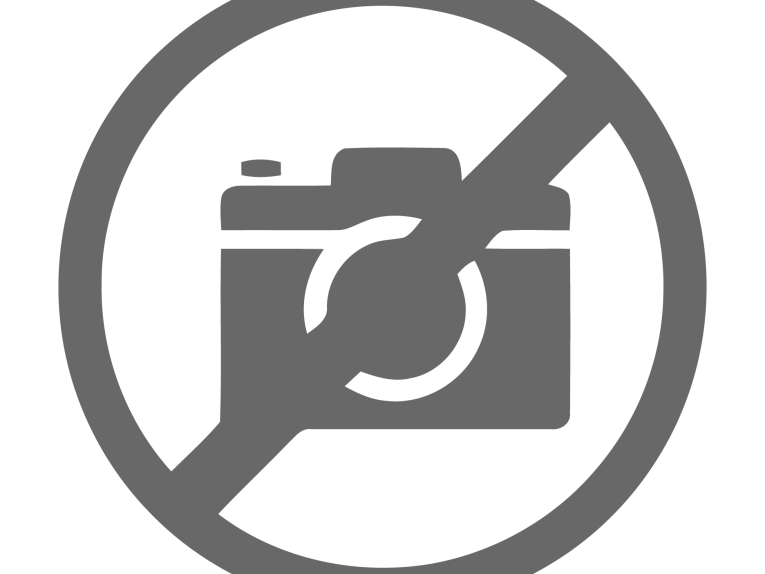

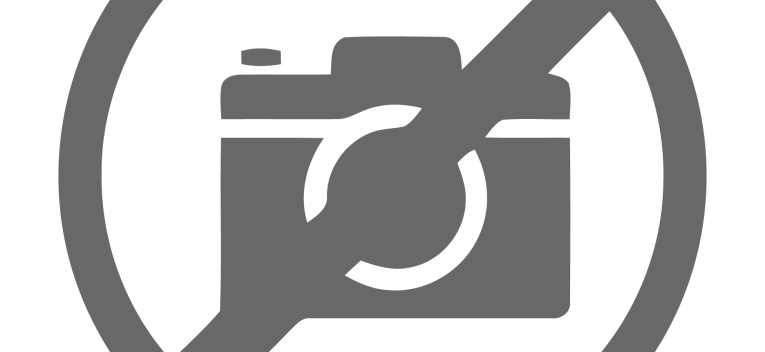
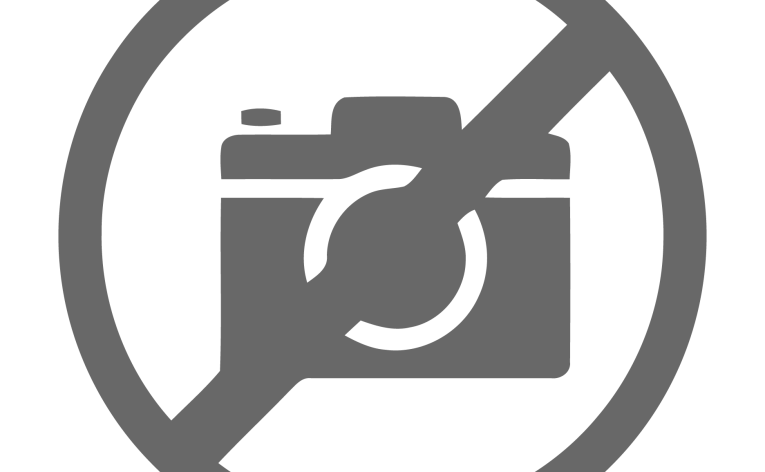
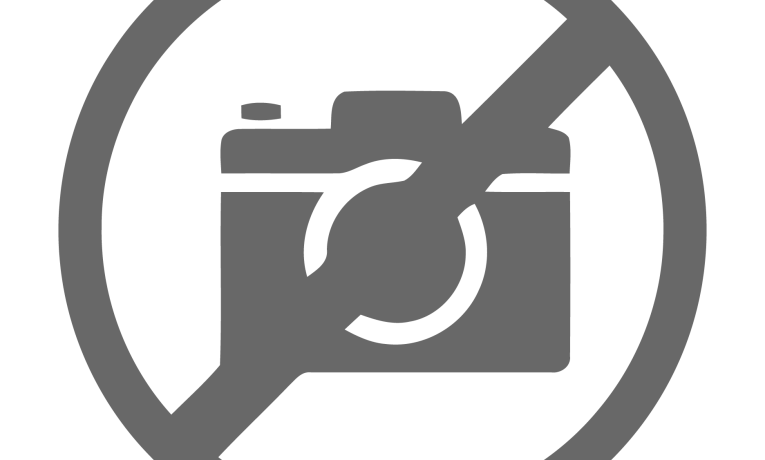
Features for the Faital Pro 6PR160 are fairly extensive. The frame is a proprietary four-spoke cast-aluminum frame, and as with many small diameter drivers, does not have venting below the spider mounting area. Cooling for this driver is provided by a 12 mm diameter pole vent with a 22 mm flared exit.
