After the coil is wound onto the bobbin and the lead-out wires trimmed, the collar is wrapped over the lead-out wires (see Photo 1). The collar material might be Kraft paper, a spunlace aramid fiber like Nomex, an aramid paper like Bondex, or a ceramic inorganic paper such as Tufquin. In extreme high-power applications, where the structural reinforcement responsibilities of the collar are significant, the collar may even be a layer of aluminum.
There are many subtle ways a speaker designer can use the collar to “tune” the speaker-design for optimum response, added strength, increased thermal tolerance, better assembly fit, and more. Often, and for reasons we will address, the collar extends into the neck joint. Let’s take a look at the requirements for voice coil collars. Primarily, the collar is used to properly dress the lead-out wires from the coil, positioning them against the bobbin and increasing the strength of the voice coil above the voice coil winding. Alternatively, lead-out wires may be glued directly to the bobbin without a collar. Still, there are quite a few sound reasons to use a collar.
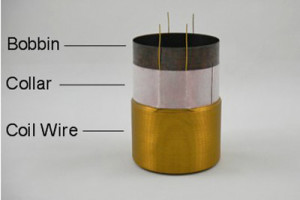
(Source: Precision Econowind)
Increase Bobbin Strength
A collar is used to stiffen and strengthen the space between the top of the voice coil winding to the neck joint. While the voice coil winding stack provides the mechanical integrity to the voice coil assembly, the space between the top of the coil winding and the neck joint (where the spider and cone meet) can be vulnerable to crumpling, especially on vented-bobbin, high-power woofers in small enclosures. The collar increases the integrity of this Achilles’ heel of the voice coil assembly.
Thermal Management
If a thermally nonconductive collar material is used with an aluminum (or titanium or bronze) bobbin or other thermally conductive bobbin material, then the neck joint adhesive and cone material will be exposed to less heat from the voice coil. If the bobbin/spider/cone neck joint (the triple joint) is exposed to too much heat, the adhesive may get soft or be otherwise damaged.
Neck joint adhesives have many requirements, and if parameters other than ultra-high temperature tolerance can be accommodated, this is the preferred approach. Poly cones with aluminum bobbins that will be used at high power really need a thick thermally nonconductive collar if heat warping of the poly cone is to be avoided. Spiders can also be singed (scorched) at high bobbin temperatures, with cotton spiders being most vulnerable. A layer of collar material provides significant margin of thermal insulation protection.
Dimensional Fudge Factor
The collar may be used to build up the outside diameter of a stock bobbin in order to fit an existing cone body. Somehow the inventory of cone neck IDs and voice coil bobbin ODs never seem to exactly match up. If the bobbin is slightly smaller in diameter than the cone internal diameter and you want to build up the bobbin so as to create a friction fit between the bobbin and cone body. The addition of a collar will then be beneficial.
The optimum selection of adhesive will be affected by whether there is a loose fit or a friction fit between these parts. If the fit is loose, then a viscous (toothpaste) bridging adhesive is needed. But it is not unusual in the summer for the viscosity of the adhesive to thin out and drip through the voice coil/cone joint onto the voice coil. Since most woofers are assembled cone face up, the adhesive bead on the neck joint leaking down into the voice coil gap could ruin the entire speaker.
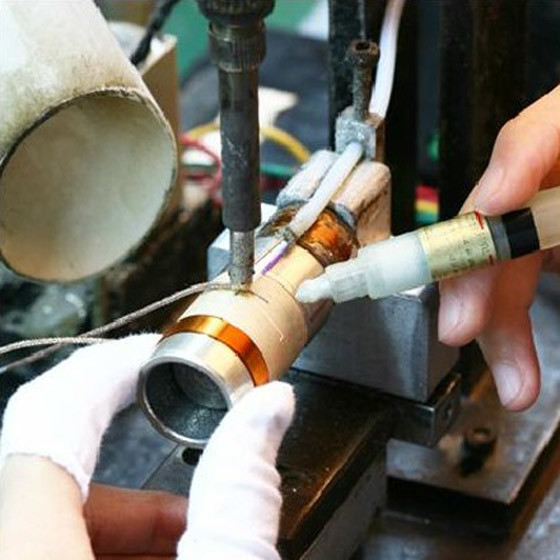
Collar Wrap
Typically, the collar material is slit to the correct width and a layer is wrapped around the bobbin.
Occasionally, a spiral-wound collar has been used, but the tight tolerances and collar material dimensional stability required can be tough and problematic, as seen in Photo 2.
