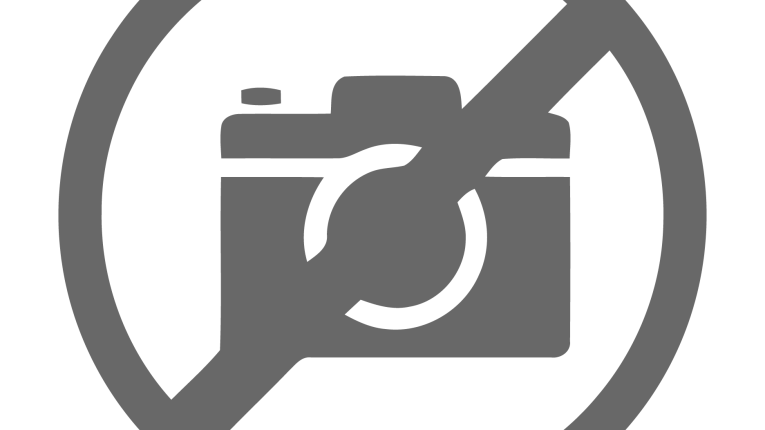
Iron Nitride and an Inside Look at Niron Magnetics
When a speaker development project is initiated, one of the first decisions is the magnet type — ferrite or neodymium. Ferrite magnet compounds are low-cost ceramics produced from iron oxide, blended with metallic elements such as strontium and barium. Neodymium (neo) is a rare earth element (REE) that—when used in an alloy composed of neodymium (Nd), iron (Fe), and boron (B)—generates a magnetic force that dwarfs that of ferrite. When light weight, compact size, and efficiency are critical, speakers rely on neo. However, designers often choose ferrite when price stability and cost are the deciding factors. And yet, there are several risks to consider associated with neo including: demand competition, supply shortages, price inflation, and geopolitical risk. While some speaker designers are opting for ferrite, taking the weight/size/performance hit that comes with it, others don’t have this option, and they are looking for a way to break the compromise.
Loudspeakers and associated consumer electronics consume about 31,000 tons of magnets annually, projected to reach 43,000 tons by 2030. While this is a real business, the loudspeaker market’s share of magnet consumption is shrinking as demand from big magnet-consuming applications, namely electric vehicle motors and wind turbines, surges. The speaker industry is already facing increased competition for neo. Analysts project global demand will outstrip neodymium supply as early as 2022.
Geopolitical tension makes matters worse. Neodymium magnet fabrication is predominately in China. Export price manipulation of neodymium magnets is used by China as a strategic trade negotiation tool. The lessons learned from 2011, when a government limit on export quotas caused prices to jump more than 10×, are hard to ignore, especially given our present-day experience with rocketing neo prices. Not to pile it on, but increasing shipping costs and the current logistical nightmare of the global supply chain don’t improve cost outlooks.
In “The State of Loudspeaker Magnetics” (Voice Coil, October 2021), we mentioned that the tide appears to be coming back to US shores with a large magnet distributor restarting its ferrite magnet manufacturing. Ambitious soup-to-nuts neo US initiatives include reactivation of the Hitachi Metals North Carolina facility (acquired by USA Rare Earth) and California-based MP Materials Corp. expanding from mining to chemical separation and eventually to finished magnet production. It’s all in response to this convergence of geopolitical and absolute supply risk.
Last, and increasingly important to consumers and companies alike, neodymium is under fire for carbon dioxide emissions, radioactive waste, and environmental contamination from acid by-products. The growing consumer preference for environmentally friendly products and the prevalence of companies setting aggressive sustainability targets has put rare earth magnets in the crosshairs.
Magnetic materials are explicitly called out by Apple, which recently committed to using only recycled magnets in new iPhones. Urban Mining, a neo recycling facility in Texas, projects it will start supplying customers in the speaker industry this year. But neo recycling is in its infancy and, even as it improves, rising demand means we can’t recycle our way out of the problem. We need a new solution.
