This article explores high-polymer piezoelectric film, a virtually untapped material that could be used in various transducers (e.g., headphones, microphones, and tweeters). The high-polymer element is polyvinylidene fluoride film (PVDF) and its application possibilities seem less familiar to speaker hobbyists than any other type of drivers. In fact, it seems that the audio engineering community at large is either not familiar with PVDF film or misunderstands PVDF piezoelectric film technology. Hopefully, this article will serve as an introduction (or reintroduction) to PVDF technology.
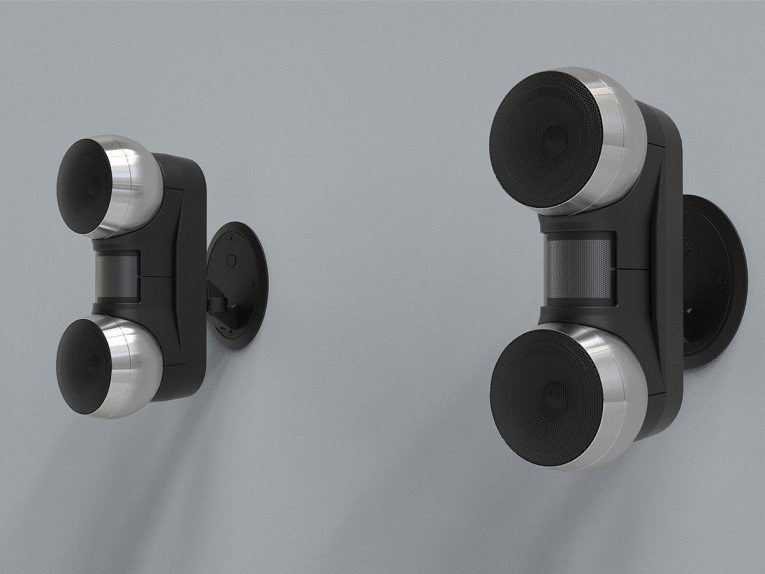
In 1985, Jesse Klapholz (a former Journal of the Audio Engineering Society editor) presented a paper, “High Polymer Piezoelectric Film in Electroacoustical Transducer Applications,” at the 79th Audio Engineering Society (AES) Convention. Klapholz’s introduction stated: “Since the discovery of piezoelectricity by the Curie brothers in 1880, there has been continued research and development because of piezoelectricity’s practical and economical applications as well as scientific importance. Piezoelectricity, simply defined, is ‘pressure electricity’ and is a property of certain materials that alter their shapes under the influence of an electrical field, or vice versa. Many different types of piezoelectric transducers have been manufactured over the years, for example: phonograph pickups, microphones, strain gauges, vibration pickups, underwater sound sensors, and tweeters.”
More than 28 years have passed since Klapholz’s talk, and while there have been a half-dozen relatively technically successful efforts involving high polymer film transducers for audio (e.g., speakers, microphones, headphones, and even air-motion transformer high polymer tweeters) only the first launch — Pioneer Electronics’s HPM speakers in the mid-1970s — made much of a commercial impact.
There are several reasons to revisit PVDF film today. Its lighter weight is better for autosound applications. It can be used as an alternative piezoelectric solution, eliminating the lead issues found in most ceramic piezoelectric speakers. The electronics for the high-voltage drive is possible now with projected sound from ultrasonic beam speakers and the potential for direct digital-sound reproduction.
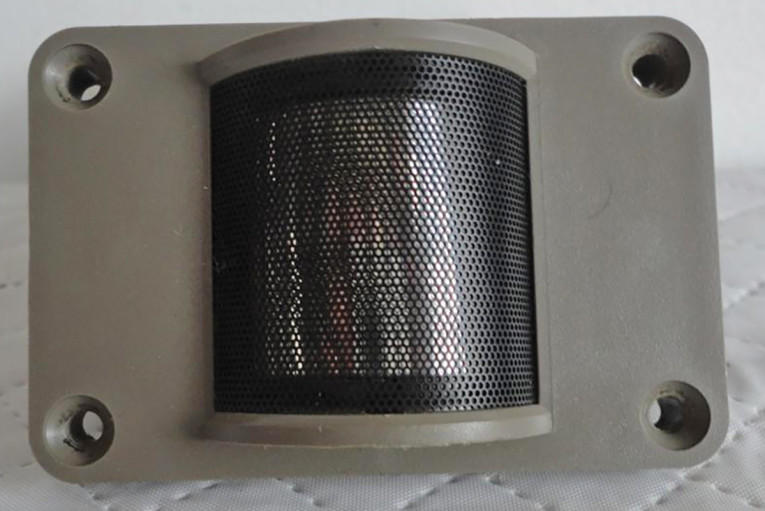
Past PVDF Speakers
More than a half-dozen PVDF speakers have been commercialized. But, for the most part, these speakers have not made it to the mainstream users, so people might be unfamiliar with all these valiant PVDF designs.
