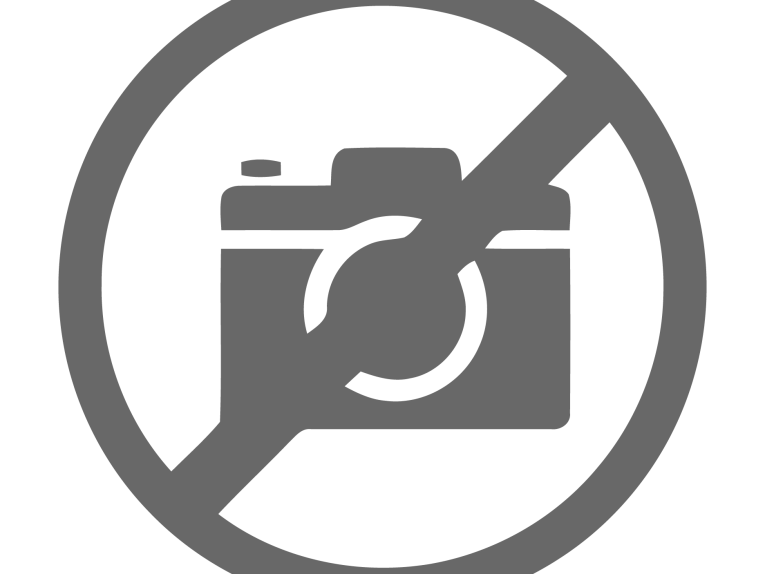
Enclosures need to provide a rigid structure to support the drivers with minimum panel resonances. No matter how much effort is spent on the loudspeaker driver design, the enclosure characteristics are still a significant factor in achieving smooth response, controlled tight bass, and a defined stereo image. I should also add that it is necessary for mundane requirements, such as weight, structural integrity, and in some situations, even weather resistance.
The contribution of enclosure materials on perceived overall product quality as well as sonic clarity is often ignored in the design and the specification of consumer audio products. But whether the product is a dishwasher, an automobile, a cooktop ventilation hood, or in more familiar products (e.g., Bluetooth speakers, conference phones, soundbars, or smart speakers), the suppression of rattles, creaks, and buzzes are core considerations in user-experience satisfaction. Noise, vibration, and harshness are not just distracting but they tend to create more wear and tear than quiet moving parts.
Wood Enclosures
Wood and wood particle board cabinets are traditionally used for bookshelf, tower, and in larger speakers, for sound reinforcement. Low- to mid-price bookshelf boxes are typically medium-density fiberboard (MDF) that are vinyl wrap-covered and “groove folded” out of a larger sheet. The grove-folding process cuts a V-groove into the wood, down to, but not through, the vinyl covering.
A bead of glue is dispensed into the V-groove and the enclosure is miter-folded into a box shape. Conventional particle-board boxes are inexpensive, readily available, and a known commodity. Most of us acknowledge that the typical MDF has good acoustical qualities but curved and shaped parts with this type of construction add greatly to the cost, along with the high weight and bulk of MDF thick-wall construction. MDF just does not lend itself to thin unobtrusive soundbars, let alone smart speakers or in-walls.
Over the years, there has been great interest in finding alternatives to wood enclosures. The ideal material should be as strong, light, and thin as plywood, and as easy to work with as particleboard. Simplified construction is another consideration such as moldable materials that eliminate joint assembly and enable rounded edges and shaped front baffles for time alignment, waveguides, as well as for aesthetic flexibility. Dramatic enclosure styling that combines unique materials and forms takes engineering and marketing courage, but the rewards can be great.
I prepared this report while attending the 2020 National Association of Music Merchants (NAMM) musical instrument, pro-sound and pro-sumer (DJ and karaoke stuff) show. All the line array speakers are still very much plywood construction, while mobile-powered DJ and band speakers are injected plastic. Enhanced materials and alternative constructions are now reaching the market and worth a look — and that is the big news in this report.
