Transformers And Inductors
The two main categories of inductors are air-core and iron-core. Air-core inductors contain no magnetic iron. The only loss in an air-core inductor is due to the copper resistance. Iron-core inductors have cores made of various alloys of iron and/or other materials that give it the required characteristics.
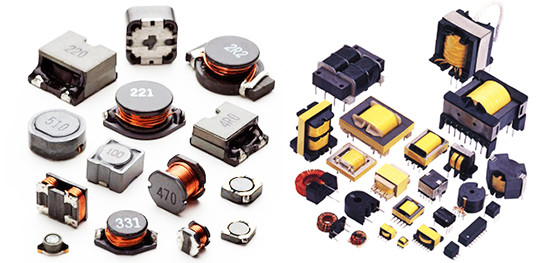
In addition to the copper winding losses, iron-core inductors also produce losses associated with the iron itself. Eddy-current losses are caused by the varying magnetic field inducing a current to flow in the core. Hysteresis losses are caused by the nonlinear manner in which the iron core becomes magnetized and by the residual magnetism left in the core. Both eddy-current losses and hysteresis losses are considered to be real power losses5,6,7.
The primary failure mode for wound devices such as transformers and inductors is an open winding, and the likelihood increases directly with the decrease in wire diameter. Both the insulation and the wire itself are more fragile and prone to damage during winding with smaller gauges.
Another failure mode is a winding short. If the device is exposed to excess current, both the wire insulation and interwinding insulation may fail. A shorted turn causes heavy current to flow and may cause the wire to fuse and open. A short can also occur to the core. If the primary winding in a power transformer shorts to the core, and the transformer is bolted to the chassis, AC line voltage can end up on the chassis if there is no third-wire safety ground. If the equipment has a safety ground, the line fuse should safely open, clearing the fault.
This is made less likely because transformers are usually made with the primary winding on the outside to maximize coupling to the secondary. In older inductors or transformers, rust or corrosion may form on the laminations, causing an increase in eddy current losses. This could change the magnetic properties enough to affect operation.
The failure rates versus temperature for audio and power transformers and chokes is shown in Fig. 11. There is no curve for failure rates versus voltage or current—this is determined by calculating the winding temperature rise and applying the temperature factor to the base failure rate.
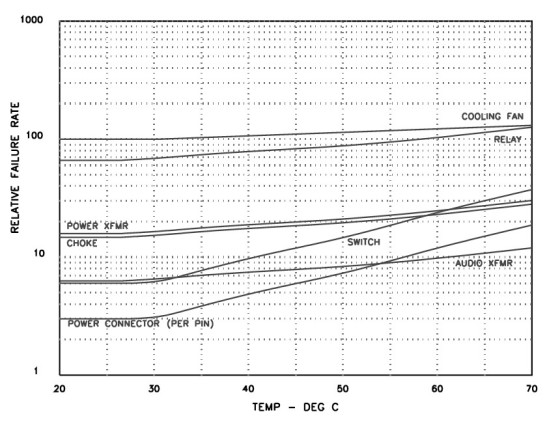
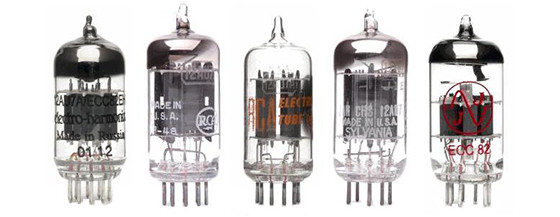
Vacuum Tubes
Vacuum tubes are not listed in TR-332. Section 7 of MIL-HDBK-217 lists the failure rate (λb) for receiving tubes as 5 failures/106 hours (200,000 hrs MTBF), and 10 failures/106 hours (100,000 hrs MTBF) for rectifier tubes. These failure rates include random failures and wearout, and there is an additional πL learning factor that penalizes tube types newly introduced
in the last three years.