Introducing Niron
Perhaps the biggest news in magnets in 40 years is Iron Nitride (FeN). While many people have recognized the potential of a powerful magnet made from globally available commodities with low price volatility, practical development of the process required time, money, and commitment. The problem has been that consistent synthesis of magnetic iron nitride is notoriously difficult, and commercially viable production would require a breakthrough.
Enter Niron Magnetics. The Niron story starts in 2002 at the Electrical and Computer Engineering Department at the University of Minnesota. Dr. Jian-Ping Wang, a leading physicist and material scientist in the field of magnetics, and a small army of Ph.D. students began untangling the mysteries of this material. After eight years of fundamental research with the collaboration of research scientists at four US Department of Energy (DoE) national research facilities (Oak Ridge, Argonne, Brookhaven, and Los Alamos), the team was awarded a project to develop a permanent magnet based on iron nitride.
Spun off from the University of Minnesota in 2014, Niron Magnetics now operates in a dedicated industrial lab facility and has been funded with $34 million to date (including $6 million from the DoE). Combining breakthroughs in nano materials with mature metallurgical methods, they are leading the commercialization of Iron Nitride. If successful, their product will promise the best characteristics of neo without the supply chain drama, at a price point that rests somewhere between ferrite and neodymium.
So What Is Iron Nitride?
As the name suggests, Iron Nitride is composed of common elements—iron and nitrogen. Manufacturing a magnet using these common elements unlocks a whole host of benefits: Magnets that are less expensive, more sustainable, globally available, and not subject to supply constraints or price instability. As a bonus, Iron Nitride has inherent temperature stability that ensures performance doesn’t falter at speaker operating temps where neo falls off or requires expensive dopants.
Dr. Jian-Ping Wang’s early work confirmed the potential of Iron Nitride as a magnet material with high magnetic saturation. While no manufactured product of any material starts at the theoretical maximum, it illustrates the boundaries of what’s possible. We remember the early neo grades from China were 25 MGOe. Today, commodity neo grades are just over 30 MGOe and premium grades have broken 50 MGOe. So, if the sky’s the limit for Iron Nitride, where do things begin?
Two New Magnet Options for Speaker Designers
Existing speaker magnet design choices are highly polarized. The Niron magnet family fills a set of market gaps and resolves the material trade-off that has long existed between ferrite and neo.
Niron’s product roadmap climbs the ladder of performance. The first commercially available Iron Nitride magnet, Generation 1, seeks to break the compromise between ferrite and NdFeB magnets. Its price-performance positioning will give designers the option to upgrade from ferrite in applications where size, weight, and performance matter, but neo is too pricey and volatile or (alternatively) substitute neo in applications where price-performance, environmental sustainability, and temperature stability matter in addition to absolute size and weight.
The advantage is likely most compelling in applications where cost and size/weight pressure converge, where speakers need to maintain performance at higher operating temperatures, where long-term purchasing agreements make price volatility a serious risk, and where there is a consumer-facing sustainability branding opportunity. Autosound comes to mind as a potential sweet spot.
The company’s second product, Generation 2, looks to compete with neodymium based on absolute performance. Targeted for 2023, it follows neo’s path to higher residual flux density, competing with a significant portion of available neo options, with superior temperature tolerance.
Superior High-Temperature Performance
Stable performance across a wide temperature range makes Niron especially competitive against temperature-doped grades of neo, primarily because of the cost of the dopant dysprosium. For high power neo magnet speaker operation, Dysprosium Oxide is part of the neo recipe to avoid real-time performance loss and partial demagnetization—and this additive costs 4× the price of neo!
Iron Nitride’s material structure offers superior temperature performance without the expensive additives. Iron Nitride has a low reversible temperature coefficient, which means that it holds its magnetic properties at high operating temperatures slightly better than ferrite and significantly better than neo.
Environmentally Sustainable
Compared to neodymium, Iron Nitride avoids significant environmental damage across water contamination, radioactive waste, and acidic byproducts from mining and processing steps that are required for neo. As companies and consumers take steps to mitigate climate change, Iron Nitride generates ~70% less C02 emissions over its lifecycle vs. comparable grades of neodymium. This is assuming non-recycled inputs.
