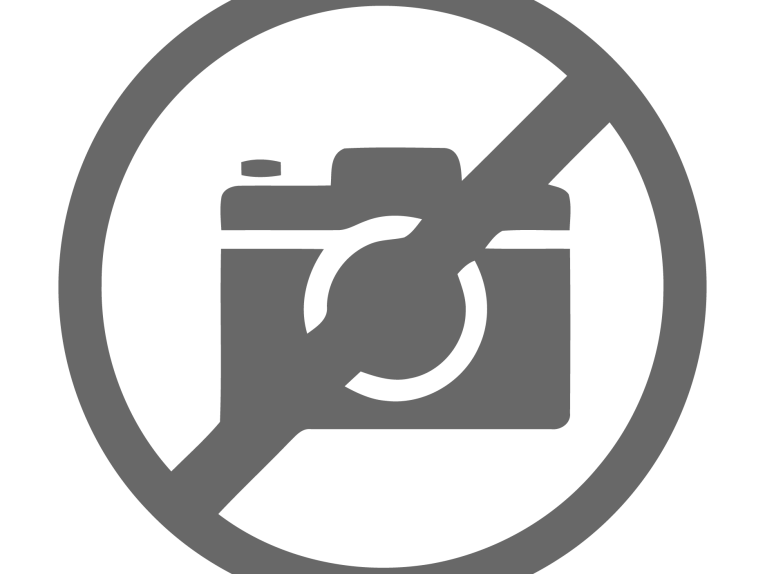
How does a product get from the obvious problem to these nebulous solutions described on the boxes? What are the solutions or techniques to protect devices from liquid damage? Further, what are the strengths and weaknesses of each solution?
Potential Risks
Going into the elements, our devices are exposed to a plethora of conditions from the steam in bathroom to cooking liquids (e.g., oil, soda, and alcohol in the kitchen) and to our bodies where our body perspiration is quite corrosive. The variety of elements that can cause damage to our expensive electronic accessories is quite vast. Further, the variety of solutions that can be used to protect devices from the inside and out are also extensive.
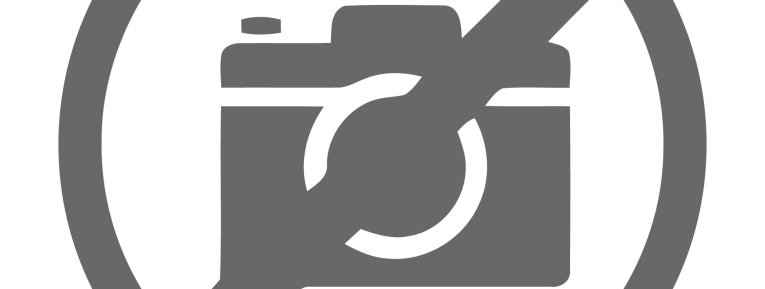
All these solutions adhere to the ingress protection (IP) scale in regard to water and dust protection. There are other tests, such as salt mist and sweat testing with artificial sweat (!!) but there is no standardized scale to represent the protection levels in this space. For example, one company might mark the box for its device as sweat proof after a 48-hour salt mist test and another brand with the same box marking might require submersion in artificial sweat solution.
That said, the methodologies to pass these tests or protect the devices can be divided between mechanical and coatings. The mechanical can be subdivided into barriers and gaskets, while we can partition coatings into conformal and ultra-thin.
Mechanical Safeguards
For the mechanical approach, there are gaskets, and barriers. With gaskets, there are issues with the durability of the material used. As well, gaskets require precise tooling and good quality material to maintain durable seals. For barrier protections (e.g., plastic housings), the quality of the plastic resin as well as the accuracy of the tooling are factors. Some materials such as nylon, ABS, and PVA have the affinity to absorb moisture.
The time between molding and ultrasonic welding increases the likelihood of pores/bubbles developing from trapped moisture during the ultra-sonic welding process. In most audio manufacturing operations, the plastics sub-supplier factories are operating in south China’s humidity and most companies do not vacuum pack the plastics after molding. Therefore, they absorb moisture and acquire deformities and/or imperfections by the time they arrive for the ultra-sonic welds in final assembly. [1] These gaps or gaps from inaccurate tooling will over time allow liquids into your devices which leads to failures.
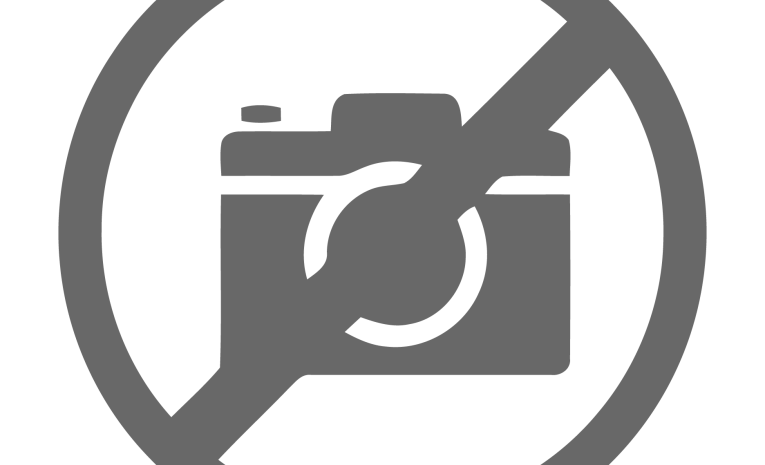
A classic conformal coating is potting where electronics are literally submerged or sprayed/sputtered with a chemistry (see Photo 1). The solutions include materials such as urethane, silicone, acrylic, and so forth. They are relatively thick in micrometers and effective for moisture protection but they prevent heat exchange and are not re-workable. These techniques are popular in low-tech devices (e.g., refrigerators and other appliances). Also, they are popular in military and industrial applications. Relative to acoustic applications, these solutions are not feasible for transducers or microphones as they add far too much mass to the diaphragm material.
