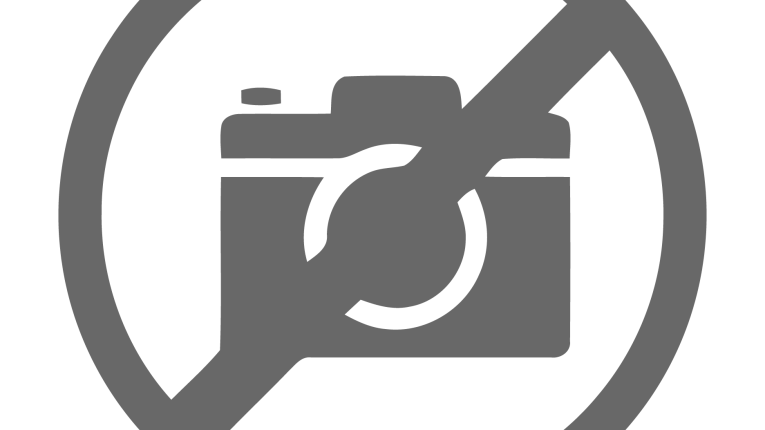
The frequency response of a bass reflex speaker with a fourth-order high-pass Butterworth response and a f3 (-3dB frequency) of 100Hz is shown as Figure 2. In this example the system is putting out 83dB, and you can see it drops to 80dB, or -3dB, at 100Hz. This is a Butterworth frequency response, but all bass reflex alignments responses are similar in nature. Figure 1 (audioXpress, July 2023) showed us the basic behavior at very low and very high frequencies. Figure 2 shows us how those behaviors add together in the frequency domain.
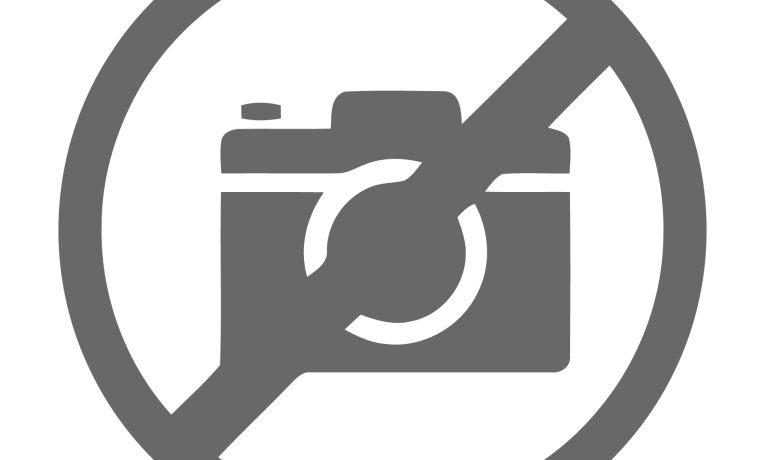
At box resonance, we can see there is a sharp dip in the driver output, with nearly all the system output coming from the port. The port and driver migrate from being mostly out of phase an octave below the box resonance to mostly in phase an octave above the box resonance.
Above the box resonance, the port and the driver are moving in phase (from Figure 1), but the port output decreases rapidly with increasing frequency (at 12dB/octave), such that by the time you get to 2×f3 (200Hz) the driver is putting out most of the sound.
Figure 3 shows the displacement of the driver and the air velocity in the port for the system with the response shown in Figure 2. These two parameters were chosen because they are what limit the physical output of the system. All real-world drivers have a physical limit of how far the cone can move in and out without damage. The distance they can travel while still being under good control of both the magnetic motor and the cone’s suspension system will always be somewhat less and is designated by the manufacturer as Xmax. Xmax is the farthest you can practically drive the cone before you run into excess distortion. Similarly, only so much air can flow through the port before it starts to resist the air flow and stops working properly. The variable that determines if the port will flow well is the velocity of the air in the port, which is why it is plotted in Figure 3.
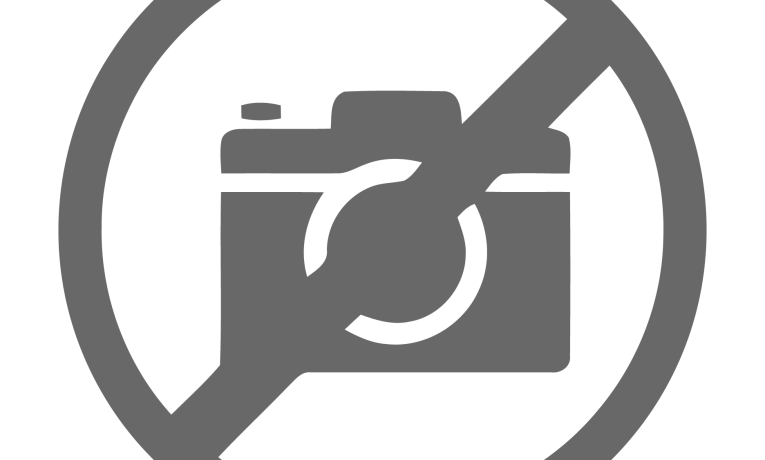
Looking first at the port velocity in Figure 3, we see that it peaks at 87Hz. Looking next at the driver displacement (above the 100Hz f3), we see that it peaks at 143Hz. The above trend will hold for all Butterworth ported designs: The port will max-out at 0.872*f3, and the driver will max-out at 1.432*f3. The curves will always look similar to Figure 3, with the frequency axis scaled by the actual f3 frequency. This might not seem like much, but it’s hugely important. It says that if we have a Butterworth response and we know the f3, we also know the two frequencies where the physical limits, driver displacement and port velocity, happen.
Note that the driver displacement increases radically below the f3 frequency and is limited at DC only by the driver stiffness. This is why ported speakers can experience cone flapping displacements when fed signals below their passband. We’re going to assume that the displacement below the system f3 will be taken care of by some other means and that we only need to worry about the maxima above f3. Note also that the large decrease in driver displacement around the f3 is one of the big advantages of the ported vs a sealed design. Most of the distortion producing mechanisms in a driver are related to displacement and producing more SPL for a given displacement generally means less distortion.
If we study Figure 2 at the above maxima frequencies, we will see that at 0.87×f3 the port is down by 3.63dB compared to the system’s mid-band. Similarly, we see that the driver is down by 5.86dB at 1.43×f3. We now know the frequencies and something about the output levels that are going to represent the system limits.
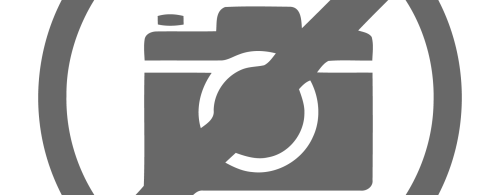
Where: fpmax is the frequency of maximum port air velocity
fdmax is the frequency of maximum driver displacement
SPLpm is decibels the port is down compared to mid-band
SPLdm is decibels the driver is down compared to mid-band
If we define the maximum system mid-band SPL as SPLM, we know that at the system limits:


