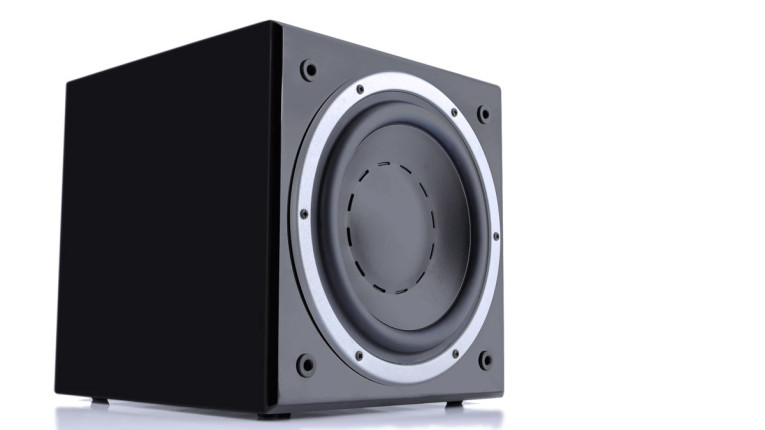
When it comes to increasing the bass, we can sort the innovations into three general areas: electronics, box stuffing, and finally in the driver design itself. When these different approaches are combined, the impact is multiplied, and achieving a game-changing product comes within reach.
Each time we revisit our “more bass bang for the buck” exploration we start with the repetition of Hofmann’s Iron Law. Josef Anton Hofmann was a speaker system designer whose work is represented by the classic New England sound from Acoustic Research, KLH, and Advent from the 1950s through the 1970s. Hofmann theorized that when a woofer is mounted in its speaker enclosure, the designer would have to accept that “a woofer system’s efficiency is directly proportional to its cabinet volume and its cutoff frequency’s cube (the lowest frequency it can usefully reproduce).
To reproduce even lower frequencies at the same output level, you need a larger box. Larger woofers are better woofers. Larger cabinets are more efficient and produce deeper bass with less power compression. If one compromises size efficiency or range, one can make a smaller design.”
Speaker Design
The old audio maxim a good large loudspeaker will always beat a good small one reflects a core aspect of the physics of loudspeaker design: the interdependency of box internal volume, bass extension, and sensitivity. Because a fundamental relationship interlocks these three factors, changing one tends to alter one or both of the others. There are actually quite a few ways to get more bang for your buck and bend the Iron Laws. Even iron bars can be elastically shaped if you put enough heat on them!
Speaker protection has been around forever in the form of limiters and more application-specific were the pioneering speaker management signal processors that appeared more than 40 years ago in Meyer Sound pro sound speakers. dbx loudspeaker management processors that could be “tuned” to a wide range of speakers and applications followed. Smart amps for smart speakers were pioneered by NXP, soon followed by Texas Instruments, Maxim-IC, and Qualcomm. In these smartphone amplifiers the dynamic guardrails are aligned to the speaker/enclosure as to excursion at the bottom end with thermal limits progressively taking over as frequency increases. Some algorithms used an upward sliding high-pass filter as the power output increased. While you won’t get increased bass performance at higher levels, you also won’t blow out your speakers. Getting a few million microspeakers blown out by ring tones could ruin anyone’s day.
Receivers often featured a “loudness” button, known technically as Fletcher-Munson compensation, that boosted low- and high-frequency components of the sound. Intended to offset the apparent loudness fall-off at those frequencies, especially at lower volume levels. Boosting these frequencies (mostly typically implemented only on the bottom end), produced a subjectively flatter equal-loudness contour that appears to be louder even at low volume, preventing the perceived sound from being dominated by the mid-frequencies where the ear is most sensitive. With digital audio, bass psychoacoustic processing using more sophisticated algorithms became practical and ideal for compromised audio systems such as Bluetooth speakers. An early example was the SRS Truebass, followed by the popular Waves MaxxBass, and the more recently introduced Bongiovi VSub.
