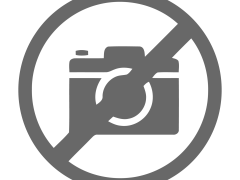
The dirty secret is that after you drag your bottles back to the supermarket in most localities they just dump them in the garbage.
I am tired of having my groceries splatter on the street because the recycled brown paper bags ripped apart due to poor tear strength caused by the lack of longer fibers. These days the grocery packers know how inadequate recycled paper bags are and double- and triple-bag—a net loss over using just one new quality (unrecycled) paper bag.
Any good idea can take a wrong turn, resulting in misguided efforts at productivity, such as the infamous USSR shoe factory in the 1960s that made only left shoes because their output would be higher than making matching pairs. Great for Russian jokes but some fool running the show was serious. Perhaps that factory manager has joined the board of directors of the green movement.
While I have been pondering all this for years, what triggered this article (rant) were some comments I heard at the ALMA China Symposium. I was on a panel focusing on profitability and providing value and heard many good ideas. But one approach suggested that with the application of sophisticated design simulations, cheap materials could be used for achieving good performance but shortened life. The product would last long enough (perhaps a couple of years) that it would be too late for the customer to return it to the store. Somehow this approach was considered “green.” I take exception to this, because planned obsolescence and disposable products are anything but green, at least from my perspective.
If you are still reading, then you might ask what are my two cents on criteria for sustainable product design? These include bioplastics, sustainable, biodegradable, or end of life recyclable attributes are all aspects of a truly green product. I think that a conscionable green design philosophy focuses on the total integration of “good citizen” eco-friendly materials and processes and long, useful life.
Let’s look at a product category that is “disposable”; for example, the typical earphone fails within the first year of use. Intermittent cables and connectors, worn foam eartips, and an inadvertent visit to the clothes washer/dryer are some of the causes of premature failure. Some popular earphones cannot retain stable operation if you break into a sweat at the gym, let alone encounter a downpour.
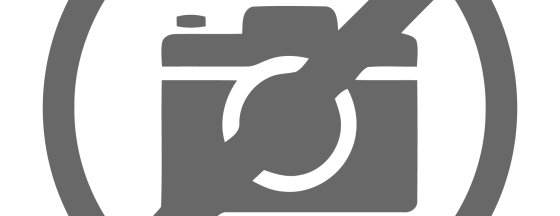
Contrast this with a headphone or earphone that can be worn for years, looking and feeling good, and maintaining its sound quality. This is true high value, and these qualities are inherently green. One example that comes to mind was never intended as a “green” product — the iconic B&O earphone (www.bang-olufsen.com). This product has a classic “design” (rather than short-term “fashion”), retains its appearance without discoloration or fading, has quality cables and connectors that last for years, and the value provided to the owner is excellent (Photo 1). While the purchase price is stiff, this earphone will outlast a half dozen cheap earphones for about the same cost of ownership. Meanwhile, the sound quality, comfort, and style are superior.
What about the paper in speaker cones and green issues? When you consider the millions of people who toss out the Sunday NY Times every week — each a couple of pounds of cellulose “newsprint” — this is a real consideration and does add up. But 10 grams of speaker cone paper used for 10 years is not a consideration. Let’s get real.
Yet audio performance can be improved by adding bast family fibers (such as banana leaf and hemp fiber) and other renewable organic fibers. Fostex (Photo 2) and Dai-Ichi are known for their use of banana leaf fibers due to the high tensile strength in their high-quality cones. Banana fiber is extracted from the bark and leaves of the banana plant. The appearance of banana fiber is similar to bamboo and ramie fiber. Characteristics include high strength, small elongation, and light weight to strength ratio. Paper and fabrics from banana fibers were first used in the 13th century in Japan.
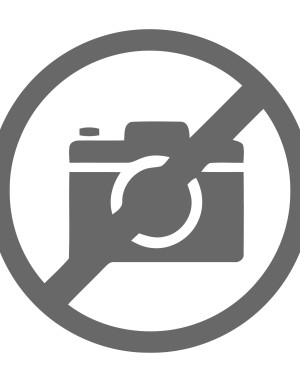
Although hemp and other bast family fibers have been used as a secret sauce in speaker cone formulations from back in the days of Rudy Bozack’s audiophile loudspeakers in the 1960s, more recently, hemp cones are now being promoted as the “next thing.”
