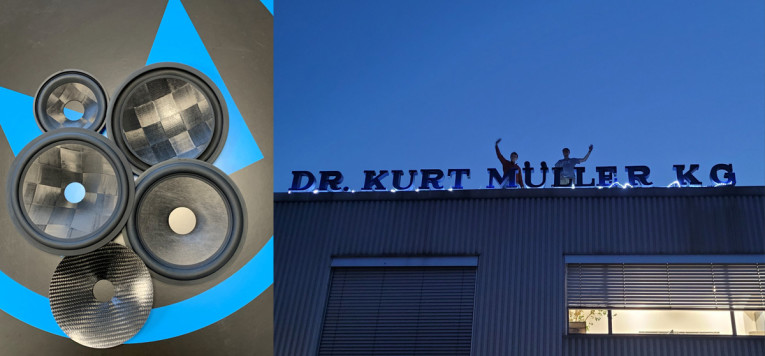
Perhaps the oldest surviving cone factory in the world and certainly one of the most advanced, DKM was originally founded in 1922, in Berlin, as “Pappenguß Gesellschaft für Zellstoffabrikate mit beschränkter Haftung“ (which could be very loosely translated to Cellulose Pulp Cardboard Molding Manufacturing Company LLC). In 1938, its division "Pappenguss-Membranen Dr. Kurt Müller", was supplying products to important customers those days such as Siemens, AEG, and Loewe.
In 1945, after the war, DKM transferred its production from Berlin to the Hannover area of Germany and started to produce cones made out of used paper. During this same period, Dr. Kurt Müller’s old friend Heinz Ebers joined the company as a partner; and both families continued to manage the company until 2009. In 1947 the company relocated to its current location in Krefeld, and also exhibited at the very first Hanover Fair.
Grundig was one of DKM’s first customers when World War II ended. Company owner Max Grundig visited DKM’s factory in Lachendorf by train. In postwar Germany, money had no value so Grundig promised to exchange completed radios for cones and other driver parts. Following this agreement with DKM, Grundig visited all the other component suppliers with similar barter arrangements and finally produced his first radio called the "Heinzelmann."
Parallel to its cone production development, DKM modified its manufacturing process to produce even stronger parts for glove boxes, door panels, and other cellulose-formed parts for the automotive and television industries. Based on this modified process, DKM founded a separate company, which is now part of Johnson Controls.