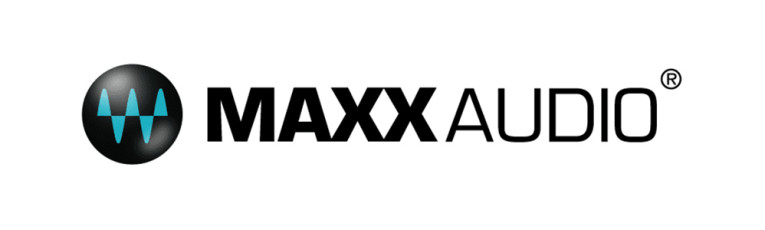
Waves Maxx Audio
MaxxBass works on enhancing the bass of small speakers by harmonics around an octave higher than the original. The speaker system design sets the frequency below which MaxxBass processes and high passes the bass below. The process is most credible the lower you can take the speaker system without bringing in the processing. If your speaker makes it down to 80Hz and Maxxbass is used to take it further down to 40Hz, that will come off better than using MaxxBass on a speaker that is struggling below 180Hz. Too much make-up can look clownish, yet if the signal processing calibration is artfully done, you can increase the impression of bass, even though the speaker cones are moving less. Nuvoton and other IC companies offer the Waves Maxx processing.
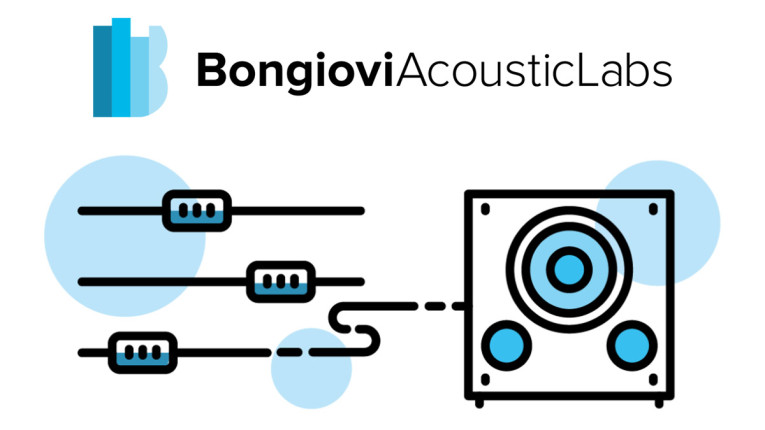
Bongiovi Media and Technology Lab
The Bongiovi DPS Suite of algorithms improves the audio capabilities of speaker systems inside of televisions, Bluetooth speakers, and soundbars gaming headphones and automotive applications. Core DPS is a powerful algorithm for improving the audio capabilities of speakers while providing several key features such as Voice Clarity, Level Smoothing, Detail Enhancement, and Speaker Protection.
The Virtual Subwoofer (VSub) is a crucial algorithm for lower-end speakers, allowing them to reproduce bass frequencies that would normally be lost. The VSub algorithm can provide up to 30dB of dynamic bass boost without hurting small Bluetooth, TV speaker drivers. VSub is also flexible enough to dramatically improve the bass response of higher-end systems with or without a subwoofer. Maximum Bass Response: VSub dynamically enhances the low-frequency response of speaker systems to provide rich bass at all listening levels. Even as overall system volume is decreased, low-frequency content is always reproduced.