Today, in large permanent-install and touring sound speakers, the wood is mostly cut on CNC and associated automated processes. Yet once the sawdust settles, it still takes a week for time-consuming box assembly, bondo patching, sanding, and primer coating, followed by the additional steps of painting or application of truck liner, fiberglass, or other coatings.
In the distant past, attempts at composite construction resulted in some painful initiatives with awkward procedures for attaching drivers to honeycomb panels and joining panels. After field use, patching damaged panels were problems not easily nor inexpensively resolved.
Composites
With the ongoing advances in composites construction for aircraft, boats, and automotive, it is time for us to take another look. Layup of fiberglass and carbon fiber weaves and then infusion with a thermoset resin was time consuming, required skill, and come with some liabilities (e.g., VOC fumes and high flammability). Thermosets require cooking, usually in autoclaves (large ovens) to cure the epoxy resin binders. Hand layup yields only a couple pieces off the wood tools per day.
Compression molding — with a positive and negative tool using sheet molding (SMC) — is quicker with a couple of parts per hour, but post-tool secondary operations are still needed. A new breed of thermoplastic composites avoid the autoclave ovens previously required for curing thermosets. With thermoplastics, the sheet is preheated and then compression molded, enabling a finished five-sided ”tub” in 10 minutes that just requires the baffle mounting. The enclosure will have a slight draft for removal and this shape enables manufacturers to nest the tubs when shipping them from where they are fabricated to the assembly warehouses. In pro sound, there is often some customization, such as adding the hardware to the components on the baffle and this entire assembly chain lends itself to an efficient solution.
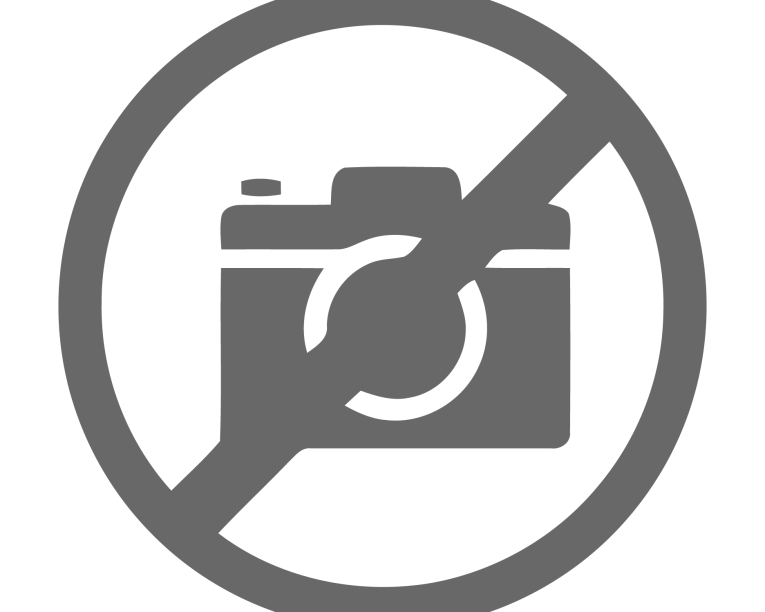
Plastics
Plastics dominate consumer products today. The usual injection-molded plastic thin-wall construction found in today’s soundbars, in-wall speakers and low-cost home theater systems are marginally adequate. Most audio engineers are unhappy with the hollow, buzzy sound that comes from plastic speaker enclosures. Yet, plastics enable stylish shapes with excellent consistency with an established supply chain and design rules. But from inexpensive resins to mid-grade ABS, and even the stiffer blends of polycarbonate+ABS, cabinets still have high levels of breakthrough. This is the speaker’s backwave sound energy passing right through the enclosure shell.
Higher sound transmission loss is the measure of how good a barrier the enclosure is to prevent sound from passing outside the enclosure. When driven hard, cheap plastics contribute too much of their own “self-noise” (rattles and creaking (stress) noise, degrading sound quality.
