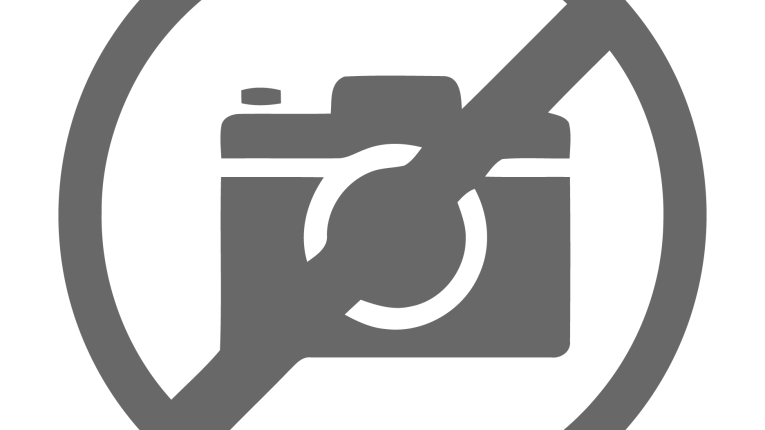
Let’s start with a confession, in many ways I have mixed feelings about the “green movement.” Another admission is this article is an updated report of the one we published back in 2015 in Voice Coil’s sister magazine, audioXpress.
When Eco-Friendly Ideas Go Wrong
Of course, it makes good sense to conserve resources and not pollute. It is also good practice to maximize efficiency in product design. Yet there are aspects of “eco-friendly” initiatives that are actually wasteful and counterproductive. For example, recycling glass made from cheap and plentiful raw materials (limestone, sand, and salt cake) costs more and uses more energy for handling and producing than making new glass bottles. The dirty secret is that after you dutifully drag your bottles back to the supermarket in most localities they just dump them in the garbage.
Any good idea can take a wrong turn, resulting in misguided efforts at productivity. Consider the infamous USSR shoe factory in the 1960s that made only left shoes because their output would be higher than producing matching pairs. Great for Russian jokes but some fool running the show back then was serious. Planned obsolescence and some disposable products are anything but green, at least from my perspective. Perhaps the most irresponsible example was Delphi’s biodegradable wiring harness used by Mercedes in the mid-1990s. Potentially deadly over time, not to mention the Mercedes models with these crappy harnesses are unsellable. The plastic insulation flaked off on the main engine harness, throttle body harness, starter/alternator harness, and Mass Air Flow meter harness. On the other hand, biodegradable materials are obviously fine for disposable baby diapers, and also sane for product packaging, smartphone cases, plastic cups, and other shorter-term stuff.
Quality products should probably not be biodegradable. Intentionally designing in UV degradation is not a good approach and product stability and appearance will suffer. One aspect that is not apparent is serviceability. If a product can be repaired, it would not be tossed so quickly and therefore not need to be replaced. A positive example is a headphone in which the cable has connectors on both ends. In this case a cable can be replaced by the user so the headset does not need to be tossed or sent to a repair shop when the cable becomes intermittent.
Disposable Products
Let’s look at a product category that is “disposable” (e.g., the typical in-box earphone fails within the first year of use). Intermittent cables and connectors, worn foam eartips, and an inadvertent visit to the washer/dryer are some of the causes of premature failure. Some popular Bluetooth earphones cannot retain stable operation if you break into a sweat at the gym, let alone encounter a downpour.
Contrast this with a headphone or earphone that can be worn for years, looking and feeling good, and maintaining its sound quality. This is true high value, and these qualities are inherently green. One example that comes to mind that was never intended as a “green” product — was the iconic Bang & Olufsen earphone. This product has a classic “design” (rather than short-term “fashion”), retains its appearance without discoloration or fading, has quality cables and connectors that last for years, and the value provided to the owner is excellent. While the purchase price was expensive, this earphone will outlast a half-dozen cheap earphones for about the same cost of ownership. Meanwhile, the sound quality, comfort, and style are superior.
