The first part of this article explored polyvinylidene fluoride (PVDF) piezoelectric film loudspeakers. Now, our exploration of this technology focuses on its many other successful applications — from headphones, microphones, guitar pickups, and accelerometers to its ancient use in phono cartridges. Finally, we will examine recent developments in fourth-dimension (4-D) audio — PVDF electro-active polymer (EAP) products for haptic vibration in headphones, which creates an extreme bass sensation. Aside from these applications, we will discuss why PVDF film transducers are relevant for audio design including their lighter weight without neomagnetic structures, the piezoelectric effect without the use of lead (which is now used now in piezo ceramics), and the availability of semiconductors for driving the high voltage needed for high-polymer films.
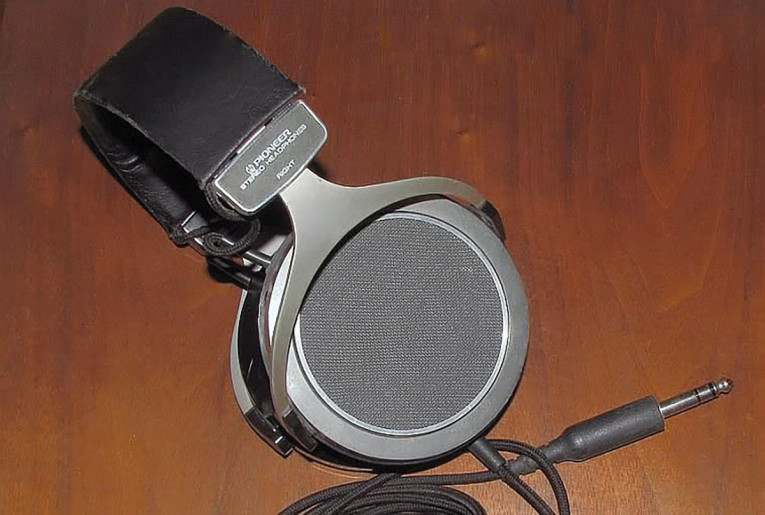
In Part 1 of this article series, we touched on PVDF’s slow acceptance into mainstream audio, but let’s take a closer look. What we have is transducer technology with unique capabilities and design advantages. Lightweight and flexible, piezoelectric film transducers can serve as highly reliable low-cost alternatives to more expensive speakers, headphones, mics, and musical instrument sound pickups.
Headphones
The flat frequency response over a wide range is a consequence of the PVDF polymer film’s softness, which eliminates the self-ringing found in brittle materials such as piezoelectric ceramics. In the late 1970s, Pioneer introduced a well-reviewed series of PVDF film headphones — the SE-300, the SE-500, and the SE-700 (see Photo 1). These products were advertised as being “the world’s first high molecular polymer stereo headphones.”
PVDF film headphones have three practical downsides. First, they are barely efficient enough to play from the average receiver headphone jack let alone a smartphone’s headphone output. Second, a piezoelectric device is electrically a capacitor, and some amplifiers have difficulty with reactive lossy loads.
This aspect is a real deal breaker for mainstream acceptance today. High voltages are required and PVDF film transducers aren’t very efficient. However, the classic step-up transformers aren’t pocket portable. On the other hand, a purpose-built high-voltage swing amplifier that can drive lossy capacitive loads is readily achievable, but it requires integration into the headphone. Since PVDF requires high voltage and not high power, the power amplifier necessary to drive PVDF film loudspeakers could be designed with much lower power/current requirements yielding a more efficient, compact, and economic system.
Today, DC-DC and boost converters, voltage doublers, and the like are inexpensive, readily available high-efficiency power integrated circuit (IC) devices. Third, PVDF stretches and it’s difficult to obtain enough excursion from the semi-tensioned PVDF film diaphragm for it to reproduce bass at high output. In the 1980s, Sony also had a development project for PVDF film. Toshitaka Takei, the team’s lead developer, designed a loudspeaker using piezoelectric film. Because of the difficulties driving them with existing amplifiers, development at Sony was halted. While Sony never commercialized the product, Takei eventually left Sony and founded TakeT around 2003, a low-production and expensive headphone manufacturer that uses PVDF film (see Photo 2).
