In order to avoid unpleasant surprises, it is worth getting in touch with the dispensing technology manufacturer's contact person at an early stage of the project. This way, all costs can be made visible from the start.
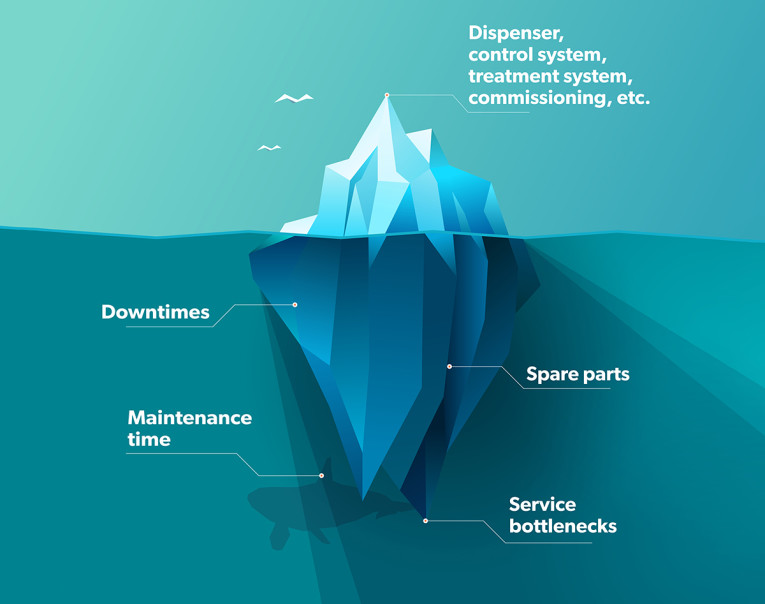
Let us compare it to looking at an iceberg. At the top you can see only the investment in the equipment itself. Depending on the need: Dispenser, control system, treatment system, commissioning, etc. But other factors are lurking beneath the surface of the water. What happens after the initial operation of a system? You may be faced with maintenance time, spare parts or downtime, depending on the availability of spare parts, service, etc. And all this can be associated with further costs.
A reliable partner knows the hidden areas below the surface of the water. Together with you, efficient and rewarding products can be put together. At preeflow, for example, work is done daily to reduce the areas below the surface of the water as much as possible. The portfolio is constantly being developed to meet your specific and individual needs for your process. The goal is: To provide an exceptionally good experience, together with your investment.
Best Choice According to ROI
Let us go into more detail to determine the return on investment (ROI). So, after what period of time or after what quantity of dispensing operations have I covered all the costs of my initial investment? Exact data depends on the material to be dispensed, the dispensing equipment used, the cycle times, the process parameters and much more.
In most cases, you will receive at least two offers. Why the one that is cheaper at first sight is not necessarily the better one in the long run, is shown by the example of our DC rotors.
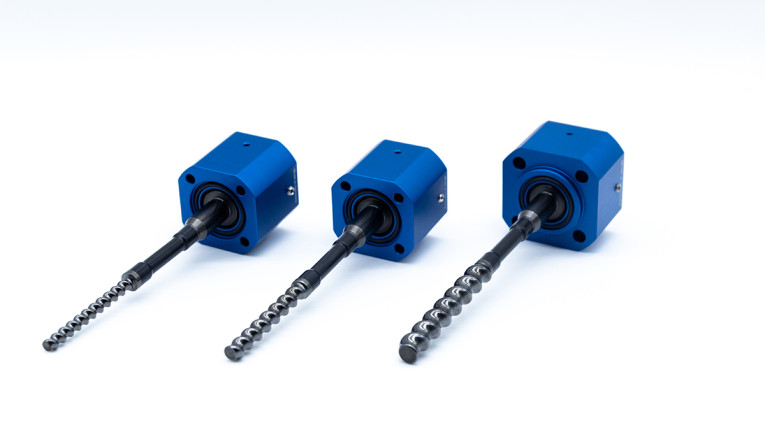
Various system providers promise to fulfill all the requirements and to be able to implement dispensing with their system. Among them is preeflow - the eco-PEN was recommended for this application. Equipped with a special stator material and a Diamond Coated Rotor (DC Rotor for short) - developed for highly abrasive (and sometimes heat-conductive) materials. Even for the most challenging applications. The Diamond Coating, specially developed by ViscoTec, is a new type of multi-layer coating that has a surface hardness of well over 2000 HVpi. In addition to the extreme hardness, the coating also has tribologically optimized properties. Hard fillers can be dispensed with the DC rotors and the sliding properties and friction values are optimized - for the best possible overall performance.
