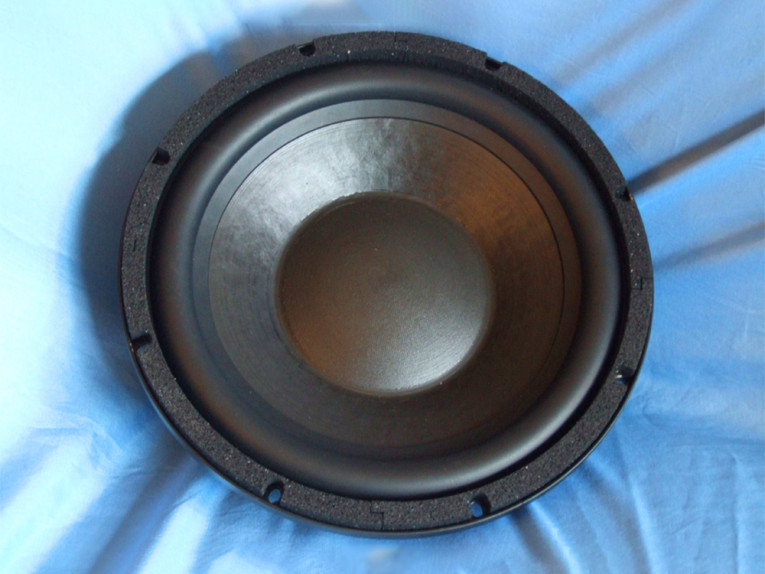

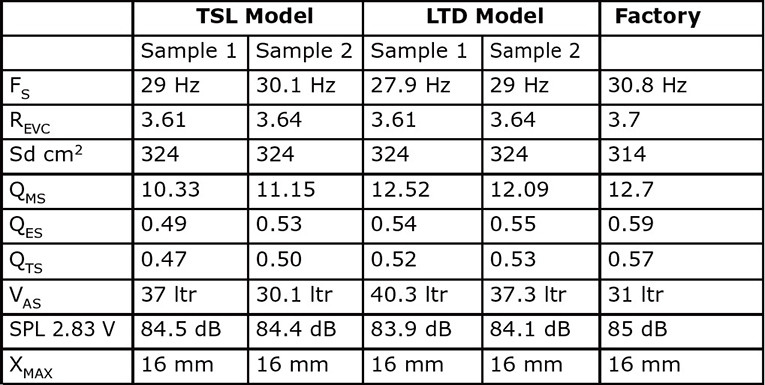
Wavecor’s SW275BD01, which is the 4 Ω version of the subwoofer (the SW275BD02 is the 8 Ω version), has a well-appointed feature set that includes a proprietary cast eight-spoke (four twin spokes) cast aluminum frame that has minimal reflection surfaces and has a completely open 1.5” deep space below the spider mounting shelf. Other features include the incorporation of a very stiff black mica/paper composite cone, further stiffened by a 4” convex black hard paper dust cap. Suspension is provided by a FEA optimized low-loss (high Qm) NBR surround plus dual 6” diameter black flat conex spiders (dampers).
All this is driven by a 65 mm diameter (2.5”) voice coil wound with round wire on a black fiber glass non-conducting former. The motor system powering the cone assembly utilizes three 18 mm thick by 135 mm diameter ferrite magnet sandwiched between a black plated 7 mm thick front plate and a black plated 10 mm thick T-yoke that incorporates an 18 mm diameter dual-flared pole vent surrounded by eight 10 mm diameter peripheral vents. This format drives more air out the gap area and across the front plate below the spider mounting shelf for enhanced cooling of the motor system. Additional cooling is accomplished with eight 12 mm diameter vents in the cone below the dust cap. Along with Wavecor’s balanced drive technology (a shaped extended pole piece), the SW275BD01 also incorporates an aluminum shorting ring (Faraday shield) that reduces distortion caused by eddy currents. Last, the braided voice coil lead wires terminate to a pair of gold terminals.
