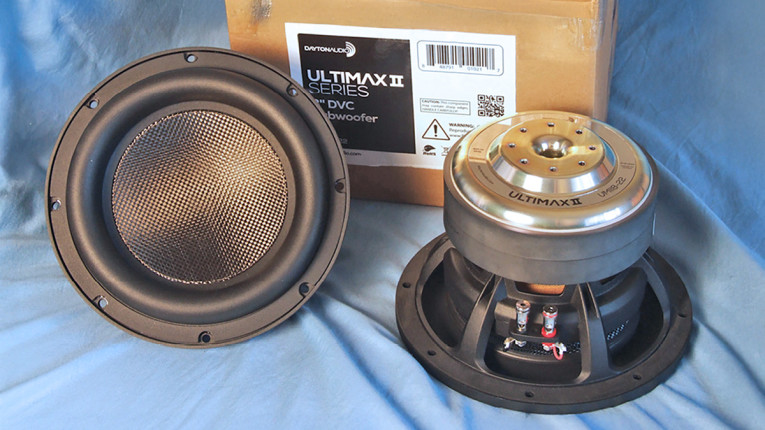
The common feature set (see the cutaway drawing in Figure 1) for the new line includes:
- Five models: 8”, 10”, 12”, 15”, and 18” diameter.
- Large aluminum shorting ring and aluminum pole sleeve for lower magnetic distortion.
- Lightweight and rigid woven carbon fiber cone assembly.
- High Xmax from 18mm to 28mm (18mm on the 8” up to 28mm on the 18”).
- The frame and motor are designed with extensive thermal venting.
- 2.5” to 3” diameter DVC 2Ω flat wound voice coils with power handling from 400W (8”) to 1200W (18”).
- Dual back-to-back spider configuration.
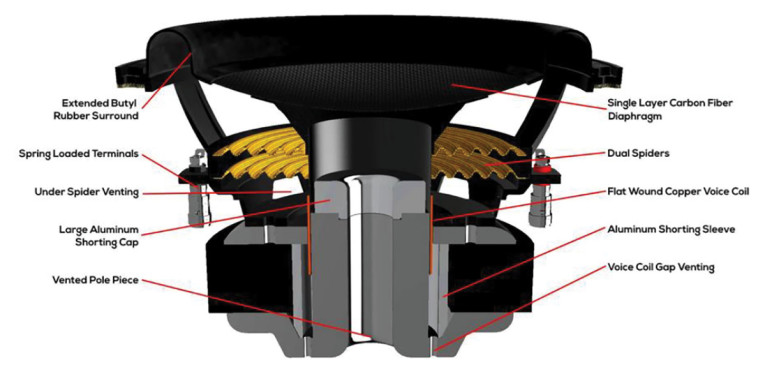
All Thiele-Small Parameters (TSPs) are optimized for compact sealed enclosures, but also capable of low-frequency extension vented designs.
The new Ultimax II 8” version (Photos 1-3, like the UMII10-22, has a similar generous feature set that includes a proprietary eight-spoke cast-aluminum frame that is substantial enough to support the heavy motor assembly and incorporates eight trapezoid vents that measure approximately 30mm × 7mm located below the spider mounting shelf. The mounting shelf itself utilizes a 15mm high standoff to mount the two opposing spiders.