Renewable bio-fibers can be defined as resources that re-grow in less time than trees. I mentioned banana leaf and pineapple leaf, and bamboo also grows rapidly. In Asia the only attention bamboo typically gets is to cut it back, not intentionally cultivate it. Bamboo is edible and is not uncommon in Asian dishes, but has little nutritional value, so if you eat your bamboo fiber speaker cones, those will be empty calories.
Some Green Fillers
Petroleum resins can be partially replaced with processed grain fibers and processed sugar cane (ultra-fast growth cycle and strong fiber). The application of organic (food) starches as a binder is not new—most of us made papier-mâché with newspaper as kids—which is an application of food starch as a paste. This process is more applicable to cones fabricated by paper processes.
Aside from substituting various other organic fibers for wood (cellulose) in the speaker cone paper-making process, organic fillers can also be used for plastic cones.
Specifically highly filled bioplastics are a viable alternative to conventional poly cones. An example is wood flour or soy flour and PP (polypropylene). “Flour” here is essentially a finely milled sawdust typically with a sizing (coating) coupling agent to improve consolidation with the main ingredients such as polypropylene resin. The key issue is not to replace the existing PP fillers that are readily available and unlimited supply of inorganic mica, talc, or glass, but rather to reduce the petroleum-based polypropylene content.
For poly cones, polypropylene is compounded with the fillers along with some re-grind using a compounder.
Wood flour (and soy flour) can be compounded with ABS, PC, or PP into pellets. The cheaper grades use larger wood particles and result in a textured surface; the very fine stuff does not change the surface significantly and has fewer issues with flow for injection-molded cones. A side issue is the moisture content of the wood and soy flour. For most applications the flour must be kept in a humidity-controlled storage area, although some fabricators have used the moisture to cavitate producing a “foaming” effect to occur, providing lower-density, same-weight cones with higher strength. The price of soy and wood flours is cheap — 30 cents to under $1 per pound depending on the type of wood and particle size. Compounding with too much flour fillers results in fractures and cracking.
Many consumer products, from cellphone cases to the “fake” wood trim in cars, contain wood flour compounded with plastics. The “skin” may have a photographic image of a wood pattern. While this may sound tacky, Mercedes does this because it is a more stable solution for car trim than solid wood. Bioplastics are a major component of many Euro car interiors. Another green angle is surface finish coatings from recycled chemicals.
I have noticed wood earphones and headphones and bamboo formed parts have potential here for the earcup and earphone exterior shell. Bamboo acoustics are superior to plastic parts and have a distinctive bio-friendly appearance.
Another interesting path is regrind PC (polycarbonate) from recycled CDs and DVDs. Depending on the recipe, this process can be used for speaker cones, headphone exterior shells, and earcup baffles. Wood flour additives commercially developed for this application provide the damping characteristics needed for acoustical parts.
But the days of voluntarily being a good citizen designer are over and Big Brother has taken the lead. Today we have RoHS and more recently REACH, not to mention Energy Star and other looming regulatory standards.
RoHS: Reduction of Hazardous Substances
Complete RoHS compliance is the law, and penalties are excessive for non-compliance of even traces of restricted or hazardous substances. Loudspeakers present a couple of issues, such as cadmium plating which is now gone from your plating options of the magnet steel. Beryllium diaphragms may sound good, and are allowed, but have REACH (end of life) requirements (see REACH below).
Maybe the fake beryllium diaphragms made of Ti are not such a bad idea.
While piezo speakers have mostly left the scene already, the lead additive needed for good sensitivity mixed into the ceramics has put the nail in their coffin. High-stability piezoelectric ceramics, specifically PZT, are composed of lead zirconium titanate. You may remember CTS bought Motorola’s ceramic tweeter group a while back and then closed that product line down. If you wonder what innovations CTS is up to now, they are the guys that made those sticking brake pedal assemblies for Toyota.
