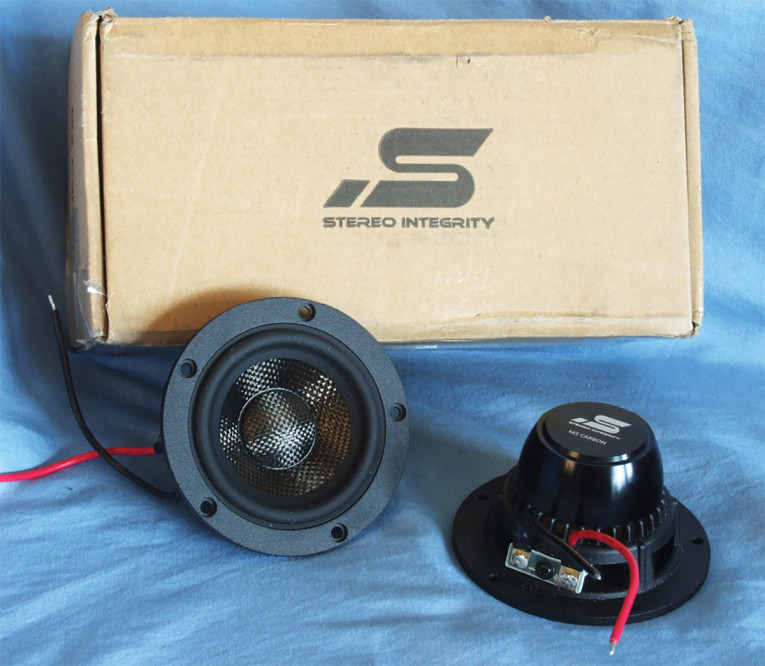
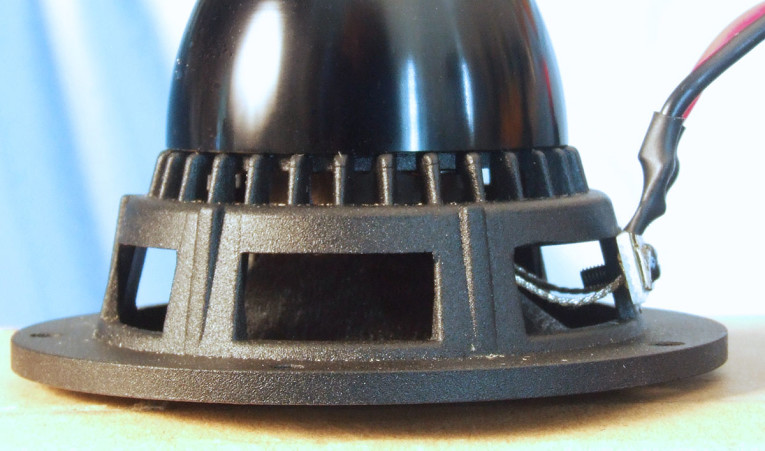
The cone assembly includes a black woven carbon fiber/paper sandwich curvilinear cone and 1.1” diameter convex black woven carbon fiber dust cap. Suspension is provided by a synthetic copolymer surround plus a flat 55mm diameter cloth spider with a linear roll configuration. This is connected at the neck joint to a 26mm (1”) diameter aluminum former wound with round copper wire. Voice coil tinsel leads terminate to a terminal fitted with color-coded 4” lead wires. The FEA and Klippel designed motor structure incorporates a neodymium slug with a metal return cup (a lot of the development of this driver was done by Warkwyn).
Since this midrange is to be crossed over at a minimum of 500Hz, I chose not to use the multi-voltage LEAP 5 LTD Thiele-Small parameter (TSP) testing protocol and instead established parameters with a single-standard low-voltage 20Hz to 40kHz sweep coupled directly to the LMS oscillator. The goal here was to establish an enclosure volume to ascertain the impedance resonance and Q. This information is useful if a passive high-pass network is employed, and of course, not relevant if using active filters.
Following my established protocol for Test Bench testing, I no longer use a single added mass measurement and instead use the company supplied Mmd data (3.89 grams for the M3). The single impedance sweep for each driver along with the Mmd data was used to produce the TSL parameters for the two M3 samples. Figure 1 shows the low-voltage free-air impedance curve. Table 1 compares the single sweep TSL data and factory parameters for both Stereo Integrity M3 samples.