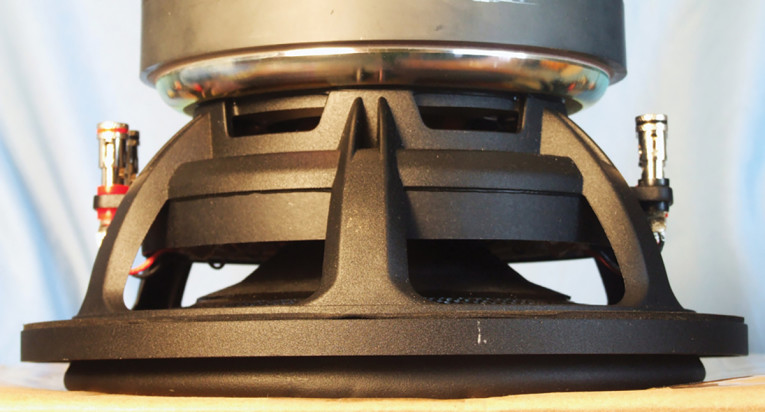
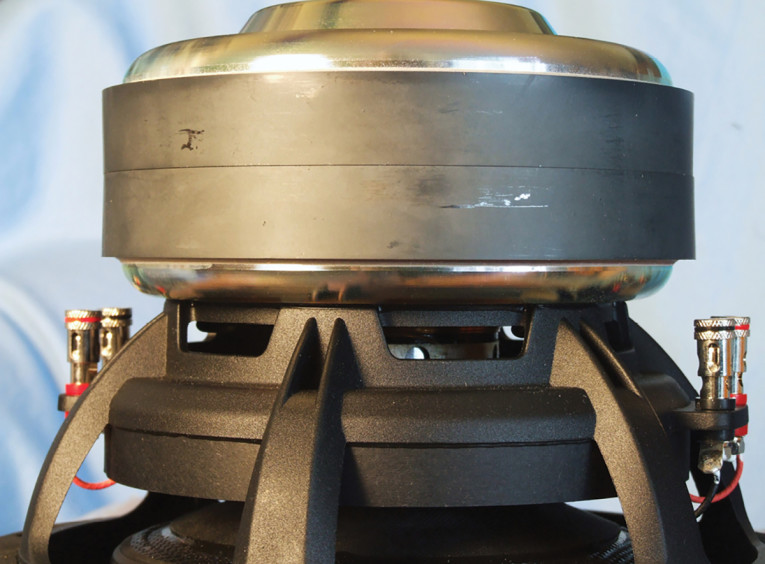
All this is driven by a 50.8mm (2.0”) diameter four-layer voice coil wound with flat copper wire on a vented aluminum former. The motor system powering the cone assembly utilizes two 20mm thick × 145mm diameter ferrite magnets sandwiched between a milled and polished 10mm thick front plate and a milled and polished shaped T-yoke that utilizes a flared 15mm diameter pole vent surrounded by eight 3.5mm diameter peripheral vents that exhaust from the gap area.
The UMII8-22 further incorporates a set of dual aluminum shorting rings (Faraday shields), one being an aluminum sleeve on the inner diameter (ID) of the motor magnets and the other as a cap on the pole piece that reduce distortion caused by eddy currents. Last, the braided voice coil lead wires are stitched into the top spider and terminate to a pair of chrome-plated color-coded push terminals located on opposite sides of the frame.
I began characterizing the new UMII8-22 8” subwoofer using the LinearX LMS analyzer and the Physical LAB IMP Box (the same type test fixture as a LinearX VI Box for measuring voltage and current separately). Sweeps were generated with the driver securely mounted in free air at 0.3V, 1V, 3V, 6V, 10V, 20V, 30V, and 40V. The measured Mmd provided by Dayton Audio was used rather than a single 1V added (delta) mass measurement. It should also be noted that this multi-voltage parameter test procedure includes heating the voice coil between sweeps for progressively longer periods to simulate operating temperatures at that voltage level (raising the temperature to the first and second time constants). The 40V curves were too nonlinear for LEAP 5 to achieve a reasonable curve fit and were discarded.
The remaining 14 sine wave sweeps for each woofer were further processed with the voltage curves divided by the current curves to produce impedance curves. Phase curves were generated using the LEAP phase calculation routine, after which the impedance magnitude and phase curves plus the associated voltage curves were then copy/pasted into the LEAP 5 Enclosure Shop software’s Guide Curve library. This data was then used to calculate parameters using the LEAP 5 LTD transducer model.