The cone assembly consists of a curvilinear paper cone with a front side waterproof hydrophobic coating and a 2.2” diameter convex paper dust cap, likewise with a waterproof hydrophobic coating. Compliance is provided by a triple-roll treated poloycotton pleated surround with the remaining compliance coming from a 4” diameter flat cloth spider with constant height waves.
The motor design on the Faital Pro 6PR160 utilizes a neodymium ring magnet fitted with an aluminum shorting ring (Faraday shield). The neodymium ring magnet motor was FEA-designed, using a 37 mm (1.46”) diameter voice coil wound with round aluminum wire on a nonconducting glass fiber former. The neodymium ring magnet is sandwiched between a milled and polished front plate and a cast-shaped T-yoke with a 13.5 mm bump-out. Last, the voice coil is terminated to injection-molded terminal block with color-coded push terminals.
I commenced analysis of the 6PR160 using the LinearX LMS analyzer and VIBox to create both voltage and admittance (current) curves with the driver clamped to a rigid test fixture in free-air at 0.3 V, 1 V, 3 V, 6 V, 10 V, 15 V, and 20 V. The Faital Pro driver remained acceptably linear enough for LEAP 5 to curve fit at 20 V, which is a new Test Bench record for this diameter woofer!
Following my established protocol for Test Bench testing, I no longer use a single added mass measurement and instead use the physically measured Mmd data (11.8 grams for the 6PR160). I post-processed the 14 550-point sine wave sweeps for each 6PR160 sample and divided the voltage curves by the current curves to generate impedance curves, with the phase derived using the LMS calculation method, and along with the accompanying voltage curves, imported to the LEAP 5 Enclosure Shop software.
Because Thiele-Small (T-S) data provided by the majority of OEM manufacturers is generated using either the standard model or the LEAP 4 TSL model, I additionally created a LEAP 4 TSL parameter set using the 1 V free-air curves. I then selected the complete data set, the multiple voltage impedance curves for the LTD model, and the 1 V impedance curve for the TSL model in the transducer parameter derivation menu in LEAP 5. Next, I created the parameters for the computer box simulations. Figure 1 shows the 1 V free-air impedance curve. Table 1 compares the LEAP 5 LTD and TSL data and factory parameters for both of Faital Pro 6PR160 samples.
LEAP parameter calculation results for the 6PR160 correlated reasonably well with the factory published data, except for the Xmax and Vas numbers. Faital Pro uses its own definition of Xmax, which is why it’s different. Standard practice and what you will find in my book (The Loudspeaker Design Cookbook) is Xmax= (Hvc-Hg)/2, so with a voice coil length of 12 mm and a gap height of 6 mm, Xmax is 3 mm. Faital Pro uses Xmax = (Hvc-Hg)/2 + Hg/3, so it would be 3 mm plus 2 mm (Hg/3), which is why it publishes an Xmax for this driver at 5 mm. This actually is somewhat similar fringe-field compensation factor to what I do in finding the maximum SPL of a driver in a LEAP 5 box simulation when I raise the input voltage until the excursion maximum is Xmax + 15% (this comes from Mark Gander’s work at JBL Pro some years ago, and is based on excursion beyond Xmax producing 3% THD), which for the 6PR160 is 3.45 mm, but even that is more conservative than the Faital Pro’s Xmax definition.