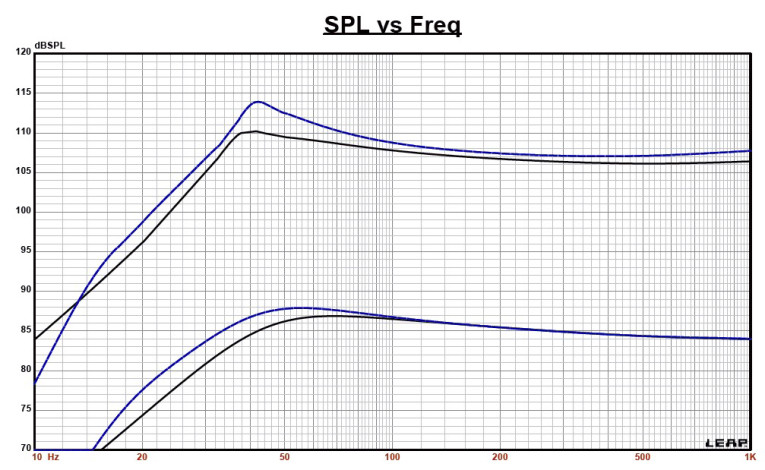


I began characterizing the new SW275BD01 subwoofer using the LinearX LMS analyzer and VIBox to measure both voltage and admittance (current). Sweeps were generated in free-air at 0.3V, 1V, 3V, 6V, 10V, 15V, 20V, and 30V. I used the measured Mmd that was provided by Wavecor (an actual physical cone assembly measurement with 50% of the surround and spider removed) rather than a single 1 V added (delta) mass measurement. It should also be noted that this multi-voltage parameter test procedure includes heating the voice coil between sweeps for progressively longer periods to simulate operating temperatures at that voltage level (raising the temperature to the first and second time constants).
I processed the 16 sine wave sweeps for each woofer and divided the voltage curves by the current curves to produce impedance curves. I generated the phase curves using the LEAP phase calculation routine, after which I copy/pasted the impedance magnitude and phase curves plus the associated voltage curves into the LEAP 5 Enclosure Shop software’s Guide Curve library. I used this data to calculate parameters using the LEAP 5 LTD transducer model. Because most manufacturing data is produced using either a standard transducer model or in many cases the LEAP 4 TSL model, I also generated LEAP 4 TSL model parameters using the 1 V free-air that can also be compared with the manufacturer’s data. Figure 1 shows the 1 V free-air impedance plot. Table 1 compares the LEAP 5 LTD and LEAP 4 TSL Thiele-Small (T-S) parameter sets for the Wavecor SW275BD01 driver samples along with the Wavecor factory data.
From the comparative data shown in Table 1, all four parameter sets for the two samples were reasonably similar and correlated well with the factory data. Following my normal Test Bench testing protocol, I used the Sample 1 LEAP 5 LTD parameters and set up two computer box simulations—one in a 1.25 ft3 Butterworth-type sealed enclosure with 50% fill material (fiberglass) and for the second example, a Chebychev/Butterworth vented alignment in a 1.5 ft3 box with 15% fill material and tuned to 22 Hz.
Figure 2 gives the results for the SW275BD01 in the sealed and vented enclosures at 2.83 V and at a voltage level sufficiently high enough to increase cone excursion to Xmax + 15% (18.4 mm for SW275BD01). This resulted in a F3 of 38 Hz (-6 dB = 30 Hz) with a Qtc = 0.68 for the 1.25 ft3 closed box and a -3 dB for the vented simulation of 33 Hz (-6 dB = 26 Hz). Increasing the voltage input to the simulations until the approximate Xmax +15% maximum linear cone excursion point was reached resulted in 110 dB at 47 V for the sealed enclosure simulation and 114 dB with a 62 V input level for the larger passive radiator box. Figure 3 shows the 2.83 V group delay curves. Figure 4 shows the 47 V/62 V excursion curves.
