
Serious hi-fi enthusiasts get excited about the musical experience delivered by electrostatic headphones. Producing a natural, airy sound, they provide greater clarity, less distortion, and extended bandwidth when compared to other types of headphones where high-resolution audio sources are involved.
Most electrostatic speakers apply an electric charge on a thin elastic membrane situated between two conductive plates. The charged membrane moves in direct response to the electrical input, generating the sound waves that our ears and brain interpret as music, and moving us to joy and tears.
Despite their high quality and accurate audio reproduction, electrostatic speakers can be prohibitively expensive, sometimes fragile, and until recently, were handmade because of mechanical precision requirements. Seeing a need for affordable, high-quality headphones that could be more easily manufactured, Warwick Audio Technologies, Ltd. designed the High-Precision Electrostatic Laminate (HPEL) transducer, a patented technology based on an ultra-thin diaphragm and a single conductive plate instead of a pair (see Photo 1). With its origins at Warwick University in the UK, Warwick Audio has developed a lightweight laminate only 0.7 mm thick that is perfectly suited for electrostatic headphones.
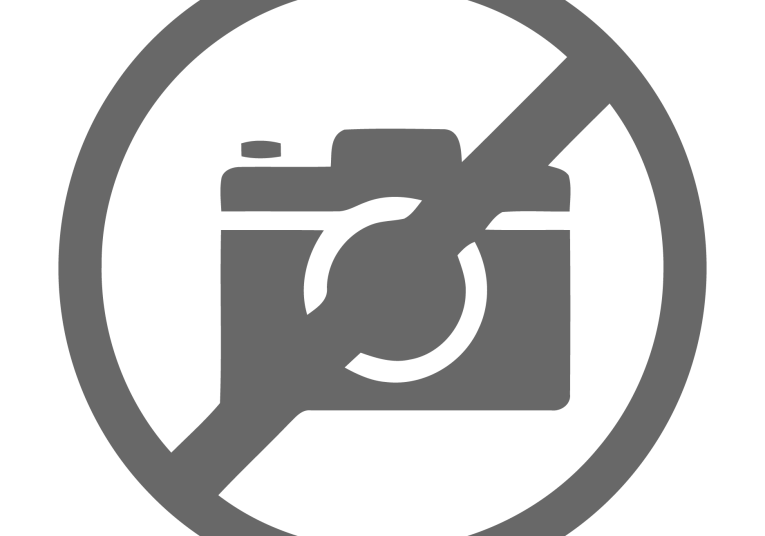
The new HPELs are lightweight thin-film structures manufactured through a semi-automated lamination process. “The technology we’ve developed is unique,” explains Martin Roberts, Diretor of Warwick Audio Technologies (WAT) and MD of Sonoma Acoustics. “The HPEL transducer is made up of a metallized polypropylene film, a polymer spacer with hexagonal cells, and a conductive mesh” (see Photo 2).
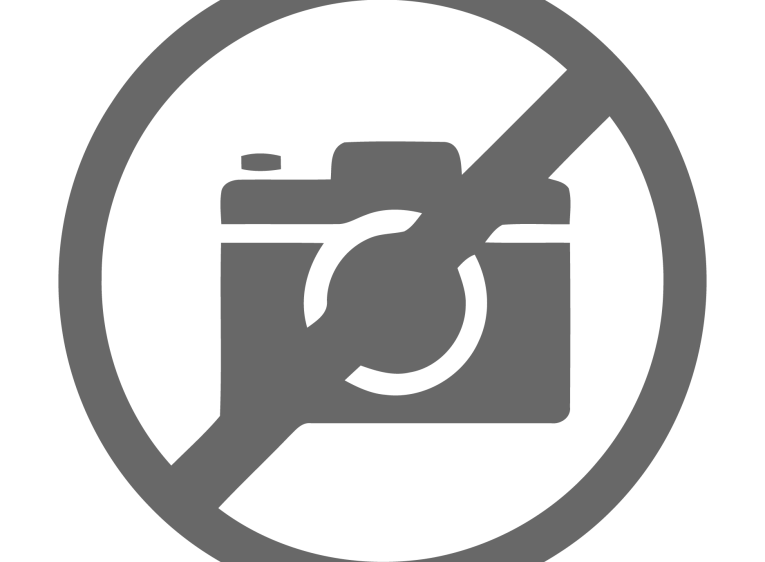
In the typical setup, direct current (DC) bias voltage is applied to the elastic membrane and alternating current (AC) drive signal to the surrounding plates. Warwick’s one-sided speaker involves both the DC bias and the AC drive signal applied to the elastic membrane, with a single wire mesh (plate) positioned opposite the membrane as a ground plane. The fabrication method makes it possible to reproduce the transducers at a significantly lower cost than traditional electrostatic speakers. This means that for the first time, electrostatics may be considered a commercially viable high-resolution audio option across a wide range of device types and market segments.
