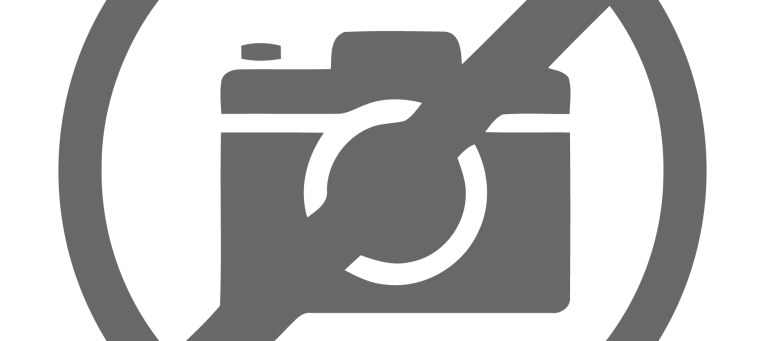
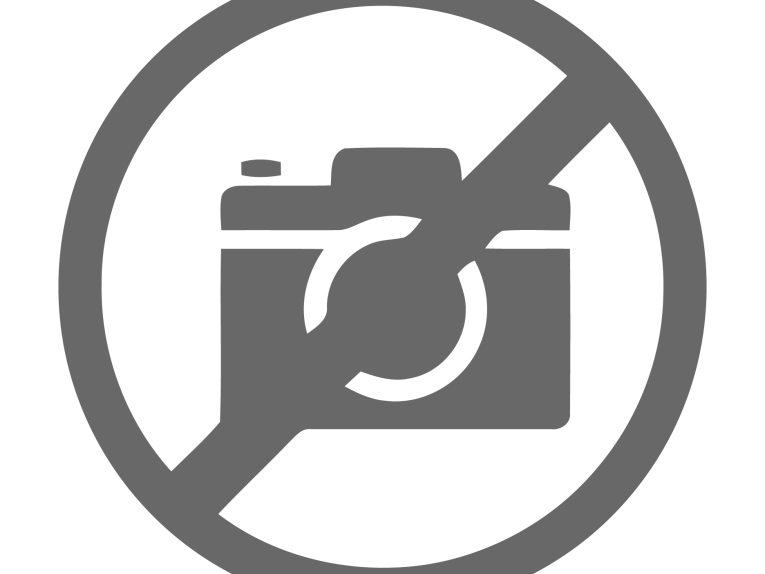
Oberton built its own 21,500 ft2 factory building in 2006 (see Photos 1–4). This company is probably more vertically integrated than a lot of pro sound OEMs, producing all the important parts (e.g., voice coils, diaphragms, metal parts, etc.) for all the low-frequency loudspeakers and high-frequency drivers in its own factory with 100% quality control. As a result, Oberton can guarantee the tolerance of 1” drivers to a ±1 dB frequency response in range 2,000 Hz to 15,000 Hz compared with the reference driver of each model.
Photo 5 shows the driver and the horn that Oberton supplied for this month’s Test Bench explication. It is the company’s recently released ND72CT/HB 1.4” compression driver along with the H-1464 1.4” cast aluminum 60° × 40° constant directivity horn. The ND72CT version of the ND72 has a 72 mm (2.85”) diameter two-layer voice coil with copper-clad aluminum wire (CCAW) wound onto a Kapton former, driving a unique cotton composite diaphragm and polycotton surround (see the dome on the right shown in Photo 6) — the entire assembly is field replaceable.
According to Oberton, this dome has a “soft” sound and is highly recommended for use in stage floor monitors. However, the ND72 also has an alternative dome (see the dome shown on the left in Photo 6), named the Hybrid Dome, which turns the ND72CT into the ND72HB. The Hybrid Dome is a combination of carbon composite (the gray material) diaphragm with a center cotton composite “patch” that reduces break-up modes. The result is a dome with excellent stiffness and good internal damping making the subjective sound quality, again according to Oberton, that avoids the metal sound of some titanium domes. Note that all the testing for the Oberton ND72 was with the Hybrid Dome (ND72HB) unless designated otherwise.
