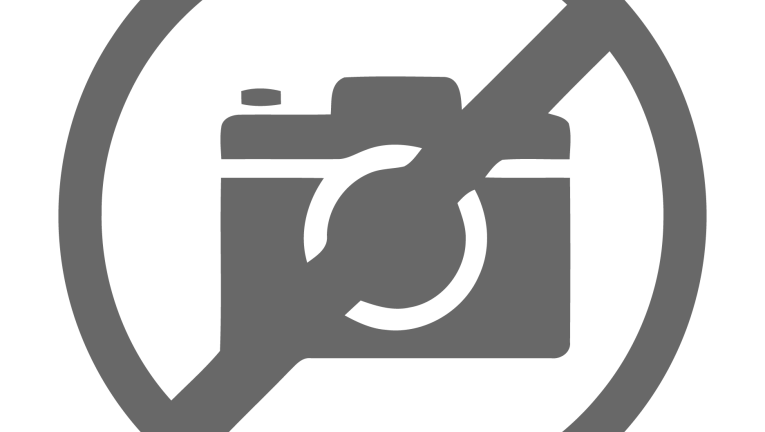
"Rub & buzz" is the term commonly used to describe any one of several possible manufacturing defects that cause undesirable noises to be emitted during speaker operation. The most common defect categories are rub, buzz, and air leaks. Rub-related noises occur when the speaker cone is off-center or canted and thus mechanically rubs when it moves to create sound. Buzz defects occur when loose particulate matter — chipped magnet material, bits of glue, etc. — are trapped in the gap between the speaker's voice coil and the cone. Air leaks are commonly perforations in the speaker surround, imperfectly sealed dust caps, or other unintentional gaps in the housing or cabinet.
As an audible defect in a speaker driver, or device incorporating a speaker, rub & buzz presents several challenges to device manufacturers. First off, it is a subjective issue, with little broad-based agreement on how much is too much – the noises created by a specific defect can be perceived very differently by different listeners. Compounding the issue is the level of distortion in a typical speaker is far greater, and more diverse, than in a typical electronic device and can mask these defects. This latter point means the standard audio measurements of Frequency Response and Distortion will only detect the most severe cases of rub & buzz.
These imperfections in a speaker can negatively impact a listener's perception of the speaker's quality, but those defects are not necessarily detectable by traditional audio measurements. To address this issue, several different rub & buzz detection methodologies have been developed within the industry: various approaches using high-pass tracking filters, distortion-oriented methods that focus only on high-order harmonics, and techniques applying human hearing-based algorithms to the distortion signal. While all these methods are applicable to rub & buzz detection, no single method has achieved uniform adoption in the industry.
With the release of APx500 software version 6.1, Audio Precision now offers multiple rub & buzz defect detection methodologies available to speaker designers and manufacturers:
• Rub & Buzz – Previously available in APx software, this method uses high-pass tracking filters to remove the fundamental signal and detect defects as excursions in the residual waveform’s crest factor or peak ratio.
• SoneTrac (new with v6.1) – A Bose-developed improvement to the aforementioned Rub & Buzz, this method filters the residual signal and ratios it to the RMS of the total signal to reduce the noisiness of the measurement result.
• High-Order Harmonic Distortion (HOHD; new with v6.1) – A classic method for rub & buzz detection, HOHD uses the THD (Total Harmonic Distortion) ratio but only of harmonics above the 10th, 10-35, 20-200, etc., which is a simple way to account for frequency masking effects.
• Rub & Buzz Loudness (new with v6.1) – Applies a psycho-acoustic loudness model to the residual signal to calculate the perceived level of the rub and buzz based on well-established models of the human perception of sound.
To support the addition of the HOHD and Rub & Buzz Loudness measurements, AP is introducing the Fast Sweep signal with APx500 release version 6.1. Fast Sweep, as its name implies, is an extremely fast stepped frequency sweep with no input or output ranging between steps, continuous transition between steps to minimize transient effects, and has a total sweep time that rivals the speed of a logarithmically-swept sine (chirp) signal. A few of the advantages of the Fast Sweep are the lack of transient ripples at low or high frequencies, the ability to sweep from low-to-high or high-to-low frequency, the support for measuring harmonics above the 20th, and precise control of the number of discrete points used in measurements.