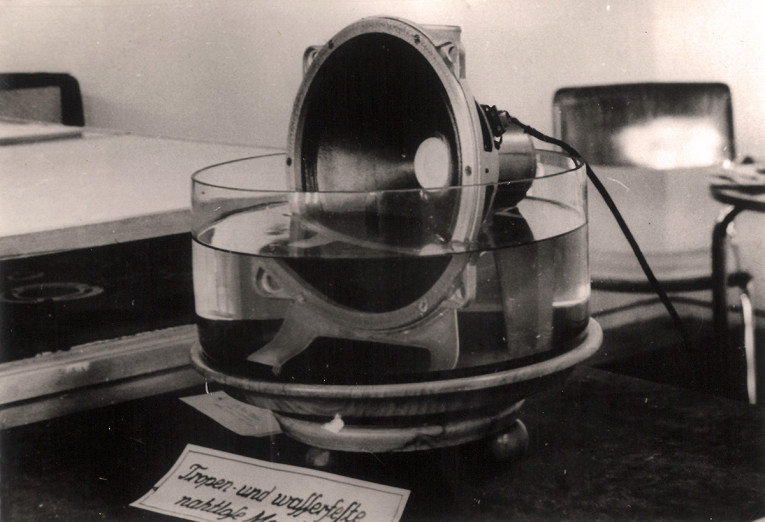
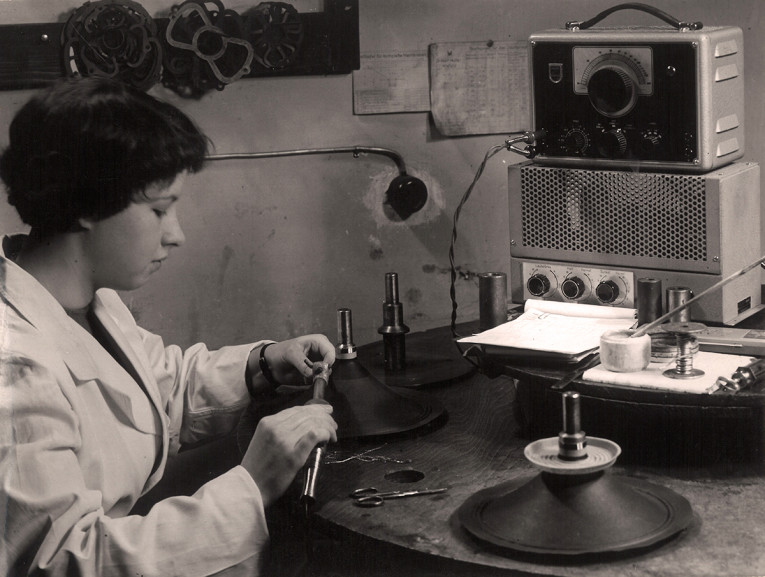
In the fities, DKM expanded its production range to include cones, suspensions, dust caps, and surrounds. At the same time, DKM created its own paper production process. Plastic materials, textile, rubber, foam, aluminum, and titanium components also were introduced with virtually all the parts production done using equipment and tooling developed and produced in-house.
In 1970, the company extended its product range and bought the company Pulsonic Ultrasonics Limited, now known as Kurt Mueller UK Ltd. (UKM), headquartered in High Wycombe, near London. The new subsidiary specialized in supplying speaker assembly parts to pro sound and guitar loudspeaker manufacturers. UKM currently supplies large, air-dried paper pulp cones up to 24" in diameter.
The next expansion came in 1995, with a Czech Republic affiliate for high-quantity manufacturing cones for the automotive industry. Today, more than 80% of DKM’s production is exported worldwide to customers that produce loudspeakers for hi-fi, automotive, pro sound, radio, and television as well as other specialized applications.
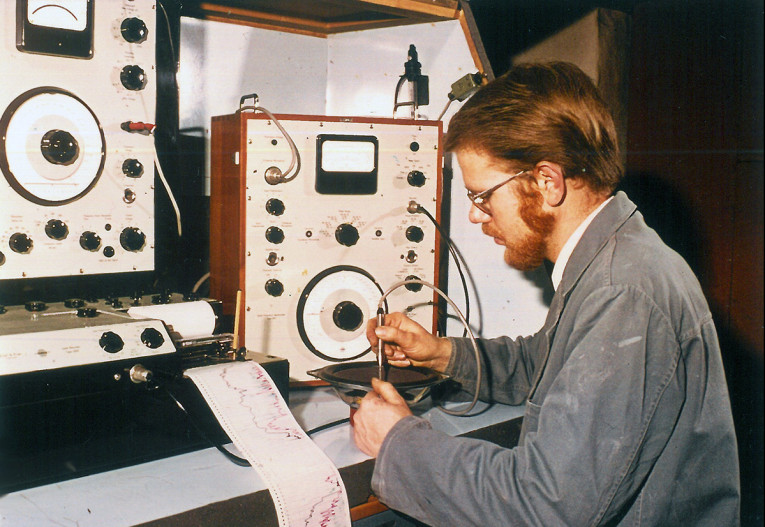
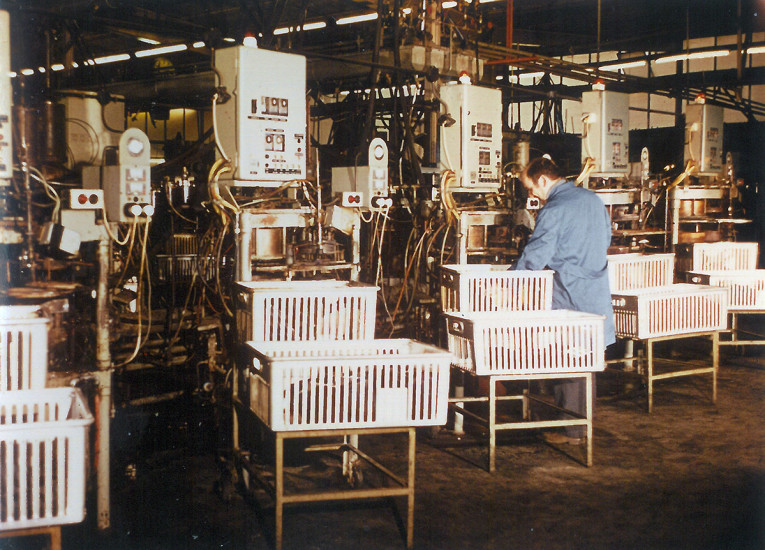
Matthias Ringpfeil, DKM’s director of engineering and a transducer engineer, provides new technology development. For readers unfamiliar with DKM, I should mention that this company has an extremely strong brand reputation in the loudspeaker industry for superior consistency, which is due at least partially to DKM’s highly automated production.