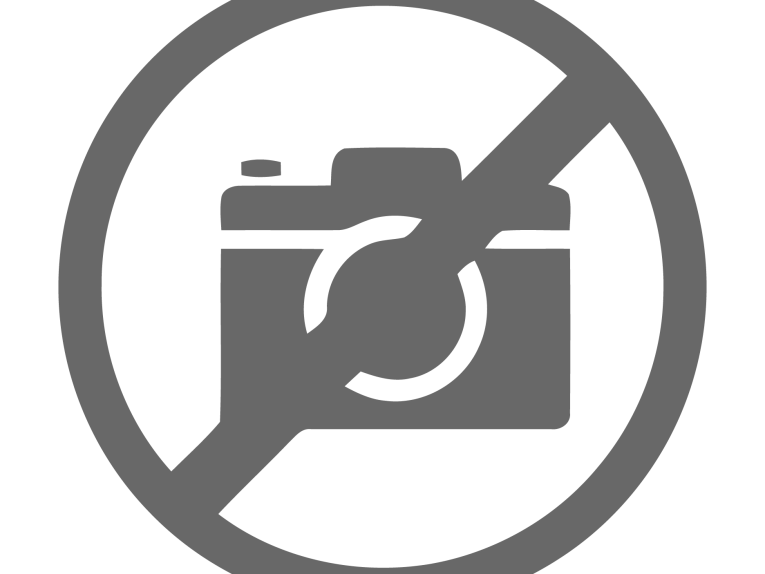
If you are still reading, then you might ask what my two cents are on criteria for genuinely sustainable product design? Long-term stability, bioplastics, recycled content, and end-of-life recyclable attributes are all aspects of a truly green product, for the appropriate parts and application. The audio industry’s self-imposed destruction of the surround receiver market through the constant obsolesce of existing models long before their functionality was compromised; constantly changing surround sound standards, HDMI, and other aspects made customers feel bad about their investment in a quality sound system over these superfluous parameters. I think that a conscionable green design philosophy contributes real value to the total integration of “good citizen” eco-friendly materials and processes and long, useful life.
What about the paper in speaker cones and green issues? When you consider the millions of people who toss out the Sunday NY Times every week — each a couple of pounds of cellulose “newsprint” — this is a real consideration and does add up. But 10 grams of speaker cone paper used for 10 years is not really a consideration. In any case, there is a sustainability scale—we have already run out of dinosaurs that have turned into oil millenniums ago. Trees grow less slowly, and bamboo sprouts even when you don’t want it to. So adding cellulose fibers to plastic resins is a notch up in sustainability goodness.
Speaker performance can be improved by adding bast family fibers (such as banana leaf and hemp fiber) and other renewable organic fibers. Fostex and Dai-Ichi are known for their use of banana leaf fibers due to the high tensile strength in their high-quality cones. Banana fiber is extracted from the bark and leaves of the banana plant. The appearance of banana fiber is similar to bamboo and ramie fiber. Characteristics include high strength, small elongation, and light weight to strength ratio. Paper and fabrics from banana fibers were first used in the 13th century in Japan. Renewable bio-fibers can be defined as resources that re-grow in less time than trees. Banana leaf, pineapple leaf, and bamboo also grow rapidly. In Asia, the only attention bamboo typically gets is to cut it back, not intentionally cultivate it. Bamboo is edible and is not uncommon in Asian dishes, but has little nutritional value, so if you eat your bamboo fiber speaker cones, those will be empty calories.
Petroleum-derived resins can be partially replaced with processed grain fibers and processed sugar cane (ultra-fast growth cycle and strong fiber). The application of food starches as a binder is not new — most of us made papier-mâché with newspaper as kids — which is an application of food starch as a paste. This process is more applicable to cones fabricated by paper processes.
Aside from substituting various other organic fibers for wood (cellulose) in the speaker cone paper-making process, organic fillers can also be used for plastic cones.
Highly filled bioplastics are a viable alternative to conventional poly cones. An example is wood flour or soy flour compounded with polypropylene (PP). “Flour” here is essentially a finely milled sawdust typically with a sizing (coating) coupling agent to improve consolidation with the main ingredients, such as PP resin. The key issue is not to replace the existing PP fillers that are readily available and unlimited supply of inorganic mica, talc, or glass, but rather to reduce the petroleum-based polypropylene content. For poly cones, the PP is compounded with the fillers along with some re-grind. The re-grind is beneficial as it tends to have been crystallized in previous processes and increases stiffness/higher Young’s modulus to the composite extruded sheets produced.