PVDF technology was introduced to the audio world when Pioneer Electronics announced a series of viable products in the mid-1970s. Masahiko Tamura and his co-workers at Pioneer’s Acoustical Engineering Research Laboratory in Saitama, Japan produced high-quality PVDF film microphones, phono cartridges, stereo headphones, and tweeters. Their work was a turning point for PVDF piezoelectric film because it showed its commercial viability in audio applications. The Pioneer HPM-100 was a four-way system designed bycBart Locanthi and his team of former-JBL engineers, all of it that is, except the super tweeter, which came from Pioneer’s Japanese research group (see Photo 1).
HPM stands for “high-polymer molecular,” in reference to Pioneer’s then newly developed high-polymer molecular film “PVDF” super tweeter. The film was shaped semi-cylindrically to project 180° sound. This driver’s frequency response ranged from 12 to 25 kHz. Locanthi continued to support Pioneer’s high-polymer film speaker development, but he also lead its development of the Technical Audio Device (TAD) pro group studio monitors, beryllium-diaphragm compression drivers, and concert-sound speaker systems. Pioneer’s Japanese team continued to develop the HPM series.
After the initial introduction of the semicircular high-polymer super tweeter, most new implementations were cylindrical and omnidirectional, with at least a horizontal approximation of a pulsating sphere. The HPM-200 was another four-way design, but it boasted high-polymer drivers operating at 2,000 Hz and higher.
The HPM-150 used a new version of the PVDF tweeter, which was then horn loaded, but it retained its omnidirectional characteristics (see Photo 2). By 1981, Pioneer had discontinued the HPM series, perhaps due to the high cost of the sophisticated designs and issues with the metallization corroding (attributed to the high levels of air pollution in many US cities 30 years ago). Another issue was extending the response below 2,000 kHz did not lend itself to practical implementations. PVDF film response at the bottom-end tends to require a larger radius, and getting down to the lower midrange proved difficult. Today, the idea of a 2.1 or 5.1 system that uses all PVDF drivers with a common subwoofer is a distant dream. Matsushita (now Panasonic), Mitsubishi Electric, Sony, Samsung, and others also had active PVDF film speaker projects through the 1980s. While some of these efforts yielded technical papers and patents, the programs never resulted in commercialized products from these brands.
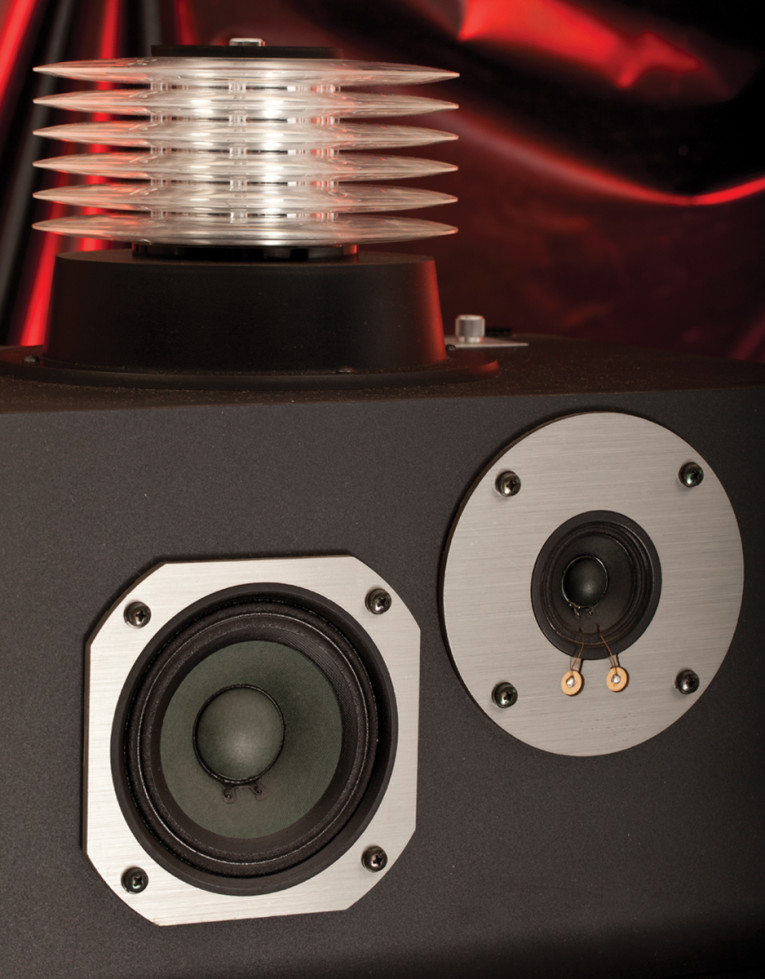