Injection-molded, thin-wall lightweight plastics provide designers with more flexibility to achieve aesthetic and efficient assembly goals, but at the expense of sonic integrity. We are faced with cheap plastic soundbars made of flimsy thin-wall plastic construction and table radio sound. Perhaps large-screen TVs provide enough distraction from the lack of sound quality, but Bluetooth speakers, in-wall and ceiling speakers, headphones and earphones, and smart-speakers are typically injection-molded plastic. ABS, HIPS, PC, Poly, and other plain materials dominate today’s speaker enclosure products.
Attributes that are important to the factory when considering new materials include injection-molding cycle time, compatibility with existing tooling (if the springback shrinkage is different than the existing plastic the tooling will need modification), flow in the tooling, moisture absorption (drying time in the hopper), and material cost per part. Other issues range from painting (polypropylene has good attributes but there is a reason that glue bottles are made from poly — it is hard to stick to or metalize).
Plastics with carbon or other conductive fill can block antenna reception. For the product managers, considerations such as surface finish, impact resistance, temperature tolerance, and acoustics must be taken into account. Chemical resistance is important if the product will be exposed to sweat — such as in wearables — and even tougher are detergents used to clean up.
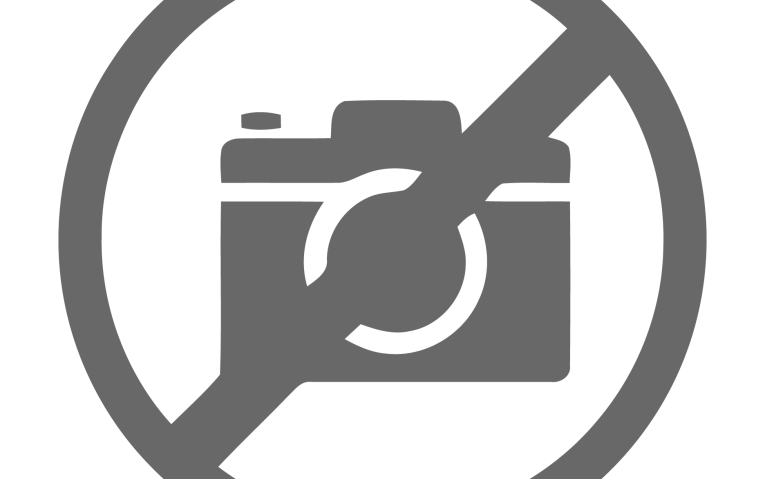
Better Plastics for Acoustical Applications
There are a half dozen injection-moldable plastics that are better than the usual incumbents, such as high impact styrene (HIPS), Acrylonitrile Butadiene Styrene (ABS), and PolyCarbonate (PC). PP (polypropylene) is low cost and offers decent acoustic characteristics but is tough to paint and PP parts are not too receptive to bonding together nor with other materials. There is a reason why most glue bottles are PP as it is tough to get anything to stick to it but there are workarounds for PP, including primers and other treatments. PP can be compounded with color so primers and painting is not required. Aside from finishing and gluing, PP is not stiff and requires thicker walls.
One enhanced PP is Symbio from Sappi. Sappi invented a new cellulose reinforced polypropylene composite consisting of virgin polypropylene and treated cellulose with increased stiffness for the same weight and wall thickness as untilled PP, but with higher damping (tan delta). Sappi Symbio is available as granules for injection molding from 20% to 40% cellulose. It is even possible to injection mold a subwoofer enclosure from medium wall thickness Symbio. Symbio PP can be reground, recycled or burned for energy. Pricing of Symbio is a modest premium over basic polypropylene and ABS.
Eastman Chemical has two thermoplastics with higher damping than polycarbonates and ABS. Its Tritan copolyester has a good appearance, clarity, toughness, hydrolytic stability, and heat and chemical resistance. It is free from BPAs (plasticizers), so contact with skin (e.g., through use of earphones or from food) is not an issue and even the mold release is derived from vegetable-based sources.