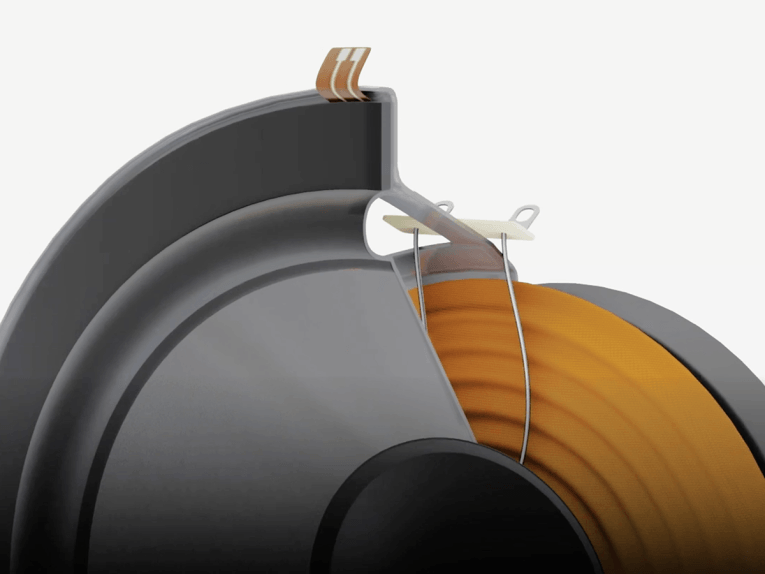
SubVo
www.subvo.com
While psychoacoustic “virtual bass” can be satisfying or at least enable modest speakers sound less tinny where size and battery life are the main considerations, another path is Servo-controlled speakers, with old-timers thinking of the Philips and later Velodyne accelerometer designs, but also the negative output impedance techniques from ACE Bass and Yamaha’s YST. Today, we have SubVo and Servobass with position sensor feedback on their woofers.
SubVo’s newly launched studio monitor subwoofer with a tracking sensor on the Scan-Speak 13” Revelator is coupled with an ICEpower 1200W Class-D amplifier. Speaker protection monitors the absolute diaphragm tracking sensor, allowing for the full mechanical excursion of 28mm in each direction, reproducing frequencies as low as 20Hz — even from a sealed box. The AI engine learns the transfer function of the speaker across its entire excursion range using the proprietary absolute position diaphragm tracking sensor to create an anti-distortion model, which yields ultra-low distortion.
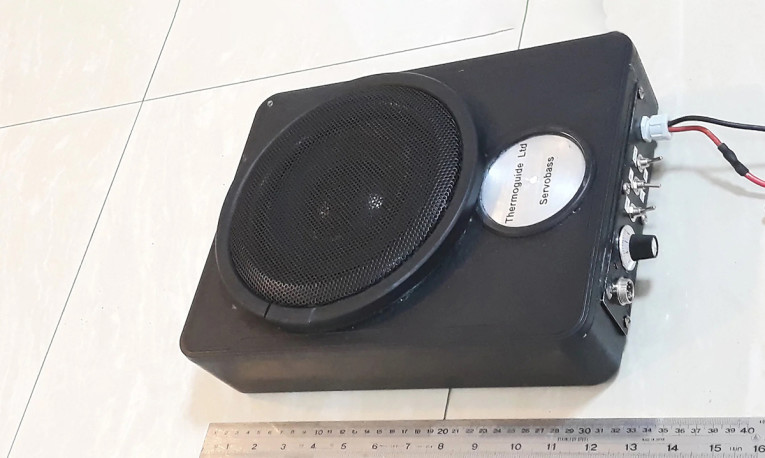
Servobass
Thermoguide Ltd
Both licensing reference designs as well as offering products, Servobass offers the ZRS-1 desktop subwoofers for home studios, gamers, bass guitar and electric drum players. By using motional feedback (MFB), tightly controlled bass transients can be reproduced down to the bottom octave of 30Hz to 60Hz, from a 6.5” driver in a sealed enclosure. Voice coil temperature is monitored in real time preventing voice coil overheating damage. Many small nearfield monitors do not reproduce below 60Hz because low-end Inter modulation with mid-range frequencies degrade clarity. Most nearfield monitor speakers use ported enclosure to enhance bass response, but the result is sloppy transient response. Adding a subwoofer with a well-designed crossover filter can eliminate these issues plus increased SPL with lower distortion.