Faital also uses a more conservative Sd number of 117 cm2 compared to the 128.7 cm2 used in my work, which is derived from the cone diameter plus 50% of the surround width on each side of the assembly. This affects the Vas calculation.
However, I followed my usual protocol and proceeded setting up computer enclosure simulations using the LEAP LTD parameters for Sample 1. I programmed two computer box simulations into LEAP 5—one a sealed box with a 70 in3 volume (50% fill material) and the second, a vented enclosure QB3 alignment with a 70 in3 volume simulated with 15% fiberglass damping material and tuned to 140 Hz.
Figure 2 displays the results for the 6PR160 in the two enclosures at 2.83 V and at a voltage level sufficiently high enough to increase cone excursion to Xmax + 15% (3.5 mm for the 6PR160). This produced a F3 frequency of 229 Hz (F6 = 179 Hz) with a Qtc = 0.6 for the sealed enclosure and –3 dB = 213 Hz (F6 = 176 Hz) for the vented box simulation.
Increasing the voltage input to the simulations until the maximum linear cone excursion criteria was reached resulted in 118.5 dB at 72 V for the closed box simulation and the 121 dB for the same 72 V input level for the vented enclosure. Figure 3 shows the 2.83 V group delay curves. Figure 4 shows the 72 V excursion curves. In the case of the vented box simulation, excursion goes beyond the 3.5 mm Xmax + 15% around 80 Hz, so a 60 Hz to 70 Hz steep (24 dB/octave) high-pass filter would be a useful addition and prevent over excursion and distortion.
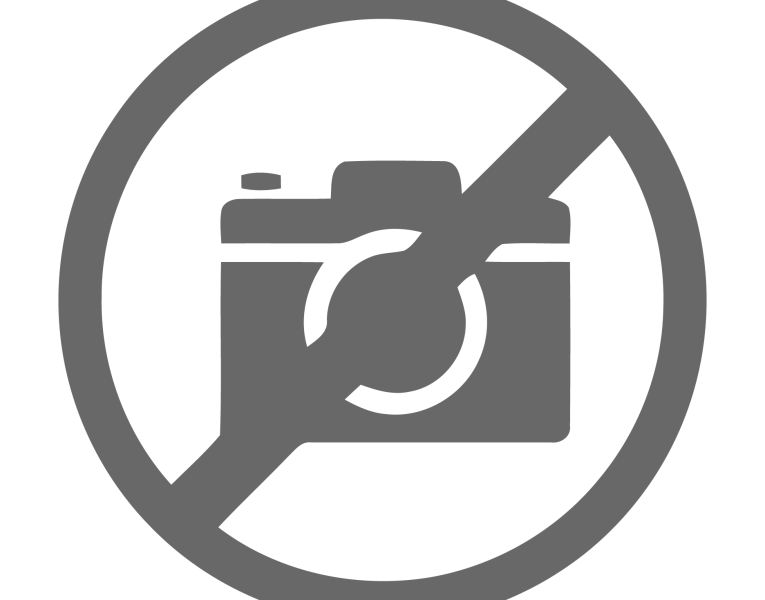
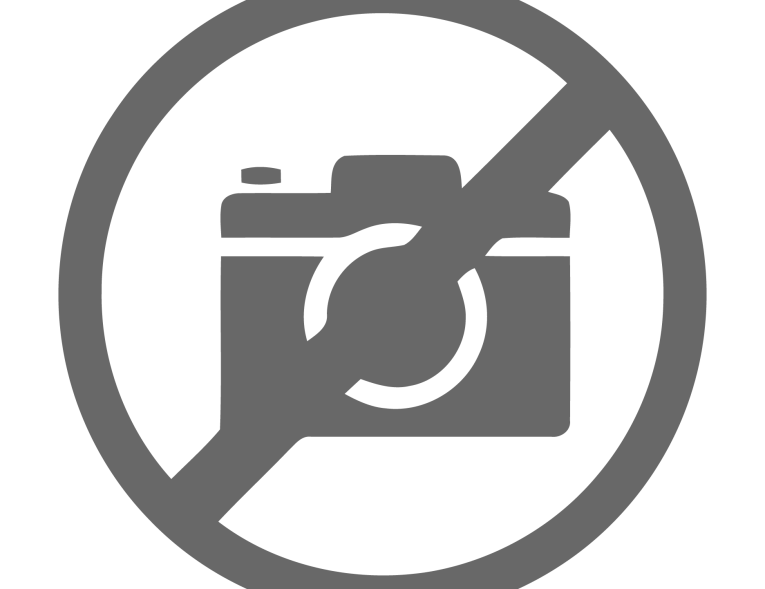
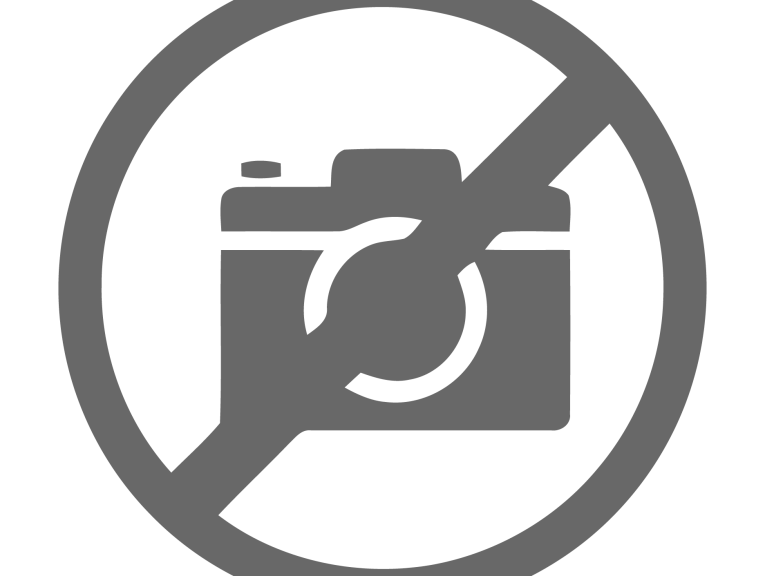
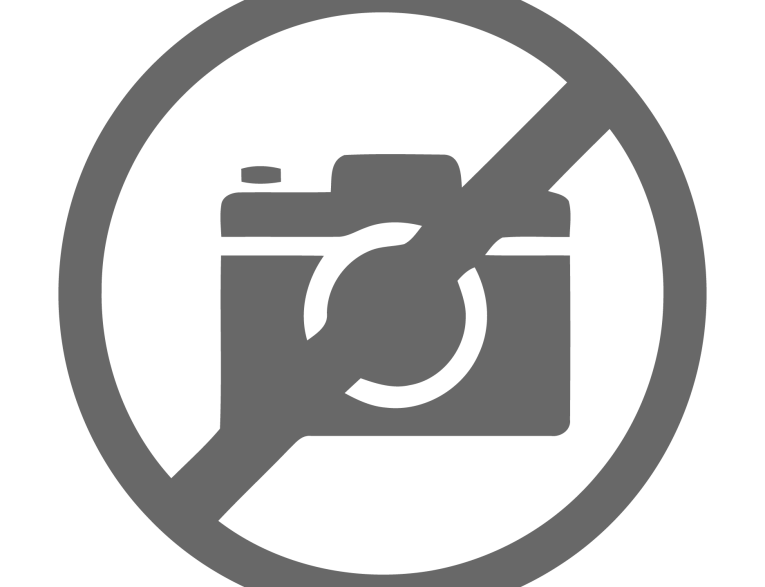
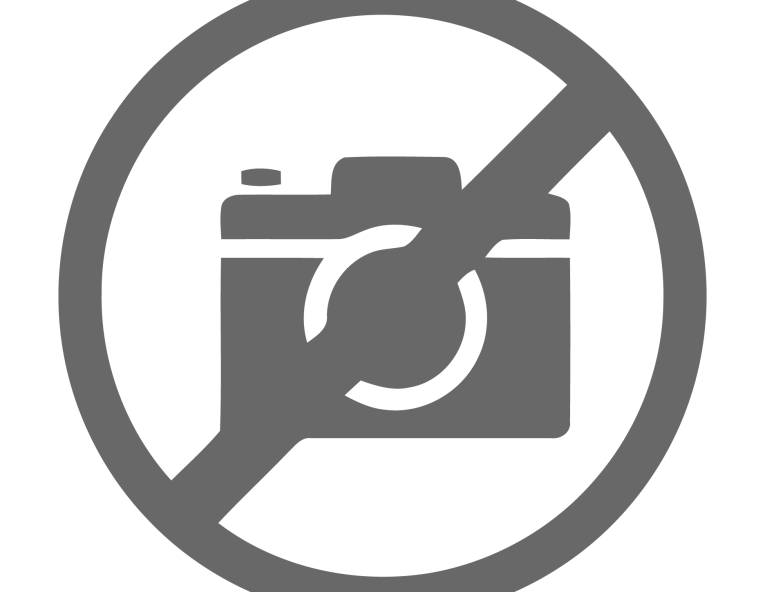
Klippel analysis for the 6PR160, performed by Pat Turnmire of Redrock Acoustics, produced the Bl(X), Kms(X) and Bl and Kms symmetry range plots given in Figures 5-8. (Our analyzer is provided courtesy of Klippel GmbH. Please note that due to customer requests, Klippel has restored the Kms symmetry range plot to the Klippel analyzer, so despite my announcement in the February 2019 Test Bench, I will continue to provide the Kms symmetry range curves in this and future Test Bench reports.)