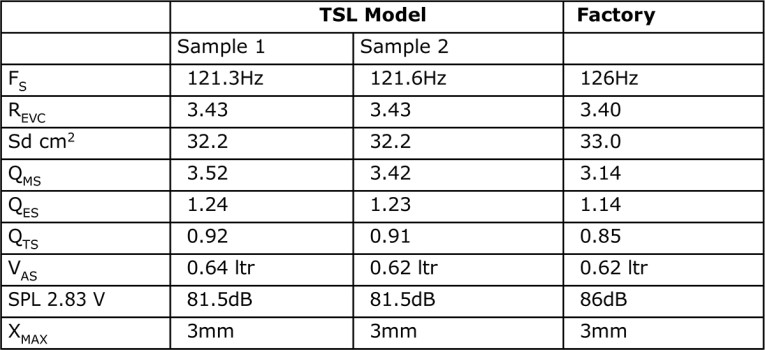
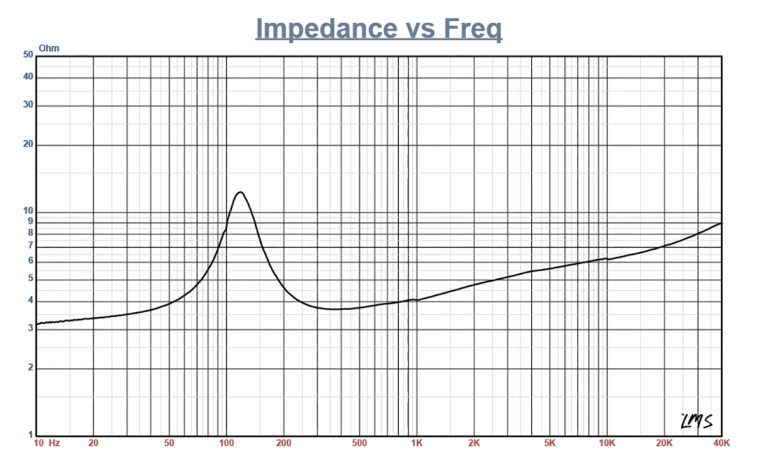
Figure 2 displays the frequency response results for the Stereo Integrity M3 midrange in the two simulated sealed enclosures at 2.83V. The smaller closed-box alignment produced a 3dB down frequency of 128Hz, Qtc=1.0 and the larger enclosure alignment was –3dB=119Hz and Qtc=0.99. Figure 3 depicts the impedance of both enclosures, while Figure 4 gives the group delay curves. As is apparent, there isn’t much difference in the box Qtc, so either volume would be appropriate, but the F0 and Q data could be used to design an LCR resonance conjugate filter to facilitate the 500Hz high-pass filter. For the purposes of this explication, Klippel analysis was not appropriate since this device is not being used in its piston range.
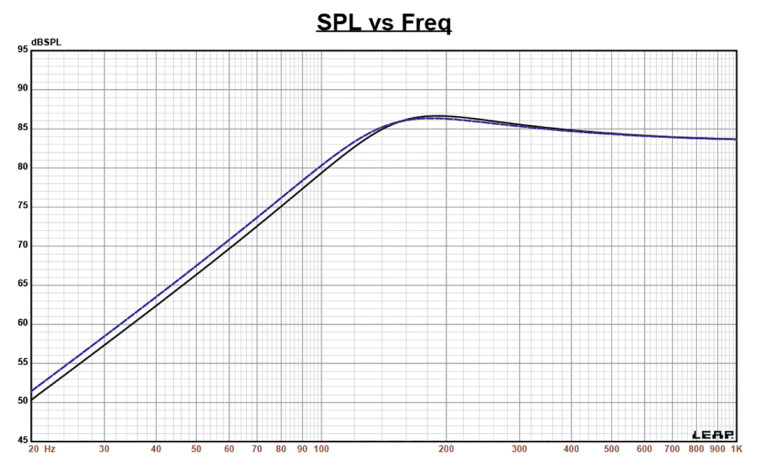
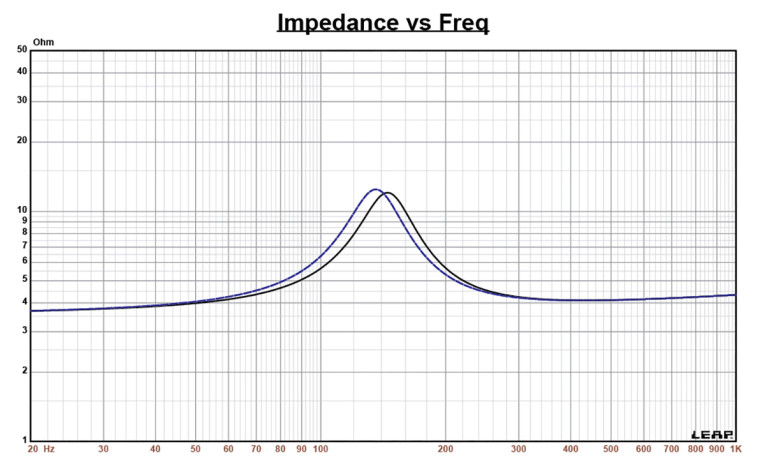
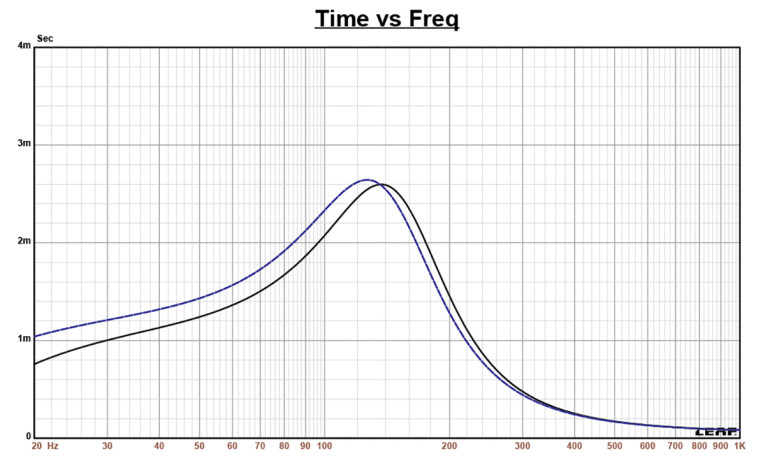
I next mounted the Stereo Integrity M3 midrange in a foam-filled enclosure that had a 12”×7” baffle and measured the device under test (DUT) using the Loudsoft FINE R+D analyzer and the GRAS 46BE microphone (courtesy of Loudsoft and GRAS