Because most all manufacturing data is being produced using either a standard transducer model or in many cases the LEAP 4 TSL model, I also generated LEAP 4 TSL model parameters using the 1V free air that can also be compared with the manufacturer’s data. Figure 2 shows the 1V free-air impedance plot for the UMII8-22. Table 1 compares the LEAP 5 LTD and LEAP 4 TSL TSP sets for the Dayton Audio UMII8-22 driver samples along with the Dayton Audio factory data.
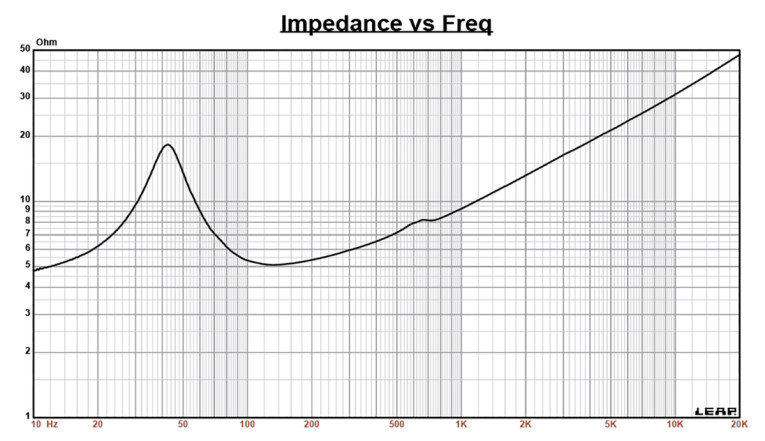
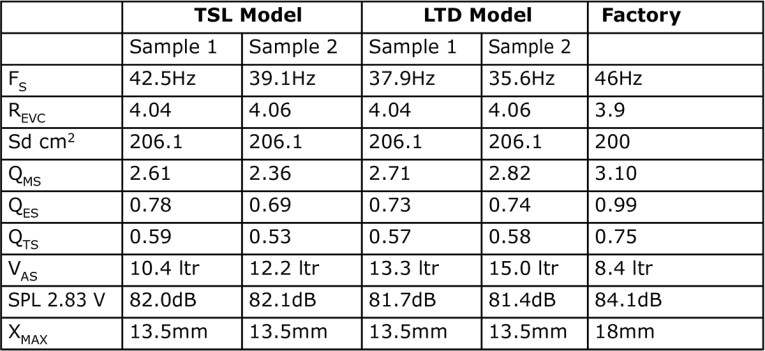
While the measured Qts was somewhat lower than the factory data, the Fs/Qt ratios were fairly close, which was confirmed by a box simulation that produced an SPL using the factory TSP nearly identical to that of the measured data. Other than that, the Xmax number for the Dayton factory data was higher than my standard calculated Xmax, because it was taken as the excursion at 70% Bl from Klippel analysis.
Following my normal protocol for Test Bench testing, I used the Sample 1 LEAP 5 LTD parameters and set up two computer box simulations, both being the recommended enclosure volumes published by Dayton Audio. The first was 0.5ft3 type sealed enclosure with an F3=51Hz. No Qtc was specified nor a percentage of damping material, but I followed my usual protocol with 50% fill material (fiberglass). The second example is a vented box in a 1ft3 box yielding an F3=23Hz. No tuning frequency was specified or a percent fill material, so I again follow my standard protocol with 15% fill material and tuned the enclosure to 30Hz.
Figure 3 gives the results for the 8” Dayton Audio UMII8-22 subwoofer in the sealed and vented enclosures at 2.83V and at a voltage level sufficiently high enough to increase cone excursion to Xmax+15% (15.5mm for UMII8-22). This resulted in an F3 of 50Hz (-6dB=40.5Hz) with a Qtc=0.72 for the 0.5ft3 closed box and a -3dB for the vented simulation of 33Hz (-6dB=2.5Hz). The vented simulation was 10Hz higher than that listed in the Dayton specs, however, I’m guessing that was a misprint, and should have been F3=33Hz.