The Bl(X) curve for the 6PR160 (Figure 5) is moderately broad and symmetrical, with a very small amount of coil-in offset. Looking at the Bl symmetry plot (Figure 6), the displacement is a trivial 0.17 mm at the 2 mm position, and close to zero at the physical Xmax of 3 mm.
Figure 7 shows the Kms(X) symmetry range curve. Figure 8 shows the Kms symmetry range curves. The Kms(X) curve is also fairly symmetrical in both directions, as well as having small amount of coil-out offset. Looking at the Kms symmetry range plot shown in Figure 8, there is a likewise trivial 0.25 mm coil-out offset 2 mm increasing to 0.31 mm the physical Xmax 3 mm position.
Displacement limiting numbers calculated by the Klippel analyzer for the 6PR160 were XBl at 82% Bl = 3 mm and for XC at 75% Cms minimum was 2.1 mm, which means the compliance is the most limiting factor for prescribed distortion level of 10%. However, using the less conservative 20% distortion criteria of Bl decreasing to 70% and Cms decreasing to 50%, the XBl and XC numbers are both greater than 3.9 mm.
Figure 9 gives the inductance curves L(X). With an aluminum shorting ring installed in the 6PR160, the inductance swing for this driver is a maximum of 0.07 mH, which is very good inductive performance.
