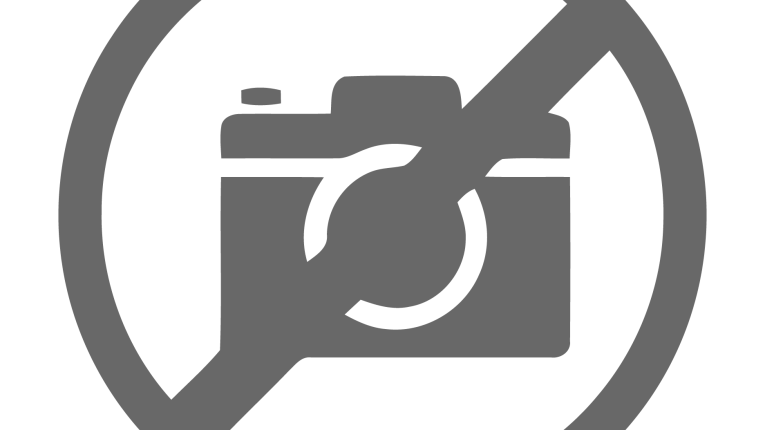
Technology Background and Introduction
Many audio product manufacturers are looking to use advanced fiber-reinforced composite materials to deliver the performance that consumers demand. Unfortunately, lightweighting of products can have unintended consequences; most notably, a lighter product — with all else equal — will have increased dynamic motions. The result of these unwanted vibrations can be as simple as an annoying visual or audible response to as serious as affecting product performance or reducing service life.
It can be shown that increasing structural mass and damping reduces random and point source excitation vibrations. However, the effectiveness of mass treatments varies significantly with frequency and loading. In addition, heavy mass treatments adversely affect structural efficiency, which is the driving factor behind the use of high‐end fiber reinforced composite materials. Other approaches, including rubber isolators and discrete tuned mass dampers, may be termed parasitic (i.e., they can effectively mitigate vibration response) but do so at the penalty of adding weight and cost to the system. The use of viscoelastic materials to attenuate noise and vibration in passive damping devices is well known. In fact, sandwiching elastomeric layers between non elastomeric layers to produce a vibration damping in what are termed as constrained‐layer damping (CLD) configurations are well documented in many engineering textbooks.
In all CLD treatment configurations noise and vibrational energy is dissipated through development of internal shear stresses in the viscoelastic material (VEM) and the damping efficiency increases with the amount of internal shear developed. However, it can be shown that significant shear strain energy is developed only near the free edges or ends of the constrained viscoelastic material. As a result, after the constraining layer reaches a sufficient shear length, damping performance is not improved by further increases in size alone. Use of a very low stiffness viscoelastic material can extend the length of the region in which damping occurs, but at the penalty of a reduction of stiffness of the treatment patch. Under some conditions of pure flexural loading, sufficient shear may be developed to make such treatments effective. However, under in‐plane tension, compression, or torsional load conditions, which exist in many structural configurations, the amount of shear developed in the VEM is very limited and constrained layer approaches are only marginally effective.
Technical Basis for Countervail
The innovative fiber-reinforced composite damping concept, using one or more Countervail layers locally, was patented by Countervail Products LLC, headquartered in Greenville, SC. The construction of the Countervail vibration damping layers have been specifically engineered to produce a systematic spatially varying stiffness. High damping efficiency is obtained by tailoring this stiffness variation to produce a redistribution of the axial force within and between the composite layers. It is this load redistribution between layers in the laminate stack that induces maximum values of energy dissipating shear stress along the entire length of the viscoelastic materials included in the multi‐material Countervail layer(s); not just near the ends, as is the case for CLD treatments.
Study of a tube loaded on one end in the axial direction by a uniform around the circumference displacement serves to clearly illustrate how the engineered Countervail fiber architecture can improve damping in structures and components where natural loading conditions render CLD designs inefficient. The unsymmetric and complex deformed shape shown in Figure 1 and Figure 2 for an axisymmetric input load on a tube that contains two Countervail layers clearly differs from the known response for a tube constructed using commercial‐off‐the‐shelf (COTS) composite materials. One set of elements down the length with the same initial circumferential position has been shaded to highlight the twisting deformation resulting from the Countervail material layers under even a simple longitudinal load. As shown by the position trace of calculated shear stresses, the radial‐circumferential (r‐Ɵ) deformations vary with axial coordinate (Z) and produce all three components of energy dissipating shear stresses that can deliver unparalleled damping loss factors even for simple axial excitation forces.