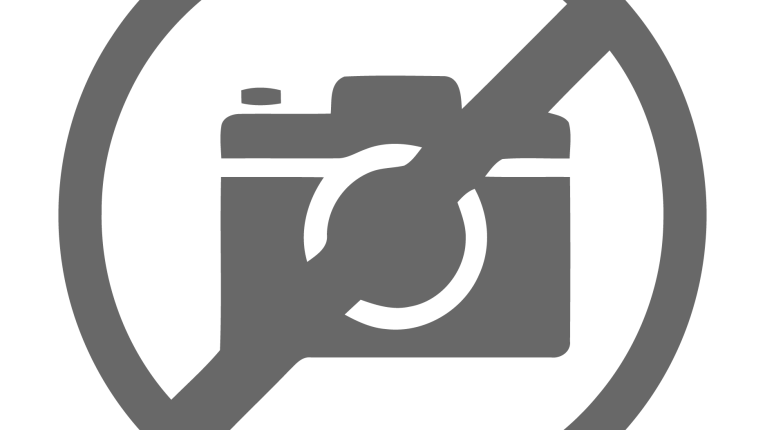
Additional New Features
In addition to the expanded selection of rub & buzz methods, as well as the new Fast Sweep stimulus, APx500 release version 6.1 now allows users to switch instantly between IEC and IEEE THD calculation modes for harmonic distortion results. Version 6.1 also adds the ability to normalize harmonic distortion results, addressing common measurement artifacts that occur when testing loudspeakers. Users can now also save all acquired waveform, impulse response, or cross-correlations results to .wav files, and this function can be included as a sequence step in automated measurement sequences.
"While version 6.1 is officially a minor release, and thus a free upgrade to any analyzer licensed for version 6.0, it delivers significant, new capabilities, especially for those involved in the design, manufacture, and test of speaker drivers and any product incorporating them," says Daniel Knighten, Audio Precision General Manager. "Simply put, APx audio measurement software now offers the broadest set of rub & buzz defect detection methodologies available."
With this latest release, new APx audio analyzers will begin shipping with version 6.1 software. Each new analyzer also includes one year of software maintenance, effectively licensing that instrument for APx version 7.0 when it is released (as well as any minor 6.x releases that occur prior to v7.0). Release v6.1 is a no-cost upgrade for any analyzer licensed for version 6.0 and users need only download v6.1 from AP.com.
Software upgrades are available for owners of Legacy APx analyzers, with options for upgrading from v4.x (or earlier) to v5.0, from v4.x to 6.0, and v5.0 to v6.0. Software maintenance contracts are available for instruments licensed for the current release (v6.0), entitling the analyzer to one, three, or five additional major software releases depending upon the contract purchased.
Release 6.1 is compatible with all analyzers in the APx500 Series, including the recently released APx517. An APx KeyBox is required to run v6.1 on Legacy APx analyzers. APx KeyBoxes already installed on Legacy analyzers (for v4.6 and 5.0), are also compatible with v6.1 and only require an updated license file once an upgrade is purchased.
www.ap.com
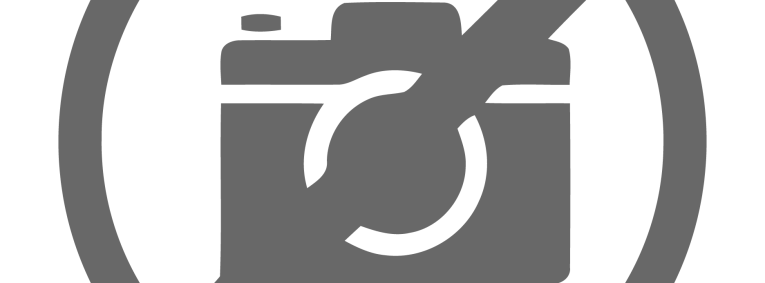