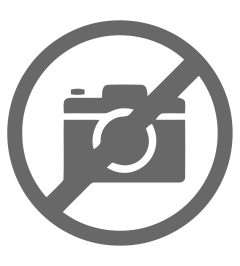
From LP cutter-head electronics to car amps, from the 1kW/ch X1000.5 to the 10W/ch FirstWatt series, from open baffles to giant pipe speakers, Nelson Pass has designed them all… and successfully so. Let’s meet this man who chooses his own direction, and gives generously to the audio DIY community.
Jan Didden (JD): Most readers will be familiar with the audio product line that bears your name, from Pass Labs. Some might also know that before Pass Labs you founded Threshold Corporation, known for among others, the Stasis amplifier series. Less people know that before starting your own company you designed amplifiers for others. Can you talk a bit of that history?
Nelson Pass (NP): Threshold was successful for about eight years before other companies showed interest. For the record, my ownerships have been Threshold, Pass Labs, and General Amplifier
(First Watt). I have collaborated with 13 other brand names that I can remember. A couple of these I should not name, several do not deserve to be named, and the following are ordered chronologically: I worked at ESS, where Peter Werback designed the amplifiers. When I gave up my little side business building car amplifiers (back in the days of Craig and Kraco), I offered Peter my small customer base, and the resulting company, Linear Power, was quite successful until he died in a plane crash. So I filled in part time for a couple years, helping out with amplifier design work, an accounting system, and a subwoofer with motional feedback.
After this I was introduced to Rob Ain and Alec Chenin of Adcom, where I designed the GFA555 amplifier and its relatives. These products were very successful commercially, teaching me to charge more money for my work.
These amplifiers used bipolar transistors in a simple four-stage circuit. The input and voltage gain stages were biased by constant current sources, which drove Darlington emitter-follower output devices. It had an interesting clip detector which sensed feedback overload in the voltage gain stage and lit an LED. It also had a very effective bias circuit which fixed the bias voltage at the output of the driver transistors through local feedback, giving the amplifier improved thermal stability.
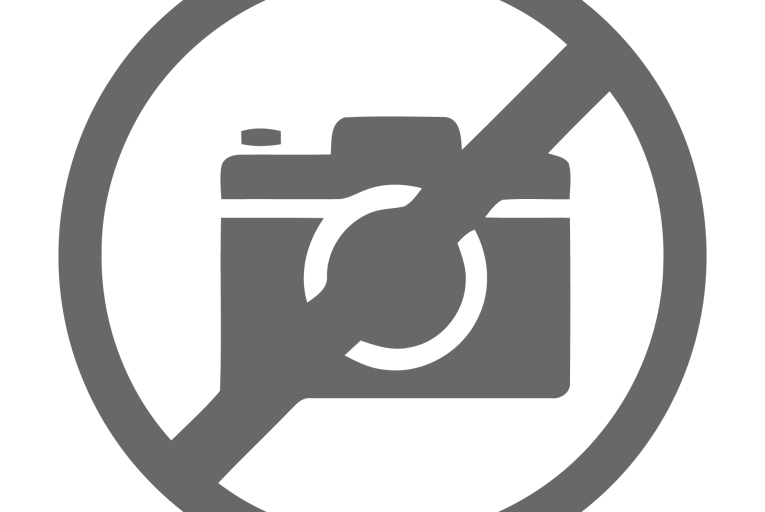
JD: The Adcom amplifiers were quite successful, weren’t they? They had and still have a very good reputation, and still command a good price on the used market. Your reference to feedback bias circuit is intriguing. Can you give some more details about that?
NP: It’s pretty simple. For production convenience, you want to make the bias current of the amplifier output stage easy to adjust and you want it to stay at that value forever, so I made up a simple self-adjusting bias circuit. Here are two diagrams, the first showing a simplified version of the GFA555 (Fig. 1)
and the second another version which I later patented (Fig. 2).