REACH: Registration, Evaluation, Authorization and Restriction of Chemical Substances
A Euro standard for what to do with the product at the end of its life is a big issue. The general concept is component parts are labeled so they can be separated into like materials for recycling. More serious aspects are what to do with toxic materials when it is time to toss the product. Nasty stuff includes mercury in batteries, the lead in ceramic tweeters, the beryllium in high-end speaker diaphragms, boron in phonograph cartridge shanks, or the cadmium in the magnetic structure plating in your old speakers.
Energy Star and Department of Energy
While flat screen TVs are now coming under government efficiency regulations, and Best Buy along with the other big retail chains are requiring energy star ratings and standby modes (which will require switching power supplies in receivers), how far behind can speaker efficiency ratings be? Wait until the consumer finds out our bookshelf speakers are about 1% efficient!
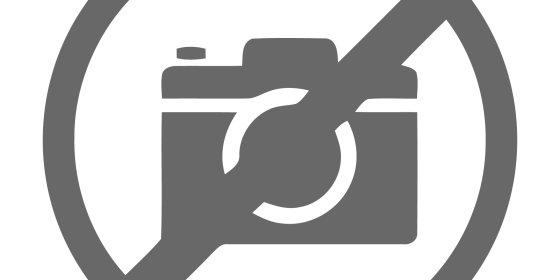
Biodegradable
Quality products should probably not be biodegradable (Photo 3). Intentionally designing in UV degradation is not a good approach and product stability and appearance will suffer. One aspect that is not apparent is serviceability. If a product can be repaired it would not be tossed so quickly and therefore not need to be replaced. An example is a headphone in which the connectors on both ends of the cable could be removed and replaced so the headset does not need to be tossed when the cable becomes intermittent.
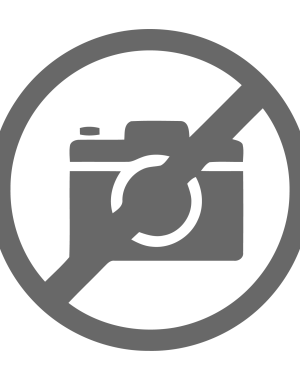
recycled and tamper resistant.
Eco-Friendly Packaging
Green packaging for your product can be a combination of recycled materials and minimizing the volume of packaging materials. Aside from recycled paper packaging, you might consider bamboo paper/cardboard materials. Some retailer chains cannot accept small packaging for high-value goods because they would be too easy to shoplift. One unique approach is from giant MWV (www.meadwestvaco.com). They offer their Natralock solution (Photo 4), a combination of recycled materials and tamper resistance (tear resistance) for high value items such as headsets, memory sticks, and so on.
Good Citizen Factory and Conflict Materials
All this attention to the earth would be senseless if there is a lack of concern for its inhabitants. A “good factory” means that it has clean working conditions, good worker treatment, and training and education for factory workers. This aspect received a lot of attention when stressed-out Foxconn workers started jumping from the factory roofs like lemmings in 2010.
More insidious are conflict materials. You may have heard the term “blood diamonds,” which refers to diamonds mined in a war zone and sold to finance an insurgency or a warlord’s activity, usually in Africa. Last July the Dodd-Frank Wall Street Reform and Protection Act was signed into law and requires public companies to report conflict material importing and use such as tin, gold, tungsten, and so on from areas such as the Democratic Republic of the Congo (which you may know as the Belgian Congo or Zaire, depending on when you went to school). While this issue seems alien to the speaker industry, we have a long history of conflict materials. Back in the 1970s the loudspeaker industry shifted away from alnico to ceramic magnets due to the economic sanctions on mined metals such as nickel due to racial issues in Rhodesia (now the Republic of Zimbabwe).
I think the above captures a balanced and comprehensive approach to eco-friendly good citizen product engineering strategy. But there are some flies in the ointment. I must say that I have had clients tell me that the last thing the dealer wants is a customer walking away with a headphone that will look good and work well for the next decade. Audio history footnotes such as Sansui, Nikko, Technics, Kenwood, and a dozen other Japanese brands built receivers that worked forever, only to find they designed out their future business. Not every customer wants a “classic and iconic” look, at least not all the time. Sometimes a purple fur earphone headband may just be what you’re looking for.
Originally published in Voice Coil, February 2011