Other suppliers may use the same or similar dispensing technology, but their standard products cannot withstand the demands of the highly abrasive dispensing materials in the actual process for long. Conventional dispensing systems are quickly brought to their limits when processing thermal pastes. The replacement of spare parts follows not long after. This also includes costs for retrofitting and the ordering process. This is clearly shown in the following graph. It shows the costs in relation to the number of parts produced and the number of dispensing processes.
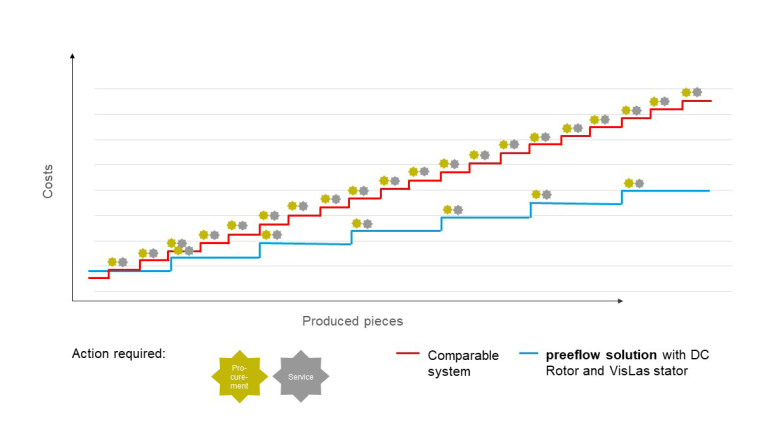
The initial investment for the preeflow solution with special equipment is initially somewhat higher, but from the very first spare part change, it is the most economical and effective solution. Thanks to the robust components in the one- or two-component dispensers, maintenance and spare parts changes are reduced by two to three times. This saves you time and money. The process becomes more reliable overall.
To calculate the ROI for your specific application, long-term tests can be helpful. preeflow implements these tests under process conditions in its in-house technical center. In addition to the headquarters in Germany, numerous distributors and 5 subsidiaries worldwide support implementation and decision-making - one of them is most likely not far from you. Benefit from a guaranteed delivery time of spare parts within 24 hours, worldwide, from more than 20 years of experience in micro dispensing and from an outstanding service! It is up to you to make the best choice.
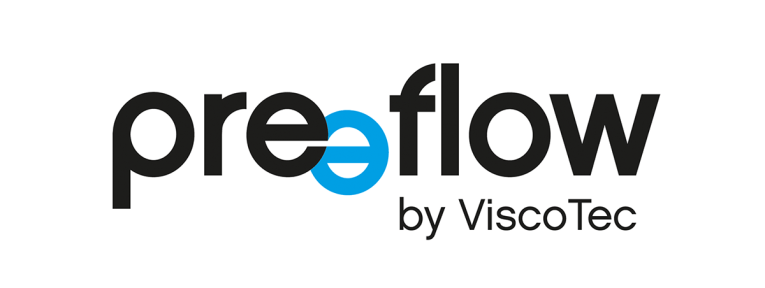
Micro dispensing in perfection!
Established in 2008, preeflow ensures precise, purely volumetric dispensing of liquids in the smallest of quantities. preeflow products are appreciated worldwide, not to mention because of their unique quality - Made in Germany. An international distribution network offers professional service and support in all areas of preeflow dispensing systems.
The various fields of application include, among others, automotive, electrical and electronics industry, medical technology, aerospace, renewable energies, electrical and hybrid technology and measurement and sensor technology. The complete preeflow portfolio can be easily integrated due to standardized interfaces. Worldwide more than 50,000 preeflow systems are working in semi or fully automated dispensing applications to the user’s and customer's complete satisfaction.
preeflow is a brand name powered by ViscoTec Pumpen- u. Dosiertechnik GmbH. ViscoTec primarily deals in systems required for conveying, dispensing, applying, filling and emptying medium to high-viscosity fluids. Read this article to learn more about loudspeaker bonding with preeflow. The headquarters of the technological market leader is in Töging (upper Bavaria, near Munich). In addition, ViscoTec has subsidiaries in the USA, in China, Singapore, Indie and in France and employs about 270 people worldwide.
www.preeflow.com
www.viscotec.de