Other features include a FEA-optimized neodymium ring magnet motor structure, a continuous rated power handling of 100 W with a peak power handling of 200 W, a 1 kHz recommended minimum crossover frequency (second-order high-pass filter), heatsink fins on both the front and the back of the assembly, 109 dB sensitivity, plus color-coded chrome push terminals.
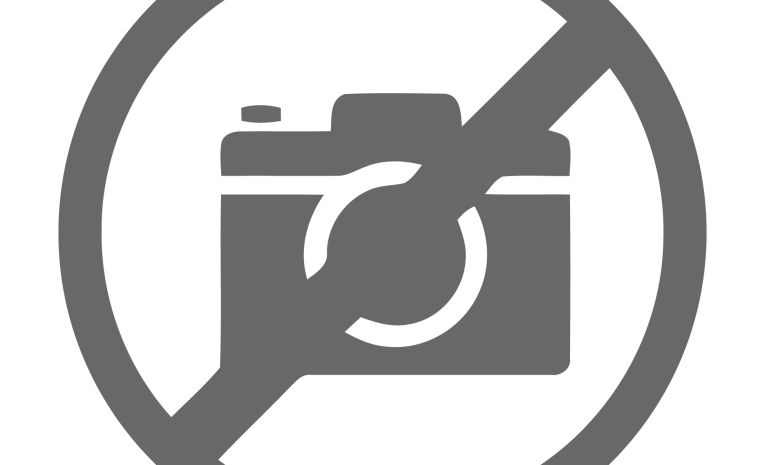
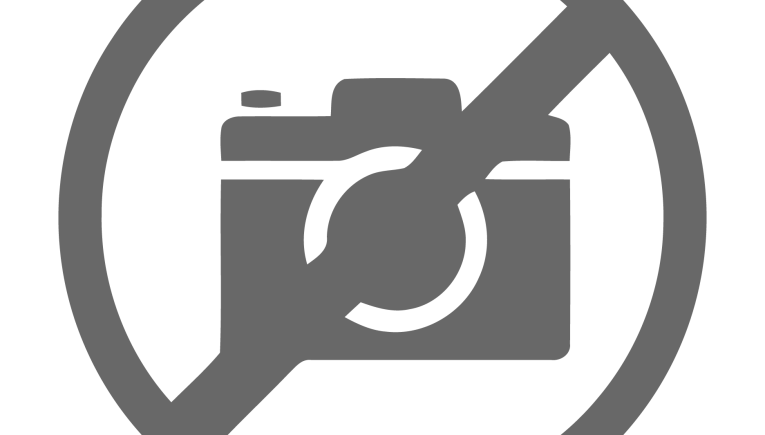
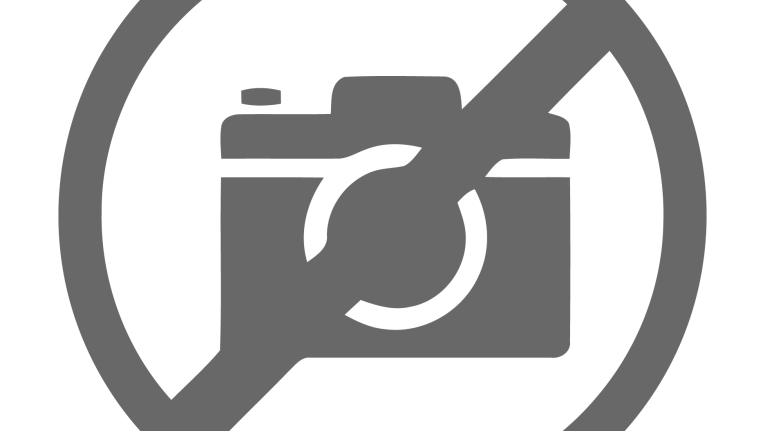
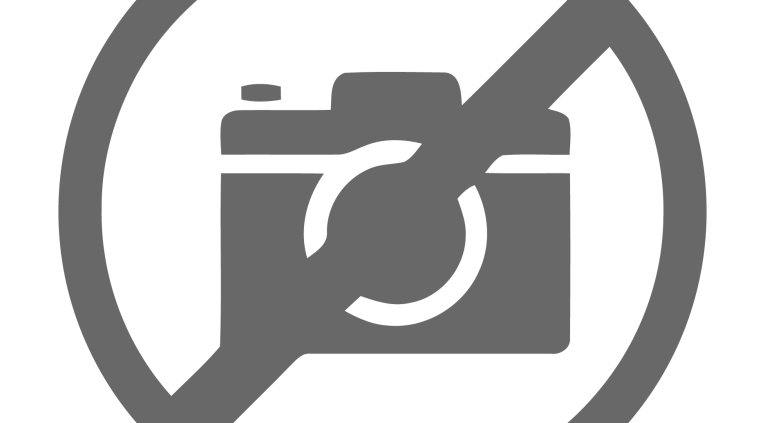
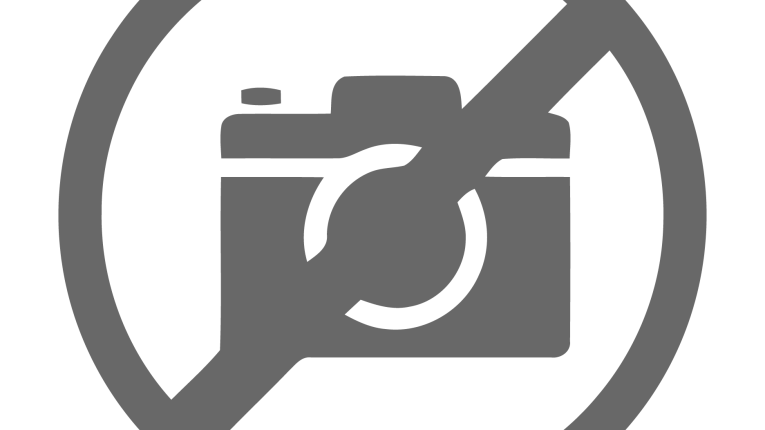
I began the testing using the LinearX LMS analyzer to produce the 300-point stepped sine wave impedance plot shown in Figure 1, with the solid black curve representing the ND72HB mounted on the H-1464 horn and the dashed blue curve representing the compression driver without the horn. With a nominal 16 Ω impedance (the ND72 is also available in 8 Ω), the ND72HB had 9.72 Ω DCR (Re), with a minimum impedance mounted on the H-1464 horn of 11.59 Ω and at 3.6 kHz.
For the next set of SPL measurements, I free-air mounted the Oberton ND72HB/H-1464 combination without an enclosure and measured both the horizontal and vertical on and off axis at 2.0 V/0.5 m (normalized to 2.83 V/1 m) from 0° on-axis to 60° off-axis using the LoudSoft FINE R+D analyzer and GRAS 46BE microphone (supplied courtesy of LoudSoft and GRAS Sound & Vibration).
Figure 2 displays the on-axis frequency response of the compression driver/horn, which is relatively smooth with no major anomalies from the 1 kHz recommended crossover frequency to about 15 kHz, with the typical downward sloping response of a constant directivity horn. The breakup mode for the damped carbon composite diaphragm peaks at about 16 kHz.
Figure 3 shows the 0° to 60° on- and off-axis response in the horizontal plane. Figure 4 shows the normalized horizontal plane response. Figure 5 shows the 180° horizontal polar plot (in 10° increments with 1/3 octave smoothing applied), generated by the CLIO Pocket analyzer and accompanying CLIO microphone (courtesy of Audiomatica SRL).
