Klipsch used variants of the T35 (the K-77 tweeter) starting around 1959 in the big Klipschorn. The K-77 was also used in other Klipsch models including the Cornwall, Heresy, and La Scala. Klipsch employed this tweeter for 40 years until EV discontinued production in 2000. Yet the T35 lives on today, better than ever, in Klipsch products (and other pro and hifi speaker systems), manufactured exclusively for High Performance Stereo by Dai-Ichi in the Philippines. This trip down memory lane relates the story of the T35, with a look at not just the tweeters, but also the people behind these developments.
Got A Light?
Electro-Voice (“EV”) was founded in 1930, first specializing in mikes, then developing phono cartridges in 1948, and, starting in the early 1950s, offering loudspeakers. Eventually ownership shifted to Gulton Industries, best known for electric cigarette lighters and rechargeable flashlights. Jim Long, a long-time EV guy, swears that he never heard any mention of cigarette lighters during the Gulton years, but I remember their TV ads, and I had one of their rechargeable nicad flashlights (I also come across a Gulton cigarette lighter recharging patent). By the way, Jim helped with many details of this story, but the errors are all mine. Anyway, Gulton was acquired by Mark IV Industries in 1986. Mark IV funded the acquisition of many audio companies, including Altec Lansing, University Sound, and Cetec Gauss, all operating under the umbrella of Mark IV Audio. Apparently, this was an audio-brand-eating umbrella.
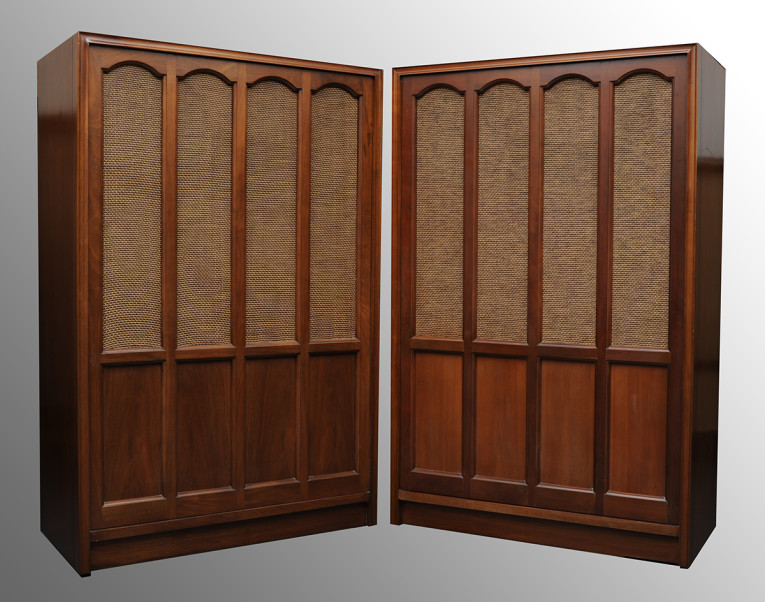
In early 1997, the purchase of Mark IV Audio by Greenwich Street Capital Partners of New York City was finalized. Later that same year, Greenwich announced plans to purchase Telex Communications. EV and Altec were merged in 1998. In June 2006, EV, along with all of Telex Communications, became part of the multinational Bosch conglomerate. EV was soon moved from Buchanan, Mich., to Minneapolis — Telex’s turf.
The US speaker industry has seen its ups and downs over the years, and EV’s history contains its share of pain and suffering. Much of the fabrication techniques and secret sauce has been spilled and lost. Some of this is due to the corporate ownership shifts and resulting geographical relocations of these companies, along with senior engineers opting for retirement. Back in the early 1970s, EV was a key supplier for my fledgling disco speaker manufacturing operation. EV’s OEM speaker sales were the job of John Boyers, a really wonderful guy who did anything possible (and some impossible stuff, too) to help EV’s OEM customers. Gary Gillum, Klipsch’s chief engineer in the late 1970s remarked, “John Boyers was a saint to me and taught me a lot. He broke bread with us at our home (log cabin) in Hope, Ark. Nice guy.”