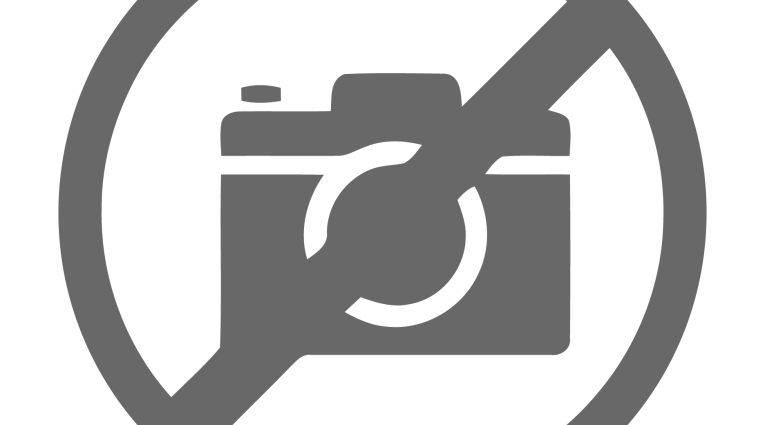
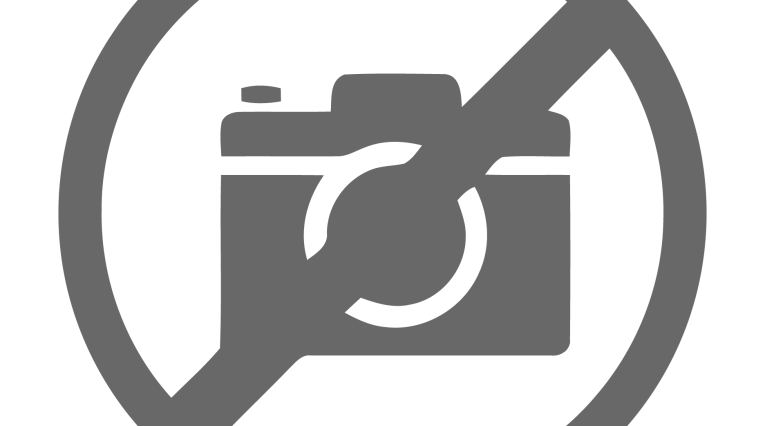
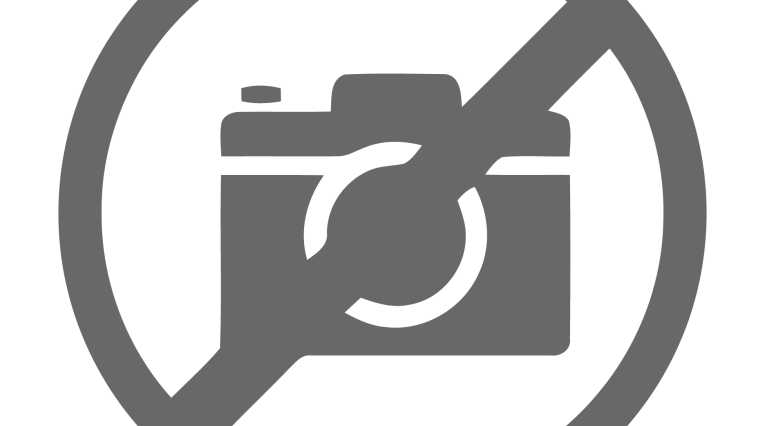
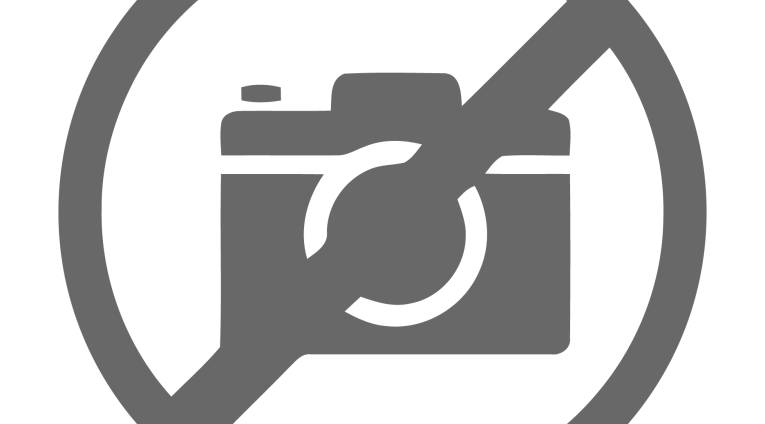
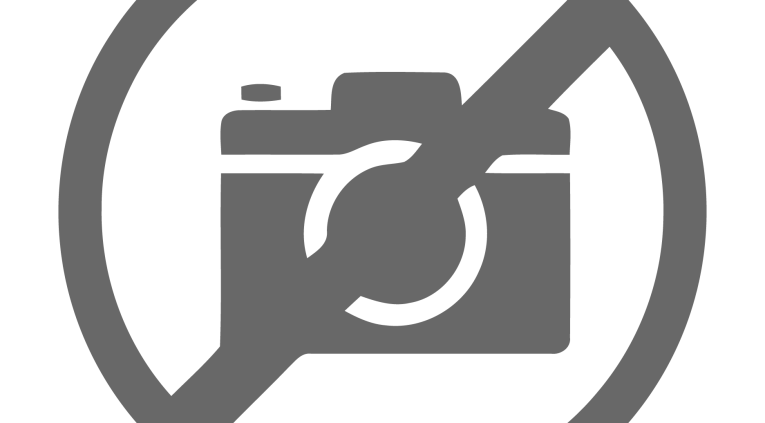
With the Klippel testing completed, I mounted the 6PR160 in a foam-filled enclosure that had a 15”× 8” baffle and then measured the device under test (DUT), using the LOUDSOFT FINE R+D analyzer and the GRAS 46BE microphone (courtesy of LOUDSOFT and GRAS Sound & Vibration).
I measured both on and off axis from 200 Hz to 20 kHz at 2 V/0.5 m normalized to 2.83 V/1 m (one of the really cool tricks FINE R+D can do) using the cosine windowed Fast Fourier Transform (FFT) method. Figure 10 gives the 6PR160’s on-axis response, indicating a fairly smooth rising response with no break up modes or peaking out to about 5.8 kHz, where the driver begins its low-pass roll-off.
Figure 11 displays the on- and off-axis frequency response at 0°, 15°, 30°, and 45°, showing somewhat more directivity than most home audio 6” woofers. The -3 dB at 30° with respect to the on-axis curve occurs at 2 kHz, so a cross point in that vicinity should work well to achieve good power response. Figure 12 shows the normalized version of Figure 11. Figure 13 displays the CLIO horizontal polar plot (in 10° increments). And finally, Figure 14 gives the two-sample SPL comparisons for the 6PR160, showing a close match throughout the operating range.
For the remaining tests, I employed the Listen SoundCheck AudioConnect analyzer and SCM microphone to measure distortion and generate time-frequency plots. For the distortion measurement, I mounted the 6PR160 rigidly in free-air and set the SPL to 104 dB at 1 m (10.7 V) using a pink noise stimulus. Then, I measured the distortion with the Listen microphone placed 10 cm from the driver.