Simulating Acoustic Playback
To develop a transducer like this, which can be easily manufactured and inexpensive without compromising sound quality, the Warwick Audio team thoroughly investigated the influence of many design elements before settling on a final version. “We had developed numerous prototypes that clearly performed. The big issue was that we were not entirely sure how varying individual material and design parameters affected the transducer’s performance,” Roberts says.
The dynamics of the HPEL are dependent on the extremely complex interplay between membrane tension, AC signal level, speaker geometry, elastic and dielectric material properties, thermoacoustic losses, and the added mass effects of the air next to the open side of the membrane. The designers wanted to improve bass performance by reducing low-end roll-off, minimizing distortion, and maximizing the sound pressure level for a given electrical input. But they discovered that small changes to any component greatly affected the acoustic output.
Although Warwick Audio had significant mechanical, electrical, and acoustic expertise, they had no in-house simulation capability to help them understand this interplay. In order to perform a virtual optimization of the HPEL transducer design, they enlisted the help of Xi Engineering, a COMSOL Certified Consultant firm that specializes in computational modeling, design recommendations, and solving noise and vibration problems in machinery and other technology.
Dr. Brett Marmo, technical director of Xi Engineering, oversaw the development of the COMSOL Multiphysics software models they used to analyze the behavior of the HPEL. COMSOL software enabled Xi Engineering to model nonlinear effects that would arise with amendments to the HPEL’s asymmetrical design.
“We kept the early model simple, focusing on specifics that influence sound quality. For example, keeping the first harmonic as low as possible to understand the acoustic-structure interaction and the HPEL’s performance at low frequency,” Marmo explains, describing their preliminary tests. “Our model showed how applied voltage affects signal levels, which helped us understand sound distortion for an initial case.”
Because the transducer is one-sided, the electrostatic force varies with the position of the vibrating membrane, decreasing with the square of the distance between the membrane and the mesh. Once they understood the resulting nonlinear distortion and were able to predict its effects, the Warwick engineers could then electrically cancel any related distortions.
Perfecting the HPEL Transducer Design
In a more extensive simulation that involved a structural-MEMS-acoustic coupling, he examined the impact of adjusting parameters like the size of the hexagonal cells in the wire mesh, thickness of the wires, membrane tension, spacing between membrane and mesh, and material properties of each component. Marmo and his colleagues also studied the effects of different DC biases, which are often responsible for distortion at low frequencies, and looked at conductivity along the plate to discern whether voltages were higher in one area than another. They then used COMSOL to study the thermoacoustic losses and model the displacement of the membrane for different frequencies (see Figure 1).
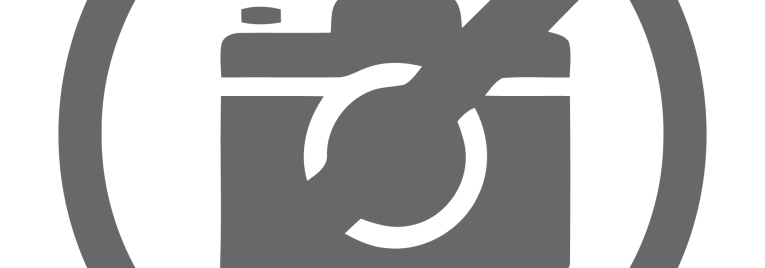
“We found that this type of simulation was the only accurate way to truly model planar electrostatic transducers,” Marmo continues. “For this case, lumped parameter modeling can characterize limited aspects of performance, such as low-frequency amplitude response. One parameter might be excellent but there may be significant distortion created elsewhere. Multiphysics modeling encompasses all dimensions that affect our perception of sound, such as the time-domain response and nonlinear distortion.”
