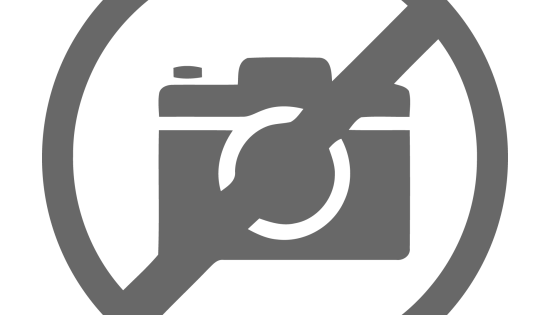
Designers choose them because they’re inexpensive, easy to use, and operate on standard desktop computers. These tools provide basic one- and two-dimensional modeling and simulation. For years, designers have created outstanding products using these simple simulation tools to supplement their knowledge of acoustics, design, and materials. So how much better could their products be if they paired their knowledge and experience with heavyweight simulation tools?
It’s not a hypothetical question anymore. The kind of acoustic simulation tools that were once the exclusive province of automotive and aerospace engineers are now available to loudspeaker designers. A speaker designer working in a home studio can design a new enclosure or ported box using the same simulation technology automotive engineers use to design quiet auto interiors or, more precisely, almost the same simulation technology. The important difference is that these new high-end simulation tools are accessible to any designer, not just highly trained analysts with doctoral degrees and six-figure budgets.
A growing number of reasonably priced, user-friendly simulation solutions put high-end acoustic analysis within the reach of designers who can benefit from high-end analysis but don’t want to make a career out of learning how to use new tools.
Actran, a member of the MSC Software portfolio of products, offers one of these solutions. MSC is best known for the highend simulation and analysis software that helped the Apollo space missions travel to the moon and back. However, the company has been working for years to simplify simulation software and make it accessible to a broader range of users without reducing its power.
Consumer product designers use Actran MSC’s suite of acoustic and vibration simulation software to create audio devices (e.g., telephones, hearing aids, musical instruments, and loudspeakers). Actran enables engineers to create 3-D simulations of the following:
• sound radiation by vibrating structures (e.g., speaker drivers)
• sound absorption within enclosures
• leakage through enclosure walls
• absorption by porous materials
• specific materials’ properties
• sound propagation in narrow ports and cavities
Actran enables loudspeaker engineers to take a broader view of speaker design including the finite elements (e.g., the drivers and enclosures), the infinite elements (e.g., sound wave emissions), and the underlying physics. With Actran, engineers can model 3-D designs to bring drivers and enclosures into phase for optimal sound. It shows the whole sound field so you can evaluate the physics and make modifications for higher performing products.
Designers have tackled these tasks with mathematical modeling in the past, but they’ve been limited by the accuracy of basic 1-D and 2-D simulation software. Mathematically modeling a transmission box in one or two dimension does not realistically simulate how sound will travel through the transmission box when it’s an actual 3-D object.
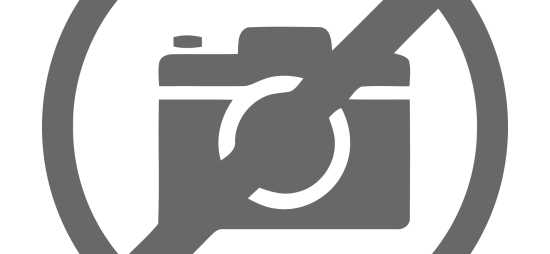
Three-dimensional modeling with a simulation solution such as Actran is much more accurate. Engineers can create 3-D CAD models and mesh in a free tool (e.g., Gmsh), then Actran can read the mesh directly from Gmsh. The user does not have to mathematically model the design, which increases accuracy while reducing simulation time and cost.
Engineers can model an enclosure, (e.g., a transmission line box) and change the internal configuration to manipulate sound transmission paths. Engineers can create sophisticated designs without making them too complicated to simulate and optimize.
They can also experiment with different materials from the integrated material library. Actran can accurately simulate the acoustic behavior of laminates, the most commonly used enclosure material. Few simulation applications can handle laminates, and none can do it with Actran’s simplicity and accuracy.
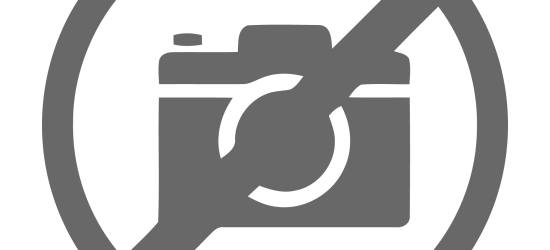
Figures 1–4 show a complex transmission line box design and the effects of adding porous materials to the inside. If there’s a problem with the design (e.g., a sound leak through the enclosure), the designer can use Actran to simulate the sound path through the enclosure and identify the leak’s source. They can then iterate the design to eliminate the problem. Simulating and analyzing every iteration shows the designer the best possible solution. Actran’s shared and distributed parallel processing capabilities enable engineers to quickly solve problems. Running simulations faster enables loudspeaker designers to modify their designs for optimal performance without increasing prototyping and production costs or time to market. Actran users can create simple scripts to test a variety of material properties, eliminating repetitive manual processes.
Actran also enables them to automate computation chains with a specific material property varying among 100 different values to determine the value for optimum acoustic performance. These optimization capabilities represent a significant reduction in prototyping costs. A major loudspeaker manufacturer might build and discard 20 prototypes a week to perfect a design. Actran simulation can reduce that number to just one or two.
Designers working with low-end tools can also locate problems—if they know what to look for and where to look. If they don’t, 1-D and 2-D views aren’t much help. Actran’s 3-D simulation models depict the entire design, not just a single plotted result. They reveal where the problem is and how it is generated. It’s a more accurate approach that yields superior results.
Speaker designers can use Actran to simulate any material available to them—and even some that aren’t. For example, consider a designer trying to perfect a new port box shape. He experiments with a variety of dimensions, enclosures, and dampening materials. The shape holds promise but doesn’t deliver the sound he suspects it could. Using Actran, he can determine what properties he needs from an enclosure material and tell his supplier what he needs. This kind of functionality has been available for years, but now it’s accessible to non-PhD engineers working on standard computer hardware.
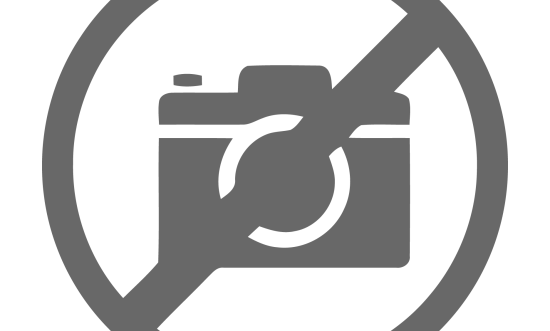
is shown here in graph form.
Editor’s Note: Dr. David Burd is manager of engineering and technical support at Free Field Technologies, an MSC Software company. www.fft.be
Originally published by Voice Coil - June 2013