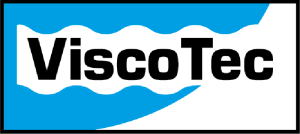
According to statistics, the proportion of connected cars in the USA will be around 97% in 2035; the figure could be similar in Europe. An increase in the level of automation across the entire value chain in automotive manufacturing has already been evident in recent years. Starting with the OEM and the system and component suppliers and extending up to the tool and die makers. Wherever it was and is feasible, manual activities are being partially or completely automated. Manufacturers of high-quality integrated loudspeakers have recognized the potential of automation for themselves and are following suit. Not without a lot of challenges.
If manufacturers of audio systems want to remain the first point of contact as partners of the automotive industry, quality must be guaranteed in addition to improved performance in assembly. One hurdle: Loudspeaker components are mostly bonded together. Only a technology that can guarantee precise dispensing of adhesives at high cycle rates is therefore suitable for reliable scaling from manual to semi- or fully automatic speaker production.
As a rule, the individual main components of a loudspeaker, i.e., coil, permanent magnet and diaphragm, and the intermediate components are always assembled in the same order. It starts with the sealing ring that encloses the loudspeaker, followed by the connection of the coil and the connection of the cone to the dust cap and to the coil, and from the cone to the enclosure and the chassis. Next, the basket and the frame are connected, the cone to the coil, and then the coil and the spider. After attaching the so-called upper plate to the chassis, the magnet and the plate are connected. Depending on the country of manufacture, these steps are performed manually or only partially automated.
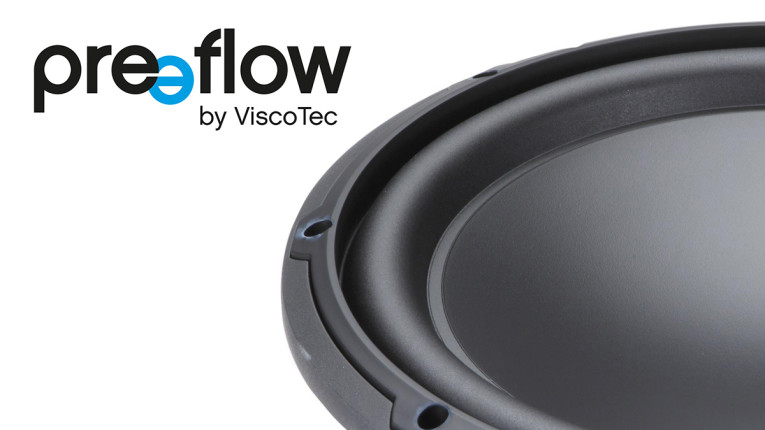
Individual Components and Adhesive: Finding the Right Vibes
Important parameter: The adhesive. It must perfectly match the materials used. Carbon steel, sintered ferrite, neodymium, rubber, or foams, for example, are bonded together using epoxy resin (1 or 2-component) or acrylic. This bonding ensures that the electrical vibrations are precisely converted into mechanical vibrations. Then, in turn, a surface is rhythmically made to vibrate, which in turn radiates the sound.
As a result, every faulty form-fit and material-fit connection in the "loudspeaker" system leads to audible losses in quality. Particularly in focus: The diaphragm suspension, also called surround. It keeps the diaphragm flexible and connects it air-tight to the loudspeaker basket. In this context, it is interesting to note that small loudspeakers hardly differ in principle from headphone drivers, apart from the fact that the diaphragm is located closer to the ear.
In principle, a headphone diaphragm can reproduce the entire audible frequency range from 20Hz to 20kHz. Whilst frequencies below 150Hz are perceived by the entire body, and not only by the ears in natural hearing, this is not the case with headphones. Since the physical principles of loudspeakers and headphones are almost the same, production can theoretically be automated for both products if precise dispensing can be ensured on both a large and a tiny scale, even at high cycle rates.
One technology that masters this precision and high cycle rate with ease and, what is more, has demonstrably been running maintenance-free for three years in the plant of a loudspeaker manufacturer, is preeflow. The mere fact that the dispensing system does not require any plant shutdowns is an indicator of the high performance that is possible in production and, at the same time, has an extremely positive effect on the total cost of ownership. Companies wishing to automate such dispensing and bonding tasks are free to make their own plans, as preeflow can be adapted to almost any speaker shape and size.