Even if you never apply any plate voltage, tubes will still fail once the heater/filament opens or its emissions fall below a useful level, but these MTBF numbers should be welcome news to tube equipment owners who leave their components on at all times.
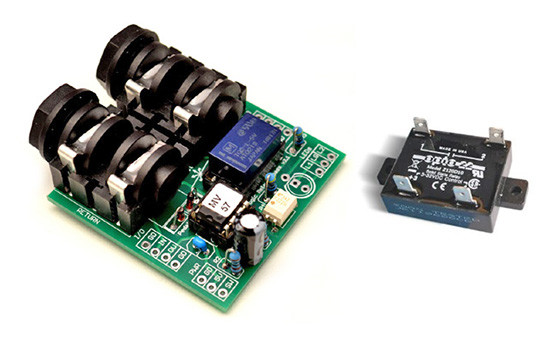
Electromechanical Relays And Switches
When a relay coil is energized, the contacts do not transfer immediately. A delay of 1μs to 10ms is required in order for action to take place. The magnetic field in the coil exerts a mechanical force on the movable armature and causes the contacts to make or break the circuit in which the relay is connected.
Time-varying magnetic and mechanical forces, as well as armature inertia, allow relay contacts to “bounce” one or more times when they open and close. In addition, if the contacts close into a low resistance, high current flow can cause a back-emf to be generated that tries to force the contacts open. Some over-travel is provided in the armature system to minimize rebound and provide for some contact wiping, but contact bounce is largely unavoidable.
When the circuit to an inductive load is opened, most of the energy stored in the load will be dissipated through arcing at the contacts. Design engineers must select contacts large enough so that deterioration from destructive melting is minimized, but not so large that the current density falls below the critical level needed to ensure low contact resistance. A slight fusing of the contact surface after each operation is actually desirable to remove oxidation and maintain a fresh metal contact surface.
For “dry” circuits (very low voltage and current) it is necessary to use precious metal contacts that do not oxidize. If these contacts are ever exposed to high current, the arcing will destroy the surface plating, which cannot again be used in dry applications.
Switch contacts have all the characteristics of relay contacts. In the direct-acting contacts of slide and rotary switches, the speed of operation is that of the actuating lever or shaft. Toggle switches use indirect actuators to increase the contact speed, so they will bounce when opening and closing.
The failure rates versus temperature for relays and switches is shown in Fig. 11. The failure rates versus contact current for relays and switches (per contact set) is shown in Fig. 12.
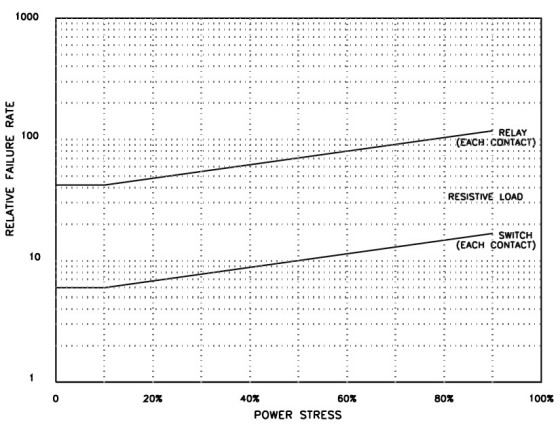
Connectors
The failure rates versus temperature for connectors (per pin) is shown in Fig. 11. While all plug-in connectors are given the same failure rate in the reliability specifications, the contact material is important, especially for low level (dry) signals. Copper and tin-plated contacts will eventually oxidize and cause increased noise, or a high resistance or open circuit.
Even silver, the best electrical conductor, is not immune to this problem. Noble metals such as gold or rhodium provide much better long-term performance. For those of you with optical connectors in your digital audio components, their λSS base failure rate according to TR-332 is 100 versus only 0.5 for electrical coax connectors.
