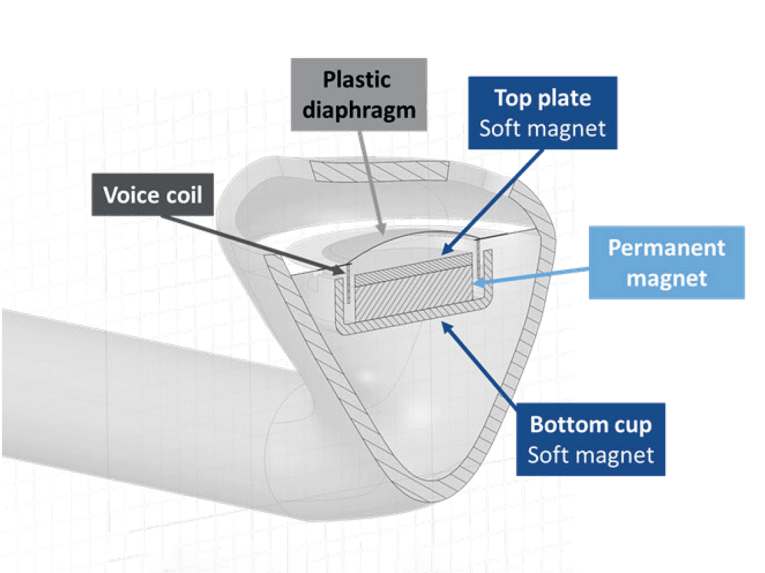
Carpenter Technology developed and studied design with high-performance Hiperco 50 and Hiperco 27 soft magnetic alloys and found that Hiperco 50-based microspeakers are more sound pressure level (SPL) dense and require less current to operate relative to a 1008 steel-based magnetic assembly.
Introduction
The audio market is experiencing considerable market growth, especially in high-value speaker segments. The organic growth of microspeakers, such as wireless headphones and cell phone speakers also drives OEMs and ODMs to provide more creative audio solutions to customers. The paramount challenge to miniaturization is the ability to improve the performance of the dynamic drivers in microspeakers.
Dynamic drivers dominate the microspeaker space, so we identified opportunities for improved design to optimize the driver’s performance. Inside the transducer of the dynamic driver, the permanent magnet is between the top plate and bottom cup, both of which are a soft magnetic alloy, an electromagnet. The plastic diaphragm on the top of the assembly is attached to a voice coil generally made from a high-conductive material (e.g., copper or aluminum). This magnetic assembly within the dynamic driver is one of the most important driving factors of the driver’s performance (see Figure 1).
The fundamental working principle of the magnetic assembly follows the equation F= i.L x B, where the magnetic flux, B, and the current, I, interact to produce a tangential force, F, where L is the length of the conductor or the length of the voice coil for the case of the transducer (see Figure 2). The force of the voice coil moves the diaphragm vertically to move sound waves. The figure of merit of sound intensity, SPL, is highly dependent on the force created by the magnetic assembly and voice coil interaction.