Then, Audax introduced its half-egg-shaped dome tweeter in its Audax HD3P piezoelectric polymer tweeter. Until this point, most PVDF transducer designs used planar or curved films. However, F. Micheron and C. Lemonon’s, “Moulded Piezo Electric Transducers Using Polar Polymers,” (Journal of the Acoustical Society of America, 1978) introduced a vacuum-molding technique to fabricate 3-D-shaped transducers (e.g., cones, portions of spheres, corrugations, and so forth). They found that these transducers could be designed to meet certain acoustical parameters, which could not have been obtained with planar or curved films. Perhaps inspired by their work, Audax launched the HD-3P elliptical dome tweeter around the late 1990s. It was a both a technical and commercial experiment in PVDF production.
Audax priced the tweeter high to keep sales low, just in case the product did not survive in the field. Why the HP-3P was not developed into a family of products was perhaps due to some combination of external business issues at Audax, technical production, and service-life challenges. The PVDF film coating was a vacuum deposit of pure gold, and the diaphragm was clamped to an elliptical ring with a sealed and pressurized chamber behind it. The elliptical dome was formed by the constant, positive force from the pressurized nitrogen gas on the film.
As with other PVDF speakers, an electrical signal is fed to the metal electrodes deposited on both sides of the ceramic film, the diaphragm’s surface area responds by elongating and contracting proportionally in size with the signal. Sound waves are generated by the diaphragm’s stretching, which converts the vibration into a pulsating motion rather than a piston motion. The transient ability is outstanding because the HD-3P’s moving mass is approximately 20 times less than a conventional 20-mm dome tweeter, while the directivity is equivalent. The waterfall plots (i.e., 3-D response graphs showing frequency, amplitude, and time) were impressive. The HD-3P was supplied with its own crossover network, which could be adjusted between 4 to 6 kHz. System sensitivity was in the 86-to-94-dB range.
Early units suffered from Audax’s worst fear, a less than perfect gas seal, which caused the nitrogen to gradually leak away. Its first visible sign is that in high-pressure weather, wrinkles or creases appear in the gold dome with a resulting loss of top-end response.
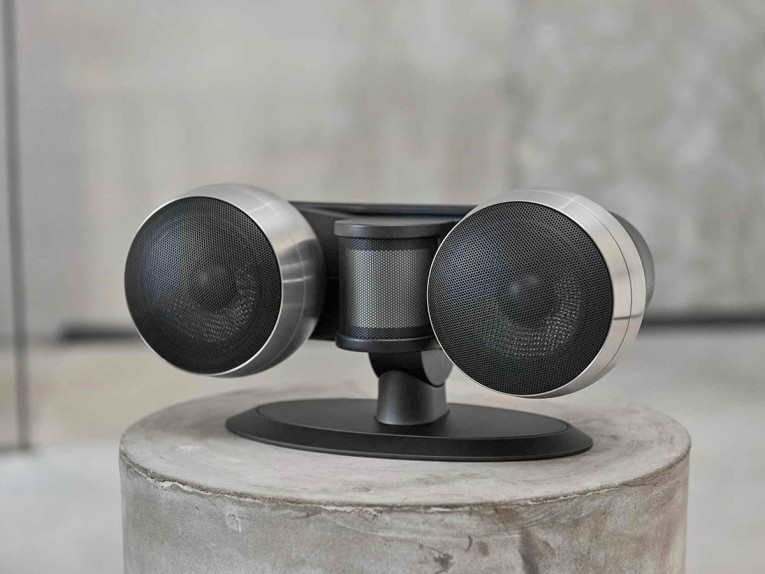
Gallo CDT
More recently, Anthony Gallo Acoustics Europe and FILS have been refining the technology. Anthony Gallo refers to his speaker as “a tweeter without compromise.” Photo 3 shows his proprietary design, which is called the Cylindrical Diaphragm Transducer (CDT). Gallo spent years refining this design, and the company’s marketing literature emphasizes the CDT’s unique construction. “The CDT uses no voice coil or magnets. Instead, the signal is passed across the conductive surface of the diaphragm, which attempts to expand while the driver’s cylindrical shape supplies the necessary restorative force.” The specifications show the CDT has a 3-to-25-kHz range. The diaphragm is made from Kynar and coated in silver. The construction resembles the lines of the Pioneer’s early HPM tweeters.