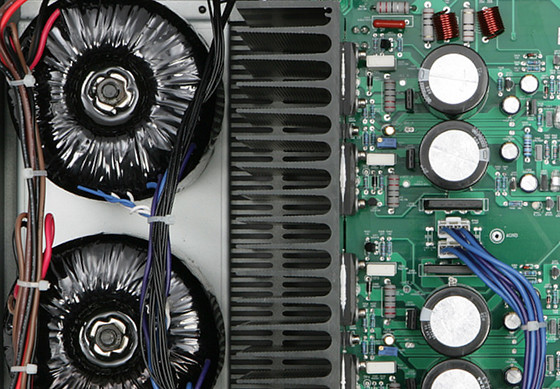
So What Can We Do About It?
If you design electronic audio equipment, the choice of stress derating and temperature are the two primary variables you have control over that will affect the reliability of your design.
Parts Derating
Everyone knows that you should never exceed the maximum specified rating (voltage, current, wattage, or temperature level) of a component. However, for long and reliable life, a part should never even be operated at its maximum specified rating. The ratio of the actual applied level to the maximum rated level is called the derating factor. In the absence of specific failure rates, a good rule of thumb is that every 20% reduction below the maximum rated electrical stress level will double the life of a component.
The same rule of thumb says that every 10°C reduction in temperature will double the life of a component. Refer to the temperature derating curve in Fig. 13. In general, the highest temperature that a part should be exposed to (including self-heating)— the design limit temperature (Tdes) — can be derived
from the following formula:
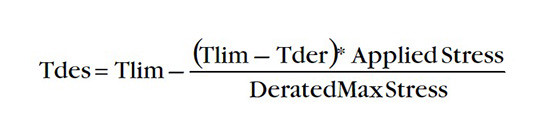
There is a logarithmic relationship between stress and failure rate, so it pays to be conservative. If you wish to be unusually conservative, never apply more than half the rated voltage, current, or wattage to any component, but this may result in excessive component costs.
Table 2 (see part 2) lists derating factors that are a bit more practical. To apply these factors, multiply the maximum rating of the part by the derating factor. For instance, let’s say a ceramic capacitor is rated for 50V. You should not apply more than 40V across the cap (50 × 0.80). The applied voltage is always the DC level plus the peak of any AC voltage ripple that may be riding on top.
Where more than one factor is given, you should not exceed any of the factors. For instance, the voltage and current deratings for an IC regulator are 0.80, which would lead to a power derating of 0.64. However, the power derating limit should not exceed 0.50 of ratings for these components, so either voltage or current will need to be less than 0.80 its rating.
Temperature
The relationship between reliability and temperature is an inverse exponential:

where R is reliability and T is temperature.
Ambient temperature is the most important factor for long life expectancy and high MTBF. Removing heat is very important to increase reliability. Heatsinks (conduction) and fan cooling (convection) are more effective than simple heat radiation. This is because heat removal by conduction and convection are directly related to the thermal conductivity and temperature, while heat removal by radiation is exponential to the fourth power of temperature.
Compact designs make temperature control more difficult. Heat-producing components are forced closer to heat-sensitive components, and the internal temperature rise is greater for a given power dissipation because the heat-radiating surface area is smaller.
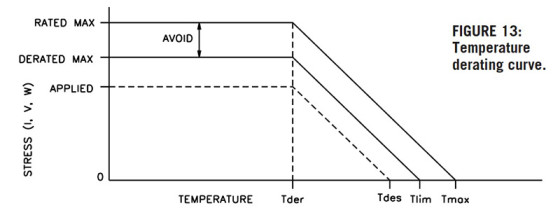
Design Tools
One way to increase MTBF is to use fewer components. You can achieve this by minimizing the number of protection devices, which results in a higher calculated MTBF, but may produce a worse real-world reliability due to subsequent damage after a power component fails. In order to evaluate these cascading effects, reliability engineers use additional design tools.
One of the most important is the failure mode and effect analysis — FMEA (see sidebar in Part 1). The FMEA takes each mode of failure for a given component (short, open, degradation, value shift, and so on) and then determines the effect on the overall equipment. A failure in one device can propagate and lead to subsequent failures in other components.
