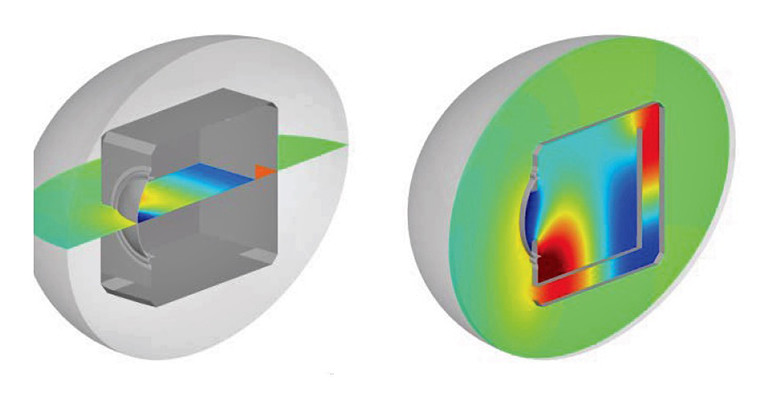
In addition, it is often important to assess an audio device’s performance in the final system assembly, which is almost always different than that of a microphone or speaker alone (i.e., in the uninstalled configuration). Consider, for example, a vehicle audio system in which loudspeakers are mounted in the door structure. The acoustic performance will be driven not only by the loudspeaker, but also by the door structure, the cavity inside the door, and the internal door components.
A high-quality, expensive loudspeaker can have poor performance if the overall system design is not properly done. Foreseeing these types of issues before speakers are chosen and the door is tooled enables engineers to design a system optimized for performance, cost, and weight, and to eliminate unnecessary costs and headaches from late design changes.
Acoustic simulation software enables audio system manufacturers and integrators to determine the acoustic performance easily, accurately, and early by providing detailed information about what to expect before hardware is built, and more importantly, why because simulation illuminates the physics involved in each design. Second, simulations enable designers to rapidly evaluate several different configurations at initial stages of product development and enables the assessment of complete system performance to ensure superior audio quality.
Actran, MSC Software Company’s acoustic simulation solution, is based on Finite Element Analysis (FEA) technology. It provides predictive simulation capabilities to assess the vibro-acoustic performance of audio devices, which include speakers and microphones. It also enables the improvement of audio recording systems by simulating complex phenomena (e.g., aeroacoustic background noise).
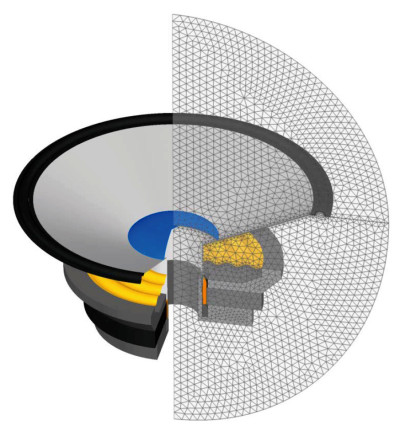
• Loudspeakers
• Microphones
• Headsets
• Televisions
• Cell phones
• Car sound packages
• Hearing aids
Actran can create 2-D axisymmetric models to evaluate many designs in a short time. It can also model 3-D simulations, which are used when a design is not symetric (e.g., to assess the speaker performance integrated in a cabinet, a ported box, or a loudspeaker in a complete car door).
Acoustic simulation of audio devices poses several challenges ranging from advanced modeling capabilities to better understanding the physical behavior of a given design. One challenge is the visco-thermal dissipation in small cavities or narrow channels. Let’s consider a loudspeaker: acoustic waves are slowed down and damped out when passing through the thin air gaps between the voice coil and the magnet. Visco-thermal dissipation can be found in any audio application where small cavities are present (e.g., headsets, cell phone speakers, and microphones).
It is worth noting that although modeling dissipative slits is relatively easy because the geometry is simple, modeling small cavities of arbitrary shapes is more complex. Actran Version 15.1, which was released in the spring of 2015, provides several additional modeling capabilities to loudspeaker designers (see Figure 1). This version can provide simulations ranging from the simple and well-known Low Reduced Frequency (LRF) model for thin slits or narrow channels to innovative models specifically developed for complex 3-D arbitrarily shaped geometries.