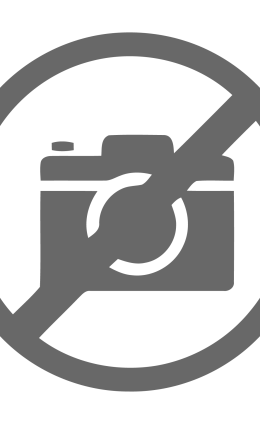
the GFA555 bias generator.
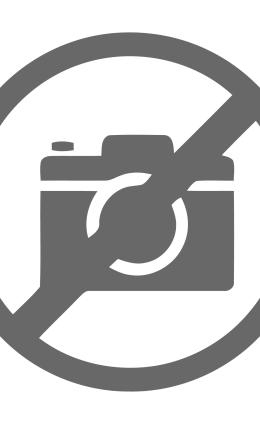
generator as patented by Mr. Pass.
In the GFA555 circuit, the bases Q7 and Q8 see the voltage across R1 and begin conducting when that voltage is enough to bias up their PN junctions (about 1.3V). This controls the voltage across the bases of drivers Q3 and Q4 with a local
feedback loop and biases output devices Q5 and Q6. The loop eliminates the thermal drift of Q3 and Q4, which improves the output stage bias current stability. This still leaves the thermal drift of output devices Q5 and Q6, but the thermal characteristic of the PN junctions of Q7 and Q8 tend to compensate for this if they are in thermal contact with the output stage. The second circuit is similar, but uses an optical isolator, which eliminates any electrical connection between the current sensing and bias control parts.
Of all the collaborations, Adcom was the most personally enjoyable. I enjoyed working with Rob and Alec, and we had a good relationship up to the sale of the company. I still talk to Rob occasionally.
The relationship with Nakamichi was more profit oriented. Around 1985 we were approached for a patent license and design work, which resulted in the Nakamichi versions of the Stasis amplifiers. Actually, we did not have to do a lot of work—they took our existing schematics and rendered them into their own version of the product. At the end of the process, they brought one up to Foresthill to have it tweaked, and there we were.
Nakamichi also led to design work for several car audio amplifiers by Soundstream. This project was a lot more work, but ultimately resulted in a product line that included the D200, D100, A100, A50, and so on. There wasn’t anything groundbreaking in the circuits, but it was my first commercial experience with switching power supplies.
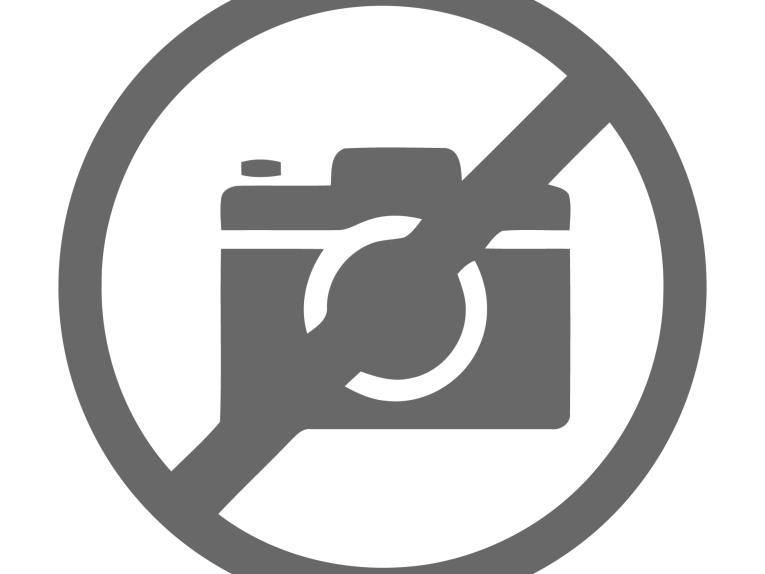
JD: In the 80s switching power supplies were relatively new and didn’t have a very good reputation. The Sony TAN86 and 88 come to mind. When they failed it was difficult to find a repair service that actually understood enough about these circuits to be able to repair them. What was your experience at the time? Now that the technology for switched supplies has matured, would you use them for power amplifiers?