The simulations made it possible for the engineers at Warwick to tweak design parameters in order to optimize overall performance. Ultimately, they were able to predict what was causing spikes in the frequency response and smooth out the signal for better fidelity.
“This represented a huge cost and time benefit for us,” says Roberts. “We went from making multiple prototypes by hand each week to simply dialing up a new one in the software. In addition to settling on a final design we’re very happy with, it is now easy for us to customize our transducers for clients’ individual requirements.”
Marmo’s team compared each model with physical measurements provided by the Warwick design team. “The simulation results were astoundingly close to the physical measurements,” comments Dan Anagnos, CTO at WAT. “That was probably the most exciting aspect, seeing the simulation come to life and knowing it was giving us an accurate picture of how the speaker would perform.”
Freedom and Flexibility with a Simulation App
With simulation results verified and Warwick satisfied with their design, the next step was for Xi Engineering to put Warwick in control of further modeling. The Application Builder available in COMSOL software enabled Marmo’s team to build an app from their simulation and host it online.
The app’s interface allows users to change certain inputs to test changes to a number of parameters, such as the DC bias, AC signal level, frequency range and resolution, material properties, speaker size, wire mesh shape and size, and spacer placement (see Photo 3). The original model setup is not accessible from the app; instead, it allows users to run further tests without needing to learn the software.
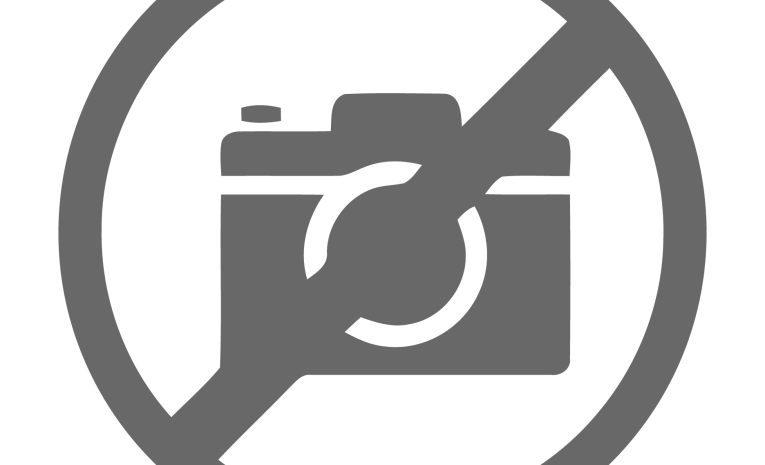
“Providing Warwick with a simulation app removed the need for them to purchase the software or appoint an experienced user,” Marmo says. “Simulation apps put customers in charge, so they don’t have to come back to us for small changes and they can test exactly what they want. It also frees us to explore new challenges, rather than working on variations of the same problem.” Xi Engineering expects to use computational apps more and more in the course of its work for other customers.
Warwick is doing the same, sharing the app with their own customers — companies wanting to find the HPEL transducer best suited to their particular headphone designs.
“The team at Xi Engineering have been superb. They have deep expertise and helped to unpack the complexity of our product,” adds Roberts. “The intuitive app that Xi developed for us is an additional bonus. Without revealing any intellectual property, we can give our own clients access to our design through the app, so they can test and incorporate the technology into their own high-end headphones.”
Warwick Audio’s HPEL Electrostatic System
HPEL transducers are manufactured exclusively by Warwick Audio Technologies, Ltd. in the United Kingdom. The Warwick HPEL transducer is available to OEMs and ODMs for licensing in a range of headphone and loudspeaker products.