Thermoguide’s small size (20cm x 20cm x 20cm) nearfield subwoofers are intended to be placed on a desktop with small monitor speakers placed on top of them in home and pro studios, thus perfect acoustic wavefront alignment can be achieved at the listener’s ear height. With Desktop Nearfield Subwoofers, room reflection effects are significantly reduced. These desktop subwoofers blend well with any near field monitors by using fourth-order Linkwitz-Riley crossover filters at 100Hz or 200Hz where the monitors are relatively flat with smooth phase shift.
Thermoguide-Servobass's bass enhancement MFB technology can also be used in soundbars, smart speakers, car audio, in-wall speakers, portables, and spatial sound speakers. It is all analog, patent-infringement-free, and easy to implement.
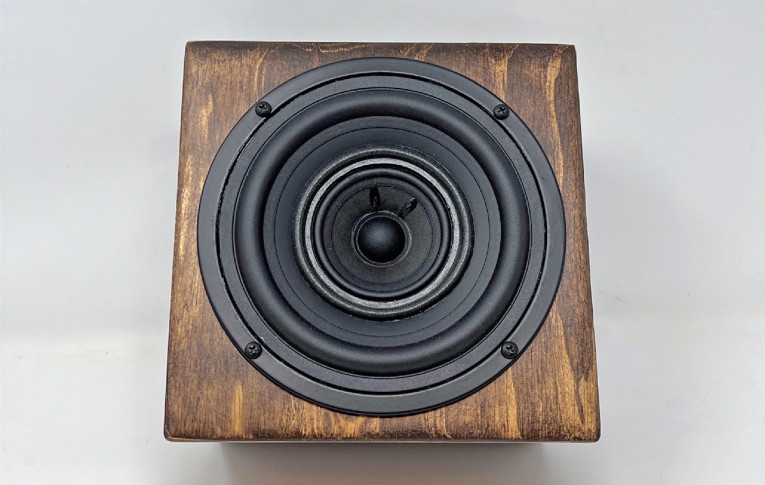
Dinaburg C2S
Dinaburg Technology LLC
Increasing bass output, at least from the driver itself, is about maximum volume velocity — that is the piston area × the peak excursion. X-max is a measure of this. One approach to improve all this is a passive ring radiator — specifically the Dinaburg C2S topology. In this elegant configuration, a passive ring radiator is added around a smaller diameter active loudspeaker. The ring radiator acts as a stabilizer, matching the air volumes axis-symmetrically of the boundary of the active loudspeaker cone. The stabilizer is concentric and in the same plane as the active loudspeaker. The concentric passive ring radiator reduces the required excursion from the active loudspeaker to produce lower frequencies similar to the benefit a bass reflex port design has over a sealed chamber. The coplanar concentric stabilizer (C2S) has a better coupling to the outside air volume than a bass reflex port would have or even a non-concentric passive radiator, which might have to be located on a different side of the enclosure. The passive ring radiator (C2S) acoustically filters out the upper range of the sound energy in the back chamber, minimizing comb filtering and enables the passive ring radiator to present a stable phase relationship to the listener on- and off‐axis.
Box Stuffing
Back in the early 1950s, Ed Vilchur of Acoustic Research acoustic suspension fame used fiberglass in the enclosure because it was more compliant (compressible) than air alone and lowered the in-box resonant frequency. Over the last 35 years, “magical” box stuffing has been introduced and some of this stuff is real (pardon my pun). Ever since loudspeaker designers realized the acoustic benefits of partially or fully enclosing a loudspeaker in a cabinet, they have sought to extract the maximum bass performance from a minimum cabinet size.