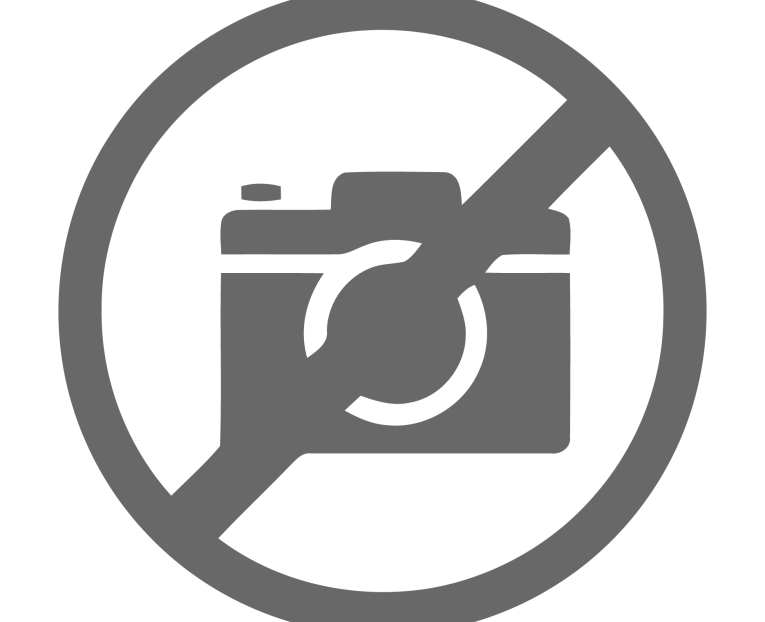
Eastman TREVA is a cellulose-based engineering bioplastic that offers both superior damping and reduced environmental impact. TREVA is chemically resistant, dimensionally stable, and has excellent flow, and it is BPA-free. Eastman undertook acoustic testing of molded in-ear monitors using cumulative spectral decay (CSD) 3D waterfall and total harmonic distortion (THD) along with an expert panel of listeners to evaluate the role of materials on resonance, distortion, and perception sensitivity. Eastman’s long history in creating polymer resins from cellulose comes from its 140 years of film development.
ABS/PA
INEOS is a spin-off of materials science giant BASF. INEOS Terblend stabilized ABS/PA (PA=polyimide) blend with enhanced dimensional stability, rigidity and high flow ability. Various application-specific variants of Terblend include glass fiber reinforced, and UV resistant for outdoor speakers.
Thermosets and Thermoplastics
Thermoset and thermoplastic resins have very different properties and in consumer electronics, thermoplastics have the lion’s share of the market. Think of thermoplastics (HIPS, ABS, PC, PP, nylon, etc.) as being similar to butter—butter can be melted and cooled multiple times to form various shapes. Thermoplastics are typically injection-molded into shaped parts although thermoplastics can be the binder for woven glass, Kevlar, carbon fiber and tapes for compression molding.
While thermoplastics can be remelted back into a liquid, whereas thermoset plastics are cured into a permanent solid state. Thermoset plastics contain polymers that cross-link together during the curing process to form an irreversible chemical bond. The cross-linking process eliminates the risk of the product remelting or warping when heat is applied. Once the final state is achieved, any additional heat beyond would lead to charring.