Wood flour (and soy flour) can be compounded with acrylonitrile butadiene styrene (ABS), polycarbonate (PC), or PP into injection-molding pellets. The cheaper grades use larger wood particles and result in a textured surface. The very fine stuff does not change the surface significantly and has fewer issues with flow for injection-molded cones. A side issue is the moisture re-gain content of the wood and soy flour. For most applications, the flour must be kept in a humidity-controlled storage area, although some fabricators have used the moisture to cavitate producing a “foaming” effect to occur, providing lower-density, same-weight cones with higher strength. The price of soy and wood flour is cheap — 30 cents to under $1 per pound depending on the type of wood and particle size. Compounding with too much flour filler results in fractures and cracking and overall degradation of impact strength.
Development of bioplastics has been driven by automotive interiors as stick-slip creak noise when the car body flexes can be “hushed,” and reduce weight to meet higher Corporate Average Fuel Economy (CAFE) regulations, designed to improve the average fuel economy of cars, as well as the sustainability benefits in marketing a greener vehicle.
Consumer Products
Many consumer products, from cell phone cases to the “fake” wood trim in cars, contain wood flour compounded with plastics (or just cast wood solids with a binder). The cosmetic “skin” typically are films comprised of layers of photographic images of a wood pattern. While this may sound tacky, automotive interior engineers do this because it is a more stable solution for car trim than solid finished wood. Bioplastics are a major component of many car interiors. Another green angle is surface finish coatings from recycled chemicals.
Eastman, which you may remember as Eastman Kodak before the company sold that division, has a strong consumer electronics sustainability program (eastman.eco). Its Tritan is becoming a popular alternative to Nylon 12 (EMS 90) in headbands in Sony, Skull Candy, and others — offering less creep and plastic fatigue, and is BPA-free, which is good for products that are in contact with the skin.
The low creep minimizes the clamping force fading, which would reducing the low-end response and increase noise leakage (not what you want from your ANC headphone in the last hours of a long flight). Now Eastman has introduced Tritan Renew, which contains the durability and performance with up to 50% certified recycled content.
Eastman’s new recycling technology transforms single-use waste into basic building blocks that are then used to make durable, high-performance, skin-contact materials. Not regrind but a (molecular) chemical polyester renewal process that offsets the use of fossil fuels and lowers greenhouse gas emissions.
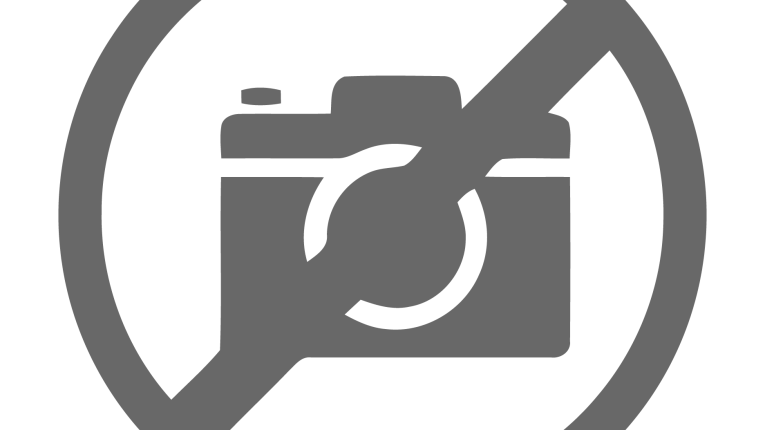
Waste plastics are broken down into molecular building blocks that can be reused and made into new products, such as the Tritan Renew (Figure 1). The constant characteristic of virgin materials is a reduction of the amount of plastic going into the waste stream without compromising function or aesthetics. That certainly fits Eastman’s motto “Be part of the circular solution to help keep plastic waste out of the environment and the dinosaurs in the ground” (Figure 2).
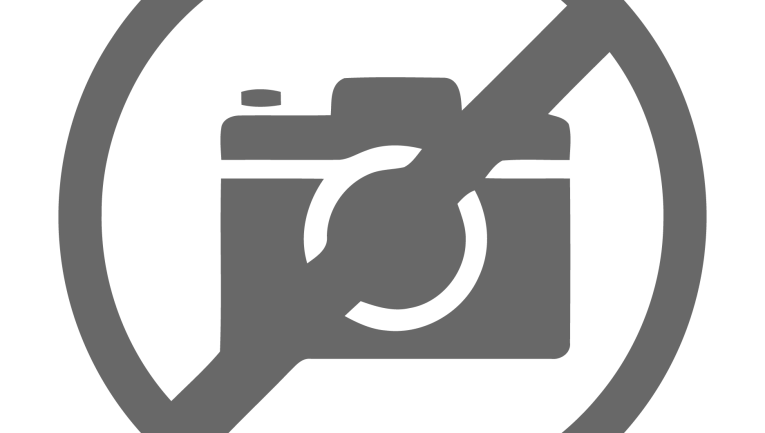
We touched upon reducing the petroleum derived content of plastic resins with wood (cellulose), and Eastman was a pioneer in their cellulose plastics for film photos. This head-start enabled Eastman’s Treva, which has a high cellulose content and is also available as part of its recycled resins program.