EV had a rich OEM catalog in those days, and many famous brands and many musical instrument and pro sound speaker systems used EV components. The EVM cast frame woofers with aluminum flat wire voice coils had unprecedented sensitivity. Later, in the early 1980s, high excursion models were introduced, eventually leading to the awesome and innovative EVX 1500 and 1800 subwoofers by Doug Button. While Jim Long remembers that these were “bleeding edge” products that had a limited product life, I and quite a few other speaker engineers remember the EVX ultra-long-throw woofers as a source of a lot of food for thought. Most aspects were brilliant; a couple of the innovations needed further development, which is the downside to being the first duck in the pond. In any case, Doug’s less ambitious DX EV long-throw woofers have been a mainstream high-performance choice for decades. After EV, Doug went to JBL, where he continued to research and develop new speaker techniques.
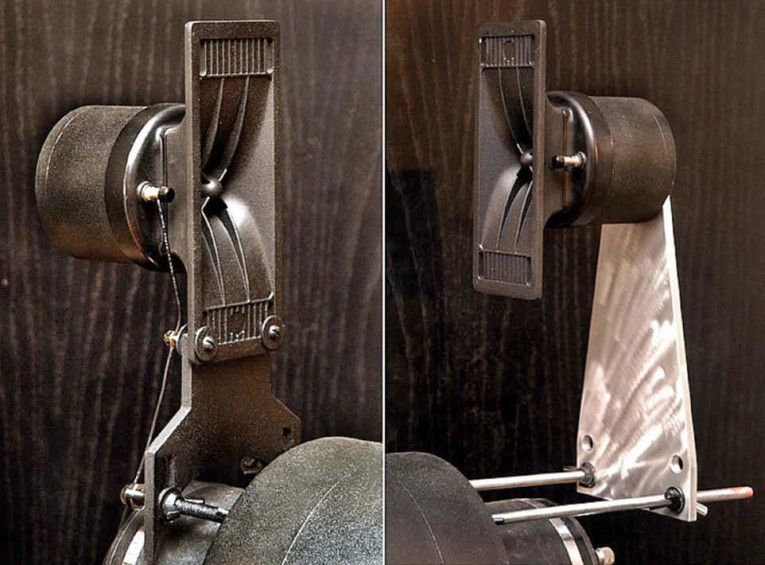
Key Players
My story of the lost art of the T35 super tweeter begins in the early 1950s with the introduction of the Patrician (Photo 1), a huge speaker system that EV launched to compete with the mammoths from Klipsch, James B. Lansing Sound (JBL), Jensen, and Altec Lansing. For the top-end response a horn tweeter was developed. The very first version of the Patrician did not have the T35, but it was integrated into the later Patricians by the late 1950s.
But before I get into the T35, let me introduce one of the saviors in this story — speaker industry veteran Tom Ressler. He started as a design engineer at EV in 1968 through 1976. Tom returned to EV as the engineering manager and later plant manager from 1983 to 1990. I first met Tom after he left EV and introduced him to Sammi Sound, Korea’s largest speaker manufacturer (in the early 1990s).
My affiliation with Sammi Sound was through the Korean government technology transfer agency (Small Medium Industry Promotion Corporation — “SMIPC”). From 1983 to 1989 I worked with Daizo Lee, considered the father of Korean speaker R&D and director of engineering at Sammi. We consulted on projects such as the military sound system in the DMZ, which projected propaganda six miles to North Korean bunkers; the computer simulations for the sound systems for the 1986 Asian Games; and also the sound systems for the 1988 Olympic Games in Seoul.
Between the economic globalization caused by the Olympic Games and militant unionization of South Korea, it became cheaper for Sammi to build in the sleepy (non-union) town of Danville, Ky., rather than the unionized factories of Seoul. At the tail end of the 1980s, there was a state of war in South Korea between workers and factory management, with the engineers caught in between. Daizo Lee left Sammi during those times to work at Aura Systems (Aurasound) for the next 15 years and now is a consultant living in Los Angeles (Since 2012 with Audio Design eXperts Inc., the makers of Riva Audio products).
Sammi’s operation in Kentucky called Stanford Acoustics focused on production of high-power compression drivers which were supplied to Federal Signal’s spec. These were similar to what Sammi made for the DMZ in Korea. Later Sammi acquired Roy Allison’s Allison Acoustics, which Tom ran. The economy in Korea was unstable and the “Asian Economic Flu” was coming. The Korean stock market crashed (Sammi had gone public), and Sammi Sound eventually faded away. Tom was looking for a new home.