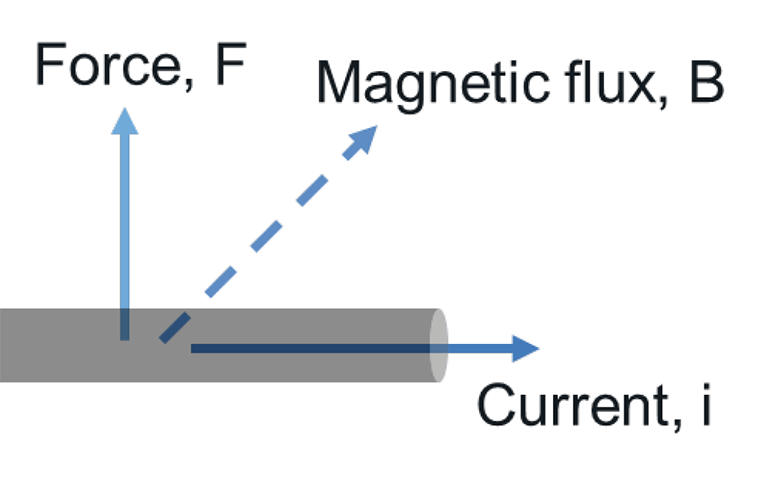
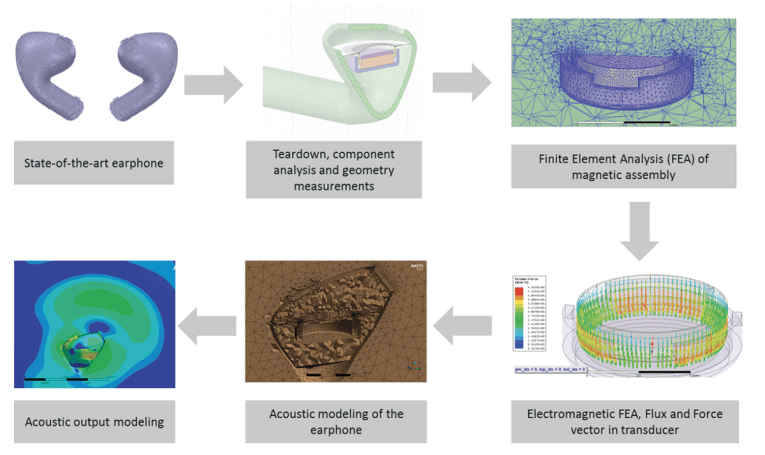
Methodology
The holistic approach started with the teardown of a state-of-the-art, commercially available microspeaker. Component functionality was preserved, and mechanical and electrical measurements were taken. We then designed and ran finite element modeling of the microspeaker, as shown in Figure 3.
The geometry of the metal and copper components, as well as their surrounding spaces, was modeled and meshed in ANSYS Maxwell 2018.2 to map the electromagnetic field. The mesh of the baseline model contained 223,441 finite elements, but plastic components were ignored, as they do not affect the generated magnetic field. The acoustic model, generated in ANSYS Mechanical 19.2, represents the cone, the surround, and the voice coil, as well as the air inside the acoustic cavities and outside the microspeaker. The simulation uses a harmonic solver, assuming a sinusoidal input and a sinusoidal response in the system, and is a coupled model of the structural vibration of the speaker with the pressure waves in the air. The displacement degrees of freedom and pressure degrees of freedom are directly coupled in the stiffness matrix and solved simultaneously.
The air inside and outside is connected by holes in the earphone to transmit air pressure. The plastic walls of the earphone, as well as the metal and magnet, are considered rigid and not modeled. The finite element mesh contained 1,539,976 nodes. The acoustic model was excited by force applied to the voice coil matching the force calculated in the magnetic model—the radiation boundary conditions to prevent the sound waves from reverberating inside the domain. The SPL was measured at the main opening of the micro speaker (earphone), where the ear canal would be located with an average value calculated across this opening.