At present, Niron is refining the process by which it can use recycled steel as a source of iron to further improve the material’s sustainability. Niron is branding both Generation 1 and Generation 2 of its Iron Nitride magnets as Clean Earth Magnets—the data suggests they’ll live up to the name.
Easy to Magnetize (Even in Assembled Magnetic Structures)
While the speaker industry enjoyed being able to magnetize magnetic structures with ferrite magnets, the challenge in the magnetization process of neodymium magnets was a rude awakening with huge and expensive magnetizing machines and fixtures. The fix was buying pre-charged (or pre-magnetized) neo slugs and bruised fingers.
The in-situ magnetization of magnetic assemblies with Niron magnets will be possible utilizing the current magnetization technology (magnetizing machines and fixtures), while pre-charged will be more common for Niron’s Generation 2 magnets.
The magnetization process of Niron’s Generation 1 magnets will be easy and fast. The magnetization and saturation characteristics of the Generation 1 magnets are projected to permit magnetizing loudspeaker assemblies employing short cycle times, potentially increasing the production of loudspeakers.
Finally, the magnetization and saturation characteristics of the Generation 2 magnets will permit magnet assemblies to be magnetized utilizing less energy compared with the energy utilized to magnetize neodymium magnets. As such, it may offer the benefit of an increased lifetime for magnetizing fixtures utilized in the magnetization process and permit reduction of the magnetization time required to increase the production of loudspeakers.
Commercial Production for Niron
What does commercial production look like for Niron? What, if any, challenges must be overcome? Working out of an industrial lab today, Niron is not yet churning out Iron Nitride magnets from the assembly line and shipping them to speaker manufacturers around the globe. However, because commercialization has always been the focus, the manufacturing methods Niron is employing in the lab today are all validated as being highly scalable, existing at the thousand-ton scale today in service of similar materials for other industries. These processes will soon face the test, as Niron has begun construction of a pilot production facility, intended to produce samples of the Generation 1 magnet.
Niron Magnetics has also begun working closely with a selection of leading speaker design and manufacturing companies, doing the design work to optimize existing speakers for the integration of iron nitride magnets and to secure a competitive edge.
Niron’s Performance
How does Iron Nitride perform in a speaker? The authors of this article recently worked with Niron Magnetics to complete preliminary magnetic studies using finite element simulations of the Niron magnet material in a variety of form factors and adjusting design parameters to optimize the magnetic return structures and extract maximum magnetic performance.
Several loudspeaker topologies have been studied and initial optimization work conducted, among them the magnetic structures of headphone drivers where Niron’s Generation 2 magnets have been studied and compared with sintered neodymium magnets. Initial findings suggest that Generation 2 magnets offer a more distinct advantage for loudspeakers where higher magnetic gap strengths are targeted. Magnetic headphone structures with a sintered neodymium magnet and with a Niron Generation 2 magnet were optimized to produce 1T in a 1mm air gap.
Figure 1 compares the magnetic field distributions for the magnetic headphone structures equipped with a sintered neodymium magnet (a) and with a Niron Generation 2 magnet (b). Figure 2 shows the magnetic field distributions in the air gap region of the headphone drivers. From Figure 2, you can see that both headphone drivers produce the same flux density in the air gap region with a maximum value of flux density of 1T. The magnetic headphone structure with the Niron Generation 2 magnet presented 10% less magnet weight compared to the neodymium version.