Since half the energy coming off a speaker’s cone is emanating from its back side, the “back wave” has to go somewhere. Certain enclosure types such as the bass reflex constructively utilize the low-frequency portion by tuning and phase inverting the energy to contribute to constructive bass output. Other enclosures such as acoustic suspension depend on the stuffing to enhance the air spring compliance to provide a bit more low-frequency response. The sound energy inside the speaker enclosure is slightly turned into heat energy by the box stuffing fibers’ frictional movement (shearing action). This frictional shearing is modeled in electrical circuit analogies (i.e., Thiele-Small parameters or SPICE circuit simulation programs) as an increase in the size (value) of a capacitor in series with the woofer.
In a mechanical description of the mechanism, the fiberglass stuffing enables the air spring of the trapped air in the enclosure to become less stiff and the speaker’s resonant frequency in the enclosure drops somewhat. As with bass reflex tuned port designs, the stuffing’s absorption at higher frequencies suppresses box modes, smoothing upper frequency, and transient response. Acoustic suspension designs benefit from increased stuffing to a point, while too much stuffing in a vented design will reduce the useful output from the port.
While enclosure stuffing is generally understood to influence the low-end response, its effects on midrange clarity are less widely appreciated, especially in the case of soundbars, smart speakers, and small surround sound satellite enclosures. These typically compact extended range speakers, so there’s a lot of midrange energy being dumped off the cone’s back. This sound energy bounces around and comes back through the cone—or the bass reflex ports if used.
Stuffing Choices
There are two main categories of stuffing, foams, and fibers, along with next-generation meta-materials. Open-cell polyether and polyester foams have similar properties, where foam density and cell structure are related to acoustical performance. The foam’s primary advantage is ease of handling.
Foam can be cut to order in fixed, non-friable geometries, making for ease of warehousing, inventory, handling, and assembly. Foam’s poor, low-frequency absorption is of limited benefit in sealed enclosures at low frequencies. Foams can deteriorate when exposed to UV light, fungus, ozone, and so forth, but these don’t tend to be issues in sealed or passive radiator systems where the foam cone surrounds go first!
The higher-performance stuffing used in acoustics include acrylics, wool, and glass fibers. Fiber length, texture, diameter, and packing density tend to be the major acoustical variables for a given fiber type. Optimal fiber geometries give the best results, though attention to detail tends to increase costs.
Wool is an expensive fiber and impractical for mass-produced speakers. On the other hand, when properly applied, it does have excellent acoustical characteristics. Since the fibers tend to bunch up, it’s difficult to get consistent packing density and volume due to its dimensional instability.
Fiberglass is a low-to-medium priced fiber with good-to-excellent performance. Fiberglass is generally used pre-cut in sheet form, with specified thickness and density. As anyone who’s ever worked with fiberglass can attest, there are adverse worker reactions (itching), which can be due to fiber aspect ratio and resin selection. There had been questions about health (which was a drawback to Asbestos which over long exposure is deadly), with fiberglass there are two aspects that are the culprits, one is the phenol-formaldehyde resin binder and the other the fiber aspect ratios—neither has serious health impacts.
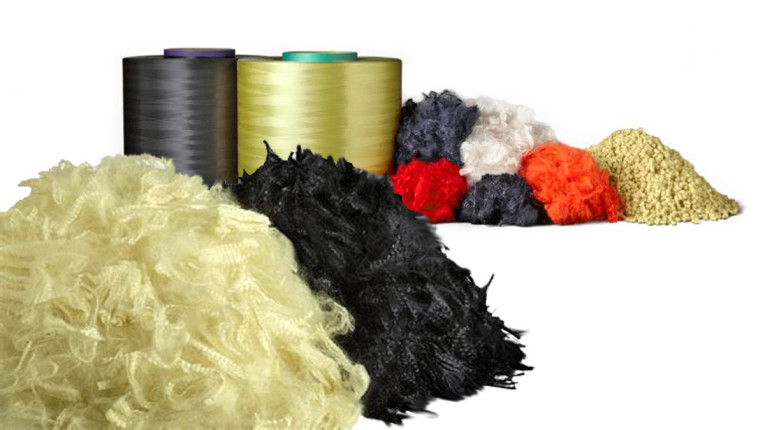
Teijin Aramid
www.teijinaramid.com
Twaron is an aramid fiber especially suitable for the acoustic dampening of loudspeaker enclosures and superior to conventional glass-fiber insulation. The inorganic origin counteracts rotting and mold formation. There are variants that are post-processed for acoustic box stuffing.
