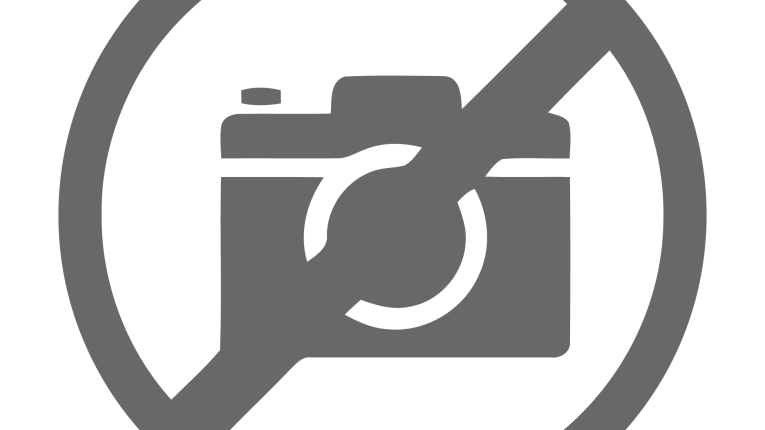
There is big news for speaker designers looking to refine their products’ sound quality through diaphragm treatments — and it's diamond coatings, or more specifically diamond-like-coatings (DLC), which is a process that I have personally watched mature over the last half-century.
Back in the 1970s, the Japanese speaker engineers at Matsushita, Pioneer, Yamaha, and others looked at high stiffness materials and began work with Beryllium and Boron. There were interesting papers, mostly “science projects,” discussed at industry events and even limited-edition flagship products produced. Yamaha had chemical vapor deposition (CVD) beryllium midrange and dome tweeters in its studio monitors, so did Pioneer with its TAD super-premium transducers. Boron, an esoteric non-metal element, was used by Pioneer and Matsushita (Panasonic Technics) for dome tweeters (and is still used in audiophile hipster phono cartridge cantilevers). The short version of the vapor deposition process was to use a tool on which particles were vapor deposited forming the part and then removed (or melted) from the form leaving the "egg shell."
These tweeter or compression driver domes were extremely vulnerable to cracking and shattering during assembly handling. But the reality is that the process essentially formed a part that while stiff, was very brittle and did not like to be mechanically shocked — not a good attribute for a vibrating speaker membrane! While boron can be a consumed supplement in small doses, in some forms and quantities it is toxic. Aside from boron, beryllium can result in a chronic beryllium disease (CBD), which is the scarring of lung tissue that may occur when beryllium is inhaled as dust or fumes (and can occur during grinding, soldering, or otherwise heating).
During the early 1980s the European Oerlikon Balzers, Inc. was researching and commercializing thin-film hardcoats for tooling, injection molding, and cutting tools for lathes. Hard coatings and stiff thin-film coatings on a metal substrate struck me as a solution for immunity to the fractures and shattering that stymied the Japanese R&D teams. Back then, 40 years ago, I had just started my consulting company and working with what was then a research team in Liechtenstein.
Thankfully, times have changed. Back then cigarette smoking was common, cars belched leaded gas fumes, and asbestos was common and used as a high temperature insulator (and voice coil collar material). That stuff is all long gone and mostly so are the boron and CVD beryllium diaphragms. No one wants to die for a couple of decibels up at 30kHz. Yes, foil beryllium diaphragms are still with us and are reasonably safe, but there are now REACH (Registration, Evaluation, Authorization, and Restriction of Chemicals) regulations in place for end-of-life disposal.
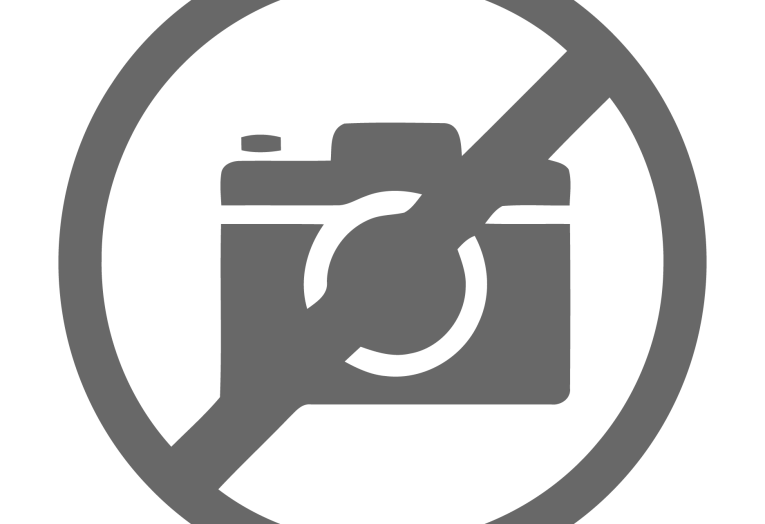
Diamond Diaphragms
Today, there are self-supporting synthetic diamond dome tweeters from Accuton, SEAS, which has its EXCEL diamond tweeters; and Bowers & Wilkins’ diamond tweeters. Yet self-supporting/no substrate diamond diaphragms are brittle and extremely fragile until final assembly. Even when assembled into a finished tweeter, the dome may sag or even collapse, and it takes little effort to shatter the dome.