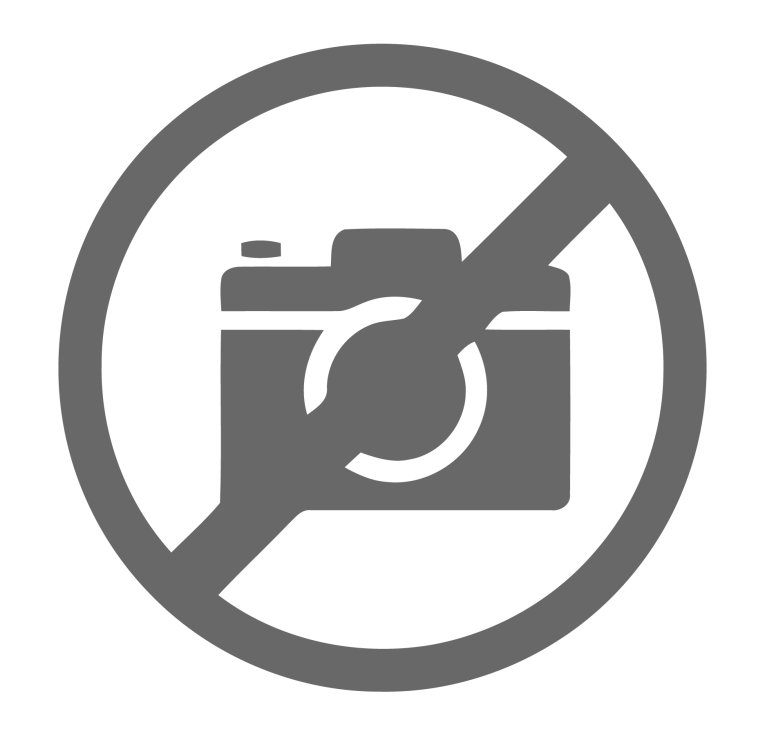
Bulk-Molded and Sheet-Molded Thermosets
Bulk-molded compound (BMC) composite (comprised of glassfiber, talc, mica, etc.) can be molded into enclosures. BMCs were traditionally compression-molded in a positive and negative tool with curing times longer than thermoplastics. BMC offers good acoustic performance, in part because of the high-density material and easily molded ribs, making it practical for rounded edges and contoured baffles. Injection-molded BMCs are also an option (with some modification of fillers).
Globe Plastics is a well-established fabricator of BMCmolded speaker enclosures, horns, and other parts, and its products are polymer materials, has addressed the main issues surrounding the production and use of composites — cost-effectiveness, scalable manufacturing of a high-performance, sustainable material. The material has extreme temperature tolerance and is weather resistant enough for speakers permanently installed outdoors.
Over the years, touring sound speaker engineers, crazed with the design requirements for huge line arrays, have looked to carbon fiber composites for rigid, lightweight, and well damped enclosures. This construction was a nightmare for joints and speaker and hardware attachments.
Another advanced thermoplastic composite sheet for compression molding is Stylight. Developed by INEOS Styrolution, Stylight is an aesthetic and structural thermoplastic composite for smart speakers and soundbars as well as larger enclosures. Stylight is a thermoformable sheet comprised of two key components — a fabric (e.g., woven carbon fiber or woven glass) and a resin (e.g., styrenic copolymers) for enclosures. While the fiber fabric plays a key role in the material’s mechanical performances, the polymer matrix has a great influence on the part surface aesthetics.
Stylight offers low surface waviness high-gloss surfaces direct from the molds, but it is also easy to paint or decorate with foils. The translucency of natural StyLight enables backlighted surfaces or a “carbon fiber look.” Stylight is a new combination of aesthetic and structural stiffness, low weight, and cost-efficient production.