Totally unique, TakeT’s approach was to form the PVDF film into a variation of Dr. Oskar Heil’s air-motion-transformer invention. This is a brilliant idea as it provides both stiffness through topology and more excursion and compliance though the corrugations (much like a spider/damper gets its excursion from the corrugations rather than stretching the fabric itself). Besides its headphone line, TakeT also manufactures a PVDF film super tweeter.
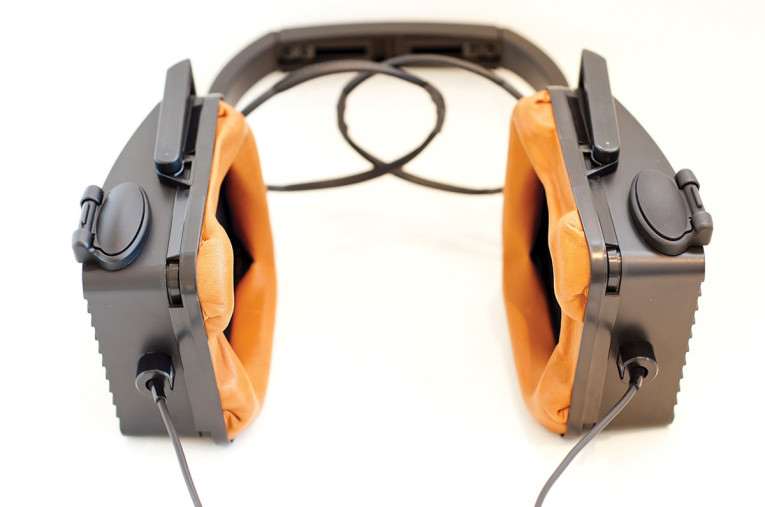
Digital Loudspeaker and Headphones
Digital loudspeakers and headphones that can provide direct conversion of sound from digital sources have been theorized for decades. PVDF has the bandwidth and may lend itself to this, but let’s save this for another article.
Another “science project application” for PVDF film is focused ultrasonic beam parametric array speakers that can place audio in a specific location over long distances. This category has a few players, but Woody Norris’s ATCO (now LRAD, which stands for long-range acoustic device) probably made the most hype.
Currently, this technology was spun off to Parametric Sound. This unique field includes HyperSonic Sound (HSS) from TK Geomedia (now owned by Turtle Beach Corporation) (see Photo 3) and Audio Spotlight from Holosonics (see Photo 4). A few others have dabbled in this esoteric field including Sennheiser’s AudioBeam and Mitsubishi Engineering. Others have patented variants but not commercialized their inventions. Implementations have included arrays of piezoelectric mics (used as ultrasonic radiators), electrostatics, and PVDF film.
PVDF Microphones
Back in the 1970s, the Allen Clark Research Centre in England reported on the design of a pressure-operated PVDF microphone. Later, the Plessey Company reported on a noise-canceling first-order pressure-gradient-operated microphone using PVDF elements in a bimorph edgeclamped configuration. As with electrets, the mass was small and exhibited high immunity to vibration pickup. The advantage of the PVDF design was its immunity to stray magnetic fields, eliminating more costly assemblies.
Extensive research in PVDF transducer technology was also conducted by the Matsushita organization in Japan. At the Audio Engineering Society (AES) Convention in 1977, Naono, Rikow, et al, presented the most comprehensive report to date concerning PVDF microphone applications.
They detailed curvature mode of operation PVDF elements with design equations and experimental models. PVDF mics were theoretically and experimentally analyzed with cylindrical and spherical diaphragms at the Technical University of Darmstadt in Germany. Researchers demonstrated that geometries were possible with PVDF that offered good mechanical and thermal stability. The PVDF also made it possible to vary the diaphragm tension and damping with a back plate/support mechanism.
