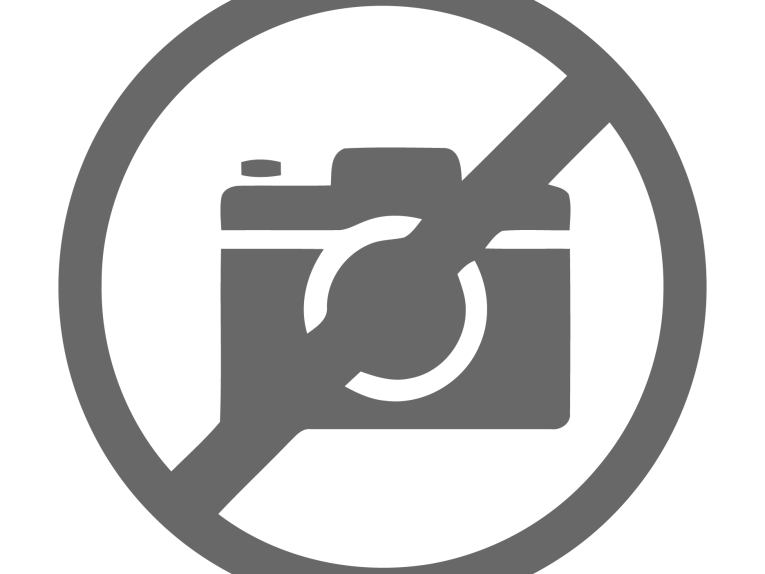
Modern electronics are demanding for micro speakers to be louder, smaller, full-range, and waterproof. These increasing demands have encouraged OBO Pro.2 to innovate advanced LSR (Liquid silicone rubber) micro speakers.
OBO Pro.2, part of the Concraft Group, has a fully vertically integrated LSR speaker value chain. We design, mass produce, and assemble LSR Speaker solutions all in our factory. We can offer proven acoustic solutions with our 5.4mm, 6mm, 11mm, 6x12mm, and 40mm, LSR speaker line. OBO Pro.2 also works with customers to make custom LSR micro speakers.
So, why LSR?
First off, LSR speakers use a superior assembly process. A traditional speaker will have its dome and surround centered, then glued together. Then the surround is centered with the frame and glued together. Multiple gluing and centering steps are slow, hard to automate, and allow for misalignment/imprecise gluing. Too much glue will make an overweight membrane, too little glue will cause a weak bond, and glue may run onto unwanted surfaces. Misalignment or bad gluing can lead to inconsistent SPL, distortion, and waterproof leaks.
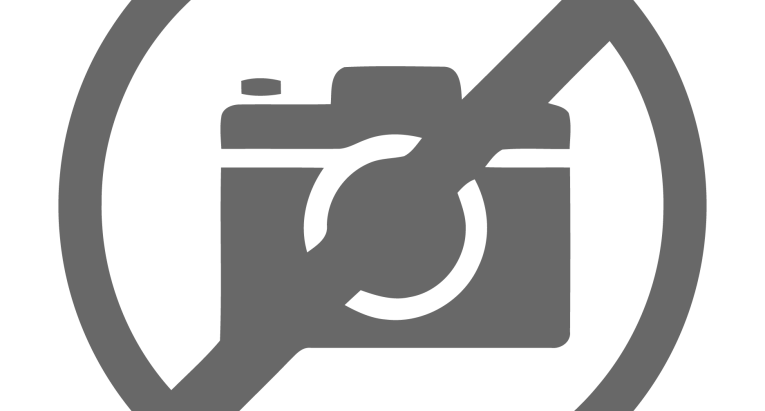
On the contrary, an LSR speaker’s dome and frame are fit inside a tightly machined mold cavity and are connected when LSR is injected to form the speaker surround — a one shot process. There is no glue involved and all tolerances are controlled by the precise machined tooling. This entire process is automated. Our result is an LSR surround that is precise and seamlessly bonded to the dome and frame of the micro speaker. Improved bonding consistency and concentricity creates consistent frequency responses (within 1dB) and lower THD.
It may be clear by now, but LSR speaker production is centered around tooling. Thus, a successful LSR speaker development requires resources and capability for precise and rapid tooling development. OBO has these unique resources and capabilities; OBO has produced precision tooling (0.002mm tolerance) for three decades and has rapid tooling modification capabilities (2-3 day turnaround). Tooling is a great strength of OBO and this allows us to confidently modify and innovate LSR designs. OBO can produce a working speaker 3-4 weeks after tooling production.
LSR surrounds have material properties that increase acoustic performance. Liquid silicone rubber is soft and flexible, with a Young’s modulus much smaller than typical PET or PEN materials. The flexible LSR allows for larger excursion in similar speaker sizes. This increased excursion generates increased bass response from LSR micro speakers — something traditional micro speakers struggle with. This is important because the cell phone, like many modern devices, is staying the same size but requiring greater battery power. When batteries increase in size, other components, like speakers, are pushed into smaller footprints. LSR speakers will address this need for smaller sized speakers that maintain full range capabilities.