Synthetic Diamonds and DLC
For a robust tweeter, headphone, earphone, or compression driver diaphragm that is best able to face the rigors and vibration of the acoustic world, one path to a long life is a thin-film coating on a substrate. But that is easier said than done as most CVD processes use microwave or convection heating at about 200°C for a few seconds. While carbon fiber is unfazed at 200°C, most carbon fiber binders are excessively degraded. Polymer films, such as PEEK and PEN, also lose integrity but the few parts that make it through the process unwarped are awesome and are limited edition successes.
There is now a state-of-the-art REACH-compliant PVD process that is well under 100°C from Oerlikon Balzers Surface Solutions (www.oerlikon.com). Specializing in hightech solutions designed for applications in growth markets, such as speakers, automotive, aerospace, energy, the tooling industry, and additive manufacturing. Applied by PVD, a vacuum-based process is used to deposit DLC coatings, also known as Amorphous Diamond-Like Carbon (ADLC). These very hard thin coatings increase the Young’s modulus and stiffness of compression driver and tweeter domes, headphone and IEM diaphragms. It is applicable on multiple substrates, such as aluminum, titanium, PEEK, PEI, PEN, PI, PSS, and composites thanks to the very low temperature (60°C to 100°C ) of the process and it does not add weight due to the very low thickness 1μm to 2 μm.
The beneficial properties of DLC film are its ability to change the sound velocity in the diaphragm. Just as with domes made of beryllium and boron, DLC domes have high stiffness but without toxicity issues. Increasing the stiffness causes the break-up frequency of the membrane to shift upward and increases the bandwidth of the loudspeaker while damping membrane resonances.
Costs
Finally, there is the topic of cost. A Beryllium 3" dome cost is typically $75 from the manufacturing source but adding DLC to both sides of a 3" dome substrate is about $5 to $15 (depending on quantities, etc.). Obviously a 40mm headphone driver would be a fraction of the cost.
DLC has wide application also for in-ear-monitors (IEM) but also TWS earbuds, headphones (the highly respected Campfire IEMs and TWS earbuds use DLC PEEK diaphragms), and there is a growing trend in thermoplastic film compression drivers that would be ideal candidates for DLC. For more information contact Bao Feng (Oerlikon Balzers Surface Solutions) by email here. VC
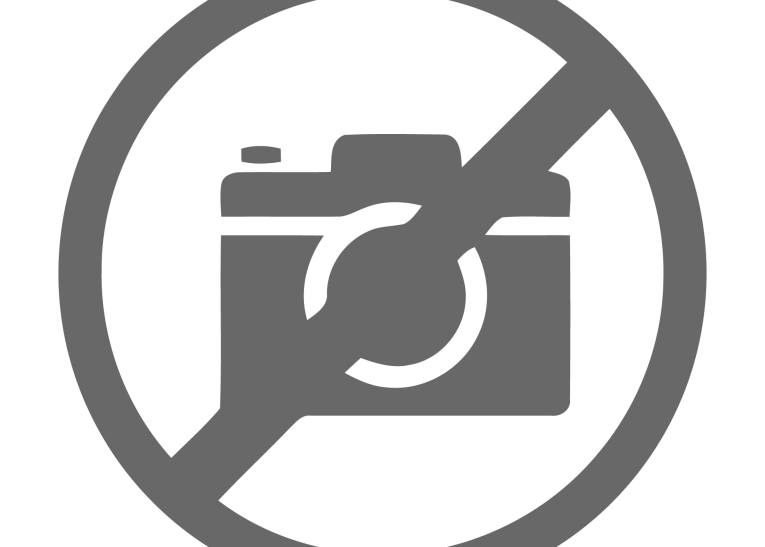