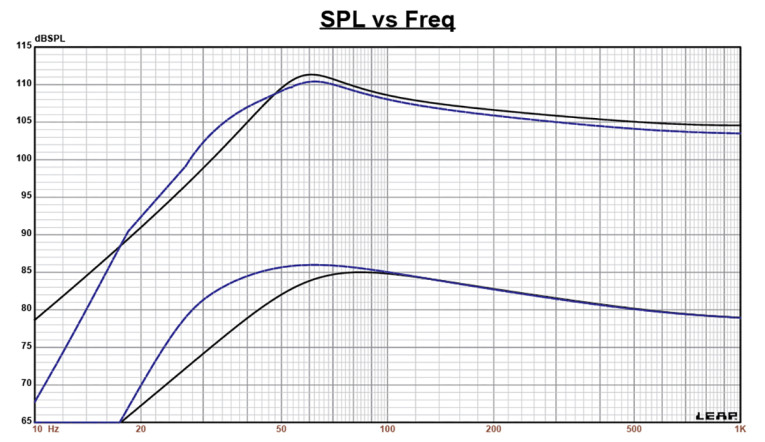
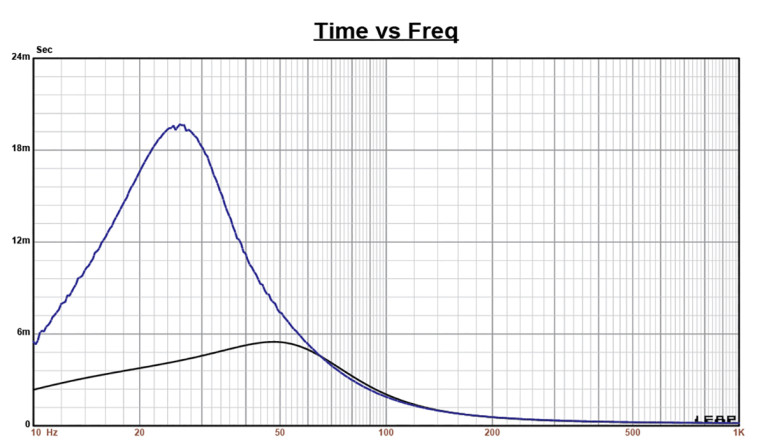
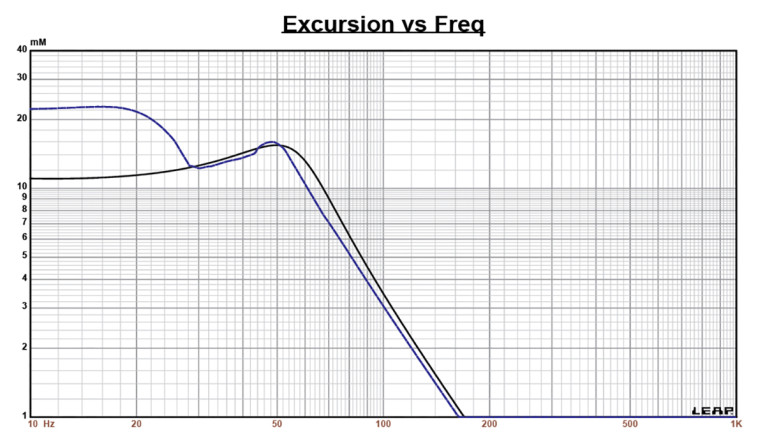
The Bl(X) curve for UMII8-22 (Figure 6) is very broad and mostly symmetrical (with an element of “tilt”) typical of a driver with a high Xmax number. Looking at the Bl symmetry curve (Figure 7) shows a relatively small 1.4mm Bl coil-out (forward) offset once you reach an area of reasonable certainty around 8mm, decreasing to 0.97mm at the physical 13.5mm Xmax position.