HPEL transducers are manufactured by a bespoke, semi-automated process with finished laminates assembled into HPEL support frames or “cassettes.” This means that customization for individual customer needs is both simple and relatively inexpensive. HPEL transducers can be customized in size (surface area) and be formed in nearly any shape—round, oval, rectangular, etc., including flat or curved. Various internal cell sizes and shapes can be accommodated, and custom mounting frames can be molded to specific requirements, with various electrical termination schemes from their integrated PCBs.
HPEL transducers show a linear performance from the lowest frequencies, around 10 Hz, to the highest frequencies, above 50 kHz, with a surprising wide dynamic range. Dynamic range is not defined by how loud a system can play, but by how quiet it can play while still resolving very low level detail and information accurately. This translates into resolving ability at the bottom end of the dynamic range, defined by the noise floor and distortion limits. Dynamics also means how quickly a system can go from very quiet levels to very loud levels, and vice versa—the transition in between must be “lightning-fast” and effortless.
Thanks to its very large diaphragm area without separate suspension components, HPEL transducers also show superior performance in terms of harmonic, intermodulation and transient intermodulation distortion with great time domain fidelity, the result of its 15 μm thick diaphragm with ultra-low moving mass.
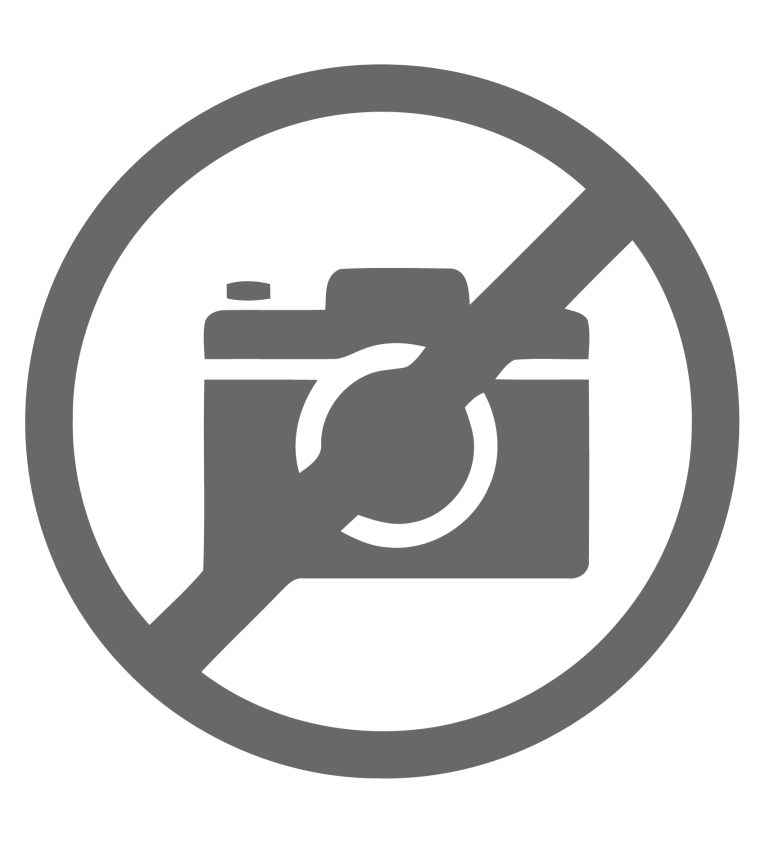
A sound reproduction system is only as good as its weakest link. For this reason, Warwick Audio Technologies has designed HPEL proprietary drive electronics to meet two goals:
- To reproduce Hi-Res Audio without degradation or compromise — ensuring that the electronic circuitry has superior audio performance in terms of wide bandwidth and dynamic range, low noise and distortion, and requisite time domain fidelity.
- To energize and power the HPEL transducer in the most ideal manner, fully optimized for the reactive load impedance over the entire operating range.