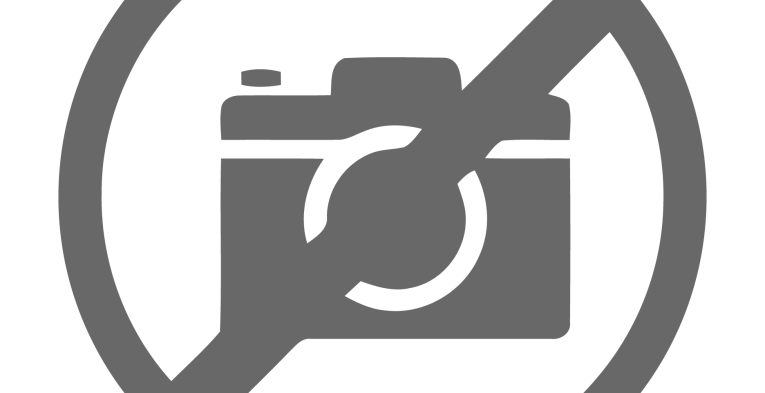
The large excursion limits of an LSR surround also allow lower frequencies to be played with the surround far from its excursion limits. When traditional speakers are straining to squeeze out bass response, they are operating close to their excursion limits. Operating near excursion limits will put greater long-term strain on the diaphragm and expose irregularities in mass or thicknesses or magnetic fields. These irregularities all contribute to nonlinear motion of the speaker, inducing rocking modes and rub and buzz. LSR grants large excursion limits, explaining how, even at lower frequencies, LSR speakers maintain linear motion and low distortion. In the figure below, we can see the LSR’s increased low end response and lower distortion in low frequencies.
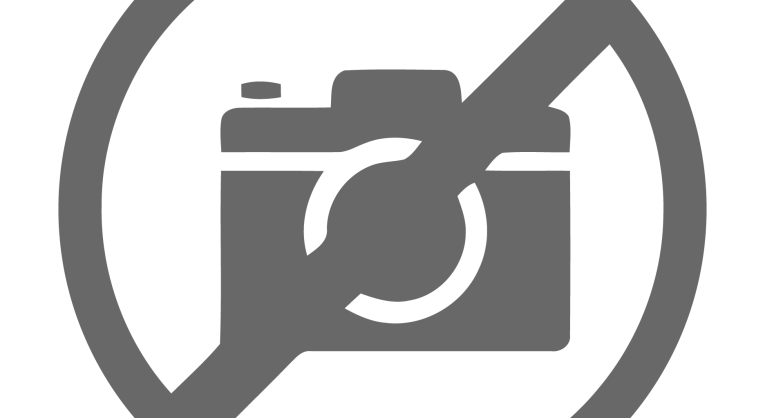
You can also change the sound characteristics and SPL of an LSR speaker with quick tooling modifications. Tooling modifications allows different LSR surround thickness and cross-section shape. This means there is no more need to source down new diaphragms or change the speaker’s assembly as you would need with a traditional speaker. Simple tooling modifications allow the customer to customize the LSR surround for a desired FR and THD.
LSR surrounds offer even cheaper methods to modify frequency response. Simply changing the hardness of the LSR will have substantial, but controllable effects on the speaker’s frequency response. As shown in the below figure, one may opt for a batch of 40 Shore Hardness LSR speakers with more bass and another batch of 70 Shore hardness with a more even response. This is a quick and inexpensive change, requiring no change to the speaker components or tooling.
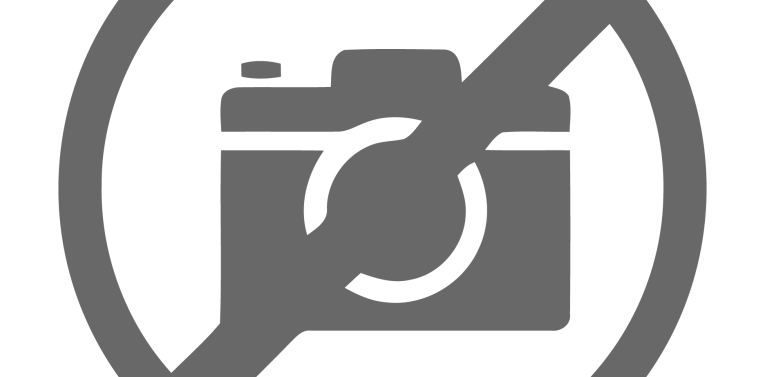
LSR surround injection molding also takes advantage of OBO’s automation expertise. Our Kunshan factory of 121,809m2 has experienced automation engineers constantly maintaining and designing automated production lines. Our automated production lines will help produce individual components and fully assemble your product. Pictured below is an automated speaker box production line.
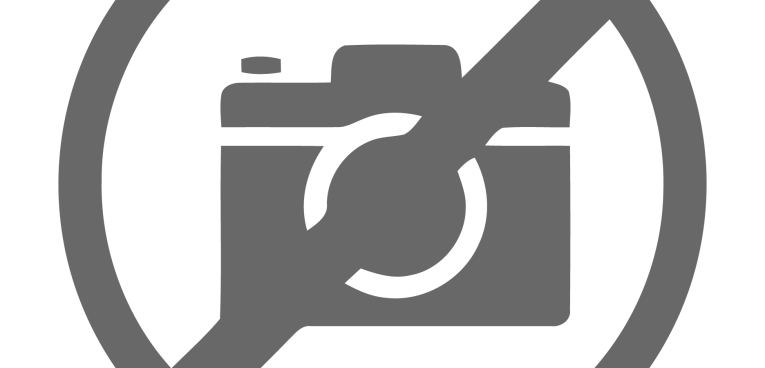
OBO will help you design, produce, and integrate audio solutions from the speaker driver to a finished speaker module.
Please feel free to reach out to our sales at sales@obopro2.com or find us on www.obopro2.com