Twaron Unicorn Hair is a speaker cabinet filler for acoustic damping purposes, which is produced by Thüringisches Institut für Textil- und Kunststoff-Forschung (TITK), Germany, exclusively for Mundorf, Germany. Unicorn Hair is predominantly made from Twaron in the form of user-friendly fiber strings of extreme thinness. Its long fibers absorb and dampen the lower audio frequency range (<1kHz) in subwoofers and long transmission line cabinets. Due to the resulting audible differences, today Twaron Unicorn Hair is an essential “must” for many well-known developers and manufacturers of high-end speakers. For loudspeaker applications, the extremely thin Twaron fibers are combed and processed into dense so-called Horsetail Hair named Twaron Unicorn Hair. In contrast to other plastic fibers, Twaron conducts heat-generated vibrations from viscous shearing action, which means that it absorbs motion energy in an entirely different manner than conventional materials used for damping purposes.
Owing to the endless fiber strings used in Twaron Unicorn Hair, the effective functional frequency-range is lower in comparison with the Twaron Angel Hair. It constitutes a significantly better alternative to the damping materials, which are otherwise used in transmission line systems. Twaron Unicorn Hair results in a direct and tight bass reproduction in (sub-) bass cabinets, and in transmission-lines. The low-frequency resonances are attenuated efficiently with deep and clean bass reproduction.
To make Mundorf Angel Hair, the Twaron fibers are first cut into 60mm long sections, carded, mixed, and pressed into a mass. The choice of the right fiber lengths and the right process for combing them into a workable mass leads to remarkable acoustic results. While Mundorf’s post-processed Twaron aramid is the high-end of box stuffing, a more mainstream solution has just arrived with Teijin Aramid’s Twaron. The high-modulus filament yarn produced with recycled content has the same exceptional strength and durability as the original renowned Twaron. While Teijin has been mechanically recycling end-of-life para-aramid products for decades, the new generation of physical recycling technology has enabled fully circular aramids to be possible.
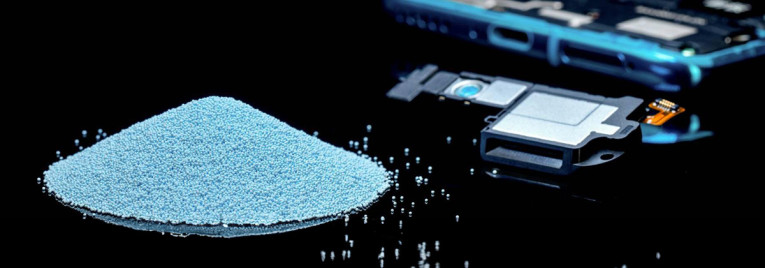
N-Bass
SSI New Materials (Zhenjiang) Co., Ltd.
Acoustic metamaterial has been working behind the scenes — relegated and buried in the speaker sub-enclosures of smartphones — but more recently finding its way behind compression driver and tweeter domes. In a recent article in Acoustics Today (a publication of the Acoustical Society of America) Michael Haberman of the Applied Research Labs of University of Texas provided an intriguing description “The defining property of a metamaterial is that it achieves effects not found in nature to address long-standing engineering challenges in acoustics. AMM devices are in apparent defiance of the intuitive laws of physics and the catalyst to dissolve Hofmann’s Iron Laws.