Driving the HPEL transducer effectively requires highly specialized electronic circuitry that will provide a high charge voltage or bias, of 1350 VDC and amplify the audio signal to high voltages — as high as 425 VPEAK — over the full operating range and load impedance variation of the HPEL. The electrostatic drive principal upon which the HPEL transducer is based requires a high DC voltage to be applied to the diaphragm to establish an adequate static charge (aka, “energizing”). This charge forms the basis for the electrostatic force that will move the diaphragm.
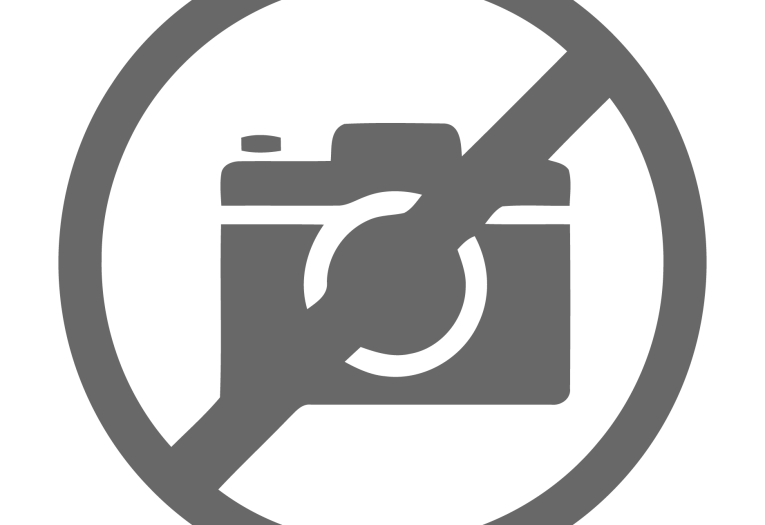
The HPEL transducer presents a reactive load impedance that is quite unlike standard electrodynamic and planar magnet transducers. The impedance increases in capacitance as frequency increases, approaching a purely capacitive load at high frequencies (especially above 20 kHz). This means that the AC amplification circuitry must be able to drive very high voltage swings at low frequencies and deliver high current at high frequencies. Warwick’s circuitry can drive the HPEL transducer with over 145 VRMS without clipping or distorting, even at higher frequencies, where the load approaches a dead short (0 Ω).
These drive requirements are implemented in best-in-class operational topologies for audio reproduction, and Warwick’s HPEL Drive Electronics use discrete transistor output stages and high-quality carefully selected passive components. Designs are available in various configurations to address portable, mobile and low power applications as well as stand-alone, at-home and in-studio use.
An assembled printed circuit board (PCB-A) provides a turn-key solution for ultra-high performance headphones and small form-factor loudspeakers for home use. This PCB combines a discrete FET Class A amplifier with very low distortion and wide bandwidth, custom 64-bit, double-precision, fixed-point DSP, with all incoming analog signals converted to digital ahead of the DSP from a multi-channel 32-bit/384 kHz AKM Premium ADC, which delivers a measured signal-to-noise ratio (SNR) in excess of 120 dB.
