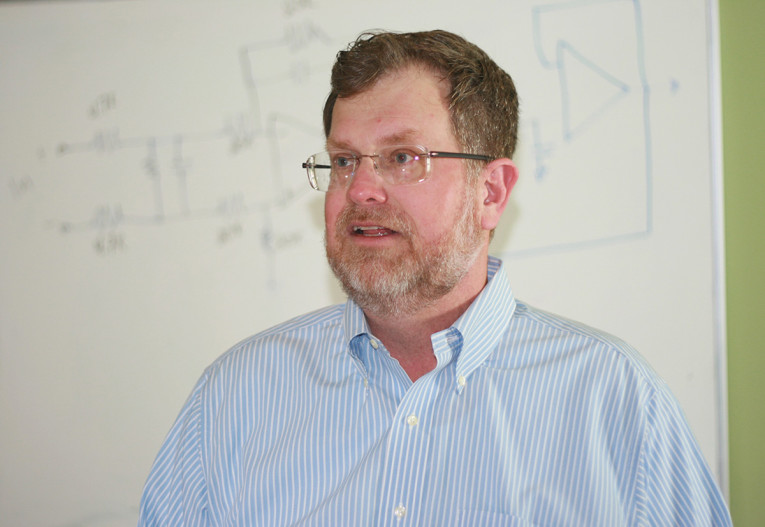
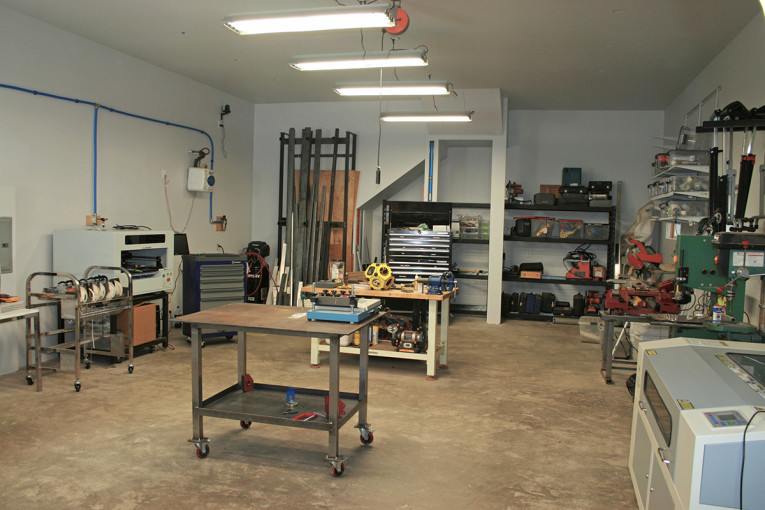
QuantAsylum is a privately held test and measurement company, with a solid catalog of product offerings for the automated testing of audio products for both design and manufacturing environments. Based in the Seattle, WA area, the company was founded by Matt Taylor, a veteran technologist with a breadth of design and management experience — including work at HTC, Microsoft, Motorola, and most recently as the CTO of Gogoro, a Taiwan-based manufacturer of electric scooters.
Not too long ago, Matt Taylor, President and founder of QuantAsylum, agreed to share an inside look and virtual factory tour of the operations at his 2500 ft2 facility in Snoqaulmie, WA (Photo 1). Inside this dedicated building is a 1000 ft2 prototype area.
The blank PCBs are sourced from China, components are purchased from US distributors, and the boards are assembled in Seattle (Photo 2). The boards are then installed in cases and the final test is performed on all units at the QuantAsylum corporate headquarters in Snoqualmie.
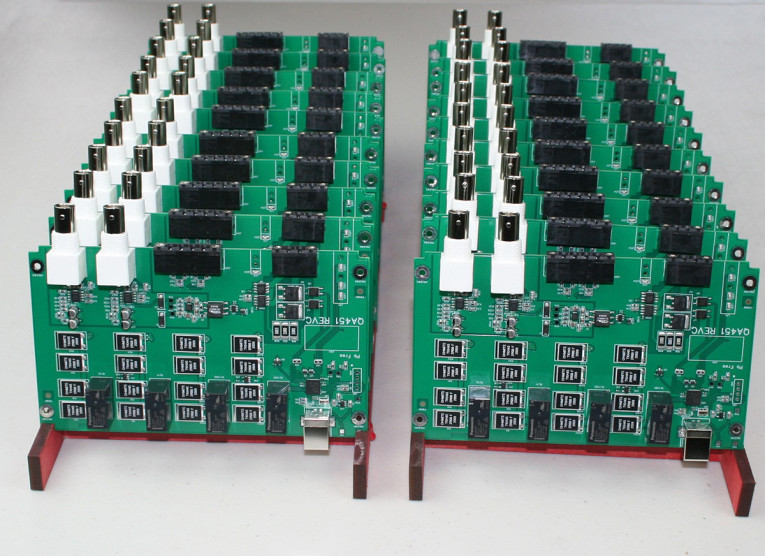
The top and bottom aluminum cases (Photo 3) are custom fabricated as blank panels in China. Cleverly, the size and footprint is universal across all QuantAsylum products, so the casework can have full-color graphics printed on demand using their in-house UV printer. The UV printer is used to print artwork on the top, front, and back panels of every case (Photo 4). The UV printing process isn’t quite as good as a traditional silk screened panel, but it provides unrivaled flexibility for a just in time US-based final assembly process.