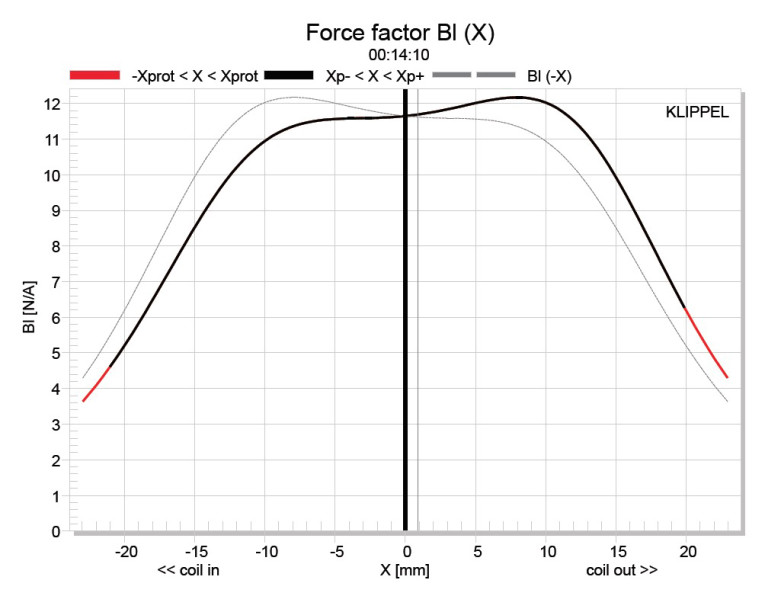
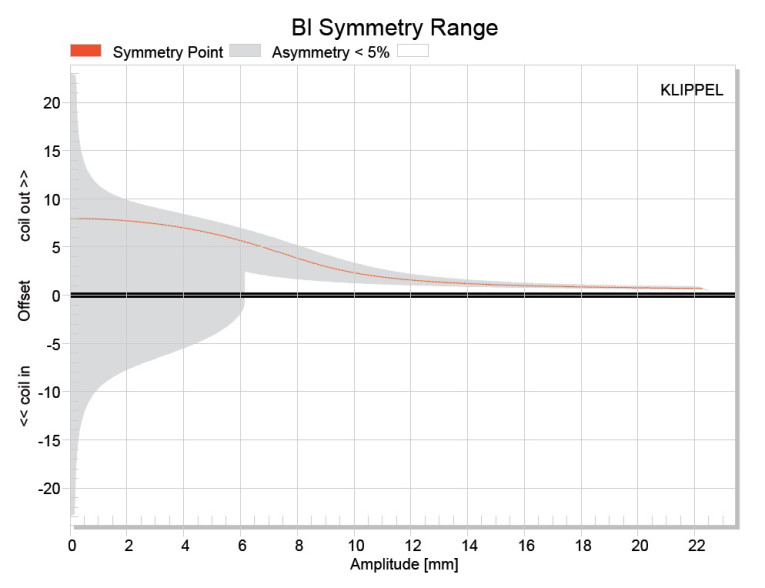
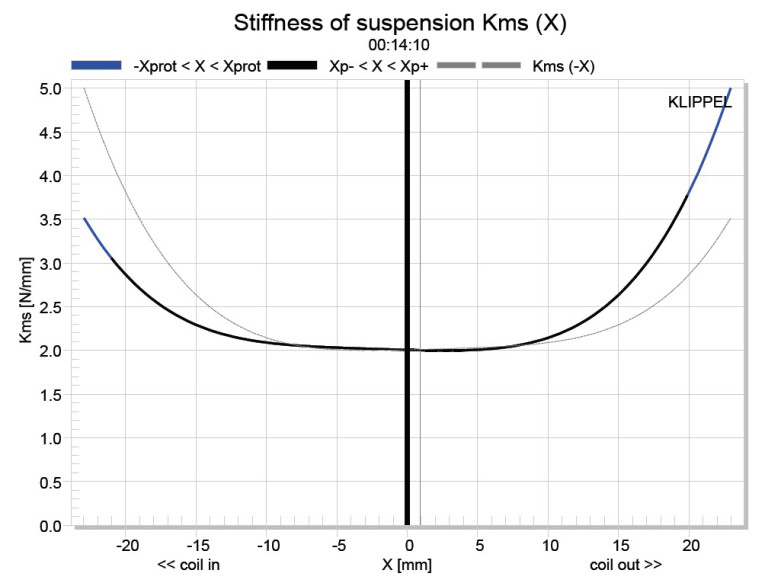

Klippel analysis for the SW275BD01 produced the Klippel data graphs shown in Figures 5-8. Our analyzer is provided courtesy of Klippel GmbH and the testing, as usual, was performed by Patrick Turnmire, Redrock Acoustics. (Please note, if you do not own a Klippel analyzer and would like to generate this type of data on any transducer, Redrock Acoustics can provide Klippel analysis).
The Bl(X) curve for SW275BD01 seen in Figure 5 is rather broad and mostly symmetrical typical (with a degree of “tilt”) of a driver with a relatively high Xmax. The Bl symmetry curve found in Figure 6 shows a 1.6 mm Bl coil-out (forward) offset once you reach an area of reasonable certainty at 12 mm excursion, decreasing to about 1.24 mm forward offset at the physical 16 mm Xmax position and beyond.
Figure 7 and Figure 8 show the Kms(X) and Kms symmetry curves. Like the Bl curve, the Kms stiffness of compliance curve shown in Figure 7 is moderately symmetrical, with some rearward offset once the analyzer gets to a position of reasonable certainty. The Kms symmetry range curve shown in Figure 8 exhibits a minor 1.2 mm coil-in (rearward) offset at a region of high certainty (12 mm) that increases slightly to 1.6 mm by the 16 mm physical Xmax of the SW275BD01. Displacement limiting numbers calculated by the Klippel analyzer for the SW275BD01 using the subwoofer criteria for Bl was XBl at 70% (Bl dropping to 70% of its maximum value) equal to 15.5 mm for the prescribed 20% distortion level (the criterion for subwoofers). For the compliance, XC at 50% Cms minimum was greater than 20 mm, which means that for SW275BD01, the Bl is the more limiting factor for getting to the 20% distortion level, however, both numbers were greater than the near or greater than the driver’s 16 mm physical Xmax. Figure 9 gives the inductance curve Le(X) for this transducer. Motor inductance will typically increase in the rear direction from the zero rest position as the voice coil covers more of pole, which is what you see in the graph. It’s easy to see the benefit of the aluminum shorting ring with inductance only varying a maximum 0.10 mH in either direction, which is a minimal inductance change for such a large motor and certainly good inductive performance.
