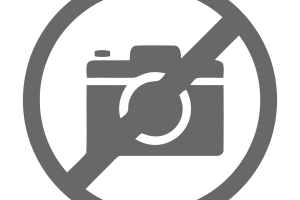
Many of NightHawk’s design elements are successfully implemented in today’s most innovative loudspeakers, but have never been used in headphones. NightHawk uses a 50mm pistonic driver with a biocellulose diaphragm designed to take advantage of the material’s outstanding rigidity and mechanical integrity at high frequencies. A patented split-gap motor significantly reduces intermodulation distortion. NightHawk’s earcups are made from “Liquid Wood,” an environmentally friendly material that offers outstanding acoustic properties and vast geometric possibilities. The sophisticated earcup enclosures incorporate support beams that enhance structural integrity and minimize unwanted resonances and vibrations.
According to AudioQuest, NightHawk is also the first completely original production headphone to use a 3D-printed part – a “biomimetic grille” that uses a complex diamond-cubic latticework to diffuse sound and defeat resonances. Far too complex to mold or machine, NightHawk’s grille can only be created through 3D printing via an advanced form of additive manufacturing known as “Selective Laser Sintering.”
NightHawk’s patent-pending suspension system allows its earcups to move freely, accommodating heads of any shape or size, while decoupling the earcups, further counteracting harmful resonances. The flexible headband efficiently distributes the headphones’ weight, providing a sure fit while minimizing clamping force and enabling long listening sessions.
As Skylar Gray explains “the mandate I received from [AudioQuest founder] Bill Low was to follow my passion. I was able to take all the time I needed to create the product that I felt was necessary — a product that we hope changes the way the world thinks about headphone design, creates a truly immersive listening experience, and provides a deeper emotional connection with music.”
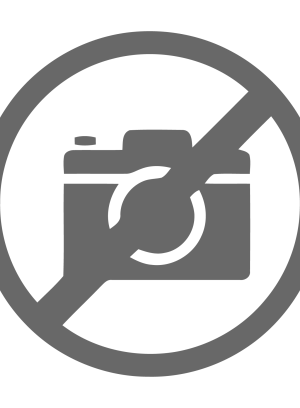
New approach and materials
Much like the internal bracing of a loudspeaker cabinet, NightHawk’s earcup enclosure incorporates support beams that enhance structural integrity and minimize unwanted resonances and vibrations. An elastomeric coating is carefully applied to the enclosure’s internal surfaces to further reduce harmful vibrations, while a damping material comprising a purposeful blend of wool and polyester enables a smooth, natural frequency response, minimizing vibration-induced distortion.
Most of today’s headphones use diaphragms made from Mylar — an inexpensive, lightweight, and technologically mature plastic material. Inspired by the advanced drive-units used in today’s high-performance loudspeakers, NightHawk’s 50mm high-excursion drivers have biocellulose pistonic diaphragms and compliant rubber surrounds. The biocellulose material is rigid and self-damping, making it far more accurate and musically pleasing than Mylar.
NightHawk’s patented split-gap motor design also dramatically reduces intermodulation distortion to provide a clean, well-defined broadband response and a large, naturally detailed representation of space. Since air turbulence is one of the major contributors to non-linear, distortion-inducing behavior in headphone drivers, NightHawk uses symmetrically distributed, equation-driven curvatures to intelligently guide airflow through its internal driver structure, thus reducing the harmful, unpredictable effects of turbulent air pockets and voice coil rocking.
“Liquid Wood” ARBOFORM
In creating NightHawk, Gray worked passionately to bring purposeful and intelligent innovation to the mature art of headphone design. No single element was taken for granted. As such, NightHawk exhibits many groundbreaking components, including sophisticated earcups developed in collaboration with the German firm Tecnaro, using ARBOFORM, or “Liquid Wood.”
Liquid Wood is made from 100% renewable raw materials. Its principal component is lignin - a byproduct in the cellulose pulping and papermaking process - whose annual production exceeds 50 million tons. Whereas the production (and disposal) of plastic is known to present environmental hazards, the production of ARBOFORM has minimal impact on the ecosystem.
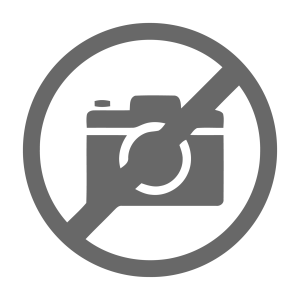
Lignin is combined with natural fibers, natural resins and wax-es, and treated in such a way that it can be injection molded. While injection molding is commonly accomplished with plastics or synthetic polymers, Liquid Wood is a natural material; thus, every NightHawk earcup is one of a kind, exhibiting subtle variations in color, pattern, and surface finish that further enhance NightHawk’s overall beauty.
Moreover, compared to ordinary plastic or wood, Liquid Wood has far superior acoustic properties and provides a seemingly endless array of geometric possibilities. In NightHawk, Liquid Wood is used to shape the earcups to more closely resemble the human ear, thereby providing a more complete and comfortable fit, reducing stress on the listener’s head and ears.
According to Gray, “ARBOFORM is a key element to NightHawk’s performance and a driving force in the excitement surrounding its release.”
Full production of AudioQuest’s NightHawk headphones is scheduled for March/April 2015. NightHawk will be available with a manufacturer’s suggested retail price of $599 US / $699 CAD / €599 / £499 (EU and UK, VAT included).
nighthawk.audioquest.com
For more information on ARBOFORM, visit www.tecnaro.de