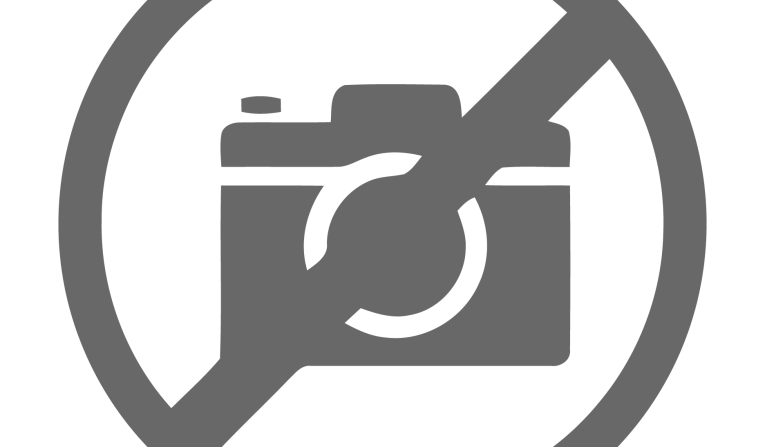
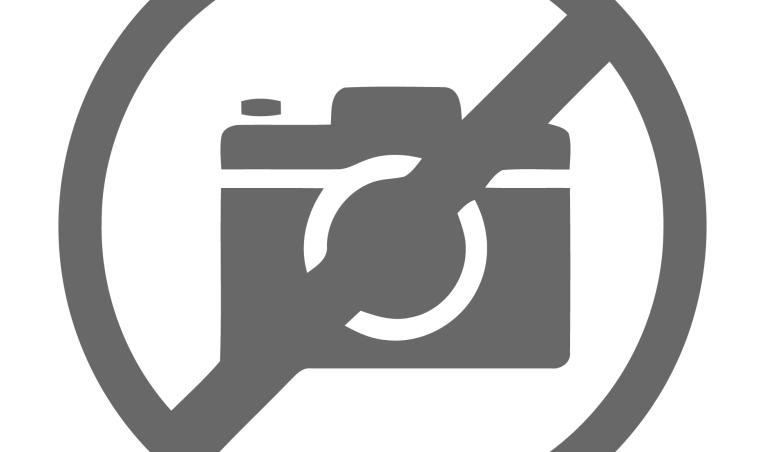
Figure 1: Magnetic field distributions in the magnetic headphone driver structure: a) sintered neodymium magnet and b) Niron Generation 2 magnet
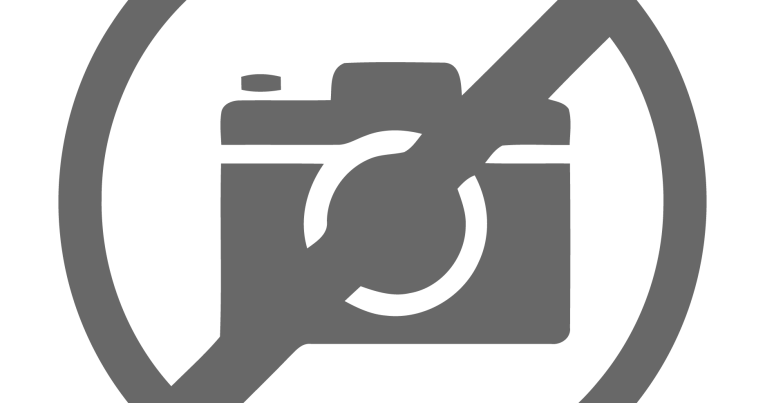
In addition, some woofer magnetic structures with ferrite and Niron’s Generation 1 magnet were analyzed. A commercial 4” woofer with an air gap of 1.2 mm was analyzed and optimized to produce a flux density of 1.3T in the air gap. Figure 3 shows the magnetic field distribution in the magnetic woofer structures equipped with a ferrite magnet (a) and with a Niron Generation 1 magnet (b). Figure 4 shows the size comparison between the ferrite woofer and the Niron Generation 1 woofer. The Niron Generation 1 woofer presented ~two-thirds less magnet volume and weight versus the ferrite woofer. For ferrite applications where weight or footprint is constrained — autosound, soundbars, portable speakers — this could be a game-changer.