In the communications sector, Telephonics became interested in the possibilities afforded by PVDF and marketed a variety of low-profile, noise-canceling, boom microphones for telecommunications headsets. Generally, the microphone element in these types of systems is located in the earpiece assembly (making noise-canceling impossible); however, the PVDF element can be made small enough to fit at the end of the boom and provide noise cancelation characteristics.
Countryman Associates introduced a lavalier microphone, the Isomax TVH. Countryman claimed the microphone was the first to use “active vibration isolation,” which the company claims to yield 30 to 40 dB less handling noise than other lavalier microphones. The “active” element is a PVDF diaphragm used for noise-canceling. The use of PVDF as a sensor (e.g., the Countryman mic) is just one of many vibration and sound sensor applications utilizing PVDF film.
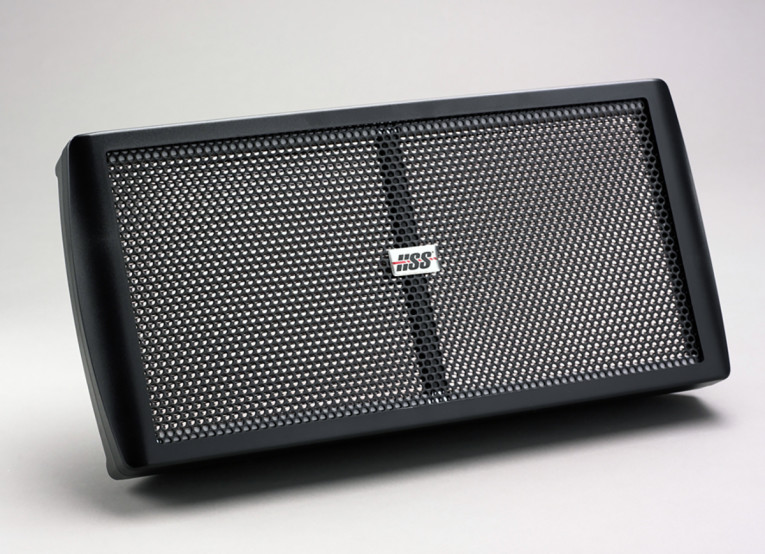
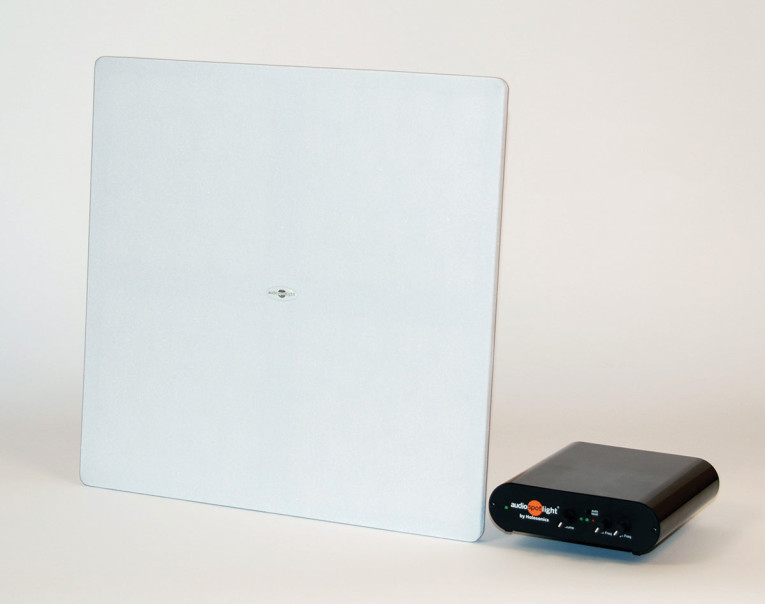
Sound and Vibration Pickup With PDVF
Piezoelectric film technology’s unique physical properties, size, and performance characteristics make it especially useful for implementation into existing applications as an alternative to a standard-sized piezoelectric accelerometer, where space constraints, cost, or design flexibility may be of concern. It can also produce voltage in proportion to compressive or tensile mechanical stress or strain, making it an ideal dynamic strain gauge.