NP: This is not really my area of expertise. As a concept, I would consider using them, but it would take a considerable investment in time and energy that I don’t have available at the moment.
I would be far more likely to use them in low power equipment, where they can be made to have lower capacitive coupling to the AC line and where noise issues are a little easier to deal with. But for the time being my attention is elsewhere.
So, shortly after founding Pass Labs in 1991 I did some work for Mobile Fidelity, replacing the Ortophon electronics driving their cutter-head. This was a particularly challenging project, as the original electronics were very complex, with tons of ancient op amps in the circuit. The goal was to create a better-sounding system by simplifying the active circuitry as much as possible.
The functions included balanced inputs, reverse RIAA equalization (full and half speed), additional equalization, feedback, feedback equalization, and balanced outputs. The outputs went to balanced Class A power amplifiers which drove the cutter-head, and feedback from the cutter-head came back to the control unit.
Because cutter-heads are very delicate and expensive to repair, there were numerous delicately adjusted protection circuits. The cutter-head drive coils were cooled by helium and monitored for temperature by running a very small amount of DC current through them. A circuit sensed the DC voltage across the coils and interpreted this as temperature. The protection needed to respond quickly, so the filters were quite sharp to avoid being triggered by the AC drive signal.
To accomplish all this, I first measured all the characteristics of the electronics and the cutter-head as precisely as possible and created a model of the system that I gave to a simulator (an early version of MicroCap). Then I began simplifying the active electronics by consolidating as many functions as possible into a few active stages. In the end I was able to get all the gain, equalization, and feedback folded into one active stage which still delivered the same “objective” performance.
The power amplifiers were cousins of the A75 design and predecessors of the later Adcom MOSFET designs. The project was successful, paid well, and broadened my experience in vinyl production and circuit simulation, but it was a tremendous amount of work over a couple years.
JD: You mentioned the A75. I believe that was a successor to the A40 which you published in Audio Amateur. Still mostly bipolar, if I remember correctly. At what point did you go to mostly or all-MOSFET designs? And what was the main reason for it?
NP: I cut my teeth on bipolars in the late 60s, and with the exception of JFET inputs, followed occasionally by small MOSFETs, the Threshold products were bipolar. In 1980 I took a
small leap with the power MOSFET version of the HK Citation 12 for an audioXpress DIY project, and after that my DIY pieces, including the A75, were MOSFET. Threshold continued to
make bipolar, but when I left in 1991 to form Pass Labs I had by then decided to concentrate on Class A FET design.
There were two reasons for it. First, I found the FETs easier to work with in terms of obtaining equivalent or better performance with simple Class A circuits.
Second, I liked the sound of the FETs better than bipolars, and still do. Now that some decent power JFETs are available, I am getting more interesting results, and I look forward to working with them more in the future.
Speaking of MOSFETs, in 1992 Adcom came back to the table for a new series to replace the GFA555 family, which had grown long in the tooth.
This became the GFA5800, 5500, and so on. The circuits are familiar by now: three stages of MOSFETs, using an input differential pair biased by a constant current source, this driving a P channel VAS, also current sourced, and followed by complementary MOSFET followers. I also delivered a simple line stage preamp design, the GFP750, which was vaguely similar to the Aleph P preamp, but also incorporated a switch for active versus passive operation.
I designed the Adcom car audio products, the GFI 4702, 4600, and other amplifiers. These were circuits based on the MOSFET designs for the home audio equipment, and they were pretty unusual for the car audio market. They seem to still have a good reputation today.
JD: Is there a principle difference in designing car audio amplifiers or home stereo amps, apart from the obvious 12V nominal supply in cars?
NP: It’s a very different aesthetic—that is to say that the customer has very different expectations. When I did the Adcom car series, I applied “high-end hi-fi” sensibilities to the design. It sounded great in the living room, but did not particularly impress the customers, and the product was only nominally successful. I think the same is true of home theater. The customer is more focused on dynamics and articulation, and some of the traditional high-end two channel qualities fall by the wayside.