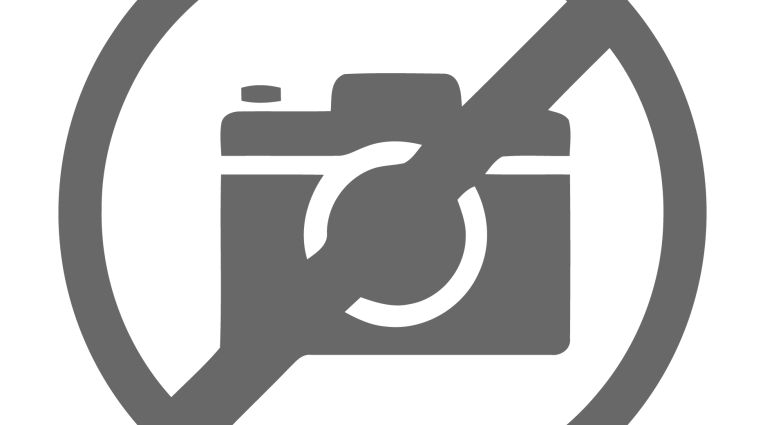
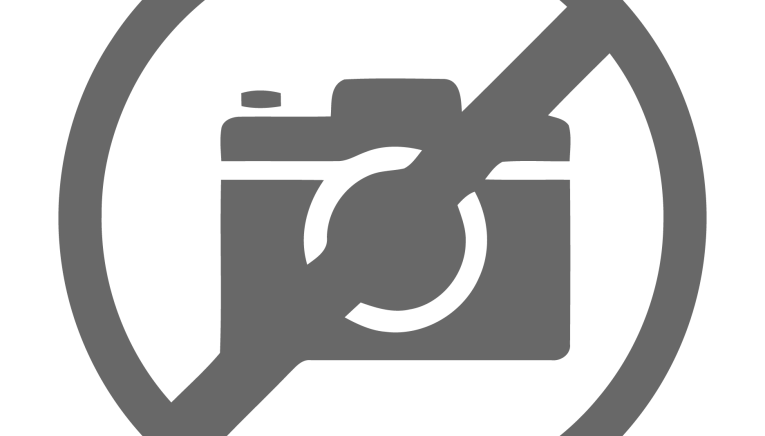

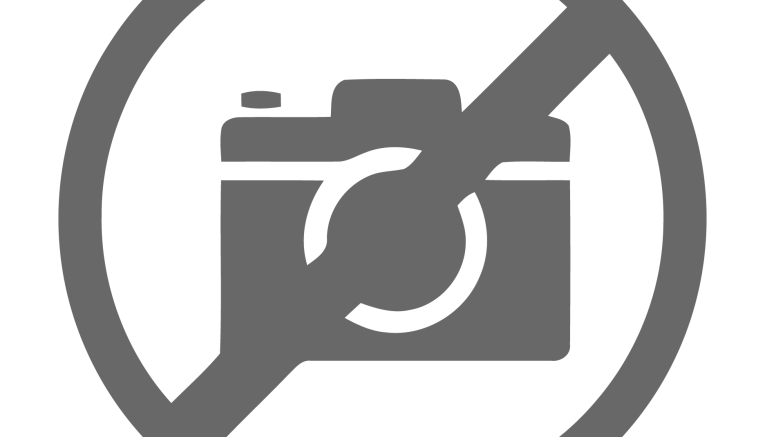
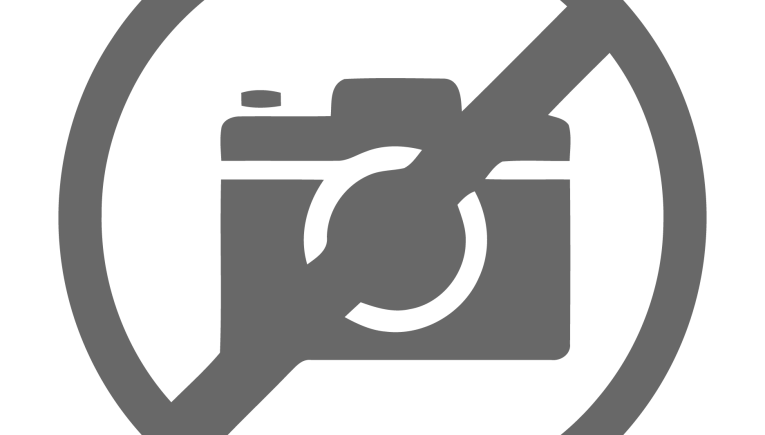
Rotating the horn 90° to capture its vertical plane response resulted in the vertical plane 0° to 60° on- and off-axis response shown in Figure 6. Figure 7 shows the normalized version. Figure 8 shows the 180° vertical plane polar plot (also with 10° increments with 1/3 octave smoothing applied), generated by the CLIO Pocket. Last, Figure 9 illustrates the two-sample SPL comparison showing the two Oberton ND72HB compression driver samples to be closely matched within 0.25 dB or less throughout the entire operating range of the transducer except for a ±1 dB area from 8 kHz to 11 kHz.
At this point, I changed out the Hybrid Dome HB carbon composite diaphragm for the cotton composite CT dome and ran another comparative sweep. Figure 10 depicts the on-axis frequency response comparison of the HB and CT domes.