Sound & Vibration) both on- and off-axis from 200Hz to 20kHz at 2.0V/0.5m, normalized to 2.83V/1m, using the cosine windowed FFT method. All of these SPL measurements also included a 1/6 octave smoothing (this is done to match the resolution of the 100-point to 200-point LMS gated sine wave curves that I’ve been using in the column for a number of years).
Figure 5 gives the Stereo Integrity M3 on-axis response, indicating a moderately smooth rising response that is ±3.5dB from 600Hz to 5kHz with a response that extends out to 20kHz. Figure 6 displays the on- and off-axis frequency response at 0°, 15°, 30°, and 45°. The -3dB at 30° with respect to the on-axis curve occurs at 4.5kHz, so a cross point in that vicinity should be work well to achieve a good power response.
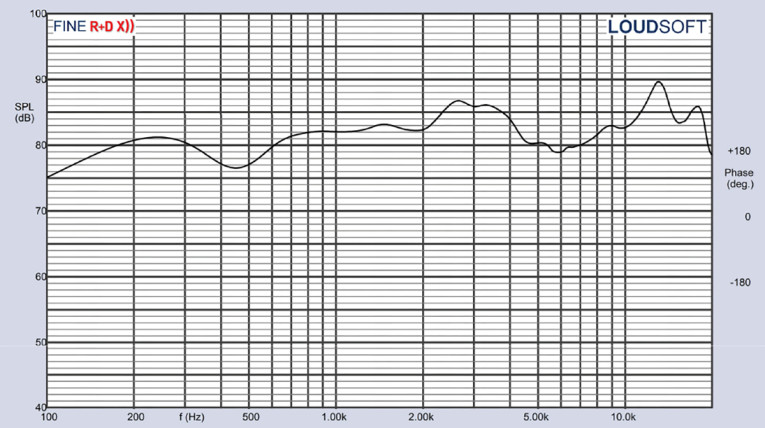
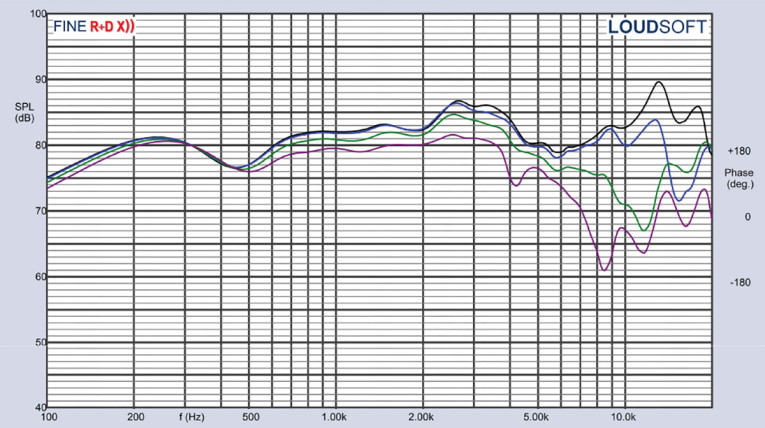
Figure 7 gives the normalized version of Figure 6, while Figure 8 displays the CLIO horizontal polar plot (in 10° increments with 1/3 octave smoothing). And finally, Figure 9 gives the two-sample SPL comparisons for the 3.5” Stereo Integrity driver, showing a close match between 0.5dB to 1.5dB up to 5kHz.