For ultra-thin coatings, there are physical vapor deposition techniques using vacuum plasma to deposit chemistry in a machine or plasma enhanced vapor chemical deposition (PEVCD). These coatings have two subsets based on the applied chemistry: Fluoro and Parylene.
First are the Fluorocarbon-based solutions applied with PEVCD, these are truly nano-scaled coatings in the 200 to 300 nano-meter (nm) range. These coatings are capable of IPx2 to IPx4 maybe IPx5 protection, and they can be delivered by brands such as P2i (UK) and FavoRed (CN). The process is typically 45 minutes to an hour in length.
There are advances that claim IPx7 but then the process time jumps to 4 to 5 hours. Some of the benefits with PEVCD are that the process can include PCBA cleaning for solder flux or other contaminant removal, and there is no curing needed post-coating. A major weakness is the batch processing in a chamber, which creates bottlenecks in production. Another major risk is with Lithium Polymer or gel pack batteries. The thin-membrane structure of these battery cells will expand and contract during vacuum processing, which can lead to shorts in the batteries.
Some weaknesses in acoustic applications include microspeakers and microelectromechanical systems (MEMS) microphones that are still subject to masking. Further, low-voltage data connectors require masking even with 300 nm coatings using PEVCD.
The second category is (slightly) thicker coatings deposited with PEVCD are called parylene. Companies such as Hz0 and SCS, both US companies, offer these solutions. They offer greater protection up to IP68. The coatings are very good at protection with a relatively thin profile of 3 μm to 25 μm. They are used a lot in military and some premium consumer electronics applications.
The major drawback is the cycle time multiplied by the expensive equipment required. The process cycle time ranges from 3 to 6 hours and the chambers are 1 m3 (35 ft3) at the largest and the equipment ranges from $250,000 to $500,000 USD (see Photo 2). Therefore, the process becomes prohibitive in high-volume production. Further, all connectors, contacts, and acoustic components typically need to be masked.
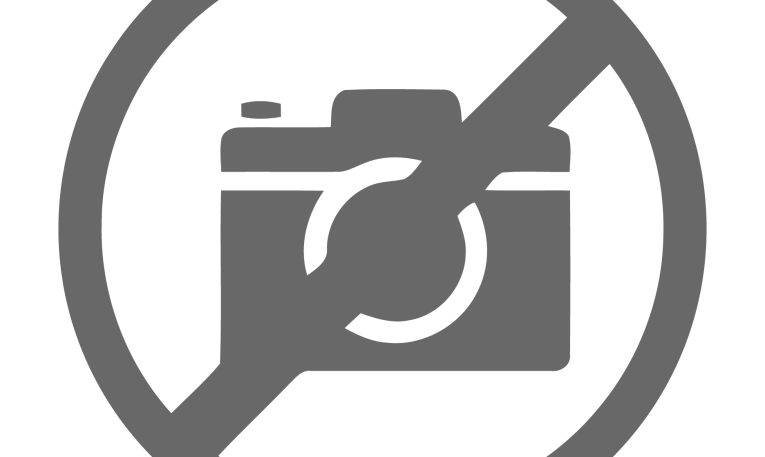
Finally, there is now a wet chemistry solution called NanoflowX from Naneon, which has headquarters in Los Angeles, CA. NanoflowX is an ultra-thin wet chemistry capable of protection up to IP68 (see Photo 3). The custom chemistry, which took 5 years to develop, has been tested against market leaders such as Dow and 3M with winning results. With a thickness profile as thin as 1 μm, NanoflowX can be deposited with dip, spray, or even a stepper for higher accuracy. Further, the entire process lasts just 5 to 15 minutes. The process is re-workable and very little masking is required. Next, there is no major barrier to entry with equipment costs so the solution is very scalable in production. This is incredibly useful for brands using multiple contract manufacturers. Specific to acoustic products, there is still a little masking requirement on microspeakers and MEMS microphones. Also, low-voltage connectors (e.g., data pins) require masking.
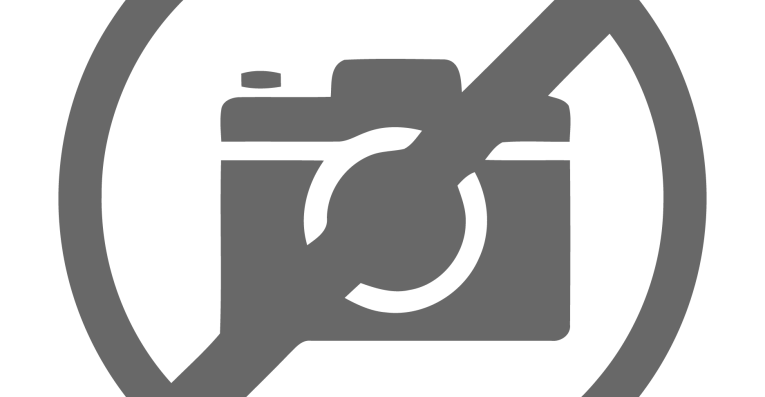
This article was originally published in Voice Coil, July 2020.
Reference
[1] M. J. Troughton, Handbook of Plastics Joining: A Practical Guide, Plastics Design Library, 1997, p. 44.