Where: SPLp is the SPL produced by the port at one meter.
SPLd is the SPL produced by the driver at one meter.
Equation 5 and Equation 6 are enough to fully constrain the system response based on the physical limits of the port and driver. They say what the port and driver must each be capable of doing to support a system with a given -3dB frequency (f3) and given maximum SPL (SPLM). At a frequency of 0.873×f3 the port must be able to output an SPL of SPLM-3.63dB, and at frequency 1.432×f3 the driver must be able to output an SPL of SPLM-5.86dB. We have constrained what the port and driver must be able to do to meet a given B4 response at a given maximum SPL, and it resulted in two simple equations!
Driver and Port Output
To make use of Equation 5 and Equation 6, we need to know how the physical limits of the port and driver affect the SPL they can produce. The Thiele-Small (T-S) model assumes that the driver is mounted on an infinite plane. The equations for the sound radiated by a circular piston on an infinite plane are well established. The simplified version of the SPL produced at one meter on-axis from a circular piston on a plane is:

Where: f is the frequency Hertz [Hz]
ρ is the air density of 1.204 [kg/m3]
S is the piston area [m2]
V is the piston velocity [m/s]
If we assume that the driver and port can be considered as flat circular pistons on an infinite plane, we can derive the SPL they generate at one meter on axis as shown.
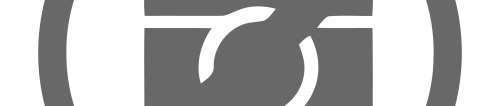
Where: f is the frequency.
SPLp is the SPL at one meter from the port decibels [dB].
Sp is the port area [m2].
Vp is the port air velocity [m/s].
SPLd is the SPL at one meter from the driver [dB].
Sd is the driver area [m2].
Xd is the driver displacement [m].
If we set Equation 8 equal to Equation 5, we have the port constraint. Setting Equation 9 equal to Equation 6 constrains the driver.