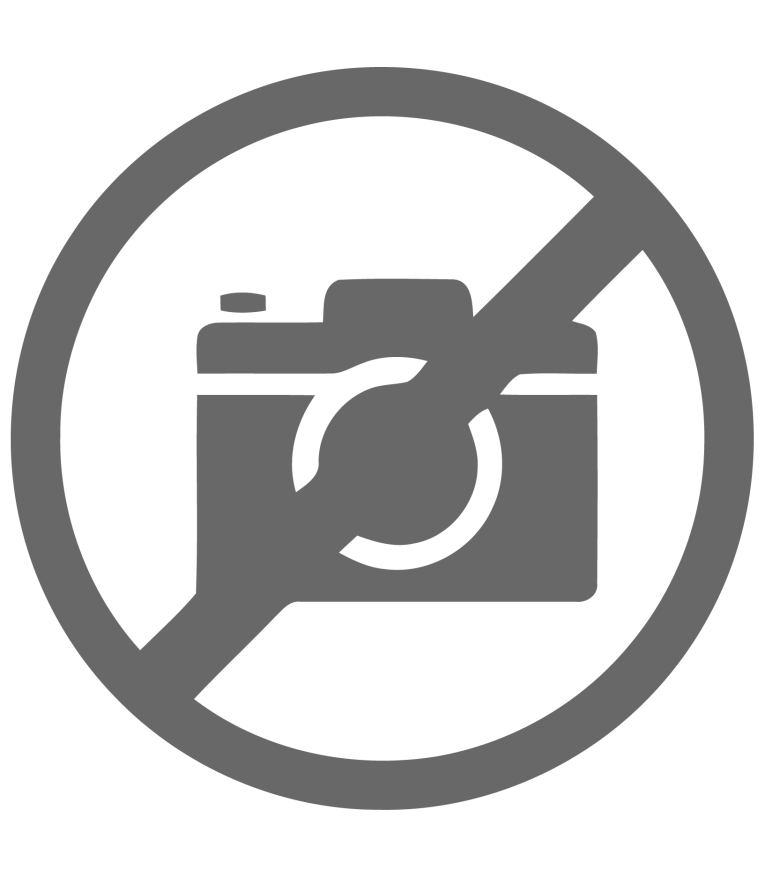
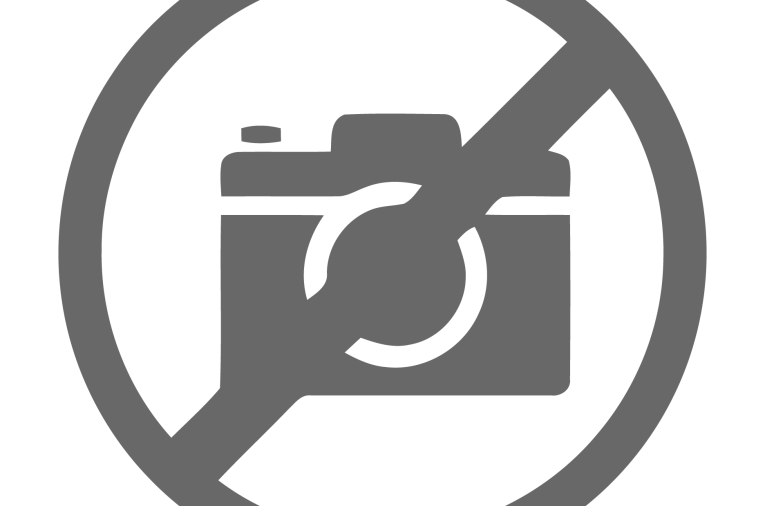
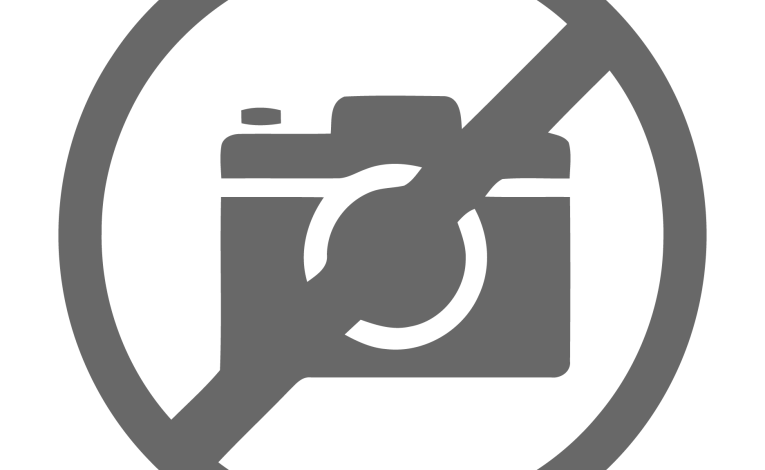
For the remaining series of tests, I again set up the Listen AudioConnect analyzer and 1/4” SCM microphone (provided by Listen, Inc.) to measure distortion and generate time-frequency plots. For the distortion measurement, I again mounted the Oberton ND72HB/H-1464 combination in free-air in the same manner that I used for the frequency response measurements, and set the SPL to 104 dB at 1 m (2.37 V, determined by using a pink noise stimulus generator and internal SLM in the SoundCheck 17 software). Then, I measured the distortion with the Listen microphone placed 10 cm from the mouth of the horn. This produced the distortion curves shown in Figure 11.
Following this test sequence, I set up SoundCheck 17 to generate a 2.83 V/1 m impulse response curve for this driver/horn and imported the data into Listen’s SoundMap Time/Frequency software. The resulting cumulative spectral decay (CSD) waterfall plot is given in Figure 12. Figure 13 shows the Short Time Fourier Transform (STFT) plot.
When you review all the objective data I took on the Oberton ND72 compression driver and H-1464 horn, along with the obvious build quality you can see in the photos, Oberton is clearly a very competent OEM and provides another place to shop for high-quality pro sound transducers. For more information about the ND72HB, ND72CT, and Oberton's complete line of neodymium and ferrite cone, coaxial, and high-frequency drives, and its line array drivers, tweeters and horns, visit www.oberton.com. VC
This article was originally published in Voice Coil, January 2020.