FILS Sound
The most recent PVDF film speaker is from Korean electronics manufacturer FILS Sound. Refinements include surface treatment for enhanced adhesion of metalized coating and lead-out wires (see Photo 4). FILS Sound uses poly(3,4 ethylenedioxythiophene), otherwise known as PEDOT (a specialized polymer film) with pure carbon nanotubes (CNTs) electrochemically deposited on the electrodes. The PEDOT/CNT-coated microelectrodes have lower impedance than the bare platinum (Pt) microelectrodes, and the PEDOT/CNT film offers excellent stability. The finished film is flexible and this property enables it to be used in unique form factors.
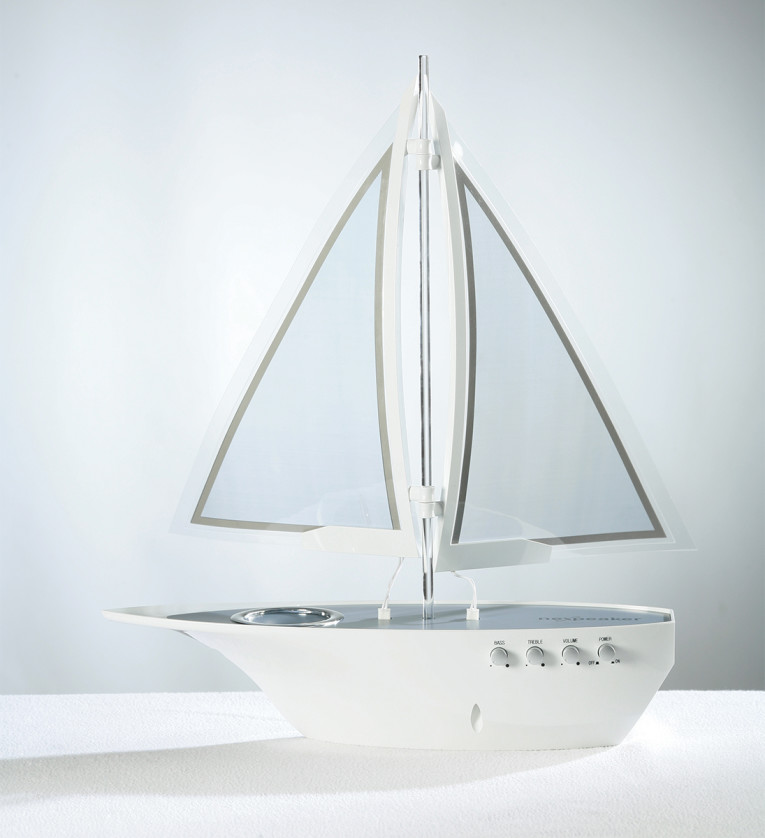
PVDF
Next, we will examine polymer film itself, otherwise known as PVDF or Kynar piezoelectric film. A polymer made of 1,1-difluorethene, polyvinyleden difluoride (PVDF) is known as piezoelectric, meaning it will produce an electrical current when bent or pressed. The material can be shaped into a long ribbon, bent into almost any shape, or formed into a dome. It can then act as a microphone or a speaker. PVDF films are made from a semi-crystalline, high-molecular resin (e.g., Arkema’s Kynar), which is extruded into sheet form. When PVDF is initially extruded for piezoelectric applications, the film must be stretched so the orientation of the polymer chains in the film’s plane can achieve enhanced piezoelectric activity.
The film stretching is performed uniaxial (usually in the direction of machine travel) or in both machine and transverse directions (biaxial). The film is coated on both sides with a conductive electrode metal, usually by vacuum deposition, to provide intimate electrical contact with the PVDF film during poling and use. The film is then polarized by an intense electric field at an elevated temperature followed by a cooling within the applied field.
Kynar’s Corporate Trail
One aspect of PVDF piezoelectric film’s spotty commercialization may be that its corporate ownership has traveled a tortuous path. DuPont invented and patented polyvinyl fluoride film in 1948. Pennwalt Chemicals acquired the rights and developed the licensing program that enabled its first widespread commercial use as a pigmented liquid coating and for more obscure PVDF-film applications like speakers. This coating had been sold under the Kynar 500 trade name since the mid 1960s. In the 1980s, the French chemical conglomerate Elf Atochem (now named Arkema) acquired Pennwalt.