Where: Vpmax is the maximum allowable port velocity.
Xdmax is the driver’s published Xmax.
According to Equation 10 the port is limited by its area, the frequency, and the maximum velocity. We’re going to assume without proof that a reasonable maximum velocity limit is 20m/sec. This is a number that floats around the Audio DIY forums and seems to correlate well with the author’s own experience. If we assume Vpmax is 20, we can rearrange Equation 10 to solve for the port area (Sp), substitute in Equation (1) for the frequency, and simplify as:

Equation 12 is the area of the port [m2] required to produce the SPL necessary for a system with a -3dB frequency of f3 to produce a maximum SPL of SPLM. The port is now adequately defined. Equation 12 will prove useful as shown, but can also be rearranged to solve for SPLM as a function of the port diameter (Dp) as shown in Equation 14.
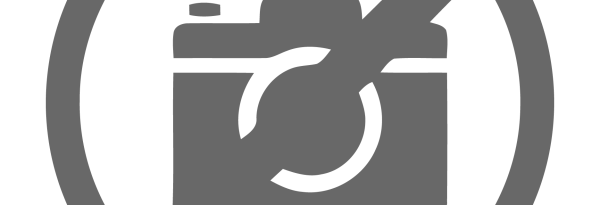
Where: SPLM is the system mid-band Max SPL in decibels.
f3 is the system -3dB frequency in Hertz.
Dp is port diameter in inches.
(Note the mish-mash of units in Equation 13. This article normally uses SI units, but port and driver sizes are typically specified in inches. We need Sp and Sd in meters squared for the other calculations.)
Equation 12 and Equation 14 define the port requirement. Equation 11 will similarly be used to define the driver requirement to support f3 and SPLM. Looking at Equation 11, we see the sum of Sd×Xmax, which is defined as the driver volume displacement. We could leave Sd and Xmax in the equations as they are both readily available for high quality drivers. But we are interested in making sweeping system-level statements. It would be more useful if we could make a reasonable approximation of the quantity Sd×Xmax as a function of the driver size. This would tell us how big of a driver is required for any combination of f3 and SPLM.
Commercial Drivers
Loudspeakers drivers are marketed by their nominal size, specified as the driver frame outside diameter in inches. The diameter of the cone is always smaller than the advertised diameter, d. I looked at the published cone area (Sd) of a lot of different drivers (i.e., woofers) with different advertised sizes (d). While there is obviously some variation, the following relationship was found to closely match the parameters of commercially available drivers.

Sd is cone area in m2.
We can also make some generalizations about the driver Xmax as a function of the advertised size. The drivers we’re concerned with are relatively long travel woofers. A reasonable approximation for the Xmax you can expect from a high-quality woofer as a function of its advertised size is:

Xmax is the displacement in millimeters.
Combining Equation 15 and Equation 16 gives us the volume displacement (Sd×Xmax) as a function of the driver size:

VD is the volume displacement in m.
Figure 4 shows Equation 17 plotted as hi-fi drivers. Subwoofer drivers, with their emphasis on low-frequency output, can typically have as much as twice the Xmax we assumed in Equation 16. Pro Audio Drivers, with their emphasis on efficiency, will typically have about half the Xmax we assumed in Equation 16. Both are plotted in Figure 4. They show a Subwoofer outputting 6db more and a Pro Audio woofer outputting 6db less than our target hi-fi solution.
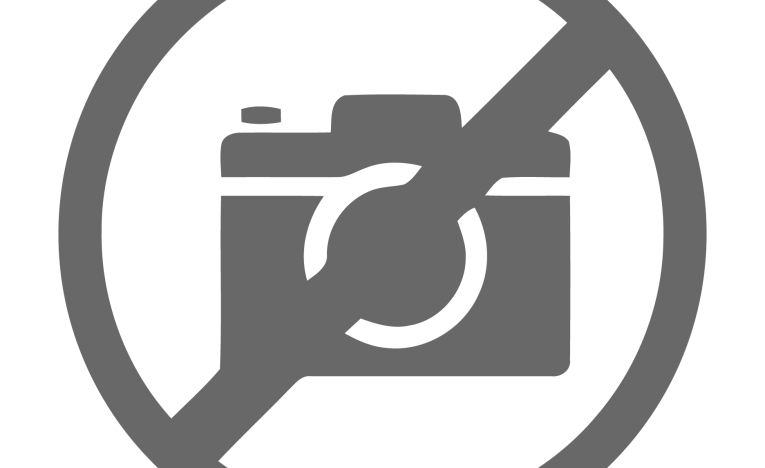
We are now able to substitute Equation 17 for the volume displacement as a function of the driver size into Equation 11 for the driver requirement. Doing so gives the maximum system SPL driver requirement as:

Equation 18 gives us our estimate of the maximum mid-band system SPL (SPLM) as a function of two basic things: 1) The system -3db point (f3); and 2) The advertised size of the driver. It makes perfect sense, yet it’s still a great finding.
We now have two pretty simple equations for the maximum system mid-band SPL based on the system f3, the port diameter (Equation 14), and the driver size (Equation 18). Plotting Equation 14 and Equation 18 against the system -3dB frequency (f3) will show us how the maximum mid-band SPL (SPLM) varies with the port and driver size.
Figure 5 is a plot of Equation 14 with the port based maximum SPL plotted against the system f3. This is all of a sudden a lot of information. Speaker system f3 frequencies are widely, if inaccurately, reported. Figure 5 says that if you know the system f3 and the port diameter, you know the maximum SPL it is likely to play cleanly. There’s no guarantee that any commercially available system is designed according to our assumptions. But our assumptions have all tended toward best case, and since Figure 5 represents the maximum system SPL for our hypothetically perfect system, it likely represents a reasonable upper limit of expectations from a commercially available system.
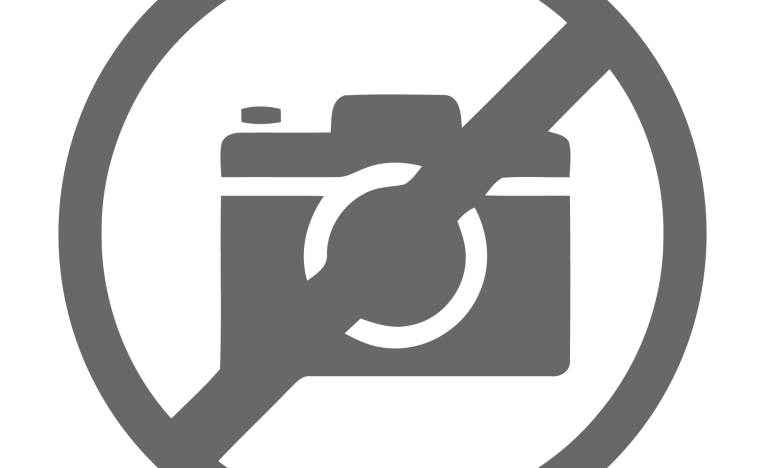
Figure 6 is a plot of Equation 18 with the driver based maximum SPL plotted against the system f3. Once again, this is a lot of information. Figure 6 makes it really clear just how much driver size matters; if you want to play louder at a given frequency, you need to go bigger. Figure 6 gives the designer an idea of what to expect from different driver sizes, and how output level will vary with f3 for a given driver size. Per the logic of Figure 4 you can add about 6dB to Figure 6 for a subwoofer driver and take off about 6dB for a pro audio driver. The combination of Figure 5 and Figure 6 give the designer a very quick idea of the port and driver sizes needed to meet a given performance target.
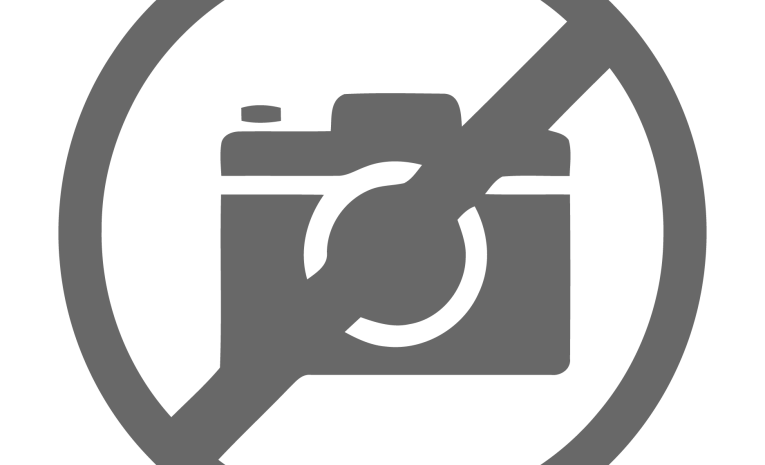
The Iron Law
Sorry, but I just love that term! It’s so in your face. It leaves no doubt that, whatever it says, you are not going to get around it! The term “The Iron Law” dates to work in the 1950s by Josef Hofmann, the “H” in KLH. He observed that with the new “Acoustic Suspension” (i.e., sealed) designs they were developing there was a relationship between the size of the box, the lowest frequencies it could play, and the efficiency. If you want a small box to play low frequencies it will be inefficient: It’s “The Iron Law”! Small quantified the Iron Law into a much more universal and useful form when he developed the equations for both sealed and ported systems. His equation for the acoustic efficiency of a ported system is:

Where: η is the system efficiency.
fs is the driver resonant frequency.
Vas is the “equivalent volume” of the driver.
Qes is the driver electrical Q.
c is the speed of sound (343.2 m/s).
Equation 19 is a quantifiable version of The Iron Law applied to a ported speaker. But it is not very useful for our purposes without a little modification. Here’s another place where our assumption of a B4 system starts to pay off. If we assume we have a modern low-loss system and choose a box loss of Qbl=7 and a woofer mechanical damping of Qms=3.0, we will end-up with the B4 response requiring:
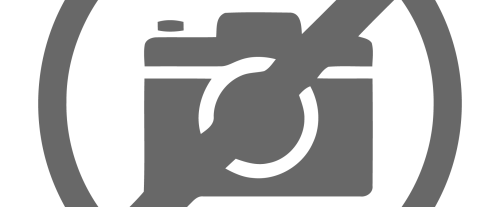
If we substitute all of the above into Equation 19, we end up with the efficiency of our typical B4 system as:


We now know the acoustic power generated but are really interested in SPL. The relationship between acoustic power and SPL at one meter from a piston on an infinite plane is:
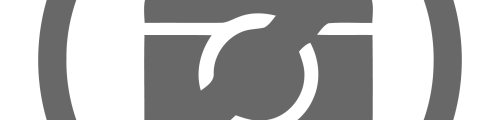
Combining Equation 21 and Equation 22, we get the SPL produced by our B4 system as:

We now have our sought-after relationship between SPL, box size, and power. But it is still not in its most useful form. We want to set Equation 23 equal to Equation 18 that defined the maximum SPL based on the driver. Doing so and then solving for the power gives us hat we are looking for:
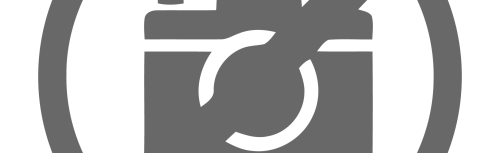
Next Article
This concludes the main analysis portion of the article. Equations 14, 18, and 24 tell the story we set out to tell. We’ll follow-up in Part 3 with an example to see how this all works together. We’ll also address some practical considerations that will make it clear that not all theoretically allowable solutions to our equations are practicably possible. We will determine the cut-off where a desirable design that is not practicable with a port can be easily realized by using a PR. A set of Excel spreadsheets for you to automate these calculations will be available as supplementary material online. aX
This article was originally published in audioXpress, August 2023
Click here to read: Bass Reflex Performance Envelope - Part 1: The Foundation
Click here to read: Bass Reflex Performance Envelope - Part 3: A Practical Example