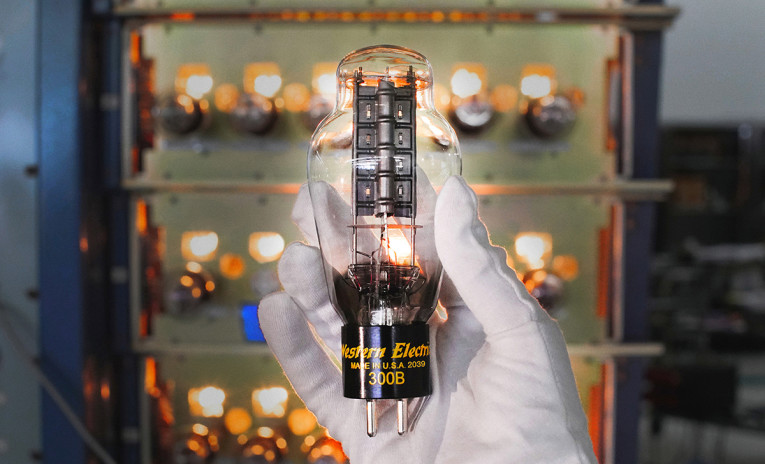