It was 10 years ago that Knowles introduced N’Bass porous powder metamaterial filler for the rear cavity of its microspeakers (supplied to Apple). This super compliant/super porous box stuffing is more compliant than the air it displaces and increases the back volume seen by the speaker by up to 100%. It provides a combination of better acoustic performance — specifically more bass — or smaller loudspeaker box designs while keeping the same performance. N‘Bass also facilitates the usage of bigger loudspeakers in what would be impractically small enclosures.
Similar to a sponge, 2 grams of the N’Bass material have a surface area of about a football field. The small back volumes used in mobile devices increase the air spring stiffness and this back pressure, raising the roll-off corner frequency. The material desorbs the air molecules when the membrane vibrates out of the speaker box. This virtually increases the available back volume for the loudspeaker. Desorbs is to release of (an adsorbed substance is this case air) from a surface.
This has been great for Apple sourcing their microspeakers from Knowles, and I looked at this for some smartphone projects, but that left out not just designers from other brands and but also applications like smart speakers, soundbars, subwoofers, but also true wireless stereo (TWS) earphones, and slimmer closed-back headphones. Then in 2016 Knowles sold its microspeaker group along with the N’Bass technology to Sound Solutions International (SSI) in China. What is now making N’Bass relevant to the rest of us is this captive in-house technology has now spun off as SSI New Materials, which is specializing in nano metamaterials and happy to hear from new customers and applications. Commercialized applications beyond smart speakers include tablets, laptops, and conference phones, with headphones and soundbars in the works.
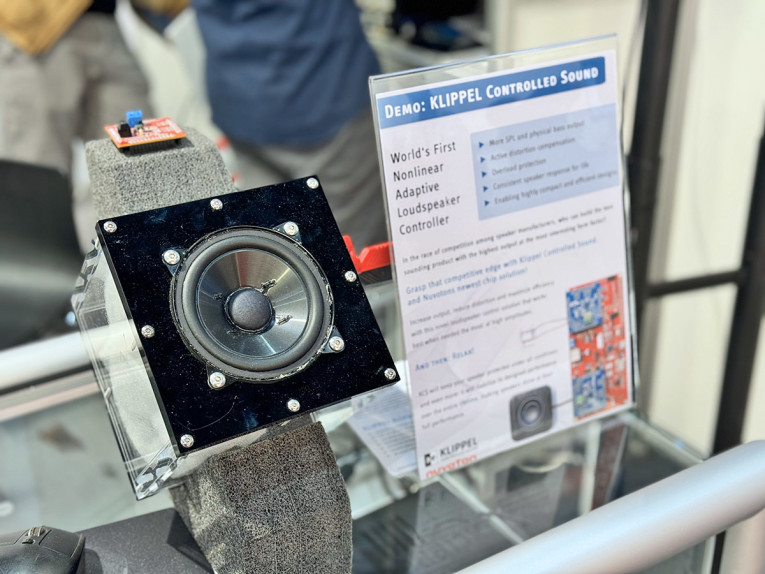
Klippel Controlled Sound (KCS)
Klippel GmbH
Nuvoton
Yet another angle is pre-distortion processing and now we have two contenders: Klippel’s KCS and TAOT’s WaveLock. I have mentioned that the development I see having the most impact on speaker design in years to come is not even a transducer but a processing technique that will change how most of us design not just integrated speaker systems but the drivers themselves. This is Dr. Wolfgang Klippel’s KCS in chip form from Nuvoton, essentially dynamic pre-distortion circuits that are calibrated to the speaker and enclosure (and even the passive radiator if you have one).
We previously mentioned that smart amps are predominately a feedforward protection circuit specifically tuned for the limits of the speaker, both displacement and thermal. Klippel Controlled Sound (KCS) technology, integrated in a Nuvoton audio amplifier chip, creates a versatile solution to improve bass performance and sound quality by compensating for nonlinear speaker responses. The Nuvoton KCS series combine the protection and pre-distortion modeling through parameter identification (using an application-specific software module for the Klippel test system) into an integrated solution with a 7W for smart speakers and huddle room speakerphones; a 20W for soundbars; and a 30W x2 or 60W mono coming in Q1 2024. The KCS calibration process flattens response but more also reduces bass distortion, which increases acoustic echo cancelation (AEC) stability margins and ease of barge-in.