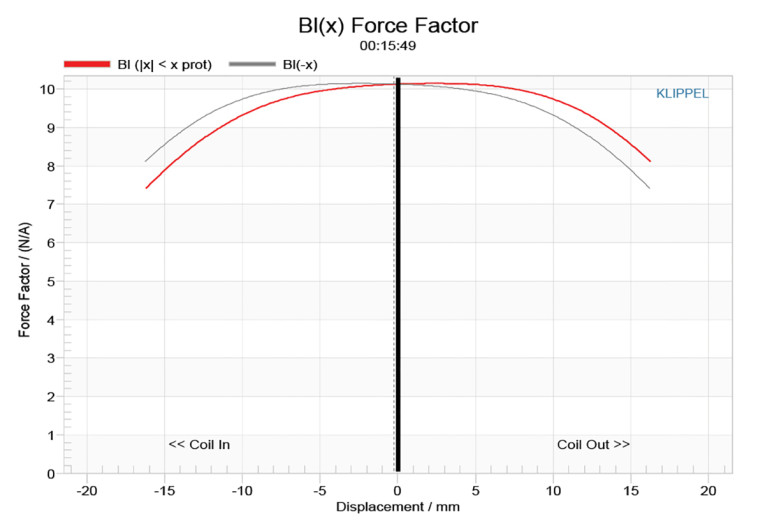
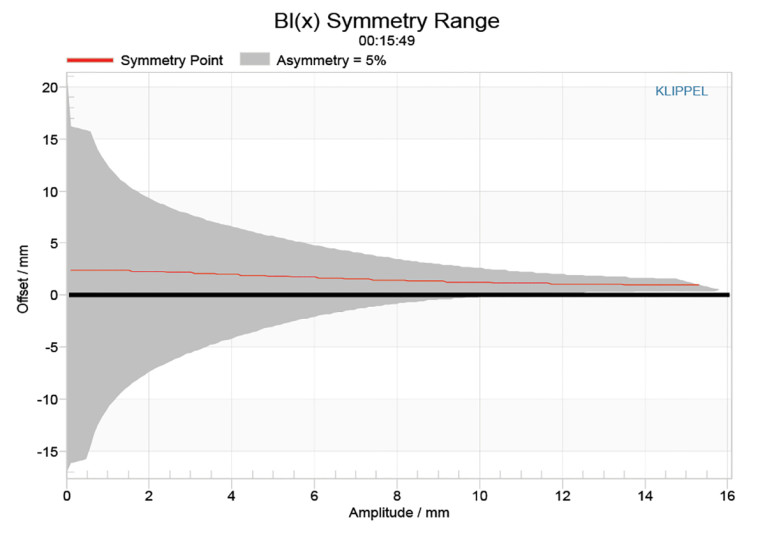
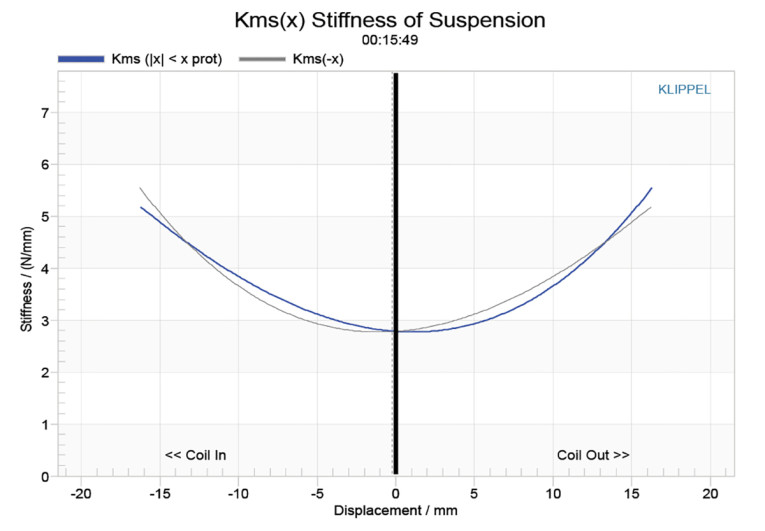
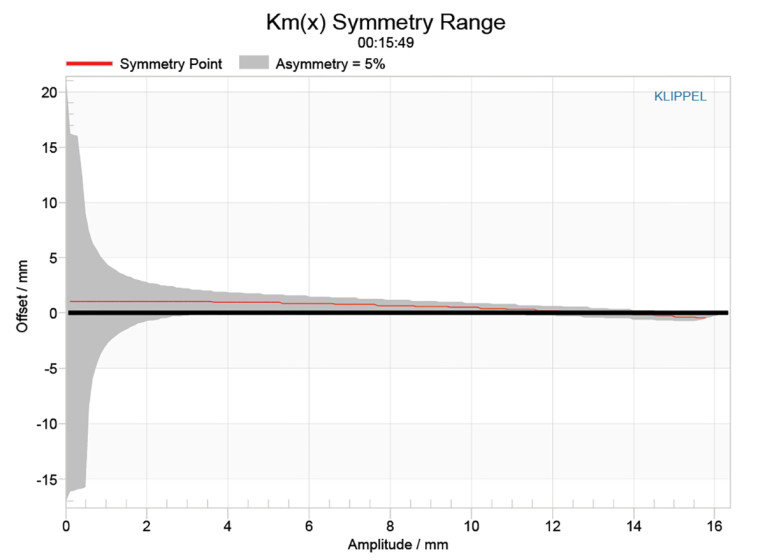
Figure 10 gives the inductance curve Le(X) for this Dayton transducer. Motor inductance will typically increase in the rear direction from the zero-rest position as the voice coil covers more of pole, however that doesn’t happen here, mostly due to the