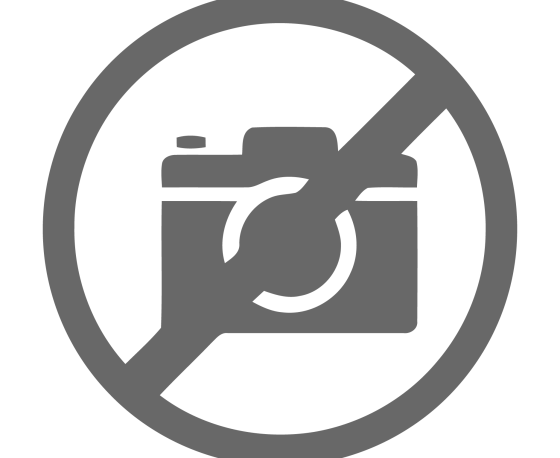
JD: I don’t want to open a whole can of worms, but you seem not to be overly concerned about getting very low distortion. For your First Watt amps you have made the point that at the low levels where most listening takes place, the distortion is very low. Yet, at high level peaks (especially with low- to medium-output power amps), distortion does rise considerably. But people like your amps. Does it have to do with the way the distortion rises, or with the spectral make-up of the distortion?
NP: The characteristic I get is the result of simple FET circuits running in Class A. This means minimal or no feedback, low-order harmonic characteristic, and monotonic but pedestrian distortion numbers. That approach usually (not always) delivers the sound that I like, and apparently my taste matches up with a portion of the buying public. The only magic involved takes place in the neural networks between our ears. What happens there is still poorly understood and varies between individuals. Whatever the deal is, ultra low distortion doesn’t seem to have much to do with it.
JD: I know you have been involved with speaker design as well; can you tell us a bit more about that?
NP: I started out building speakers, and found myself at ESS about two weeks before Oskar Heil arrived. I spent the next couple years working up all manner of enclosures and crossover networks, sharpening my electronics skills, and soaking up all there was to know about a start-up manufacturing operation.
Subsequently I spent a year running the service department at the local Sun Stereo — more valuable experience poking around inside the broken amplifiers of McIntosh, Phase Linear, Sony, Pioneer, and JVC, while I worked on my own designs at night until it was time to launch Threshold in 1975.
But the speaker bug never leaves you, and so I have always maintained a table-saw and a router. We have always kept a few examples of commercial speakers so as not to lose touch with the marketplace, but most of the time my listening space has been graced with unfinished plywood boxes. I met my wife Jill at ESS — she was the Heil diaphragm tester — and she doesn’t have any problem with that. When I met her I had the Claw, a straight bass horn with a 50ft2 mouth and 9’ depth. Since then she has lived with the Kleinhorns (nearly as large, but stereo) and El Pipe-Os at 12’ high, so a nice set of 4’ x 8’ open baffles doesn’t cross the line.
Of course, the day finally came when Pass Labs decided to offer a loudspeaker, the Rushmore, which dipped our toes in the water, and several years later I surprised her with SR1s which have grille cloths, followed now by SR2s (SR = Son of Rushmore).
I spend a lot of time with those funny little full-range speakers - Lowther, Feastrex, Fostex, and so on in open baffles. They have their own appeal and mate nicely with my little First Watt amplifiers at 10 to 25W.