An FMEA is complementary to the design process. Whenever an undesirable failure effect is found, the engineers will evaluate the compensating conditions, and perhaps change the design to make the failure effect more benign. For example, assume an aluminum electrolytic power-supply capacitor fails short. The resulting high current could then cause the rectifier bridge or power transformer to fail, or the capacitor to explode. By including properly sized protection devices in the design, the effect of the power failure is limited to an open fuse or circuit breaker, even though the MTBF is decreased a bit. All the other components in the power supply are protected from damage.
There are also situations in which operating procedures can increase the adverse effect of a failure mode. For instance, in order to maximize the life of vacuum tubes and prevent cathode stripping, it is advisable to delay the application of B+ voltages until after the tube heaters warm up. Some manufacturers provide automatic time delay relays for this function. Others provide separate power and B+ switches that require the equipment owner to manually delay the B+ application.
The second method is more reliable from a component failure rate standpoint, but it is also prone to inadvertent “operator error.”
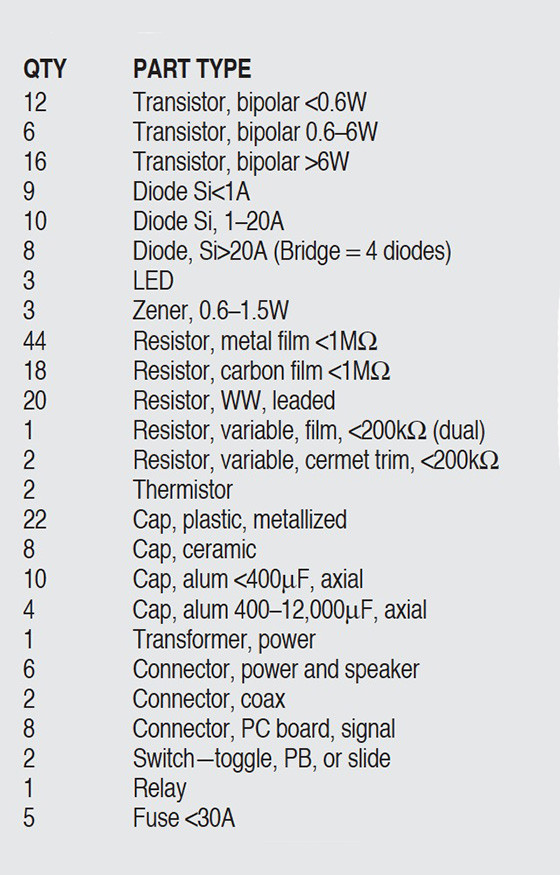
MTBF Calculation Example
Let’s take a hypothetical solid-state power amplifier and determine its MTBF in a benign home audio system. It is a 75W stereo amplifier with two paralleled pairs of bipolar output transistors, a protection relay, and an input volume control. The parts breakdown is shown in Table 3.
The quickest way to make a reliability estimate is by using the Parts Count method from TR-332, in which you assume an operating temperature of 40°C and electrical stress on all parts to be 50% (i.e., a 100V cap has 50V applied, and so forth). Also use Device Quality Level I non-hermetic parts, to avoid the considerable penalty for Quality Level 0 “remanufactured,
reworked, salvaged, or gray-market components.”
Using all the failure rates, π factors, and part quantities, you find λamplifier to be 3742.8 failures/109 hours, or an MTBF of over 260,000 hours. That’s over 30 years of continuous 24/7 operation, but it presumes that more than 7,000 hours of operating time have already elapsed.
Even if you factor in the first year multiplier to account for early failures, the MTBF is still a healthy 66,795 hours (over nine years of continuous operation). That could explain why the dreadful-sounding receiver I used in college is still working. Your garage door remote control, with its low on-time duty cycle, could last “forever.”
Environment is everything. If you took your amplifier from its controlled home environment and put it in orbit in a communications satellite, the MTBF would be 1/15 that of your home, or 5089 hours — just under seven months. The MIL Handbook has a similar factor for low-earth orbit.