extensive dual shorting rings built into the motor structure. What we do get is lower inductance variation from full in to full out travel, which is the goal you want to achieve.
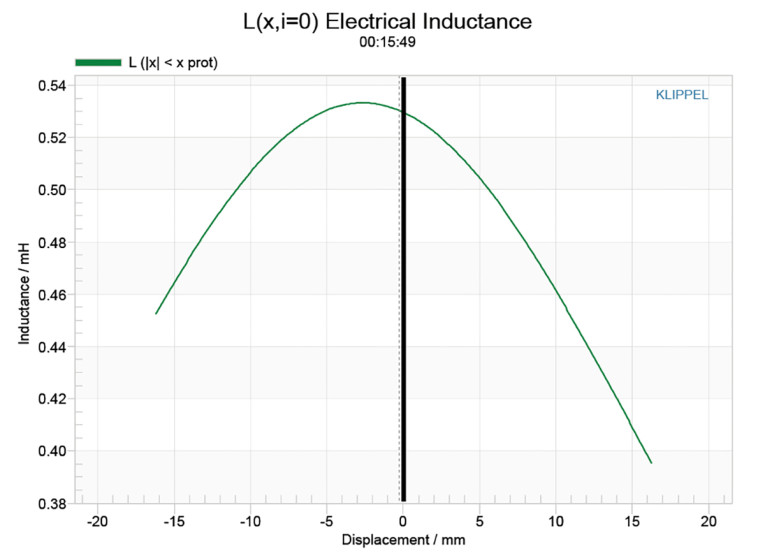
It’s easy to see the benefit of the dual aluminum shorting rings with inductance only varying about 0.05mH to 0.11mH from Xmax in to Xmax out, which is very minimal inductance change for such a large motor.