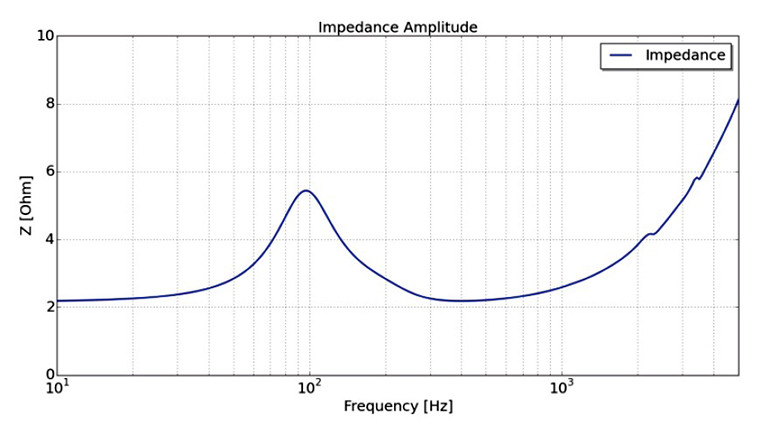
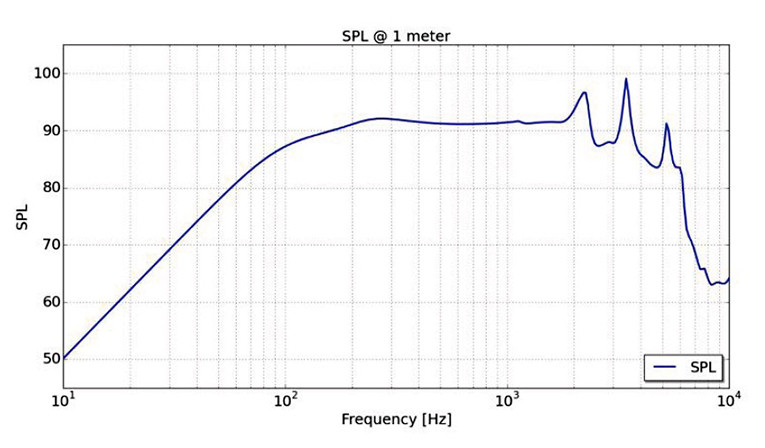
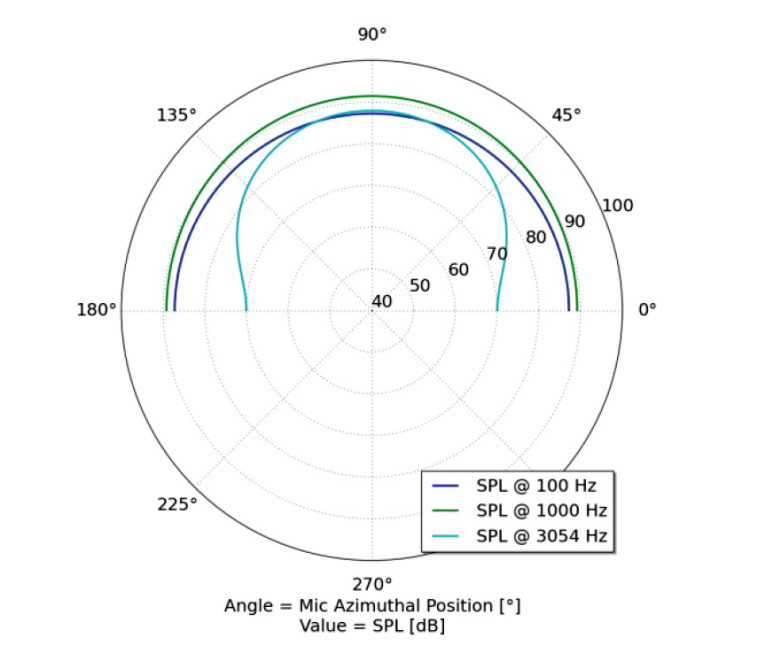
Simulation Example
Figure 2 shows a loudspeaker cutaway view that has been solved with an axisymmetric model to get accurate results faster than with a full 3-D model. This model, made for demonstration purposes, features a spider made of reflective material (i.e., nonporous), and it is vented in the back. The air cavity enclosed by the spider and the speaker structure is connected to the surrounding air through the narrow air gap at the voice coil’s internal and external surface. This is a simple design to model since it does not include a porous spider or an internally vented cavity.