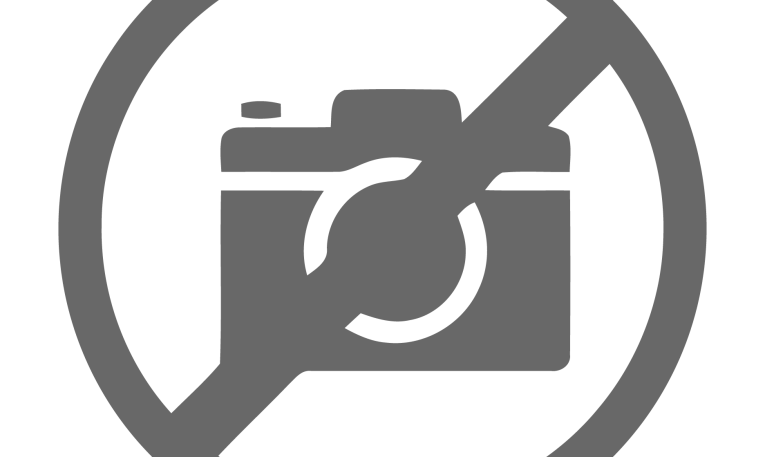
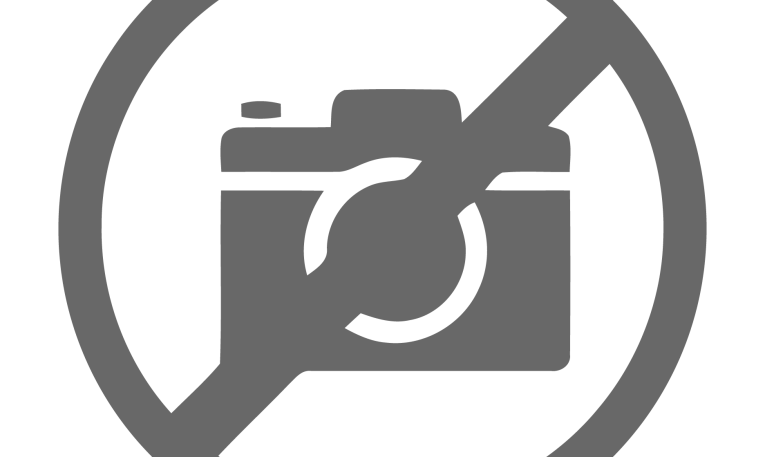
Figure 3: Magnetic field distributions in the magnetic woofer structure: a) ferrite and b) Niron Generation 1
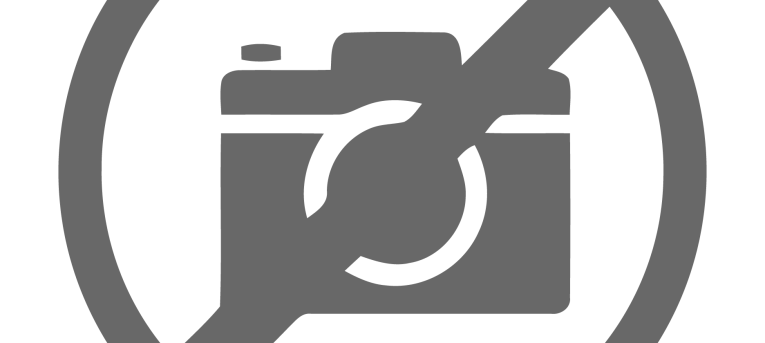
a) ferrite and b) Niron Generation 1
Conclusion
As neodymium costs continue to go up, geopolitical tensions rise, and competition for limited supply is made fiercer by the continued electrification of transport, there are limited magnetic options for speaker companies. The choice for designers has been downgrading to ferrite, raising prices, risking volume, or simply eating the cost. Now, we have Iron Nitride as an option.
As when ferrite displaced AlNiCo in the 1970s, and neodymium at least sharing the stage with ferrite today, integrating new material into speaker designs requires work. But the reward is potentially sweet. For the companies that are willing to take the opportunity, Iron Nitride promises an answer to many of the intractable problems faced by speaker manufacturers today, and a few new benefits to boot.
Niron Magnetics is now working with strategic partners that can closely collaborate with Niron to design the magnets into suitable applications. In return, these partners get priority access to groundbreaking new material and a leg up on competitors. To learn more about Niron Magnetics and its Clean Earth Magnet technology, visit nironmagnetics.com or contact Tom Grainger, Niron’s Director of Strategy and Business Development, who oversees design partnerships. VC
This article was originally published in Voice Coil, January 2022.
Read also the full audioXpress Market Update - Speaker Technology published in January 2022 for a complete overview of latest technologies for speaker applications.