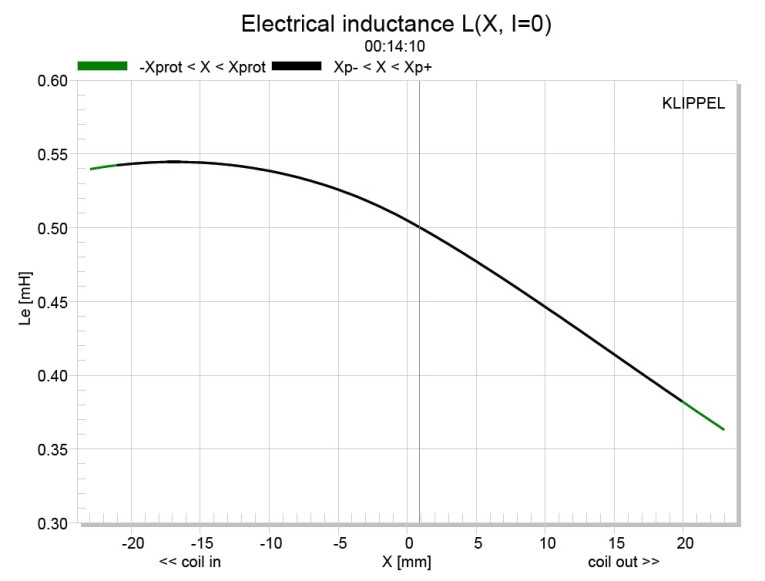
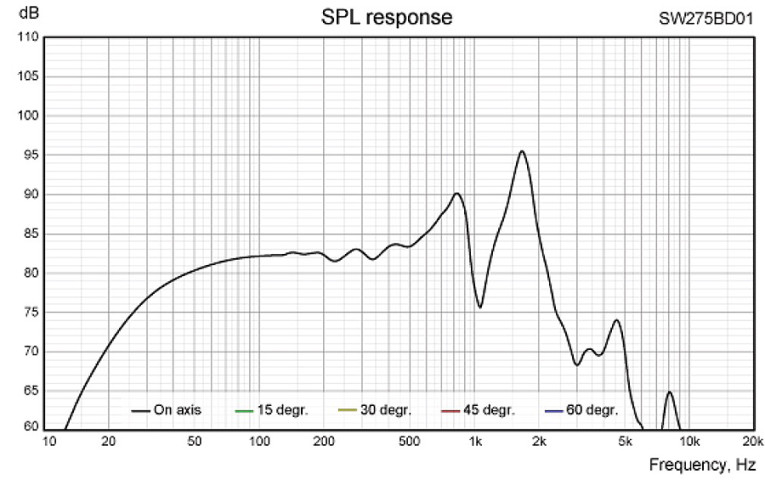
Generally speaking, I do not provide SPL and time domain measurements on subwoofers, as their upper range is generally not greater than 100 Hz to 200 Hz. Instead, you can see the factory generated SPL curve shown in Figure 10.
Next I used the Listen, Inc. SoundCheck analyzer with AudioConnect hardware, SoundCheck 16 software, and the SoundCheck SM3 ¼” microphone (all courtesy of Listen, Inc.) to perform the distortion analysis. For distortion measurements, the voltage level was set with the driver rigidly mounted in free-air and the voltage was increased until it produced a 1 m SPL of 94 dB (5.5 V), which is my SPL standard for home audio drivers. Next, I made the distortion measurement with the microphone placed near-field about 10 cm from the dust cap. As can be seen in Figure 11, this actually includes two plots—the top graph being the standard fundamental SPL curve with the second and third harmonic curves, and the bottom graph shows the second and third harmonic curves plus the THD curve with an appropriate X-axis scale.

Interpreting the subjective value of THD distortion curves is difficult and opinions vary considerably in the industry. However, looking at the relationship of the second to third harmonic distortion curves is of value. As previously mentioned in past explications of Wavecor drivers, I have used Wavecor drivers (both off the shelf and with proprietary modifications) on several projects as a consultant, and have a lot of respect for this company. As you can see from this month’s driver analysis, the SW275BD01 is another well-crafted transducer from the engineers at Wavecor. For more information, visit www.wavecor.com. VC
This article was originally published in Voice Coil, October 2018.