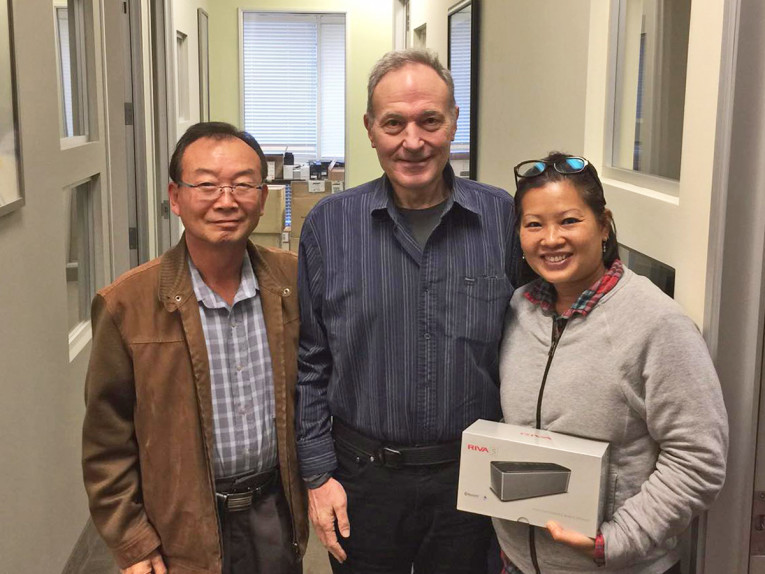
I started consulting for Dai-Ichi in the Philippines around the end of 1991. In the 1980s Dai-Ichi was buying tweeter “kits” from Sammi. But by the 1990s Dai-Ichi was already a bigger operation and technically ahead of Sammi. Pablo Tobiano, Dai-Ichi’s director, was looking for an experienced speaker guy to handle sales in the US. Tom Ressler joined Dai-Ichi in 1996 and stayed with them until he retired in 2008.
Back in 2004, at Menlo Scientific's Loudspeaker University in New Hampshire, Tom reminisced about his days at EV and the T35: “The T35 was first introduced in the 1950s as the tweeter used in the EV Patrician, corner loaded, loudspeaker system and some other models. This unit had a 30" woofer; the huge 30W featured a styrofoam cone. Later (after quite a few variants) the T35 evolved into the ST350. That was a joint design of Ray Newman and myself (Tom Ressler).”
Ray was the chief engineer at EV for many years and passed away in 1996. Ray is known for the early efforts at constant directory horns (“the white horns”) along with Don Keele, while John Gilliom worked on the EV driver (DH1012).
Jim Long notes, “Only vintage hi-fi nuts will care, but the earliest Patricians had 18″ woofers in Klipsch licensed corner horns. The Patrician 800, circa 1959, was the first one with the 30W.” More from Tom: “The ST350 was basically the same motor/VC/diaphragm as the T35, but we added a very wide dispersion aluminum die cast horn. This design was required for the Sentry IV speaker system that Ray and I also jointly developed. The Sentry IV had a 120° molded midrange horn that gave similar wide dispersion to the ST350 tweeter horn. The driver was an EV model 1823M, an alnico magnet driver (Photo 2). The low-end section of the Sentry IV was two 12″ woofers in a folded horn, 3/4" plywood enclosure, and painted black.
“The Sentry IV was designed for commercial installations, and about a year later was followed by a home or studio version, called Sentry III (Photo 4). This used a 15″ woofer and had a real pretty wood veneer cabinet. Same midrange horn and driver and also used the ST350 tweeter.” Tom briefly provided engineering support for EV during 1995-1996 and now is retired. Don Keele was also involved in development of products that used the T35 and related components. His stint of four years at EV (1972-1976) included development of EV’s constant directivity “white” horns.
Don briefly worked at Klipsch (for one year in 1977) while Paul Klipsch was still actively involved. While at Klipsch, Don, along with Gary Gillum, developed the Industrial Klipsch product line including the Pro Heresy. About 15 years before it was popular, Don introduced a line array of horn tweeters on this series (the large all horn-loaded concert system MCM 1900). At first glance this tweeter array may have looked like the T35, but actually this was the Motorola 2 × 5 piezos. Don is always at the scene of innovations, well before anyone else, always claiming innocence and having all sorts of reasons why someone else should get the credit.
Don went to JBL Pro, rejoined EV from 1994 to 1999, and then on to Crown/Harman in Martinsville, Indiana, working at Harman/Becker Automotive Systems. With Martinsville closed down, Don became an independent consultant and continues his work on loudspeaker line arrays based on CBT (Constant Beamwidth Transducer) research, first developed by the military for underwater sonar transducers in the late 70s and early 80s.