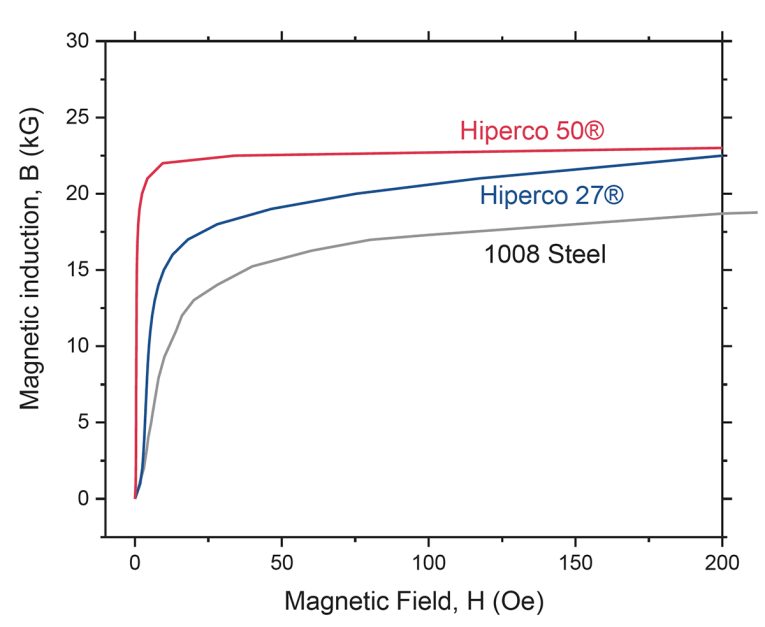
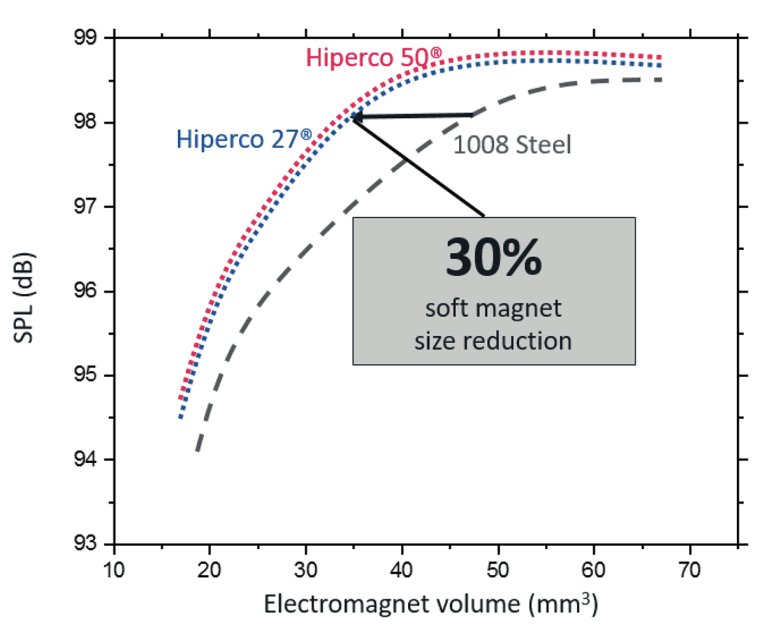
Result and Discussion
Figure 4 shows the magnetic induction of the soft magnetic structures for the microspeaker electromagnet. Hiperco soft magnetic alloys are a high-performance replacement for the 1008 steel (low C steel) used in the commercially available microspeaker. Composed primarily of iron-cobalt, Hiperco 27 and Hiperco 50 contain 27% and 50% cobalt, with 22% and 25% more magnetic induction at 200 Oe external magnetic field, respectively, relative to 1008 steel.
The higher magnetic induction in the electromagnet structure increases the magnetic flux in the voice coil interacting with the current. This increases the force output and, ultimately, the SPL of the dynamic driver. Figure 5 shows the SPL for Hiperco 50, Hiperco 27, and 1008 steel electromagnet transducer assemblies for various transducer volumes. Hiperco-based transducers produce similar SPL output with a ~30% smaller size relative to 1008 steel. Additionally, Hiperco transducers of any given size produce a higher SPL than the 1008 steel equivalents.
The microspeaker with Hiperco 27 or Hiperco 50 would enable a higher excursion space. The excursion is the distance that the audio diaphragm can travel. The diaphragm is attached to the voice coil (the copper coil in general) and moves in the Z-direction. With the 30% size reduction of the soft magnet assembly, we found that we would obtain an additional 0.36 mm space in the Z-direction, as shown in Figure 6. To put that into perspective, most of the microspeakers used in cell phones have an excursion space of 0.40 mm. From that perspective, Hiperco would enable a 90% increase in the excursion space and eventually contribute to enhancing audio intensity or SPL and other audio outputs.