Somewhat unique for a cone company, DKM offers its customers scientific R&D consulting for developing cones, dust caps, and suspension parts. Its close association with Loudsoft (FINEcone), Klippel (3-D Laser Vibrometer), and other engineering solution providers can be an enormous advantage for customers with challenging requirements. In addition, the company has developed its own proprietary measurement protocols for testing the various mechanical parameters of its loudspeaker parts.
Dear DKM – We wish you a Happy Birthday and congratulations on your first 100 years!
For more information about the company, visit www.kurtmueller.com
This article was originally published in The Audio Voice newsletter, (#391), September 8, 2022.
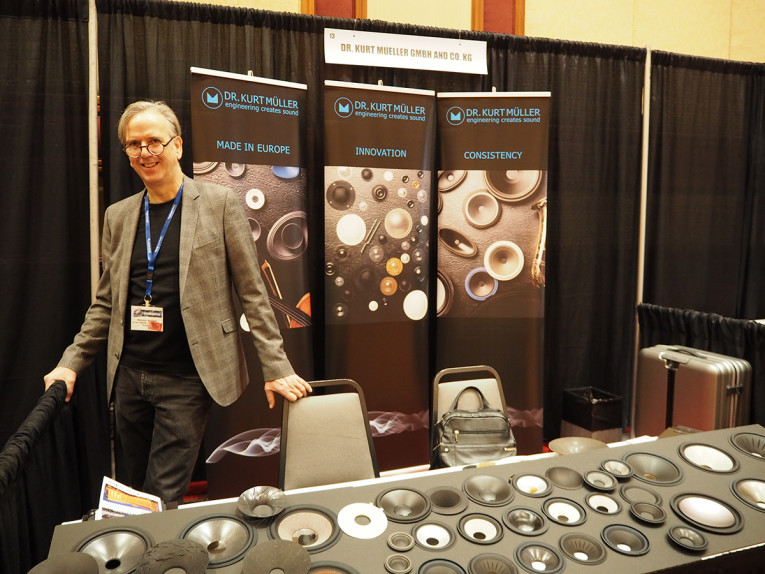
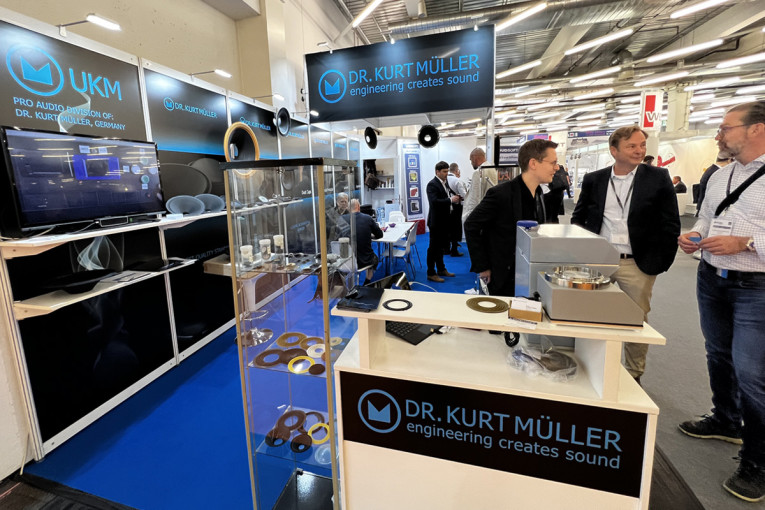