Despite its simplicity, acoustic predictions are still accurate. Vibro-acoustic simulations performed by Actran provide all the outputs normally obtained by testing physical prototypes, and several other indicators to help engineers thoroughly understand the expected physical behavior of a given design. These outputs include the loudspeaker impedance (see Figure 3), computation of the Thiele-Small (T-S) parameters, sound pressure level (SPL) spectra (see Figure 4), and directivity plots (see Figure 5), which in this example are from a circular array of virtual microphone 1 m from the loudspeaker.
In addition to these important indicators, Figure 6 shows the acoustic pressure radiating in the far field inside the 1 m radius hemisphere of the microphone array. Figure 7 depicts the acoustic velocity in the near field and at the speaker driver surface. These maps are extremely useful to the loudspeaker engineer (e.g., at higher frequencies when the speaker higher order structural modes play an important role in sound propagation). Moreover, this type of analysis is fundamental when analyzing 3-D cases. A simple directivity plot might not reveal 3-D propagation patterns.
A helpful indicator is the radiated acoustic power compared to the total supplied power. Actran makes it possible to analyze the dissipated power in the fluid and in each of the different structural parts. Figure 8 depicts a power analysis up to 1,000 Hz. It is worth noting that at low frequencies most of the power is dissipated by viscous losses. The dissipated power in the structure becomes more important above 500 Hz. However, the radiated power remains fairly constant above 200 Hz. In Figure 9, the power dissipated in different parts is shown. At low frequencies, most of the power dissipated in the structure occurs in the spider, while the surround has an increasing role above 800 Hz.
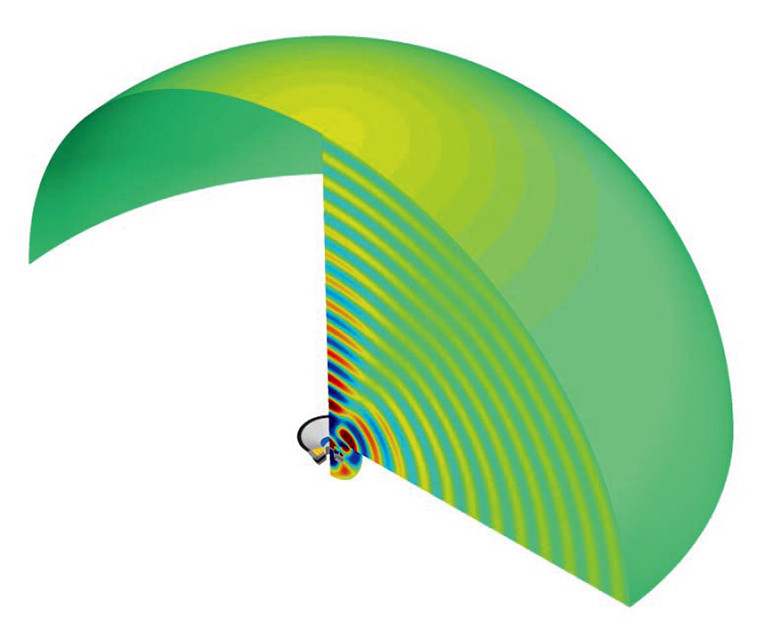
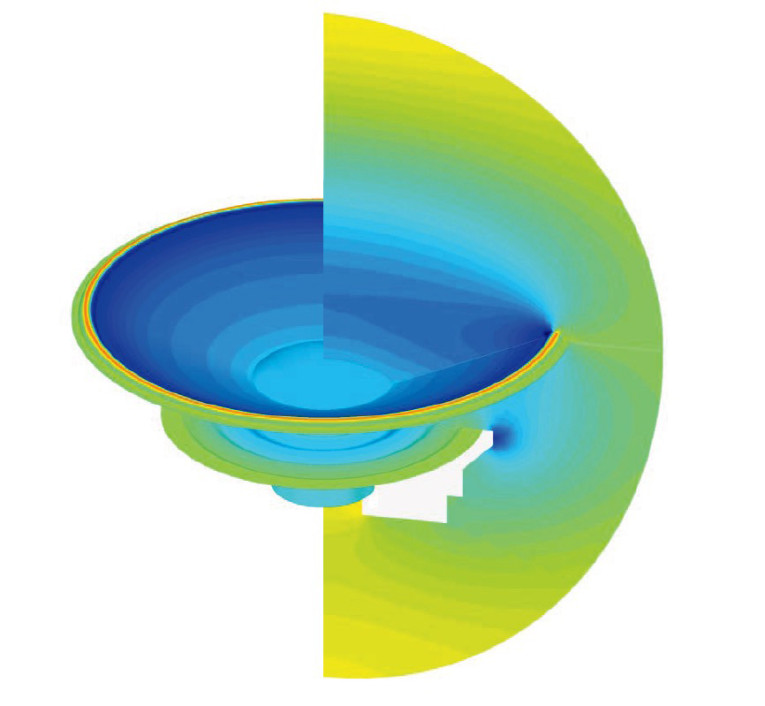
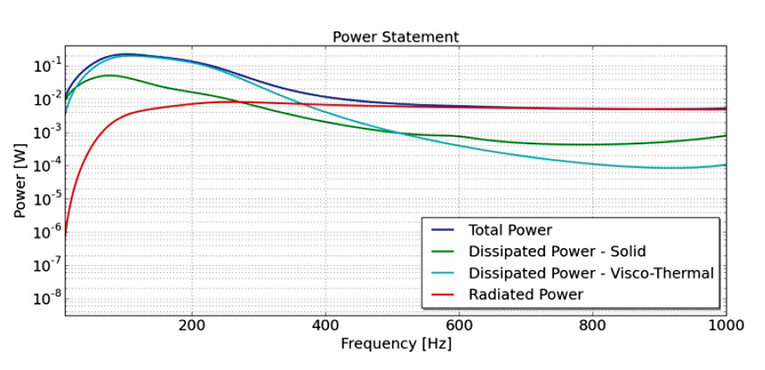
Actran’s Benefits
Actran software enables audio engineers to predict audio device performance by means of 2-D models for fast analyses or 3-D models for complete system assessments.