The assembled hardware is tested at one of two test stations, each equipped with a fanless and low-cost micro PC mounted on the back of the touchscreen interface (Photo 5 and Photo 6). Finally, Matt Taylor shared a preview of a new, not yet shipping product, the QA440 relay box (Photo 7). This innovative accessory enables flexible and seamless routing of audio channels for production testing of a 5.1 channel receiver via the QA401 analyzer. With this relay box between the DUT multichannel receiver and the QA401, the receiver can be tested under full-load on all channels, without operator intervention (e.g., cable connection and disconnection), thanks to onboard integrated relay control.
Given the circumstances not allowing for in-person visits, Taylor was kind enough to provide a behind-the-scenes interview to audioXpress and preview what’s in store for QuantAsylum.
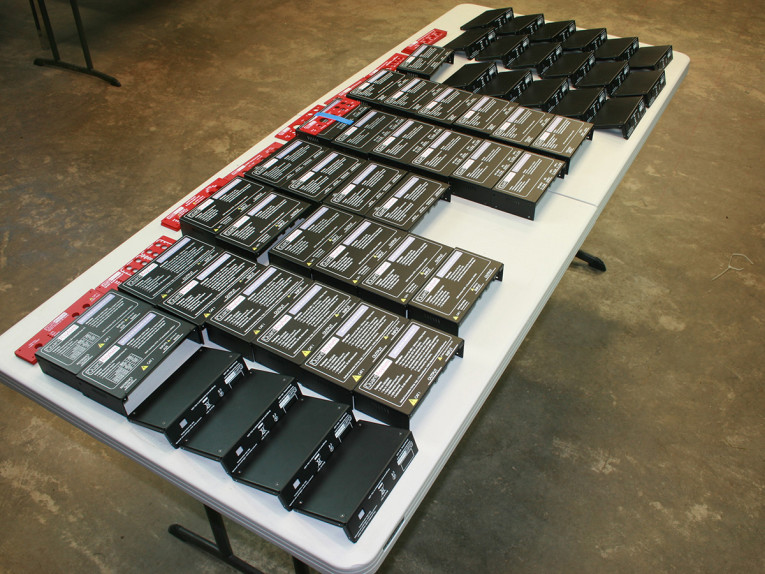
David Logvin: QuantAsylum launched its first general-purpose audio product, the QA400 Acoustic Analyzer, in 2012. Can you tell us more about the early start-up years and how you grew this business?
Matt Taylor: The first audio product (the QA400) in 2012 gave us an initial glimpse into what was needed from an audio perspective. There were a lot of companies coming to my long-time friend and business partner (based in Shenzhen, China) and those early requests helped shape the longer-term portfolio. That was an especially important time for understanding the business. Coming from Microsoft, the easy answer to meeting the needs was “Just tell them to write a program to control it!” But many of these companies wanted to test simpler things like piezo buzzers and test tones coming out of integrated circuits. And they needed to test them very, very quickly. They had the skills to build sophisticated material handling machines, but the automation software for audio testing needed to be more turnkey. In short, we weren’t there yet.
The QA401 analyzer was introduced in 2015, and then the automation solution arrived in 2018 with a software product called Tractor. Tractor enables engineers to quickly build sequences of tests without writing any code. Tests results can be stored locally or in the cloud, and operators need only interact with a touchscreen and barcode scanner to verify the operation of the product.
So, in retrospect, it took about six years to settle on the recipe and understand what the market was going to be. And there were products along the way as the recipe was being figured out (DDS generators, oscilloscopes, logic analyzers) that we probably won’t revisit because the larger market has served that segment well.