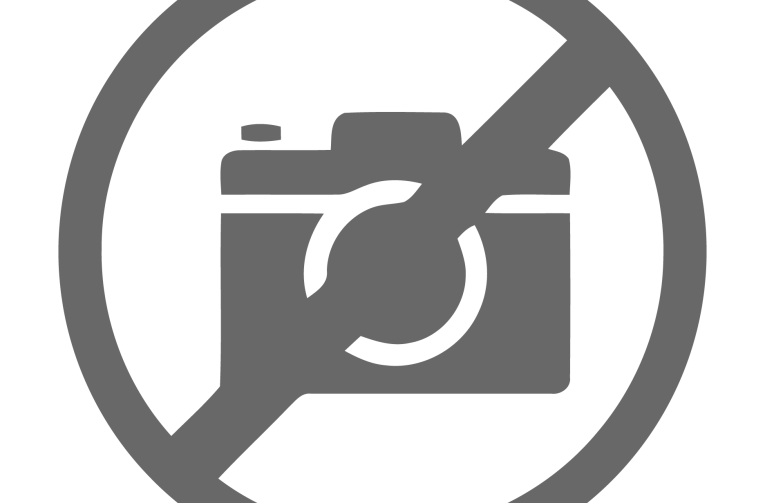
Maezio is a new solution, a next-generation continuous fiber-reinforced thermoplastic composite (CFRTP) from Covestro. Made from carbon or glass fibers with polycarbonate (PC), thermoplastic polyurethane (TPU), or other thermoplastic resin binders, Maezio products are made as unidirectional reinforced tapes and sheets for lightweight, durable formed sections of thinner wall construction. For deep high aspect ratio parts such as smart speakers, chopped Maezio can be injection molded (from manufacturing waste from sheets).
Covestro, formerly Bayer Material Science, is a world-leading supplier of high-tech polymer materials. Covestro has addressed the main issues surrounding the production and use of composites—cost-effectiveness, scalable manufacturing of a high-performance, sustainable material. Maezio works with existing thermoforming compression molding tools at high yield rates and low cycle times—a feature that can be vital when manufacturing scales are in the range of millions of parts per year. Other production technologies appropriate for Maezio include hybrid injection molding, automated UniDirectional tape laying, and automated fiber placement.
Enhanced Plastics
With many industries from automotive to kitchen appliances craving less “creaky” plastics, the speaker designer now has new acoustically enhanced plastics. Many of these new formulations work with existing tooling and product designs. For sound reinforcement applications the new thermoplastic composite compression molding sheets promise “finished enclosures in minutes”.
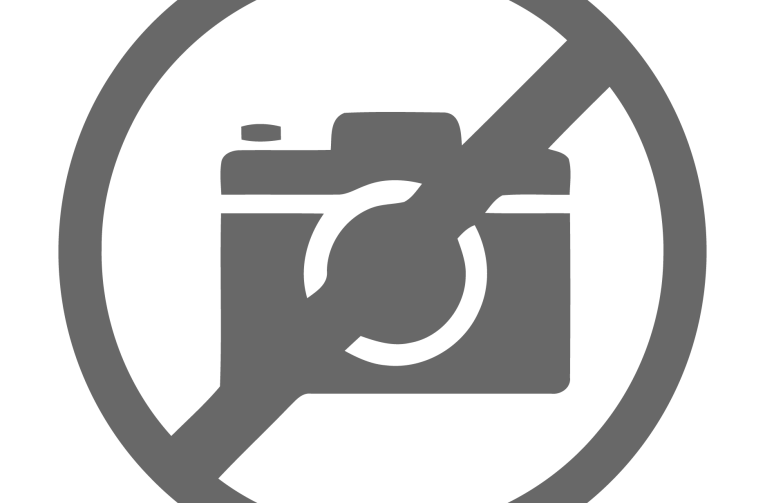
Of course, not all enhancements are the materials or exterior envelope of the enclosure. The simple cardboard tube implementation of the bass reflex port leaves room for improvement. Quest Engines has developed Stratified Stream, a patent-pending bass reflex port. Claiming improved performance when compared with traditional vented enclosures by using circular wave guides to passively inject air pressure waves generated into the port area. This allows the pressure waves to be introduced into the port with less induced turbulence, enabling the waves to develop and sustain more focused patterns.
Quest Engines’ explanation is that this can be achieved by adjusting the individual pipe lengths, pipe length ratios, overall port length, and wave guide parameters. Due to the focusing and phasing action within the system, while not creating chuffing, boom, or muddiness.