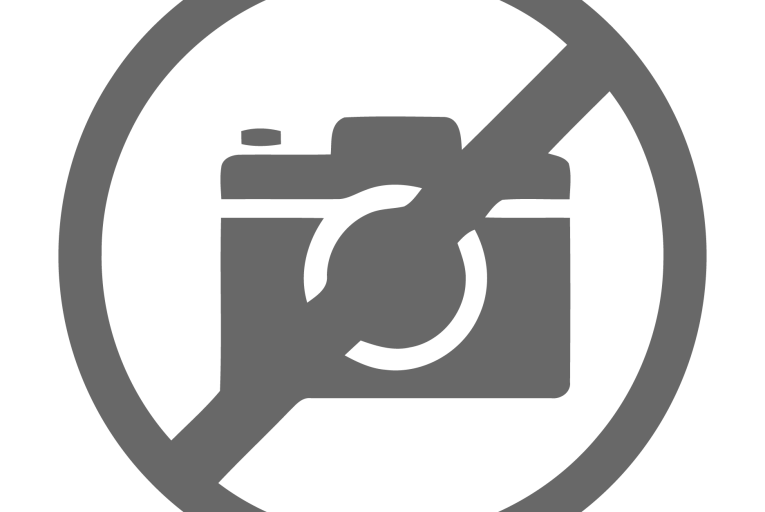
To guarantee the highest performance regardless of the input signal format, the design uses an ultra-low phase noise oscillator from Crystek, operating at 100 MHz and the output analog signals are converted using two ESS Sabre 32-bit Reference DAC chips, each operated in mono mode to provide a measured 129 dB signal-to-noise ratio. All audio circuitry is supplied by multiple stages of ultra-low noise, high current linear regulators from Analog Devices. Isolated power regulation stages are used for both analog and digital sections as well as high and low level circuit stages. These regulation stages are fed by a custom-designed, universal voltage, outboard switch-mode power supply unit, capable of delivering about 3.5 times the maximum power the amplifier is designed to draw under steady-state conditions. In addition, the unit uses a fixed high frequency switcher (operating at over 85 kHz) to avoid the possibility of any switching noise entering the audio band. This unit is designed with improved internal filtering to yield extremely low noise and ripple (< 50 mVPP).
Mobile Applications
Designed for mobile Hi-Res Audio reproduction where low power consumption and compact designs are essential, Warwick’s HPEL Portable Drive Electronics Modules are another solution for driving the company’s HPEL transducers in any portable application. These drive electronics were designed in the form of miniaturized “daughter-board” modules that provide a turn-key solution for mobile headphones, small, battery-powered and wireless, loudspeakers, Virtual Reality headsets, or even specialized OEM automotive, marine and aerospace applications.
Warwick’s HPEL Portable Drive Electronics Modules are meant to be driven from a standard low voltage DC power source or by standard 3.7 VDC lithium polymer rechargeable batteries.
The modules feature discrete amplifiers optimized to drive HPELs in a small form-factor, and can be configured as mono, stereo or multi-channel, with or without power supply. The ultra-efficient design draws < 250 mW in typical use, and provide 8+ hours of life from a 500 mAh battery, in stereo headphone applications.
Analog inputs are configurable to match any low level input source, and the modules feature pre-processing, and multi-band parametric EQ for sound optimization and customization from an external DSP.
www.comsol.com
www.warwickacoustics.com
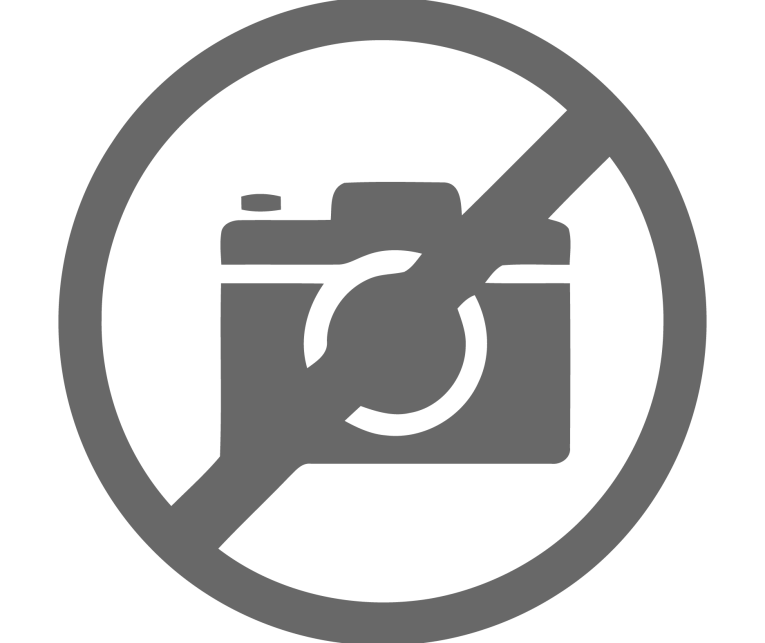
The Sonoma M1 Headphone System
The first product using Warwick Audio’s complete HPEL technology is the multi-award winning Sonoma M1 Headphone System. This comprises the M1 circumaural headphone, the world’s first to use HPEL audio transducers, and the dedicated DAC & Energizer electronics. One cannot be used without the other, and Sonoma sells the complete integrated package, including the connecting cable, designed in collaboration with Straight Wire, Inc. At the amplifier end, the jack is electrically isolated from the amplifier chassis, while on the headphones high-precision self-latching connectors are used to ensure a secure connection. A sense loop built into the cable runs to each ear cup, and if the cable is disconnected at either the amplifier or headphone ends then the amplifier automatically shuts itself down.