Moving forward, continuing to build out this ecosystem is the focus over the next few years. Multichannel voltage measurements, current measurement, relay control boxes are all coming. The aim is to broaden the appeal to engineers at mid- and small-size companies that are creating products that need to be tested at manufacturing, warranty service, and more — quickly and with a cloud-based audit trail if needed.

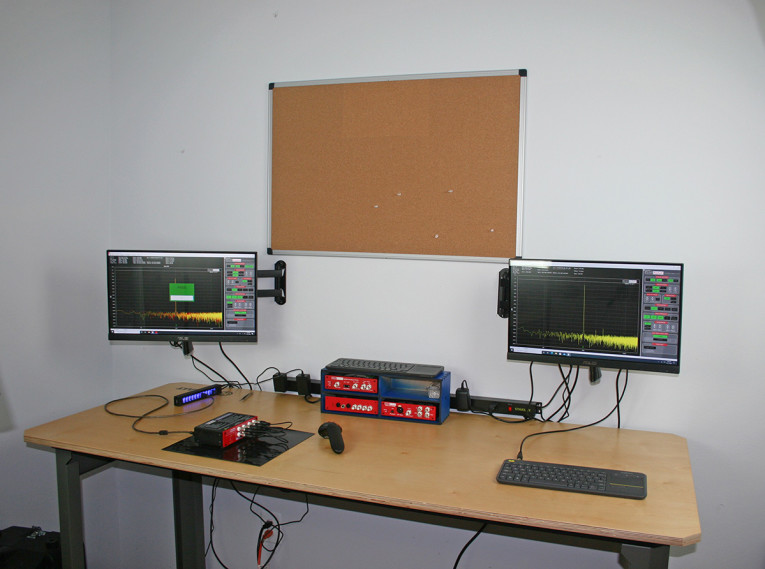
David Logvin: Can you share an overview of the current manufacturing capability and share some details about the production team?
Matt Taylor: The production "team" is all contractors, which can expand and contract with demand. Top and bottom cases and PCBs are made in China, and local assembly houses populate the boards in Renton and Bellevue (both suburbs of Seattle, WA) from parts purchased from US distributors. From there, the assembled boards go into cases, and then we test them and ship them. The time required to take a populated QA401 board, assemble it into the case, test it, box it, label it, and have it ready for UPS pickup is under 10 minutes. I do most of the design, with some occasional help with mechanical, FPGA, and software from folks around the world.
David Logvin: In many ways, QuantAsylum has avoided a lot of traditional business models that the test and measurement world favors. Conventional wisdom has often pushed lower-cost measurement systems toward a sound card-based approach. Is calibration the primary reason you decided that the QA400 (and the QA401) would be dedicated hardware systems?
Matt Taylor: I think sound cards fall short for several reasons. First, I don’t think common USB audio interfaces are suitable for factories — ASIO maybe. But there are too many unknowns with background sample rate conversions, bit depths changing seemingly at random, other apps trying to use the card. Anyone that has ever tested HiFi DACs will tell you it is an involved process to be certain the DAC that says it’s operating at 24-bit/48kHz is actually operating at that rate end-to-end. Second, sound cards aren’t usually galvanically isolated from the PC.
And finally, there’s the issue of calibration and gain. A gain knob in a factory is a big problem. Gains need to be fixed and tightly controlled. A QA401 in loopback will typically exhibit gain error standard deviation of under 0.01dB from one unit to the next. That means the QA401 you buy tomorrow will have very good agreement with the QA401 you buy next year.
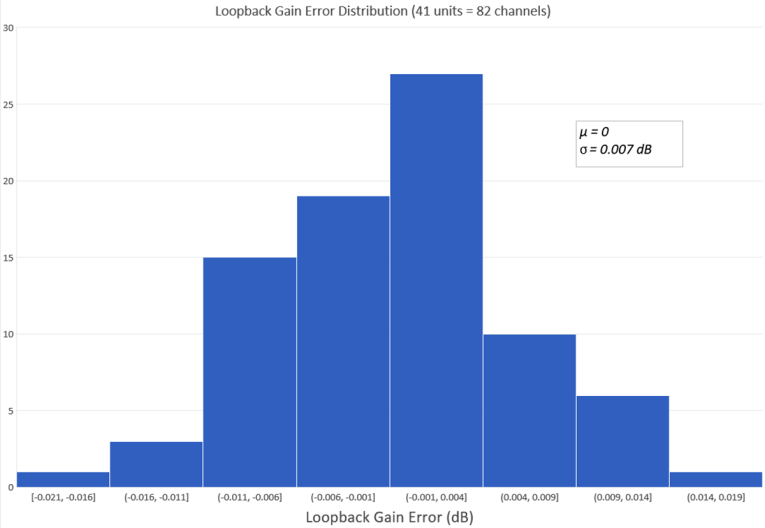
David Logvin: You take the support of small scale manufacturers and start-ups very seriously. You have made customized front panels for rack mounts and low MOQ specialized test gear with souped-up specs for unique applications (e.g., the QA480). How are you able to deliver these customized products without overloading your manufacturing and operations teams?