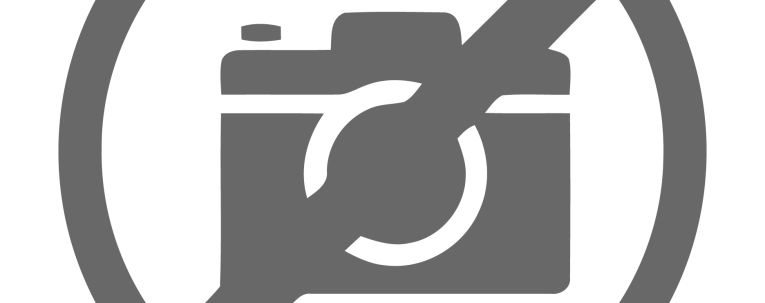
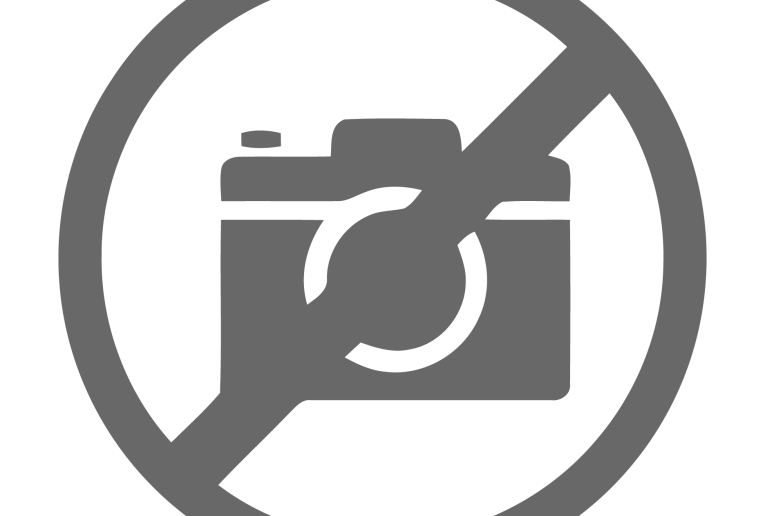
Supporting Data
Observation of the response of tubes subjected to an impulse (drop weight) load, is a simple way to demonstrate how adding just a small amount of Countervail can significantly cancel unwanted vibrations. A steel tube, a carbon fiber baseline tube, and a carbon fiber tube with integral Countervail material layers were fabricated and tested to demonstrate the vibration canceling performance of our material. For reference, all tubes were nominally 25mm diameter and both composite tubes were approximately 3mm to 4mm in thickness. The steel tube thickness was selected so that all had nominally the same frequency contented after impact. An accelerometer was attached to each tube to measure and record the dynamic time response during and after the impact event.
The test results shown in Photo 1 and Figure 3 illustrate two important performance attributes of composite elements (here a tube) that include Countervail vibration canceling layers. First, note that the initial impulse response of the carbon fiber baseline and the tube that contains Countervail layers is nearly identical. This response demonstrates that adding Countervail layers does not significantly change the overall stiffness and mass (structural character) of the construction. Second, the difference in post impact decay of acceleration clearly shows that the Countervail layers have increased the vibration damping of the tube significantly; in other words, by a factor of five times for this specific construction.