The dedicated headphone amplifier features USB 2.0, and coaxial S/PDIF for digital inputs, as well as RCA (x2) jacks, and a 3.5 mm stereo jack as analog inputs. The USB 2.0 input accepts all Hi-Res Audio formats up to 32-bit/384 kHz PCM and DSD via DoP (DSD64/DSD128), while the S/PDIF input accepts all PCM formats up to 24-bit/192 kHz. The high-level RCA inputs operate with a maximum input signal of 2.1 V (rms), while the low-level 3.5 mm jack accepts a maximum signal of 850 mV (rms).
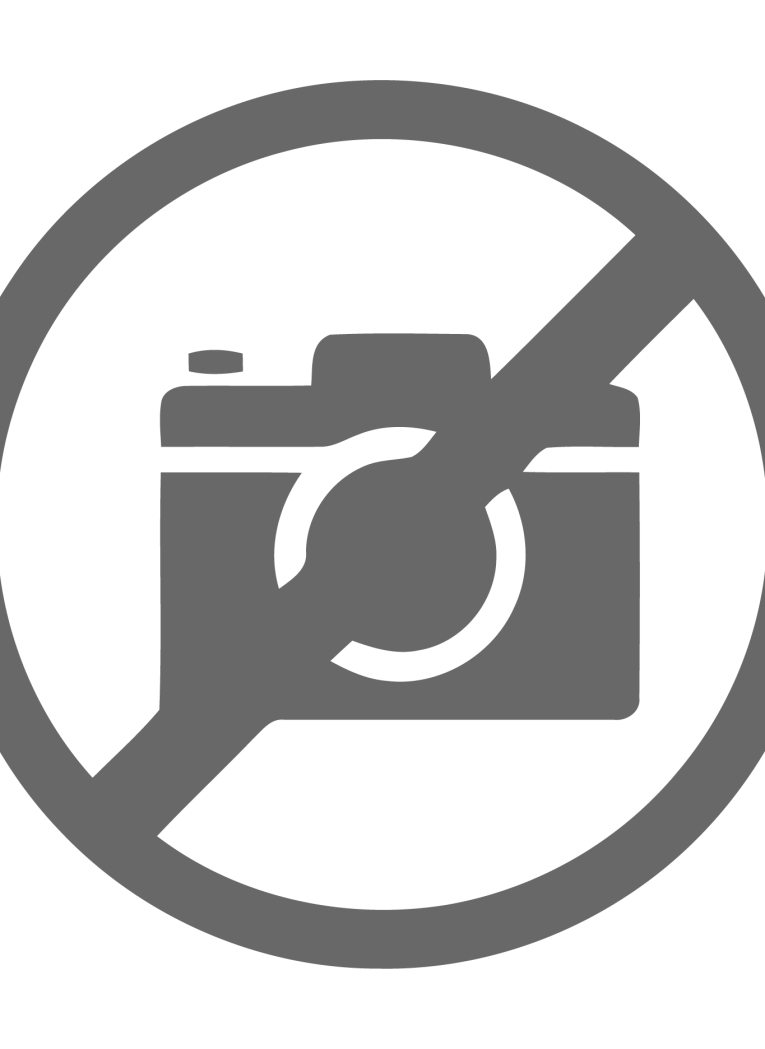
This article was originally published in audioXpress, April 2018.