Matt Taylor: Tools and the Internet are the enabler here. If someone wants four products in a single 2U rack space, a contract ME can create the front panel DXF in under an hour, then we’ll laser cut it out of acrylic in-house to verify the fit, and then that goes to be laser cut out of aluminum in Nevada or Utah, then we get it back in a week and get it powder coated locally. And then the graphics can be printed using the UV printer.
These steps are all part of the normal product flow, so a custom front panel just tags along with the other material. And usually, the requests for custom front panels are from manufacturers that are doing an install into a rack. I think it’s a smart thing to support because if they need one they usually need more. For the QA480 (a low distortion 1kHz oscillator + notch), several of the subsections on the PCB had already shipped on other products and the case artwork can be printed on demand with the UV printer. So it wasn’t a lot of effort to go from something that was originally for internal use (the QA480 was created for testing a next-generation analyzer) to something that was useful to others too.
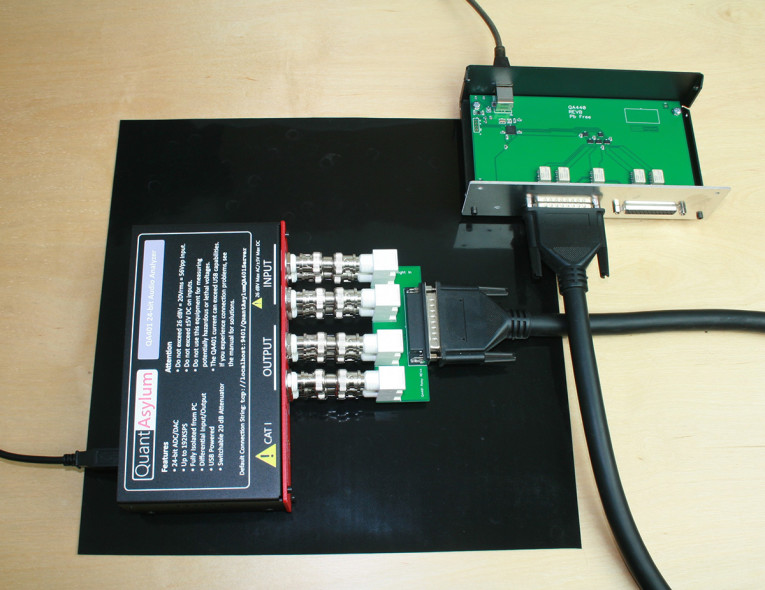
David Logvin: When I worked for small consumer electronics manufacturing companies, my mantra was to not have more SKUs (stock keeping units) than employees — to keep the focus on innovation and the core products. Do you think that is still practical today?
Matt Taylor: Yes, I think it’s still a good rule. I’ve managed big pieces of large engineering efforts with hundreds of engineers focused on a single product, and also startup efforts where I was a co-founder and first engineer. And almost universally there’s a push to get a product out the door, take the support pain by building a large support organization, learn, refine, repeat. The early days of smartphones at Microsoft were so complicated that we’d see return rates of 30% to 40% in some cases. The products weren’t broken — the consumer just didn’t want to cope with the rough edges and minutia of getting everything set up. But the support effort was large and the support organizations were large.
With QuantAsylum, the focus has been more on managing growth toward a particular support effort and return rate. That means focusing on a core set of scenarios and doing those really well, rather than doing everything. As an example, things like THD vs. power out—these are the bread-and-butter measurements you have to do well.
I like to think of our tools as your trusty digital volt meter (DVM) — the first place you turn for your fundamental measurements. We don’t do waterfall plots or esoteric distortion perception metrics. But if you want to know the output impedance of your amp vs. frequency, that’s a click away. The result is a return rate under 1% and a support effort that is a very small part of the day in spite of thousands of products in the field. The business doesn’t work otherwise.
David Logvin: Looking at your product road map, are there plans to integrate more instruments into a single chassis, or do you plan on staying with the modular-based approach that you have leveraged to date?