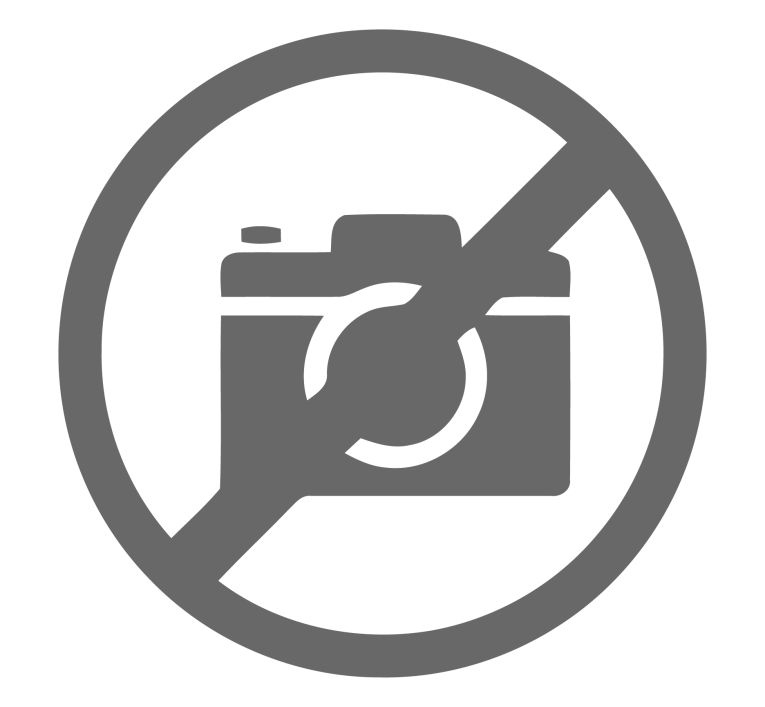
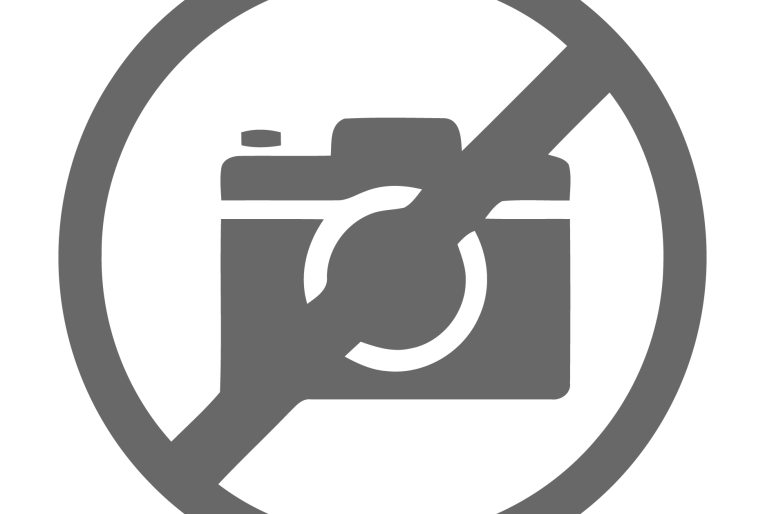
Simple plate foundations (mounts) are another application where lightweighting using fiber reinforced composites can be enhanced by integrating Countervail materials into the laminate to reduce unwanted vibrations and increase structural reliability. The basic test setup used to demonstrate the concept for two composite designs and a baseline aluminum plate is shown schematically and pictorially in Figure 4 and Figure 5. A white noise input spectrum was “colored” using a graphic equalizer, and a power amplifier was used to drive inputs to the system. An accelerometer was mounted at three locations — two on the rigid steel base fixture and one on the plate — to simulate a piece of mounted equipment. The acceleration signal was fed into a signal analyzer to measure and record the acceleration power spectral density.