Regardless of which contours are desired and required, and at which speeds dispensing is performed: Loudspeaker manufacturers remain flexible with regard to portfolio development. Critical areas such as curves are mastered with ease by the slower-running dispensing caterpillar, which avoids material buildup just as reliably as unsightly overlapping of the caterpillar ends. In terms of costs, preeflow is an efficient technology that reliably avoids dripping or stringing of the material, which represents added value from both a cost and sustainability perspective.
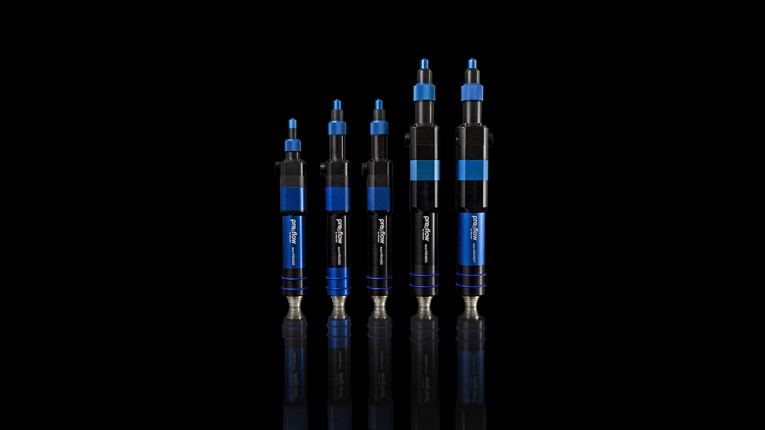
Integration Into New and Existing Processes
Loudspeaker manufacturers can use either the eco-PEN or eco-DUO precision volumetric dispensing systems. Both ensure stable dispensing even at high cycle rates. The type of speaker bonding varies from manufacturer to manufacturer, as does the exact design and materials used by a speaker or headphone manufacturer. Since preeflow masters and covers the entire spectrum of existing processes, it can be easily integrated into existing processes.
Whether coil bonding, magnetic systems, diaphragm damper adhesives, wire fixation or contact protection, in addition to UV-curing adhesives, two-component materials, and any other type of adhesive with a viscosity ranging from aqueous to paste-like, can be dispensed. Even with the smallest adhesive quantities from 0.001 ml, a repeatability of over 99% can be guaranteed, which is a prerequisite for high-performance (semi-) automated loudspeaker production.
The dispensing system can be easily integrated into existing production lines or connected to flexible industrial robots. Even after retrofitting or upgrading an existing production line, maximum flexibility and performance is assured, as product application can be achieved from different angles and positions. The question of shift-dependent downtimes and varying production line running times does not occur with preeflow, as this technology requires neither pre- nor post-processing operations.
www.viscotec.de
www.preeflow.com
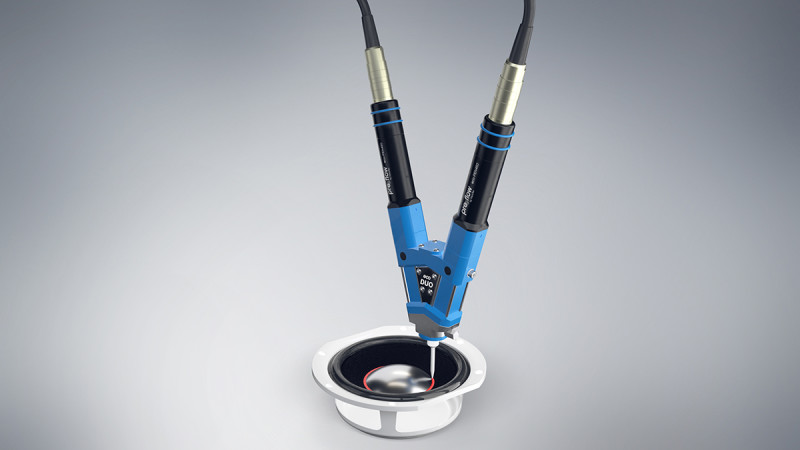