Matt Taylor: All of the products share a common custom mechanical design. This makes it easy to order cases without having to forecast; you just know they will be needed. Moving forward that stays the same: stick with the common chassis with custom front-panel for each product. For companies that would like the functionality in a rack, we can create a new faceplate and bolt two or four boxes to that faceplate. For example, for mic testing you might have two QA471 mic pre-amps, a QA460 transducer driver, and a QA401 audio analyzer. Those four boxes can be mounted to a single 2U rack faceplate. That gives you the ability to drive a speaker with the QA460, handle two mics (a reference and a DUT) each with 10dB of gain with the QA471, and then measure the signals with the QA401, take the difference and compare that to a pass/fail mask.
David Logvin: Are there any discontinued products that you plan on revisiting and updating in the near future?
Matt Taylor: Yes, there’s an omnipresent need for tools that permit very detailed power analysis. Expect to see something in 2021, hopefully that will make it easy to log current consumption at a very high rate and over several decades — from
nA to amps. There was an early product called the QA150 that had some of that functionality.
David Logvin: Another area of key differentiation for QuantAsylum is that the software is free and open source. Most test and measurement companies charge for their software and then charge upgrade fees for R&D/quality control modes or institute annual fees or maintenance and software service plans. Is the rebellious approach you have instituted something that can be maintained as QuantAsylum grows its business?
Matt Taylor: Yes, the software and upgrades should always be free. We can’t support every product forever, but the QA401 is five years old and still seeing around 10 software releases per year. Open source is very important for software like Tractor, because the manufacturing engineer may need the flexibility to do something we couldn’t anticipate.
I think another big shift here has been getting up on Github this year and migrating to REST as a control means for the product. Github means the developers have a shared common workflow. They can log bugs, submit feature requests, and Github works very well for technical writing; sharing plots and data is very fast. It’s a great way to interact with other developers and users. REST is a design philosophy for controlling and querying the things via web API. Instead of needing an engineer that knows how to write GPIB or LabVIEW — a fairly specialized set of skills — you can use an engineer who knows how to code web apps. And how cool is that!
An IT person who knows how to use Python to query an employee’s salary from the web can also make a THD reading from the QA401 using the same knowledge and same tools. The REST software interface first appeared in the QA350 DVM, and it’s been a good move. A user just shared an application on Github that they wrote in Javascript where the audio analyzer was running in a web page with really impressive performance. That is the power of REST for test and measurement — you leverage the know-how of millions of developers.
David Logvin: With more folks working from home these days, do see your role expanding in making home-based measurement systems both more useful and affordable?
Matt Taylor: Yes, I think so. Second quarter of 2020 showed more than two times growth vs. the same quarter of the previous year, and I suspect a big part of that was a shift to home-based labs. The affordability is tightly tied to performance. At a twentieth of the price, the QA401 won’t match the performance of a $10,000 analyzer. But most products shipping today don’t need a $10,000 analyzer to confirm that their output is 0dBV ±0.2dB. Nor do they need a $10,000 analyzer to confirm the THD at 100W is -90dB. There’s no question the very high-performance analyzers are needed in many R&D settings. The bigger question is, "now that you need to build out five test bays for your manufacturing line, does the QA401 product have enough margin to verify your product?" And I think for most products, the answer is yes. aX
This article was originally published in audioXpress, March 2021.
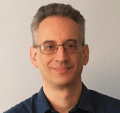
David Logvin is an acoustics engineer at TDK InvenSense, working in the MEMS microphone division. With more than 20 years of experience, he has designed loudspeakers and other products for Snell Acoustics, Outlaw Audio, ClearView Audio, Cambridge Sound Management, and others. During his 14 years at Snell Acoustics, he developed and designed dozens of high-end loudspeakers and amplifiers, as well as helped to create loudspeaker standards in close collaboration with THX. Logvin then focused his efforts on R&D, creating innovative, award-winning piezo-driven membrane loudspeakers with ClearView Audio (formerly known as Emo Labs). At Cambridge Sound Management, he put his skills in room acoustics to use in the field of sound masking for corporate applications. Most recently, he rejoined his fellow Snell Acoustics alumni, Dr. Joseph D’Appolito, to design several new loudspeakers for Outlaw Audio. In addition to his lifelong love of music and acoustics, Logvin is an active participant in the Boston tabletop game design community. He is a member of the Audio Engineering Society (AES) and the Boston AES Section and lives in Lowell, MA with his family.