There are quite a few Asian vendors that offer their own versions with recycled content, but variations in material characteristics tend to be extremely wide. In past years, there were PC based on regrind PC from recycled CDs and DVDs, but of course this feedstock has faded away. Depending on the recipe, this CD regrind process was used for applications from shoes to headphone earcups.
Covestro (the king of PC resins) is returning plastic waste through chemical recycling and also with regrind processes (Figure 3). New capacity will boost availability of Makrolon R and Bayblend R, which contain up to 75% recycled content. And, it is ramping up to establish 60,000 tons/year of mechanical recycling (MCR) for the growing demand for post-consumer-recycled (PCR) materials to be used primarily for the compounding step in the manufacture of electrical and electronic products, automotive applications, and consumer goods. Covestro is also repurposing an existing production line in Thailand for recycled PC production.
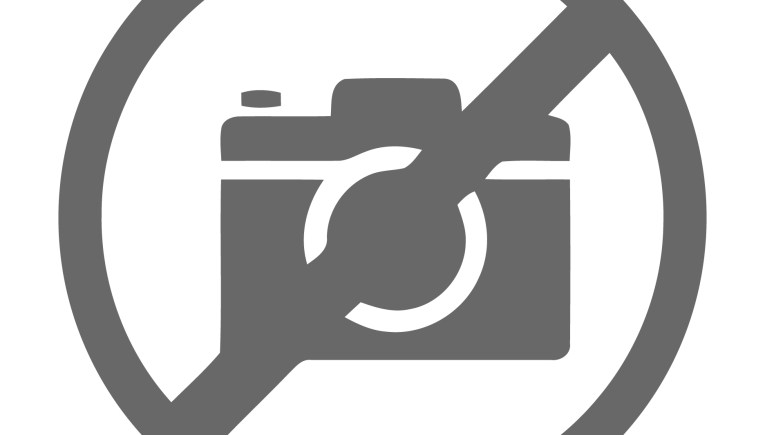
Notable, but much smaller innovators in the sustainable materials field should not be bypassed. Upm Biofore (www.upm.com) is bringing to market wood-based bio-chemicals for replacing fossil-based raw materials in various applications, such as textiles, PET bottles, packaging, pharmaceuticals, detergents, rubbers, and resins.
Woodly’s (www.woodly.com) carbon-neutral and wood-based plastic has been developed from its material processing innovations and extensive recycling, resulting in a complete de-coupling of all plastics from fossil-based feedstocks. Woodly’s product is an entirely new type of plastic based on softwood cellulose and it mimics the best qualities of traditional fossil-based plastics.
Now, let’s get to unique but very real paths to sustainability, approached from a different perspective but from a very familiar and respected audio company.
Dr. Wolfgang Klippel, with the Klippel Controlled Sound (KCS) adaptive control circuit enables speaker systems with reduced materials and weight with reduced distortion, protects the transducer against overload, and copes with time-varying properties of the suspension by using out-of-the-box and new degrees of freedom provided by DSP for exploiting a nonlinear motor topology, a soft suspension, and modal vibration of the diaphragm, panel and in the acoustical systems. By the way, speaking of sustainability, congratulations to Klippel for reaching its 25-year anniversary!
Regulations
And finally, a look at regulations… The days of voluntarily being a good citizen designer are over and Big Brother has taken the lead. Today, we have RoHS and more recently REACH, not to mention Energy Star and other looming regulatory standards.
Reduction of Hazardous Substances (RoHS): Complete RoHS compliance is the law, and penalties are excessive for non-compliance of even traces of restricted or hazardous substances. Loudspeakers have presented a couple of issues, such as cadmium plating, which is now gone from your plating options of the magnet steel. Beryllium diaphragms may sound good, and are allowed, but have end-of-life requirements under the REACH regulations.