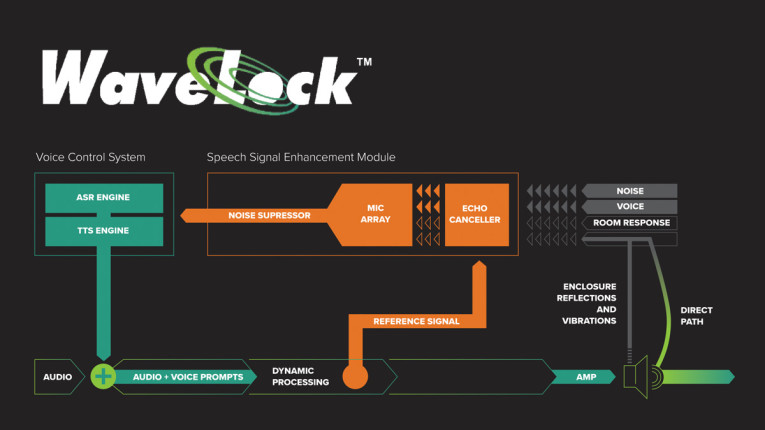
WaveLock
The Audio of Things (TAOT)
TAOT's WaveLock is a patented embedded algorithm and tool suite invented by John French and his team at Audera Acoustics. A serial entrepreneur in the audio industry since 1989, French founded Audera in 2004, and his techniques led to his invention of the BASH amplifier for Blade Technologies 30 years ago and is used in millions of products. (Blade was acquired by Sonavox Canada.)
It is well known that distortions in loudspeakers are the primary technical cause of poor dialogue/barge-in awkwardness in half and full duplex systems. For decades the industry has been seeking a viable solution to this frustration in the poor performance of conference phones, Bluetooth speakers with speakerphone functions, and more. There are several speaker vendors that offer compact linear (2” to 3”) speakers specifically for AEC and ANC applications (such as Tymphany or SEAS with cost-effective versions from parent company Merry Electronics, and others). But now with WaveLock, designers have new degrees of freedom to balance and maintain the metrics that mean the most—loudness, distortion, barge-in, bass extension, BOM costs, and size. And, for the first time, nonlinear distortions in products can be corrected remotely using pre-distortion feedforward processing with the designer able to select any amplifier.
With no hardware changes required and easy integration with firmware, lower distortion enables higher output and bass extension. The algorithm is also adaptive, automatically matching parameters for precise control of distortion. For most designs that have a processor, there is: zero BOM cost; smart amp-type thermal and mechanical protection; better wake-word detection through less intermodulation; and harmonic distortion. Check out James Croft’s article available online: “Acoustic transducer systems and methods of operating acoustic transducer systems are provided. The methods can involve: receiving an input audio signal; determining a position of a diaphragm; determining a correction factor, a motor force factor, a spring error factor, and a system spring factor based at least."
The implications for combing these technique leads to some rather nifty products with a healthy dose of “shock and awe” and I will be writing about some case studies soon.
"On the position of the diaphragm; determining a corrected voice coil current based at least on the input audio signal, the correction factor, the spring error factor, and a velocity of the diaphragm; and applying a corrected audio signal to a voice coil fixed to the diaphragm based at least on the corrected voice coil current, wherein the corrected audio signal corrects the input audio signal to compensate for non-linear characteristics of the acoustic transducer system.”
WaveLock’s licensing program is managed by The Audio of Things (TAOT), an Indiana-based audio engineering company that designs, develops, and sells components, subsystems, and products that optimize performance of voice interactive and audio devices to solve economic and performance problems in consumer, professional, commercial and tactical audio systems. VC
This article was originally published in Voice Coil, November 2023