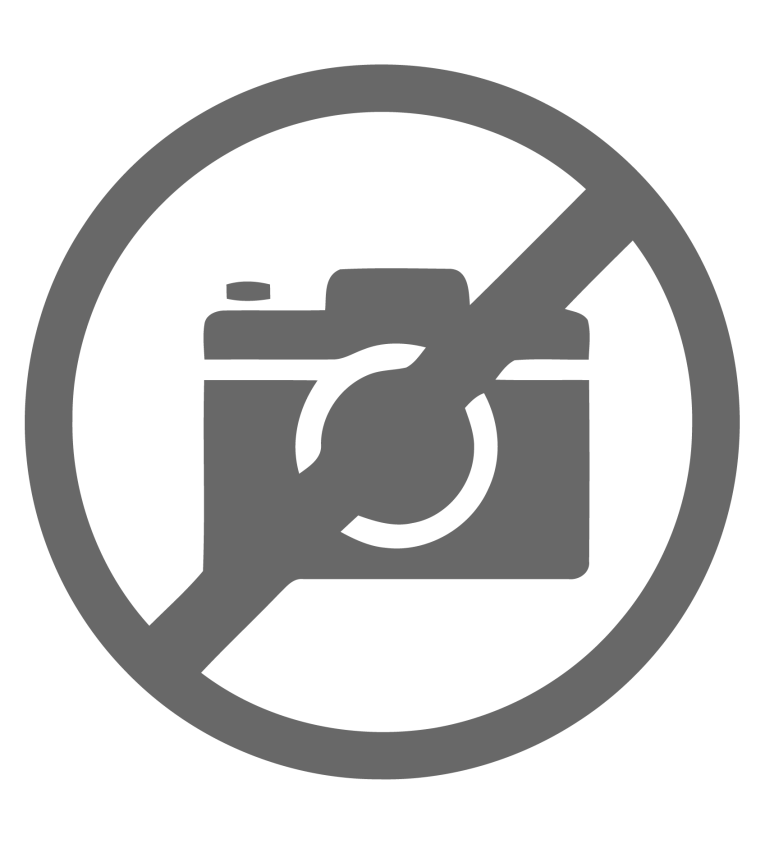
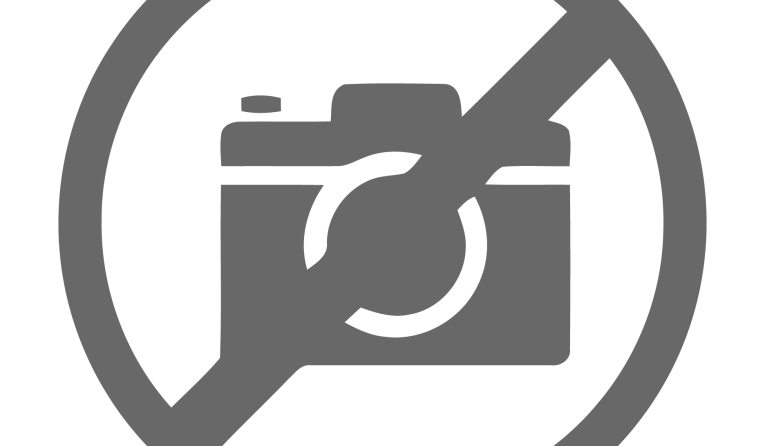
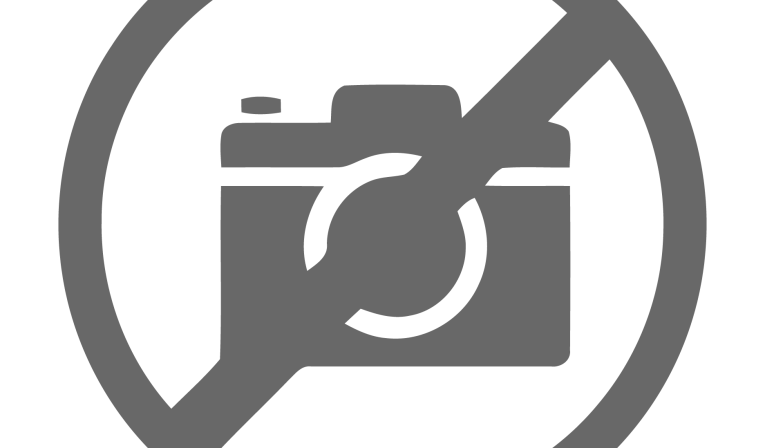
plot.
Figure 15 shows the distortion curves. I then used SoundCheck to get a 2.83 V/1 m impulse response and imported the data into Listen’s SoundMap Time/Frequency software. Figure 16 shows the resulting cumulative spectral decay (CSD) waterfall plot. Figure 17 shows the Wigner-Ville plot, which I used for its better low-frequency performance.
Looking at the data for the 6PR160, it depicts the kind of engineering integrity and high build quality you would expect from Faital Pro. For more information about the company, visit https://faitalpro.com. VC
This article was originally published in Voice Coil, June 2019.