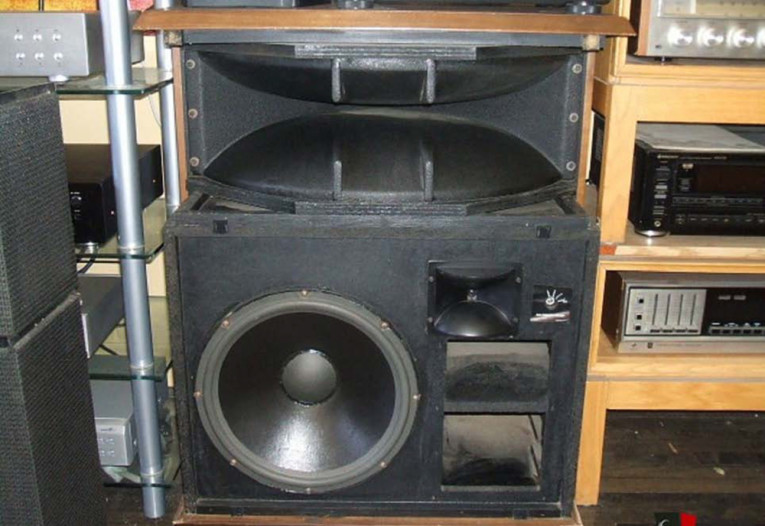
Re-Birth of the T35
High Performance Stereo (“HPS”), a manufacturer of movie theater sound systems, used the ST35 in their HPS-4000 premium speaker series. But EV was about to shut down production of the ST35 in 2000. Klipsch and HPS were impacted the most by this decision. For one thing, it meant the end of the classic Klipschorn and La Scala loudspeakers as three-way systems. John Allen, the owner of HPS, believed strongly that the performance of the HPS-4000 sound systems would be seriously diminished without the T35 and enlisted Tom Ressler to find a new home to build this product.
Tom brought the project to Dai-Ichi in the Philippines due to their vertical operation and “can-do” attitude. John corresponded with me on the T35: “I decided to do this project and finance it. I felt that I had to. I purchased some of the tooling from EV, although in the end Dai-Ichi redid all but the cast cover. The HPS/Dai-Ichi-made T35 actually performs better than the best of the EV built units—which were pretty good by themselves.”
So, with all this talk about people and companies, what about the T35 itself? Sensitivity was high—rated at 104dB 1W @1m. Distortion on the T35 was low, at least down to 7kHz, and picked up rapidly below down to 3.5kHz. This was a really tricky design, with two aspects that I thought stood out. For sure the bobbinless aluminum wire voice coil separated the boys from the men. Disassembly while not breaking the leadouts was a challenge.
Another trick to achieving extended response with the phenolic diaphragm was that until the T35, most phase plug designs assumed a piston diaphragm. Because the T35 diaphragm was 25mm (1″), the last octave was out of the piston range. So the phase plug used empirical (cut and try) techniques to put the phase plug location not where the dome should be, but where it would be. Nevertheless, production varied quite a bit in the last octave—due to jigging, the shape of the dome, weight and thickness of the fabric, phenolic impregnation (consistency), and so on. Klipsch would sort and inspect the T35 and keep those that fit their parameters. Improving top-end consistency was one of the challenges facing the re-creation of the T35.