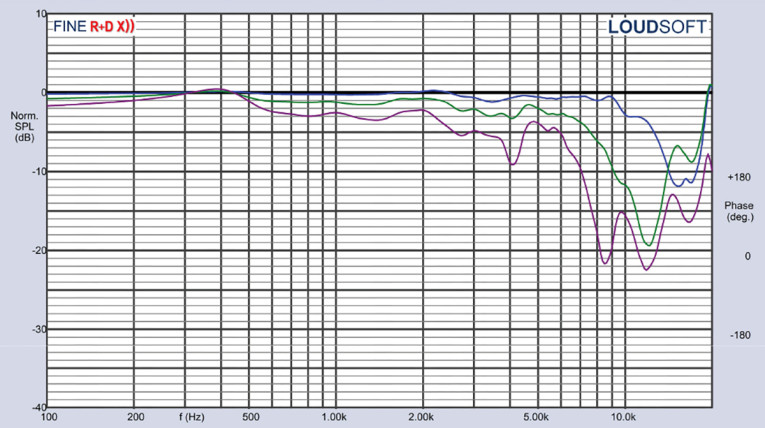
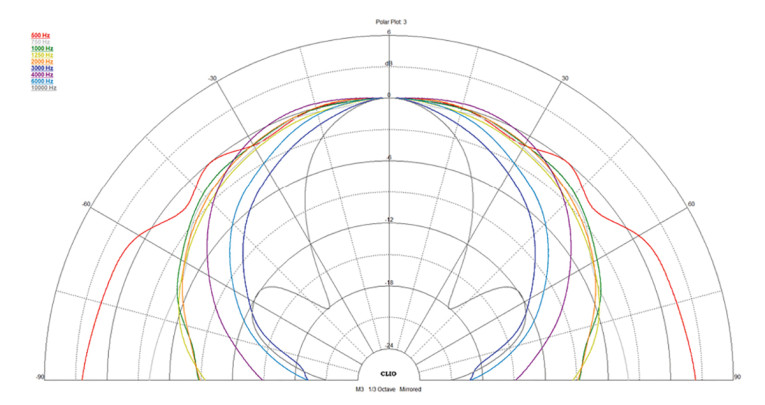

For the remaining series of tests on the Stereo Integrity M3 midrange transducer, I fired up the Listen SoundCheck AudioConnect analyzer and ¼” SCM microphone (graciously supplied to Voice Coil magazine by the folks at Listen, Inc.) to measure distortion and generate time-frequency plots.
For the distortion measurement, I rigidly mounted the 3.5” driver in free air and set the SPL to 94dB at 1m (11.8V) using a pink noise stimulus. Then, I measured the distortion with the Listen microphone placed 10cm from the driver. This produced the distortion curves shown in Figure 10.
