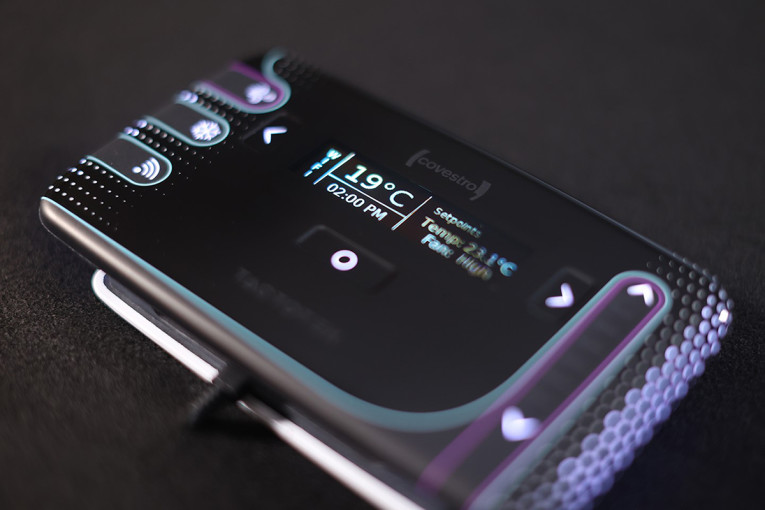
Covestro is one of the leading producers of high-performance polymers and the company has been focusing on the development of innovative, sustainable solutions for products used in many areas of daily life, fully committed to the circular economy. The company serves the automotive, construction, wood processing and furniture, electrical and electronics, and healthcare industries with 50 production sites worldwide, employing approximately 18,000 people as of June of 2021.
Covestro's presence at CES 2022 is always of great interest for the automotive and consumer electronics industries, and this cooperation with TactoTek will showcase an important concept of great interest for any developers working in control panels, wearables and integrated audio products. 3D interactive surfaces are increasingly a focus for designers looking for sophisticated shapes and rapid, inexpensive customization, as well as to make sure their creations are part of the circular economy. Covestro and TactoTek eco-friendly approach explores the possibilities of polycarbonate resin and films that give structure to in-mold structural electronics (IMSE).
Nearly invisible tactile controls with displays that are activated by touch are an example of designs and surfaces increasingly used in consumer electronics. To accomplish this, not only do the electronics need to be thin and lightweight, the material that houses them must be strong, but moldable at low enough temperatures so the electronics are not damaged during manufacturing. And thanks to Covestro’s mono-material solutions, as electronics age out, their polycarbonate housings can be recaptured and re-used, while the application’s useful life is extended. TactoTek already makes the world’s most advanced smart surfaces, and advanced materials from Covestro are a natural fit for thin, protective surfaces that house functional and decorative controls.
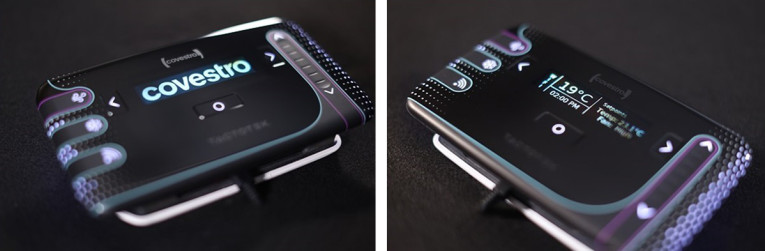
Covestro worked with TactoTek to create demonstrators highlighting functional electronics that are simultaneously control surface, computer and display. The final design to be demonstrated at CES 2022 features a Raspberry Pi computer, OLED display, all necessary circuitry and electronic components, as well as inks for coloring and decoration in a Makrolon resin, sandwiched between two layers of Makrofol film. The result? A powerful new frontier in consumer electronics with a mono-material design in which the plastic can be recovered at will and turned into new raw materials.
In addition to the Nighthawk, Covestro will showcase the BatRay overhead control console. These demonstrators are designed to show various in-home and in-car use cases that are not only innovative, but are more eco-friendly because they reduce the number of parts to fulfill a use case, reduce plastics use by up to 70% and CO2 emissions by up to 35% relative to conventional electronics.
In both units, electronics for wiring and touch controls are printed using clean, additive processes, and electronic components are surface mounted on polycarbonate film, which, along with a decorative film is inserted into an injection mold for encapsulation in polycarbonate resin. The result is a single piece, seamless, electronic structure, IMSE.
These functional and decorative surfaces include in-mold illumination, and touch controls. The Nighthawk includes a display added after the injection molding process; the BatRay includes a printed Bluetooth antenna. The high clarity, low viscosity and unique thermal conductivity of Makrolon polycarbonate resins are key to making these devices possible, while Makrofol polycarbonate films provide UV and scratch resistance.
Reducing the complexity of the material stack of any device increases the potential for efficient separation and recycling. Covestro brings over 65 years of polycarbonate manufacturing experience to bear in helping to bring these new, innovative, and more sustainable solutions to the world.
"Devices which utilize IMSE solutions are not only thinner, but also 50-70% lighter than those traditional devices, which reduces the carbon footprint of those devices during manufacturing, transportation and use," says John Skabardonis, Technical Marketing Manager at Covestro. "IMSE parts have passed the demanding requirements of the automotive industry opening the door to rapid adoption in other markets. Moreover, both cosmetics and functions of IMSE parts can be modified without tooling changes supporting efficient localization and low cost product upgrades"
"Structures aren't going away, so there's great benefit to integrating the electronic features users want within those structures and simplifying the overall assembly, turning them into smart surfaces," says Jussi Harvela, CEO at TactoTek. "IMSE solutions enable differentiated designs, are easily integrated into both familiar and unconventional locations, moreover, they are a significant step toward a more sustainable future."
www.tactotek.com
www.covestro.us
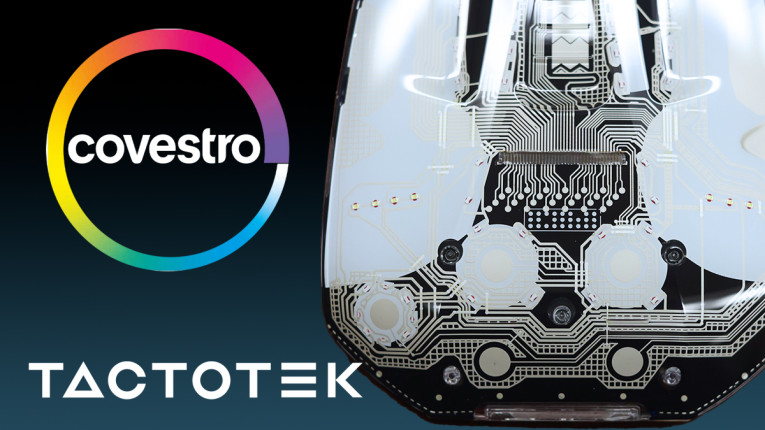