Today, Kynar 500 is a registered trademark of Arkema, which continues to offer Kynar resins, foams, and film. However, in the early 1990s, AMP acquired the Piezo Film Sensors Division from what was then Elf Atochem and renamed the division AMP Sensors. In 1998, Measurement Specialties, Inc. (MSI) acquired the Sensors division from AMP. In 2002, MSI relocated the piezo film manufacturing to its head office in Hampton, VA. While still offering piezoelectric film, MSI’s focus is on sensors rather than on PVDF film’s application to commodity transducers for speakers.
Design Challenges
A plastic piezoelectric film driver would seem to be mechanically simple: A sheet of PVDF with electrodes attached, held loosely in a frame against a soft polyurethane foam former/damper. For use in loudspeakers, PVDF’s main draw is its ability to flex when an audio voltage capable of driving a speaker is applied, converting electricity directly into sound with good linearity. There are many design rules at play here that are different from those applied to conventional loudspeaker drivers.
There are a number of hidden design challenges with PVDF speakers and a few of them are similar to the challenges found in ribbon planar and electrostatic designs. A larger horizontal radius extends the low-frequency cutoff. Design issues include lead-out wire termination, metallization, and forming the film into the target shape. Speaker system integration is another consideration since PVDF speakers are not “drop-in” replacements for electrodynamic speakers. It takes a couple hundred volts drive signal to makes PVDF speakers sing.
Lead-out wire issues are similar — but different — as with tensioned diaphragm planars (e.g., ribbons and electrostatics). With other film speakers, you can attach the lead-out wires outside the clamped area and the substrate is stable. With PVDF film, the film substrate itself — even at the attach point — is moving with the signal. Soldering lead wires to the film is difficult as the surface “moves” on the microscopic level. However, soldering with very high silver content and rubberized conductive techniques has been successfully used in mass production.
The attachment technique must accommodate extended flex life or cracking over time will result. Today, there are robust solutions, but this was not always the case in early PVDF speaker products. Metallization creates the electrodes and is an inherent requirement for the film’s self-polarization. Pioneer’s early efforts used nickel, which had a way of “evaporating” over the years. Audax addressed the metallization’s corrosion by using a gold-sputtering process. However, Audax also needed a superior seal to prevent the nitrogen gas (used to inflate the elliptical dome to the desired form) from leaking. Wrinkles and worse were common over time with Audax’s PVDF tweeters, but the failure modes were often leaky seals rather than loss of positive gas through the film membrane itself. Gallo uses silver metallization in its PVDF tweeter. And, more recent developments in PVDF metallization techniques suggest that platinum in combination with plasma-treated PVDF film will produce excellent results.
Shape is also an issue. PVDF film is not a high-force drive like PZT ceramics, yet the flexible film’s shape must be maintained. Specifically, the film expands and contracts across the “machine direction.” Some films were biaxial stretched and moved both sideways and up/down, but most PVDF loudspeakers used uniaxial film. We have mentioned that if held in a curved shape, the larger the radius, the more extended the lower end response. Pioneer managed to extend the response down to 2,000 Hz in its HPM 200. Excursion is limited, so a large radiating area and/or horn loading is needed to increase the maximum acoustic output and extend the midrange response’s bottom end.
PVDF diaphragms are not particularly stiff or high force, which limits midrange even when horn loaded. Design rules are not readily or clearly defined by the PVDF film manufacturers or in the technical literature, but attempts to hold the film in shape must not suppress diaphragm movement. Pioneer and others have used foam behind the film. Audax used nitrogen gas with some positive pressure. Dr. Oskar Heil’s airmotion self-supporting configurations may have promise for future work, as other diaphragm support solutions suppress output (although foam support backing of the film can provide some strategic damping of undesired resonances).
In 1988, Dr. Ivar Veit, of Sennheiser Electronic presented a paper, “The Piezoelectric PVDF Film — Its Properties and Application in Electroacoustic Transducers,” at the 84th AES Convention in Paris, France. The paper explored PVDF microphone applications, and it also suggested a PVDF speaker topology for an elongated cone (sort of a Walsh driver, better known as the Ohm Speaker), and another self-supporting approach, air-motion pleated film. aX
This article was originally published in audioXpress April 2013.
Read Part 2 Here