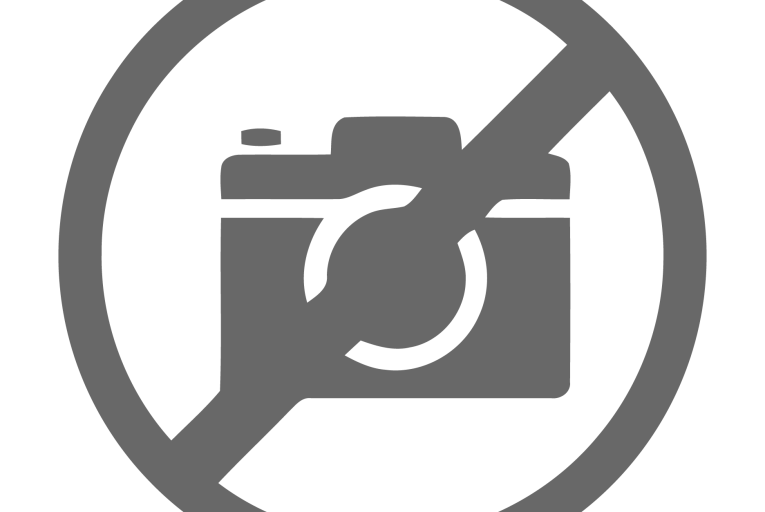
JD: You have been an early contributor to the audio DIY scene; I still remember an early article of yours in what was at the time The Audio Amateur magazine on cascodes, how they work, and their advantages. You have a knack of explaining engineering things very clearly in a few words, and you obviously enjoy doing it. You are also a very active contributor at diyaudio.com, being very generous with advice, tips, and complete amplifier designs that people can build. What do you get out of that interaction?
NP: I got my start when the boss at ESS sent an in-house paper I wrote to Audio Amateur. The first I heard about it was when he gave me the check for it. I’ve tried to do something fairly regularly for Ed Dell…
As to style, I like to speak to the teenager (me) who wanted to know this stuff—that’s my audience. There are always people who appreciate a decent explanation that gets to the meat and potatoes. I see it all as light entertainment with a little education thrown in.
The academic paper approach has its place, but it seems intended for people who mostly understand the stuff already. If you want to communicate with DIYers, you depend more on colorful analogies, a little hand waving, and very little differential calculus.
I get lots of personal satisfaction out of the whole enterprise. It gives me an outlet for some cool ideas and things that otherwise would stay bottled up, and I have an excuse to explore offbeat approaches purely for their entertainment value. Also, the process of communicating DIY stuff is a two way street — I would say I get about as much as I give.
JD: Nelson, thank you very much for your time and your frankness during these discussions. As you said earlier, diyaudio has a special place in your heart. Do you have any advice for those DIYers out there who aspire to become successful designers?
NP: Ah yes, the concluding bit of sage advice: First of all, design for yourself, not for other people, and don’t be afraid to try something. Then, when others want your designs, take great care of your reputation. You will not have much control over something that goes out into the world, but your name will still be on it. And, finally, be prepared for a lot of work.
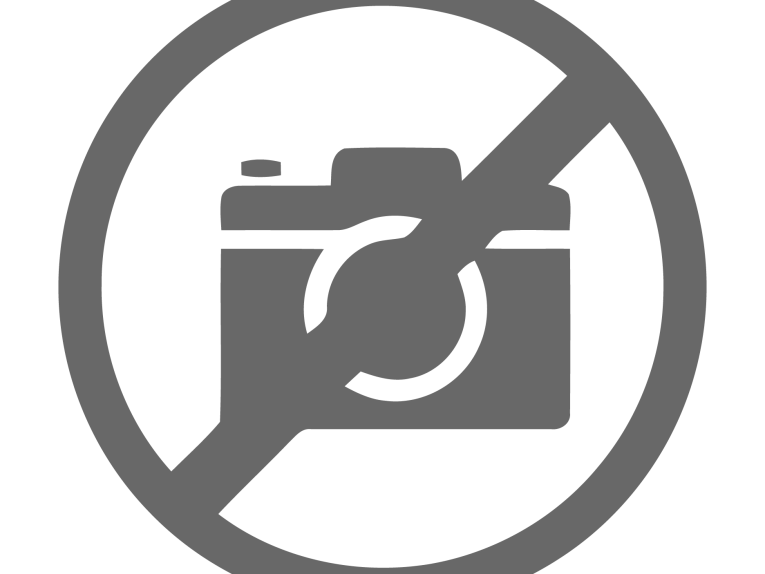