If your amplifier were shot from a cannon, the component MTBF would drop to 238 hours. (The actual amplifier life would, of course, be microseconds given its mechanical packaging.) That gives you a real appreciation for the difficulties that engineers and scientists faced while developing WWII antiaircraft proximity fuses using fragile vacuum tubes.
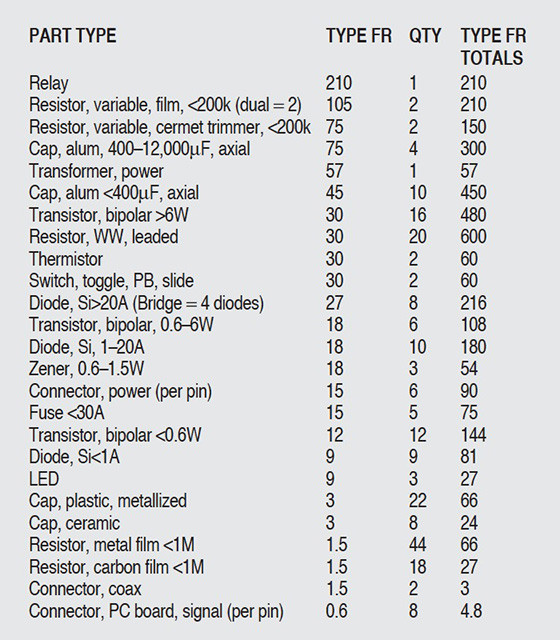
I also calculated the failure rate for the hypothetical amplifier using the MIL-HDBK-217F Parts Count method, with the same 50% electrical stress and 40°C operating temperature. The MTBF was 59,592 hours, or more than seven years of continuous operation. The MIL Handbook penalizes aluminum capacitors and the protective relay much more heavily than the TR-332 does.
Ironically, the fuses and the protection relay and its sensing circuitry, all designed to save your speakers in the event of an amplifier failure, causes the MTBF of the amplifier to drop by almost 12%!
Now, look at the parts with the highest failure rate and see what effect changes in electrical stress and operating temperature have on the failure rates of these five parts and the overall amplifier MTBF. Table 4 is sorted by Type Failure Rate (2nd column), while the 4th column is the Total Type FR, or Type FR multiplied by quantity.
You can see that devices with moving parts (relay and pots) have the highest failure rates. Next are the large aluminum capacitors. The power transformer also has a fairly high λ. I’m not sure why TR-332 does this — it is not penalized as heavily in the MIL Handbook.
This list gives you a feel for the first failures you can expect as the amplifier operating hours increase. Finally, I ran the TR-332 MTBF calculations using the same 40°C average operating temperature, but with actual electrical parts stresses, and calculated case temperatures in the power devices. The MTBF (factored for early failures) dropped from 76,337 hrs to 69,691 hrs, or 9% lower. The biggest penalty was due to the temperature rise in the output transistors and the higher voltage stress on the 63V DC rated aluminum reservoir filter capacitors (55V DC applied versus 31.5V DC for the 50% stress factor in the Parts Count method). The top six failure rate parts are now the relay, the large aluminum capacitors, the smaller aluminum capacitors, the dual volume control pot, the power transformer, and the trimmers.
I hope this article will give you a feel for the design versus cost decisions that engineers must make to bring a product to market.
References
5. “All About Toroidal Transformers,” C. Hansen, Popular Electronics, May 1996, pp. 53–56, 78.
6. “Berning ZH270 Power Amp, Part 1,” C. Hansen, Glass Audio 1/00, pp. 23–30.
7. “Power Transformers for Audio Equipment,” P. Millett, audioXpress June ’01, pp. 14–19.
8. The Joy of Audio Electronics, Chapter 3, C. Hansen, Audio Amateur Press, Old Colony Sound Lab,
This article series was published in audioXpress, from November 2001 to January 2002.
Read Part 1 here
Read Part 2 here