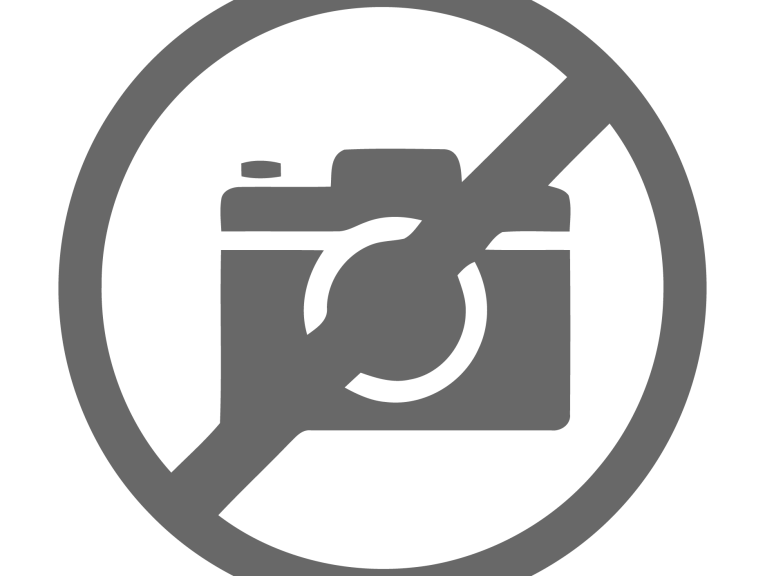
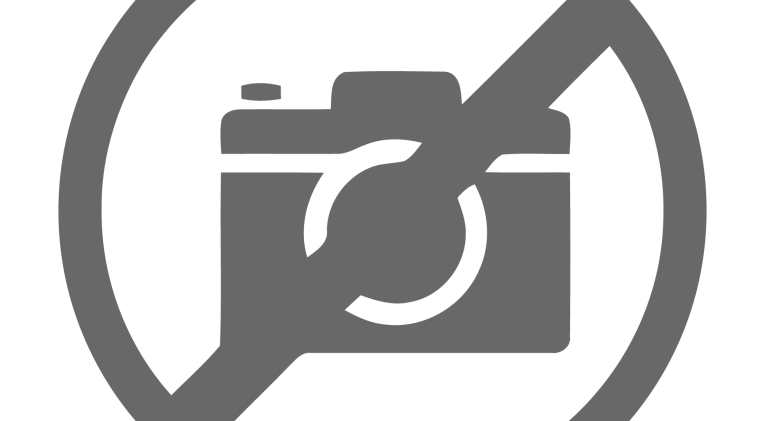
As predicted by supporting dynamic finite element analysis (FEA) of the mounting plate, adding snubbers (i.e., soft rubber washers) between the test plate and the simulated mass significantly reduced the acceleration for the aluminum plate, but had a much smaller effect on the composite plates that included Countervail materials. The random response test results for the simplified mounting plate setup described here show that the SVS composite plates had the potential to dramatically reduce (15 to 20 times g‐rms) the vibration input to equipment mounted to launch vehicle structures.
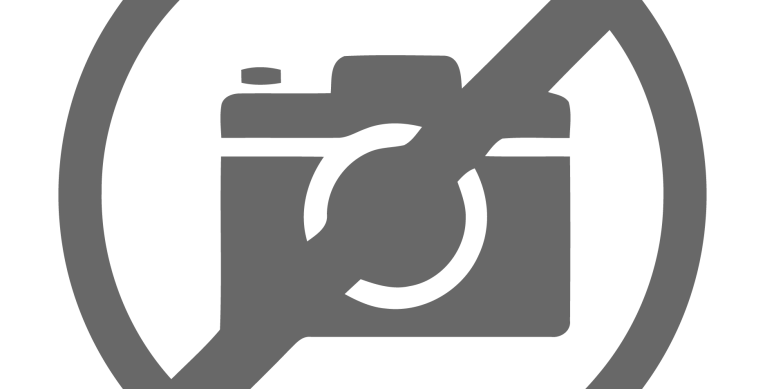
Closing Remarks
The purpose of this article was to introduce readers to an innovative vibration canceling composite material system that combines traditional constrained layer damping concepts, and a patented fiber preform. As shown by the presented data, very high levels of damping can be derived from the fiber pattern designed to maximize energy dissipation in the embedded viscoelastic materials.
Countervail materials are currently produced and sold in two basic product forms; in other words, a fiber-reinforced layer with or without a binding (laminating) resin applied at our factory. Countervail materials shipped with a laminating resin are suitable for components currently manufactured using standard oven‐vacuum bag or autoclave curing or press‐molding processes. Countervail materials without a factory applied resin are compatible with traditional wet manual (hand) layup processes or other machine-controlled liquid resin infusion processes so that integrating Countervail into a component that is currently manufactured using composite materials is seamless and generally will require little-to-no change in tooling or fabrication processes.
Note that Countervail can be added to any number of products made of plastics, wood, ceramic, and more. For more information, contact Countervail's Director Sales and Marketing David A. Stephens on this email, or directly at (+001) 847-867-4525. VC
www.countervailproducts.com
This article was originally published in Voice Coil, November 2024