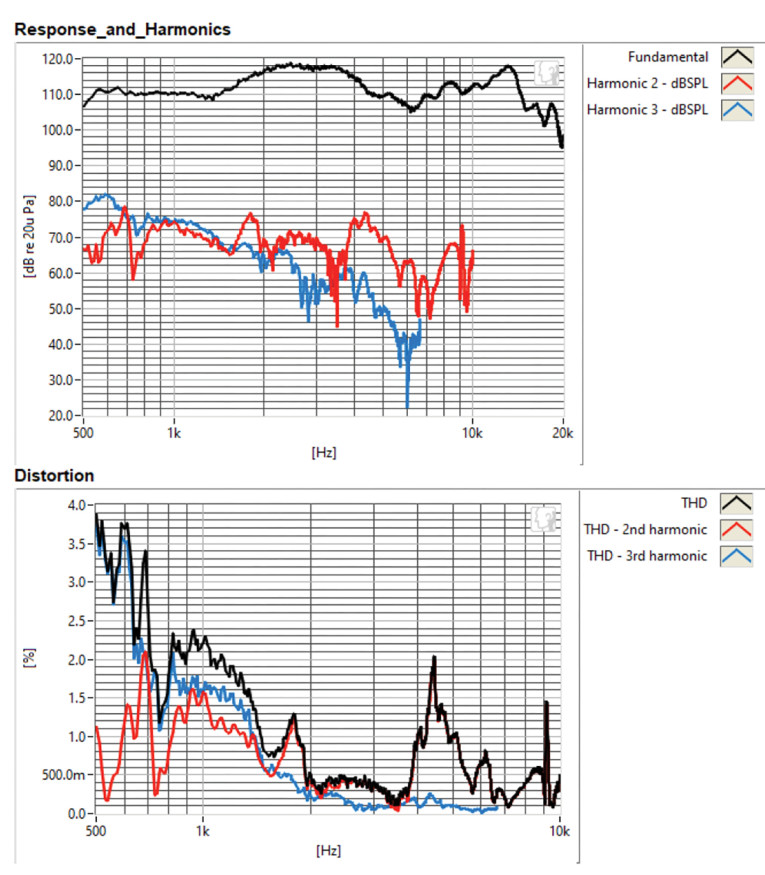
I then employed the SoundCheck software (V21) to get a 2.83V/1m impulse response for this driver and imported the data into Listen’s SoundMap Time/Frequency software. Figure 11 shows the resulting cumulative spectral decay (CSD) waterfall plot and Figure 12 shows the Wigner-Ville plot (chosen for its better low-frequency performance).
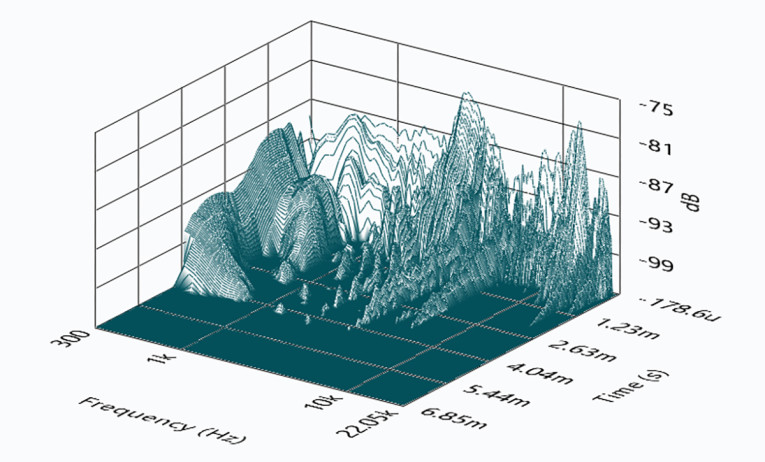
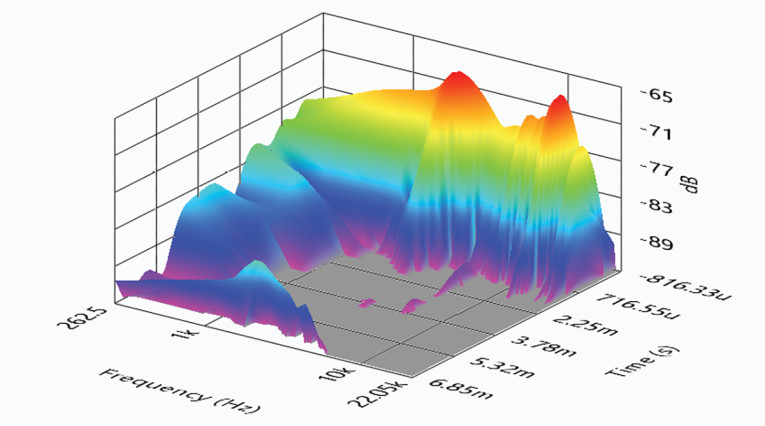
This article was originally published in Voice Coil, August 2024