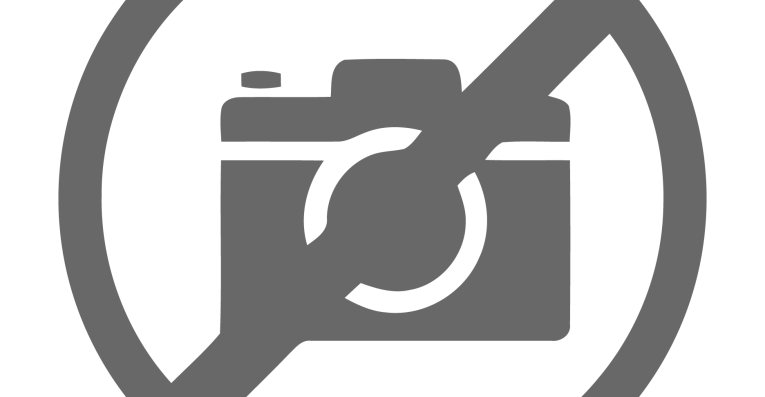
Atlantic Technology was licensing H-PAS which combined several enclosure tuning technologies — acoustic suspension, bass reflex, inverse horn, and transmission line — to produce deeper bass from small drivers in compact enclosures. The elements are cascaded one to another so as to pressurize and accelerate the lowest frequency back waves as they travel through the cabinet. These waves then radiate into the room through a vent at the lower front of the cabinet.
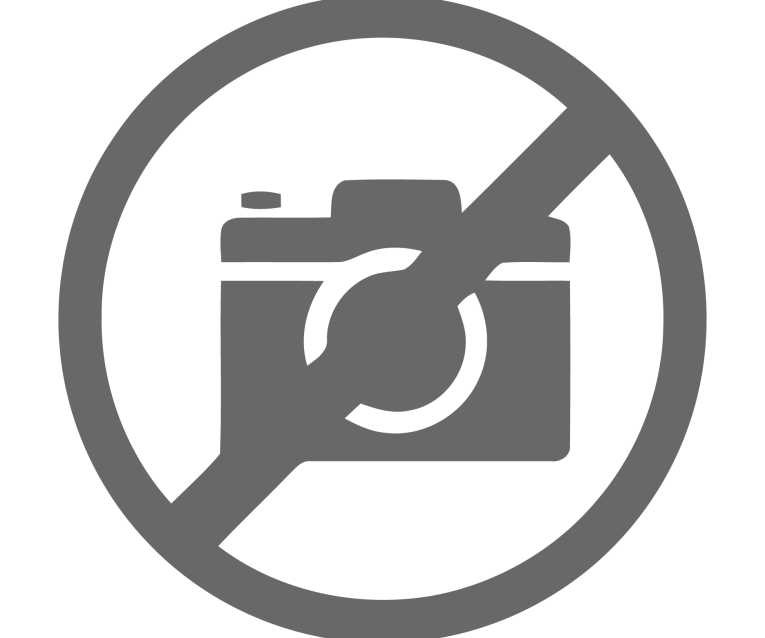
Earthquake Sound is known for high performance bass and has licensed a number of audio companies. Beyond licensing, Earthquake offers the PUMP-12, essentially two horn loaded 12” passive radiators in a single unit. The PUMP-12 adds up to +6 dB of bass without additional input power (when installed in a sealed enclosure). Also offered are the SLAPS Tuned Radiators with similar characteristics. User-tunable adjustments enable matching to a range of enclosures and woofers and suitable for high output needs where space is limited. VC
This article was originally published in Voice Coil, March 2020.
References
Sappi - www.sappi.com
Eastman Chemical - www.eastman.com
INEOS - www.ineos.com
Globe Plastics - www.globecomposites.com
INEOS Styrolution - www.ineos-styrolution.com
Covestro - www.covestro.com
Quest engines - www.questengines.com
Atlantic Technology - www.atlantictechnology.com
Earthquake Sound - www.earthquakesound.com/index.php/en/