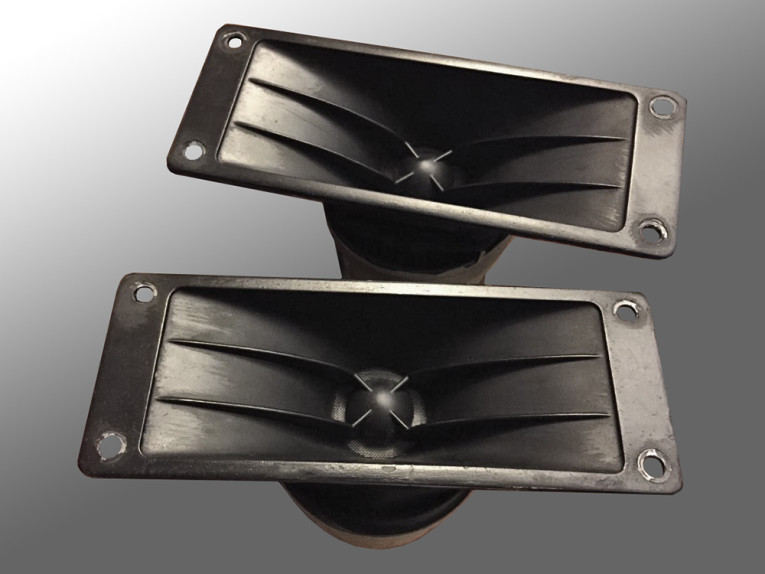
Dai-Ichi’s Development
I have heard that as the T35 went through various manufacturing groups during its EV life, the high-frequency response continued to drop. Engineers at Dai-Ichi were able to tweak the diaphragm and the phase plug spacing to bring the response back to where it was in the 1950s. The T35 also needed help on the phenolic and fabric materials in the diaphragm itself. The diaphragm in the T-35 was 1950s technology, while Dai-Ichi had spent years perfecting resin-treated fabrics for high-power voice warning applications. Magnetic structure continues as two stacked ferrite pieces (Photo 5). Special spacers needed to be designed to maintain the same back cavity volume behind the diaphragm and VC gap.
All of the T35 tooling was purchased from EV by John Allen. The front cover tool remains in the US at a die cast house. The horn and centering ring tools are no longer used and are in storage at HPS. At the request of both HPS and Klipsch, Dai-Ichi developed, and tooled, a new horn design with a recessed flange that allows for easier mounting on the inside of a speaker system, but doesn’t alter the dispersion. Both Klipsch and HPS use this new horn. During one of my visits to Dai-Ichi, their engineering guys brought up the T-35 project, sort of like commiserating about some ongoing dental work.
Apparently the very top-end response still was not up to what would satisfy both Tom and John. Dai-Ichi’s material science and fabrication specialist from Korea, Mr. Lee (not Daizo Lee, but interestingly, his past business partner) seemed to have gone so far beyond what EV had done a few decades earlier with the phenolic fabric diaphragm, and the adhesive joint between the dome and the self-supporting coil (Photo 6) also did not seem to be the culprits. I ventured the question that, of course, you are using aluminum or copper-clad aluminum wire on the coil, and the engineering manager looked both shocked and horrified — oops! Anyway, the CCA coil turned out to be the last step in the epic development of an enhanced re-creation of the classic T-35 super tweeter.
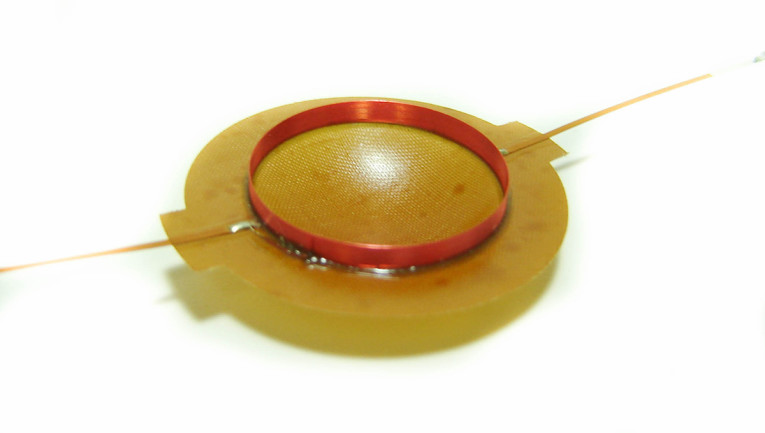
John Allen: “It took five years and 50 toolings to finally get the diaphragm where it needed to be. I doubt there are too many manufacturers that would put up with such a challenge, let alone pull it off. My congratulations and admiration goes to Pablo Tobiano for remaining committed to this project and also to Tom Ressler. Without Pablo’s dedication and Tom’s expertise, this project would not have succeeded. In my view, these men and Pablo’s engineers saved not just my company, but the Klipschorn as well.”
Dai-Ichi has given the T35 its new lease on life, and at 50+ years, this tweeter continued to do duty in movie theaters and high-efficiency home audio systems long into the future. VC
Players
www.daiichielectronics.com.ph
Gillum Loudspeaker Systems
www.hps4000.com
www.DBKeele.com
About the author
Mike Klasco is the president of Menlo Scientific Ltd. in Richmond, Calif., a consulting firm to the
audio industry. www.menloscientific.com
This article was originally published in Voice Coil, April 2010.