For example, in subwoofer applications a small piece of PVDF film attached to a loudspeaker cone or voice coil collar can serve as a transducer in a feedback/correction circuit. In another application, musical instrument contact transducers can be easily made from PVDF film. Raad, a Canadian musical instrument manufacturer, produced a line of instruments including violins, violas, cellos, and double basses with integral PVDF elements as contact pick-ups. Gibson, the legendary guitar manufacturer, produced a line of acoustic guitars with a PVDF film permanently mounted in the guitar, which functioned nicely as a contact pick-up. Because this type of pick-up design uses PVDF film’s bending mode, it is less susceptible to feedback than piezoceramic accelerometer type pick-ups.
Piezoelectric film technology has been successfully used as a low-cost shock and vibration sensor within computer hard disk and CD-ROM drives, where space is at a premium and mass loading is a concern. Within these applications, mechanical shocks (e.g., those caused by a laptop dropped on the floor) can send a computer disk drive’s read/write function off track, possibly overwriting good, adjacent track data, causing memory loss, or destruction of files. Piezoelectric film shock sensors offer a compact, lightweight solution within such sensitive electronic device applications.
Security Applications of PVDF Film Pickups
Imagine a cable is strung or woven along a chain-link fence. The cable can be used to detect unusual acoustic noise signatures occurring on the fence and acts as a microphone from which security personnel can effectively “listen” for perimeter activity. For example, any attempt to cut or climb the fence is immediately detected. Another approach is to bury a piezoelectric cable a few centimeters underground along a security perimeter. When buried, the cable becomes an excellent microphone for detecting footsteps or vehicle activity.
PVDF’s moisture resistance also lends itself to towed-phased arrays for sensing and signal feedback for certain naval applications.
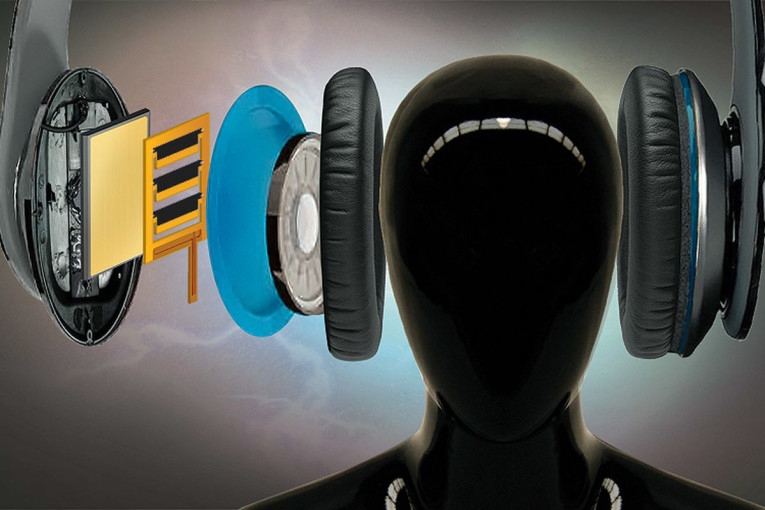
PVDF Film’s Limited Commercialization
While PVDF film has many appealing characteristics, it has not developed the broad commercial appeal that its advocates anticipated. While much audio engineering work was undertaken in the 1970s, the existence of this groundbreaking work is virtually unknown to the Chinese audio companies building speakers, mics, and headphones today.
The amplifier drive issues that blocked PVDF film acceptance as a “drop-in” alternative to electrodynamic transducers are less relevant as there are many integrated solutions from soundbars to docking stations where application-specific amplification is used. PVDF film’s high amplifier rail voltage and drive voltage (yet low power) is easy to handle with today’s technology and voltage doublers, boost converters, DC-DC converters, and so forth are ICs that can be readily and inexpensively designed fit.
Will PVDF film find broad acceptance or will it remain a niche technology? One opportunity is Vivitouch with its haptic sensory enhancement used in gaming controllers and headphones (Photo 5). Perhaps other initiatives will follow. aX
This article was originally published in audioXpress May 2013.
Read Part 1 Here