Given that the Dayton Audio UMII8-22 is a subwoofer mostly intended for application below 100Hz, I dispensed with the SPL measurements since this driver will not likely be crossed over much over 100Hz. That said, the factory-generated frequency response curve can be seen in Figure 11. I also dispensed with time domain analysis for subwoofers as the data is not really significant below 100Hz.
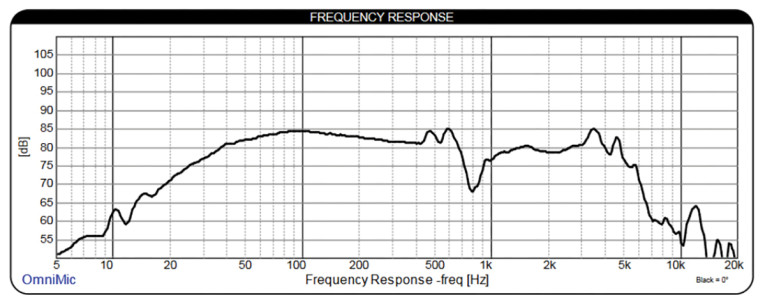
Next, I used the Listen SoundCheck analyzer to perform distortion analysis. For distortion measurements, I set the voltage level with the driver rigidly mounted in free air and increased the voltage until it produced a 1m SPL of 94dB (19V for the UMII8-22), my distortion SPL standard for home audio drivers.
The distortion measurement was then made with the microphone placed near-field about 10cm from the dust cap. This plot is shown in Figure 12. This actually includes two plots, the top graph being the standard fundamental SPL curve with the second and third harmonic curves, and the bottom graph the second and third harmonic curves plus the total harmonic distortion (THD) curve with an appropriate X-axis scale. Interpreting the subjective value of conventional distortion curves is almost impossible; however, looking at the relationship of the second to third harmonic distortion curves is of value.
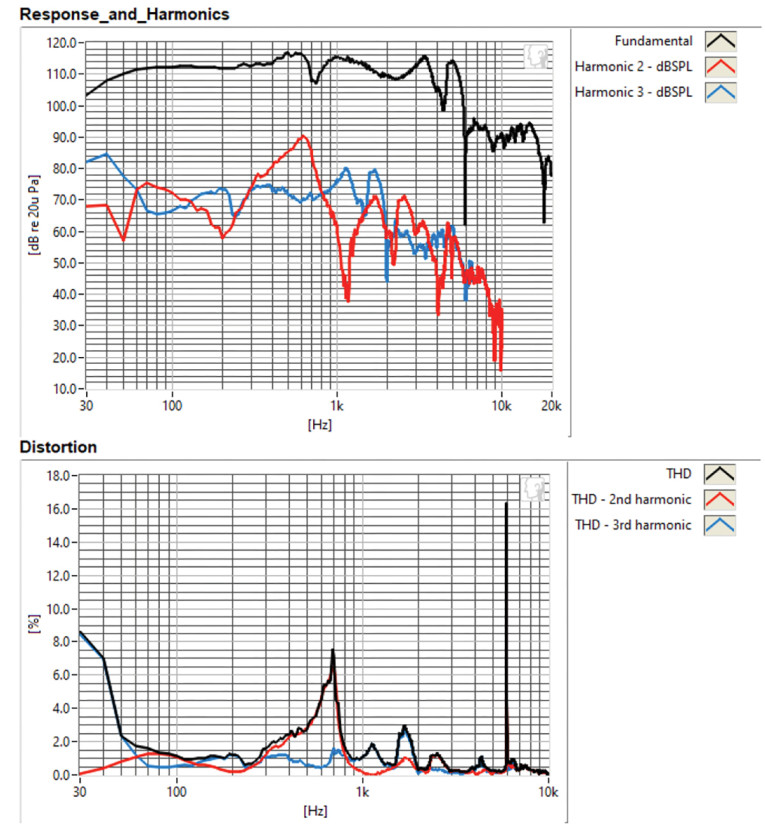
This article was originally published in Voice Coil, March 2025