REACH stands for Registration, Evaluation, Authorization, and Restriction of Chemical Substances. It is a Euro standard for what to do with the product at the end of its life and is a big issue. The general concept is component parts are labeled so they can be separated into like materials for recycling. More serious aspects are what to do with toxic materials when it is time to toss the product. Nasty stuff includes mercury in batteries, the lead in ceramic tweeters, the beryllium in high-end speaker diaphragms, boron in phonograph cartridge shanks, and the cadmium in the magnetic structure plating in your old speakers.
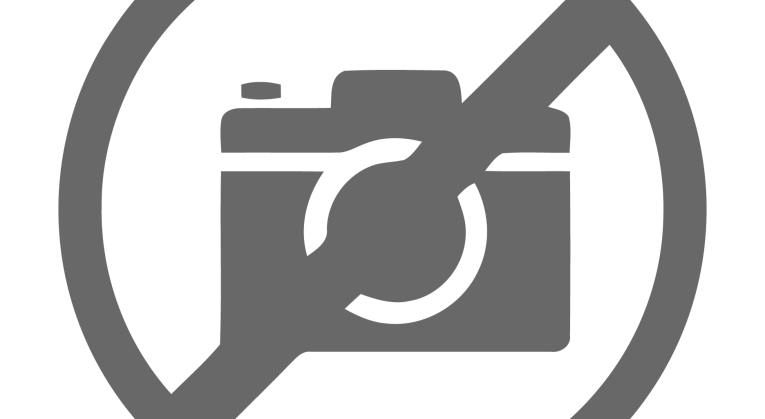
Piezo ceramic bimorph speakers have mostly left the scene, and it was primarily the lead additive needed for good sensitivity mixed into the ceramics put nail in their coffin. High-stability piezoelectric ceramics, specifically PZT, are composed of lead zirconium titanate. You may remember CTS bought Motorola’s Component Products Division (CPD), which included a ceramic tweeter group a while back and then closed that product line down. If you wonder what innovations CTS is up to now, they are the guys that made those sticking brake pedal assemblies for Toyota a while back.
Energy Star and Department of Energy: While flat screen TVs are now coming under government efficiency regulations, and Best Buy along with the other big retail chains are requiring Energy Star ratings and standby modes (which will require switching power supplies in receivers), how far behind can speaker efficiency ratings be? Wait until the consumer finds out our bookshelf speakers are about 1% efficient!
Good Citizen Factory and Conflict Materials: All this attention to the Earth would be senseless if there is a lack of concern for its inhabitants. A “good factory” means that it has clean working conditions, good worker treatment, and training and education for factory workers. This aspect received a lot of attention when stressed-out Foxconn workers started jumping from the factory roofs in 2010. More recently, when Chinese government lockdowns at one of the Foxconn factories became untenable for both the company and the workers, a more enlightened path was found when Foxconn paid workers to head back to their families’ towns.
More insidious are conflict materials. You may have heard the term “blood diamonds,” which refers to diamonds mined in a war zone and sold to finance an insurgency or a warlord’s activity, usually in Africa. The Dodd-Frank Wall Street Reform and Protection Act requires public companies to report conflict material importing and use such as tin, gold, tungsten, and so on from areas such as the Democratic Republic of the Congo (which you may know as the Belgian Congo or Zaire, depending on when you went to school).
While this issue seems alien to the speaker industry, we have a long history of conflict materials. Back in the 1970s, the loudspeaker industry shifted away from alnico to ceramic magnets due to the economic sanctions on mined metals, such as nickel due to race and political instability issues in Rhodesia (now the Republic of Zimbabwe).
I think this article captures some of the challenges and paradoxes of eco-friendly good citizen product engineering strategies. But there are also some difficulties. I must say that I have had clients tell me that the last thing the dealer wants is a customer walking away with a headphone that will look good and work well for the next decade.
Audio history footnotes are filled with cautionary tales about Sansui, Nikko, Kenwood, Sherwood, Fisher, and a dozen other brands that built receivers that worked forever and then discovered they had designed themselves out of future business. Not every customer wants a “classic and iconic” look, at least not all the time. Sometimes a purple fur earphone headband might be just the thing you or your kid wants. VC
This article was originally published in Voice Coil, March 2023.