Venting
For high-power applications, the bobbin and collar can have vent holes punched. Location, size of the holes, and quantity of the holes must be knowledgeably considered. If the velocity of air through the holes is too high, you will have a whistle modulation. Also, if the holes are too close to the winding, they can be partially closed on the back stroke and result in modulation noise. Too many large holes can reduce the integrity of the voice coil and crumpling can result. In aluminum bobbins without a collar, a long-term failure mode of metal fatigue can cause tear propagation from one hole to the next (see Photo 3).
Adhesive Interface
Many cones — especially poly, and many bobbin materials, including polyimides such as Kapton, and even aluminum — are not easy substrates to bond to. A rough material, such as a ceramic paper or Kraft paper, or spun lace Nomex provide a receptive interface for adhesives between the bobbin and cone. Bonding two “greasy” low-surface energy surfaces requires an adhesive of lower surface energy — which may not otherwise be the adhesive appropriate for the job. Bonding a lower surface energy bobbin like Kapton to a rough textured collar material enables a strong bond between otherwise tricky combination such as Kapton and polypropylene.
Acoustical Properties
By astute selection of collar material and thickness, the speaker designer can utilize the collar to somewhat control the top-end response of the speaker driver. If a woofer or mid-range speaker has a rising and peaking response, perhaps due to beaming and diaphragm breakup, instead of using a second-order network to tame this, using a thicker collar material might be the optimum solution. The collar functions as an acoustical response filter.
Tweaking the collar is far less disruptive to the design process than changing the voice coil diameter to alter the coupling between the coil and the cone. With a thick lossy collar between the bobbin and the cone, the excess upper midrange energy can be attenuated before it ever reaches the cone neck. Remember, as long as the collar OD is not larger than the OD of the voice coil winding, you should avoid gap clearance issues. But you still have to fit this to the cone ID.
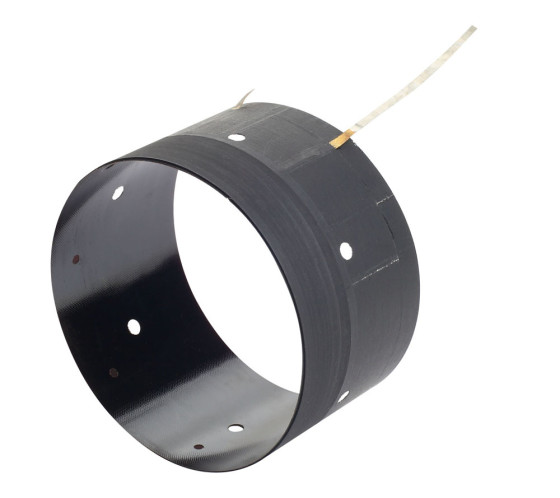
Collar Material Selection
Collar materials are often selected because they are very pliable, absorptive, and easy to drape over the lead wires during fabrication. As we mentioned, absorptive or textured materials are easier to glue to, resulting in a good bond between the collar, the bobbin, and the cone.
Pliable (soft and easily moldable) is an attractive characteristic because the collar material must conform closely over the lead-out wires. If the collar material does not tightly seal the lead-out wires against the bobbin, whistling noises may result. Additionally, a loose collar provides a capillary path by which ferrofluid can migrate from the gap. To prevent ferrofluid from migrating between the lead-out wires and the collar, a gel-type adhesive over the lead-out wires—applied along the length that will be covered by the collar—is recommended.
If the collar material is absorptive, then it is not compatible with ferrofluid. Ferrofluid may be absorbed into the collar material, changing the effective moving mass and resulting in unstable characteristics over time. But, good adhesion characteristics do not necessarily require absorption as a rough non-absorptive surface texture also may enable good adhesion. The key to finding a good collar material that is compatible with ferrofluid is locating a rough surfaced, but not absorptive material. Ideally, an intrinsically non-absorptive material should be used such as 3M (“IPT”) TufQUIN.
Common Collar Materials
There are a number of materials for collars from various vendors. Often voice coil manufacturers will source their materials from converters that stock, slit, and die cut as well as adhesive coat and distribute to their customers.
Let’s take a look at some of the options.
Kraft paper — Kraft paper is readily available from voice coil converter materials suppliers everywhere. Untreated Kraft paper is popular for collars, as it is easy to work and inexpensive. It is not ideal for thermally conductive bobbins that must withstand high-temperature operations. Kraft paper is also highly absorptive and thus, is not a good choice for use with ferrofluid.
One workaround to both higher temperature operation and sealing the Kraft paper material is for the voice coil manufacturer to impregnate (brush on) an epoxy coating, although this is a process-control sensitive solution.
DuPont Nomex 411 and 410 (aramid spunlace fiber sheet) — Nomex is an aramid-family material, in the general category of super-performance nylon.