The current to move the voice coil was also modeled and optimized to obtain a similar SPL. Figure 7 shows a comparison of the current required for obtaining a similar output. Hiperco 27- and Hiperco 50-based transducers require 6% and 8% less current input, respectively, in voice coils to provide a similar SPL output compared to 1008 steel-based transducers.
By requiring a lower current to run the device at similar output levels, utilizing Hiperco soft magnetic alloys increases the battery life of wireless microspeakers. Increasing battery life by 6% to 8%, Hiperco solutions require less charging, thus improving the user experience.
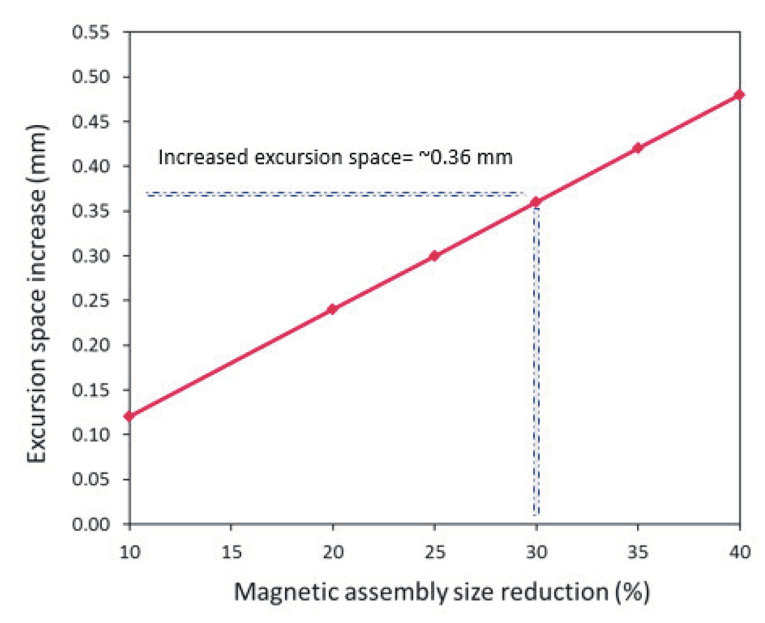
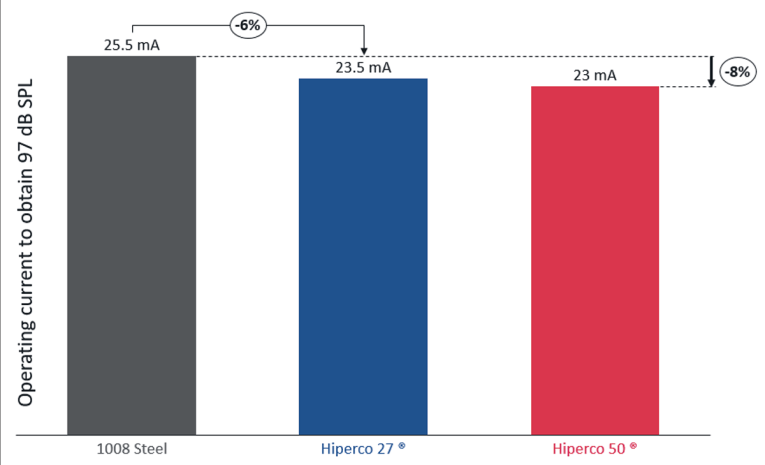
Conclusion
As one of the essential pieces of the most common consumer headphones, loudspeakers, and cell phone speakers, dynamic driver units can be optimized for increased performance, decreased weight, and increased battery time through the modification of magnetic material used within the microspeaker. Hiperco soft magnetic alloys enable electromagnet size reduction up to 30% — an operating current reduction of 6% to 8%, and a 1 dB SPL increase.
For more information, visit the Carpenter Technology website at www.carpentertechnology.com. VC
This article was originally published in Voice Coil, November 2020