Actran’s simulations can include advanced phenomena such as:
• Visco-thermal dissipation in thin air layers or small cavities of any arbitrary shape.
• Full vibro-acoustic models to account for the fluidstructure interaction of the speaker and microphone parts as well as the final assembly.
• Porous materials with full skeleton and fluid models Actran enables engineers to design superior products by providing them with direct access to advanced indicators such as the radiated power and the dissipated power within the different domains. Finally, Actran is easy to use thanks to its dedicated graphical user interface (GUI).
The Companies Behind Actran
Free Field Technologies (FFT), is an MSC Software Company founded in 1998 and headquartered in Mont-Saint-Guibert, Belgium. FFT develops and supports Actran, a powerful software suite for acoustic, vibroacoustic and aero-acoustic modeling.
Actran contains a wide set of acoustic features making it the solution for customers as diverse as top car manufacturers and their suppliers, the largest civil and military aircraft and aircraft engine manufacturers, leading producers of loudspeakers and other audio devices, consultants, universities and research centers.
FFT maintains offices in Toulouse, France; Tokyo, Japan; Detroit, MI; and Beijing, China. MSC Software is one of the 10 original software companies and a global leader in helping product manufacturers advance their engineering methods with simulation software and services. As a trusted partner, MSC Software helps companies improve quality, save time, and reduce costs associated with design and test of manufactured products. Academic institutions, researchers, and students use MSC Software’s technology to expand individual knowledge as well as expand the horizon of simulation. MSC Software employs 1,100 professionals in 20 countries. For additional information about MSC Software’s products and services, visit www.mscsoftware.com
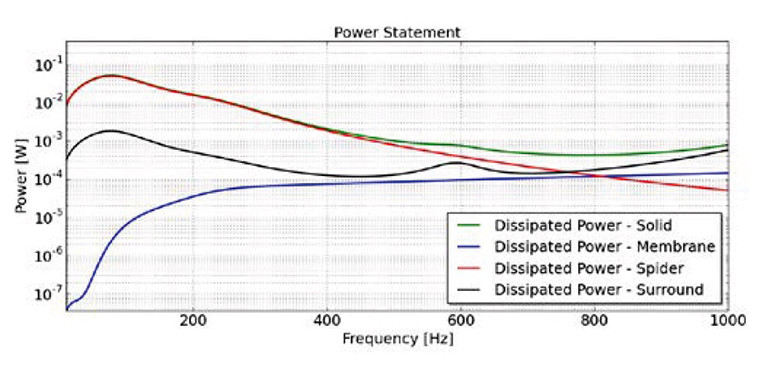
This article was originally published in Voice Coil, October 2015.