Aramids include Conex from Teijin and Bondex aramid. Somewhat unique, Nomex is a spunlace process produced by high-pressure waterjets, although there are some new spunlace aramid fibers now being produced in China. Spunlace is appealing for collars as it is pliable and popular with voice coil winders, but it has become hard to source. Nomex is harder to work than Kraft paper and care must be taken to avoid forming an air gap between the lead-out wire and the bobbin, as this will result in whistling noise. Spunlace Nomex collars are used when high adhesion, low-tear propagation, and elongation performance is required. Nomex 410 is “calendared,” a process where the material is fed through rollers at high temperature. The processed material is 0.333 mm the thickness and less absorbent.
Nomex has a higher temperature tolerance than Kraft paper, which is a benefit if thermally conductive bobbins are to be used. Resin-treated Nomex is used to reduce the dimensional instability and reduce the moisture (and/or ferrofluid) absorption of Nomex.
The trick is to bake out the Nomex and then dip the Nomex into a resin and run it through rollers. Still, even resin-coated Nomex is not fully saturated as the Nomex material edges, created during the slitting process, expose unsealed surfaces that can be absorptive. As with coating Kraft paper, attempting to seal the edges of treated Nomex is a process-control variable. One last word: Nomex has superior acoustical properties due to its excellent self-damping (tan delta) suppression bobbin resonances before they reach the cone neck joint.
IPT, Division of 3M — IPT’s CeQUIN and TufQUIN are well known and popular collar materials used by voice coil winders worldwide. CeQUIN and TufQUIN products have found acceptance with voice coil manufacturers for collars. Both materials possess good thermal stability and TufQUIN non-absorptive properties Quin-T ceramic paper, such as Tufquin-110, is another popular collar material. It offers good dimensional stability, ferrofluid compatibility, and it is compatible with high-temperature operation.
Minimum thickness for CeQUIN papers is 3 mils (0.08 mm). CeQUIN papers have been successfully B-stage coated by several companies both in the United States and abroad. They will withstand very high temperatures in processing.
TufQUIN papers, while not as high-temperature resistant as IPT’s CeQUIN papers, will withstand fairly high short-term temperature exposures. CeQUIN and TufQUIN are both used with high-performance B-stage coatings for collar applications. TufQUIN 110 offers a number of characteristics that make it attractive for use as a collar material as well as ferrofluid compatibility.
TufQUIN 110 is flexible and conformable, capable of high-temperature service through class H (180°C). Additionally, it has good physical toughness—high stiffness, tensile strength, and tear resistance, plus low moisture absorption—no need for coating or sealing with less than 0.05 mm the absorption of Nomex 110. Minimum thickness for TufQUIN papers is 2 mils (0.05 mm). TufQUIN Kb is a black version that is preferred by many voice coil manufacturers.
Thermal Shield non-woven polyphenylene sulfide (PPS) sheet is designed for use in applications requiring long-term exposure to high temperatures and resistance to chemicals, including ferrofluids. ThermalShield is not susceptible to hydrolysis and does not require baking out for dimensional stability. ThermalShield may be resin coated to enhance its performance. Thermal Shield is targeted as a drop-in replacement for the spunlace Nomex for collar applications. The thickness range for ThermalShield is a bit over 2 mils to 7 mils (0.38 mm).
ThermaVolt high-inorganic content paper was originally developed for use in high-temperature (Class 220 R), dry-type transformers. ThermaVolt has some thermal conductivity.
BONDEX, Inc. — Bondex offers aramid sheet materials used in electric motors as a replacement for spunlace Nomex. Bondex is available in a range of thicknesses and densities. Bondex is a high-temperature aramid paper with excellent acoustic properties for use in voice coil collars. It has high-temperature tolerance and withstands flame well. It has low-moisture absorption and is dimensionally stable. The thicknesses is 3 mils (0.08 mm) to 10 mils (0.25 mm).
Aluminum — For air-tight enclosures, such as autosound subwoofers or home theater subwoofers, the voice coil’s mechanical strength can be increased with a single layer aluminum collar. As with aluminum bobbins, expect an increase in eddy currents (and their secondary effects) if the magnetic structure does not use a copper cap or aluminum shorting rings. A layer of other collar materials may be added for all the reasons covered in this article.
The Collar Affects the Voice Coil and the Speaker
The lowly collar might be one of the least expensive components in a loudspeaker, but it provides many important benefits to the voice coil and to the speaker itself. In addition to improving the coil’s structural integrity and securing the lead wires, the collar can serve as a thermal insulator and may be used to improve the adhesion between the cone and the voice coil bobbin.
Additionally, the acoustical properties of the collar may be selected to influence the response of the speaker. Many materials are available for use as a collar but a careful understanding of the physical properties of these materials is required for optimum selection. New, innovative materials provide the designer and manufacturer with higher performance alternatives to commonly used collar materials.
Originally published by Voice Coil, May 2012.